Manufacturers' Vital Role in Orchestrating the Supply Chain Symphony
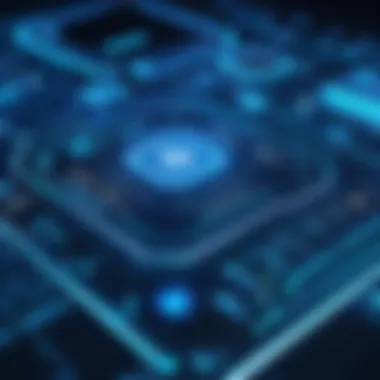
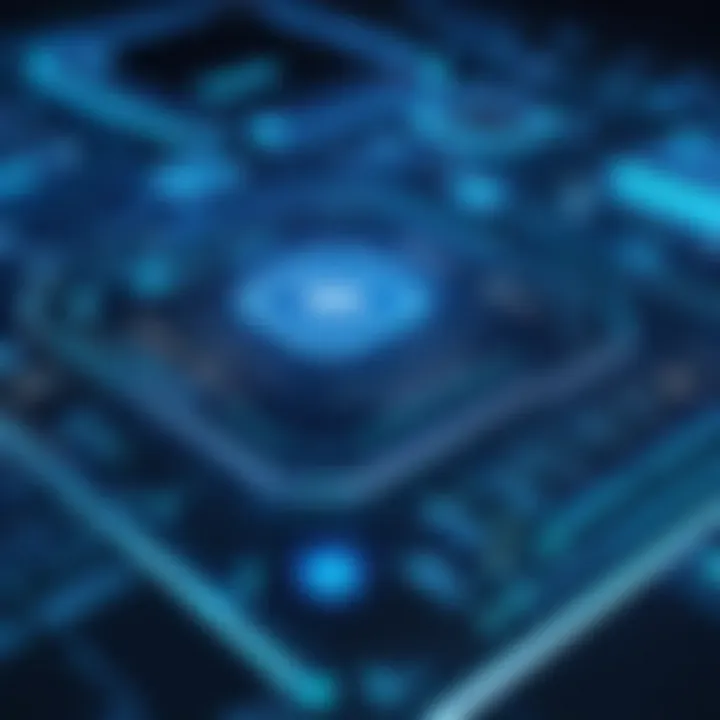
Technological Research Overview
The role of manufacturers in the supply chain is being reshaped by recent technological innovations. Automation, Internet of Things (Io T), and advanced analytics are revolutionizing business operations. Manufacturers now leverage sophisticated technologies to optimize processes, enhance quality control, and drive efficiency across the supply chain. These innovations have a profound impact on reducing lead times, minimizing production costs, and improving overall operational performance.
Recent Technological Innovations
Recent advancements in robotics and automation have enabled manufacturers to streamline production processes, minimize errors, and increase output. Collaborative robots (cobots) are being increasingly integrated into manufacturing facilities, working alongside human operators to enhance efficiency and flexibility. Furthermore, Io T technology enables real-time tracking of goods, predictive maintenance of machinery, and seamless communication between different stages of production.
Impact on Business Operations
The integration of advanced technologies has transformed traditional manufacturing practices, leading to agile and adaptive business operations. Smart factories equipped with interconnected systems and sensors enable real-time monitoring of production processes, facilitating proactive decision-making and rapid response to disruptions. Manufacturers leveraging these innovations experience heightened efficiency, reduced downtime, and improved resource utilization.
Future Technological Trends
Looking ahead, the future of manufacturing will be characterized by further automation, integration of artificial intelligence (AI) algorithms, and enhanced data analytics capabilities. Predictive analytics and machine learning algorithms will empower manufacturers to forecast demand, optimize inventory levels, and personalize products to meet evolving consumer preferences. Adopting Industry 4.0 principles and embracing emerging technologies will define the competitive landscape for manufacturers in the rapidly evolving supply chain ecosystem.
Manufacturers are the backbone of the supply chain, orchestrating the intricate dance of producing goods and services that drive the economy forward. In this article, we delve deep into the pivotal role that manufacturers play in ensuring the smooth flow of products across the supply chain landscape. Understanding how manufacturers operate and the impact they have on supply chain efficiency is crucial for any industry enthusiast.
Manufacturers form the bedrock of the supply chain, where raw materials are transformed into finished products ready for distribution. They are responsible for streamlining production processes to maximize efficiency and output quality. Manufacturers play a vital role in ensuring that goods meet market demands while maintaining stringent quality control measures to uphold product standards. Their contribution extends beyond mere production; it encompasses managing inventory levels, fostering relationships with suppliers, and embracing technological advancements to stay competitive in a fast-paced market.
The manufacturing industry has witnessed significant advancements in technology over the years. Automation and robotics have revolutionized traditional production methods, enhancing production speed and precision. Integrating Internet of Things (Io T) technologies has enabled manufacturers to monitor operations in real-time, predict maintenance needs, and optimize production schedules. These technological innovations not only boost operational efficiency but also pave the way for future growth and sustainability in manufacturing processes.
Sustainability practices have become a focal point for manufacturers aiming to reduce environmental impact. By implementing green supply chain initiatives, manufacturers can cut down on carbon emissions through efficient resource management and recycling programs. Embracing circular economy principles allows manufacturers to optimize resource utilization and reduce waste production, aligning with global sustainability goals.
Despite the advancements and focus on sustainability, manufacturers face a host of challenges in today's global market. From disruptions in the global supply chain due to pandemics and natural disasters to quality control issues such as defects and product recalls, manufacturers must navigate a complex operational landscape. Regulatory compliance adds another layer of complexity, requiring manufacturers to adhere to industry standards and environmental regulations to ensure product quality and consumer safety.
Understanding the Supply Chain
Supply chain management is a critical aspect of any business operation, especially within the manufacturing industry. Understanding the intricacies of the supply chain is indispensable for manufacturers to ensure the seamless flow of goods and services from raw materials to end products. By comprehensively studying the supply chain, manufacturers can identify bottlenecks, optimize processes, and ultimately improve the overall efficiency of their operations. This section will delve deep into the key elements, benefits, and considerations regarding supply chain management.
Supply Chain Basics
Definition of Supply Chain
The definition of a supply chain refers to the interconnected network of entities involved in the production and distribution of goods from suppliers to customers. This definition encapsulates the complete journey of a product, encompassing all stages from sourcing raw materials to delivering finished goods. Understanding this definition is vital as it sets the foundation for how manufacturers strategize their production, logistics, and inventory management. The key characteristic of defining a supply chain lies in its end-to-end visibility, allowing manufacturers to trace each product's origin, track its journey, and optimize each step efficiently. This clarity enables manufacturers to make informed decisions in streamlining operations, improving customer satisfaction, and adapting to market dynamics - all essential aspects to enhance the supply chain's performance.
Key Elements of a Supply Chain
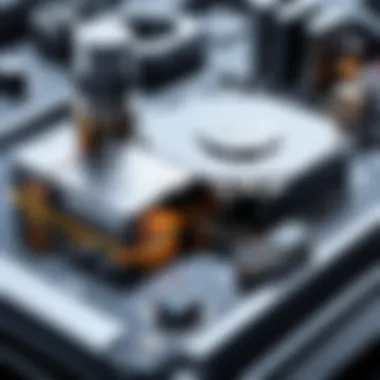
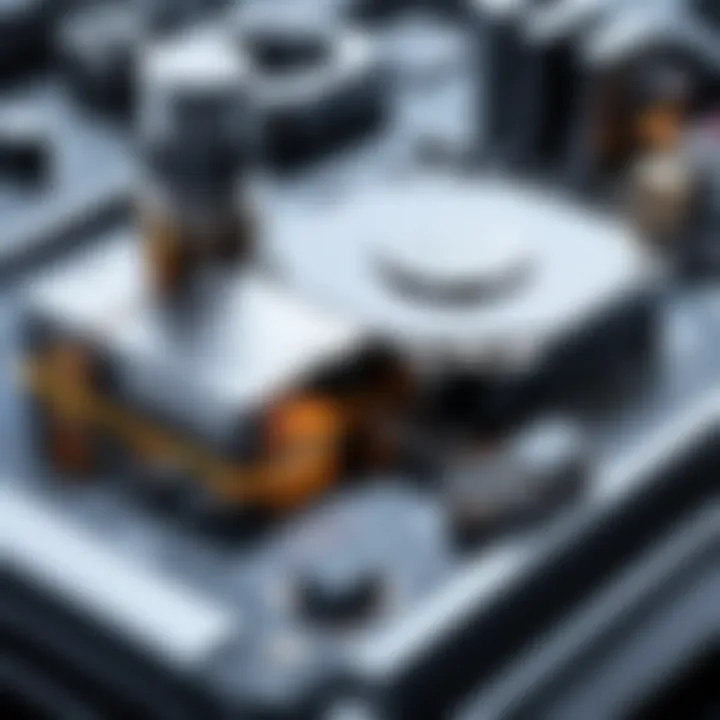
The key elements of a supply chain encompass various components such as suppliers, manufacturers, distributors, retailers, and customers. Each element plays a vital role in ensuring the smooth flow of goods and services through the supply chain. Understanding these key elements is crucial as it provides manufacturers with a holistic view of their operational ecosystem, highlighting dependencies, interactions, and areas for improvement. Manufacturers can leverage this knowledge to establish robust partnerships, implement agile processes, and enhance collaboration along the supply chain. Recognizing these key elements empowers manufacturers to optimize processes, mitigate risks, and capitalize on opportunities for growth and operational excellence.
The Significance of Manufacturers
Manufacturers, a linchpin in the supply chain machinery, hold a pivotal role in ensuring the seamless flow of goods and services. Their significance lies in the meticulous orchestration of production processes, guaranteeing efficiency and quality control. By streamlining production processes, manufacturers can eliminate bottlenecks and optimize resource utilization, ultimately enhancing the overall performance of the supply chain. This meticulous attention to detail contributes to the reliability and consistency of supply chain operations. Moreover, manufacturers play a critical role in inventory management, implementing Just-In-Time (JIT) systems and leveraging demand forecasting techniques to meet market demands with precision and timeliness.
Production Efficiency
Streamlining Production Processes
Streamlining production processes involves the refinement and optimization of manufacturing operations to enhance output efficiency. This meticulous approach focuses on eliminating inefficiencies, reducing waste, and enhancing productivity. Manufacturers employ lean principles to streamline workflows, ensuring a seamless production flow from raw materials to finished products. The key characteristic of streamlining production processes lies in its ability to identify and rectify operational inefficiencies, leading to cost savings and improved productivity. While the approach offers enhanced operational efficiency, it may require initial investments in process optimization tools and expertise, which can be advantageous in the long run.
Quality Control Measures
Quality control measures are imperative for manufacturers to uphold stringent quality standards and meet customer expectations. Implementing robust quality control measures ensures that products meet specifications and comply with regulatory requirements. Manufacturers integrate quality control checkpoints throughout the production process to detect defects early and maintain product integrity. The key characteristic of quality control measures is their role in safeguarding product quality and brand reputation. While stringent quality control measures may add production costs, they lead to fewer defects, reduced rework, and enhanced customer satisfaction.
Inventory Management
JIT Inventory Systems
Just-In-Time (JIT) inventory systems revolutionize traditional inventory management by minimizing excess inventory and utilizing a demand-driven approach. JIT systems enable manufacturers to synchronize production with customer demand, reducing storage costs and enhancing efficiency. The key characteristic of JIT inventory systems lies in their ability to improve cash flow and minimize carrying costs associated with excess inventory. While JIT systems offer agility and cost savings, they require flawless supply chain coordination to mitigate risks associated with supply shortages and demand fluctuations.
Demand Forecasting
Demand forecasting empowers manufacturers to anticipate market trends, consumer preferences, and demand fluctuations, enabling proactive inventory management and production planning. By leveraging historical data and market insights, manufacturers can optimize production schedules and inventory levels to align with forecasted demand. The unique feature of demand forecasting is its role in mitigating inventory obsolescence, reducing stockouts, and enhancing resource allocation efficiency. Although demand forecasting provides strategic advantages, inaccuracies in forecasts can result in under or overproduction, impacting profitability and customer satisfaction.
Relationship with Suppliers
Supplier Collaboration
Supplier collaboration establishes a mutually beneficial partnership between manufacturers and suppliers, fostering innovation, efficiency, and cost-effectiveness. By sharing information, resources, and expertise, manufacturers and suppliers can drive continuous improvement and operational excellence. The key characteristic of supplier collaboration is its emphasis on transparency, communication, and trust, leading to robust supply chain relationships. While supplier collaboration enhances supply chain resilience and responsiveness, it requires transparent communication channels, joint problem-solving mechanisms, and mutual goal alignment.
Ensuring Raw Material Quality
Ensuring raw material quality is paramount for maintaining product integrity, meeting quality standards, and mitigating production risks. Manufacturers implement stringent quality assurance processes, supplier audits, and material testing protocols to verify raw material integrity and compliance. The unique feature of ensuring raw material quality lies in its proactive approach to prevent defects, reduce rework, and ensure product consistency. While stringent quality checks enhance product reliability, they may lead to supplier disputes, delays in production, and increased procurement costs.
Technological Innovations in Manufacturing
In this section, we delve into the crucial role that technological innovations play in reshaping the manufacturing landscape. The integration of advanced technologies in manufacturing processes has revolutionized production efficiency and quality control measures. One key aspect is the adoption of automation and robotics, which have significantly impacted production speed and precision.
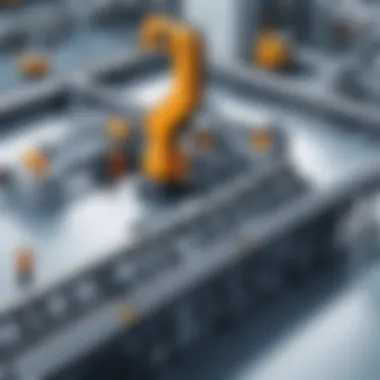
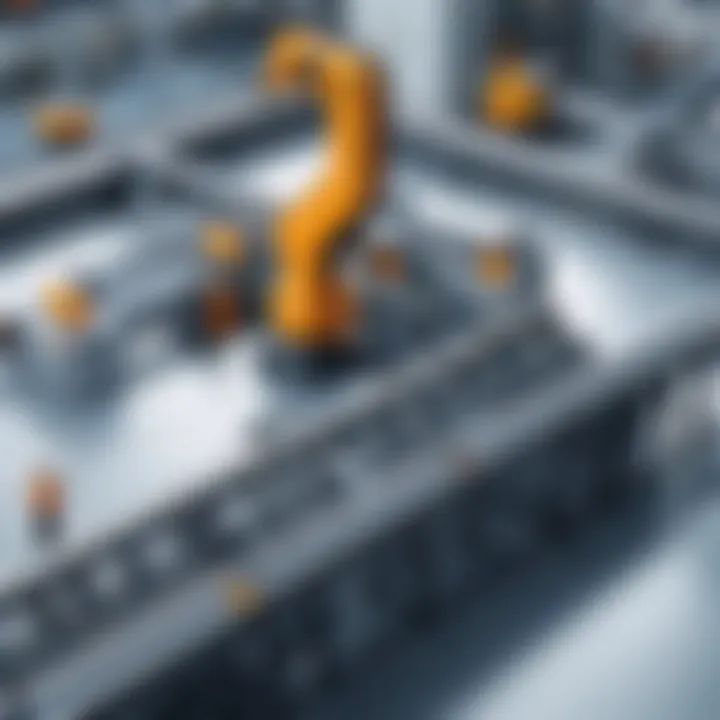
Automation and Robotics
Impact on Production Speed
Automation and robotics have a profound impact on enhancing production speed within manufacturing facilities. By automating repetitive tasks and streamlining processes, manufacturers can significantly increase their output rates and meet growing demands efficiently. The key characteristic of this innovation lies in its ability to reduce production cycle times and increase overall operational efficiency. Manufacturers opt for automation and robotics due to their capability to improve productivity and reduce manual errors, thereby aligning with the article's focus on enhancing supply chain performance.
Enhanced Precision
The incorporation of enhanced precision through automation and robotics further elevates manufacturing standards. Precision in production processes ensures consistent product quality and adherence to stringent specifications. Manufacturers favor this feature as it not only ensures product uniformity but also minimizes waste and rework, contributing to cost savings and improved customer satisfaction. While the unique feature of enhanced precision offers meticulous control over intricate manufacturing tasks, there might be challenges in calibrating and maintaining high levels of precision, which need careful consideration within the context of this article.
IoT Integration
In the realm of manufacturing, the integration of Io T technology holds immense significance in driving operational excellence and predictive maintenance practices.
Real-time Monitoring
Real-time monitoring through Io T integration enables manufacturers to gather live data from production processes, machinery, and inventory levels. This constant surveillance allows for proactive decision-making, immediate issue resolution, and optimized resource utilization. The key characteristic of real-time monitoring is its ability to provide instant visibility into factory operations, making it a strategic choice for enhancing manufacturing efficiency discussed in this article. The unique feature of real-time monitoring empowers manufacturers with actionable insights to streamline operations and ensure seamless production flow, although challenges may arise in data security and system integration.
Predictive Maintenance
Predictive maintenance, made possible through Io T integration, allows manufacturers to preemptively identify equipment failures or maintenance needs based on data analytics and machine learning algorithms. This proactive approach minimizes downtime, reduces operational costs, and prolongs machinery lifespan. Manufacturers opt for predictive maintenance due to its predictive analytics capabilities and its ability to prevent costly breakdowns, aligning with the article's emphasis on optimizing overall supply chain performance. The unique aspect of predictive maintenance lies in its foresight to transform reactive maintenance into a proactive, data-driven strategy, despite potential complexities in data interpretation and sensor reliability.
Sustainability Practices in Manufacturing
Sustainability practices in manufacturing are pivotal in the context of the evolving supply chain landscape. In this article, we delve into the diverse elements that contribute to the sustainability of manufacturing processes, shedding light on their paramount significance in optimizing operational efficiency and environmental impact. Considering the pressing need for sustainable solutions in today's fast-paced industry environment, incorporating green practices has become imperative for manufacturers looking to enhance their overall performance.
Green Supply Chain Initiatives
Reducing Carbon Footprint:
Reducing the carbon footprint stands as a fundamental aspect of green supply chain initiatives within manufacturing. By significantly curtailing greenhouse gas emissions and promoting resource conservation, this practice plays a vital role in fostering a greener and more efficient production ecosystem. The key characteristic of reducing carbon footprint lies in its ability to mitigate environmental harm while enhancing operational sustainability. This environmentally conscious strategy provides manufacturers with a sustainable and cost-effective approach to production, making it a popular choice for firms aiming to align with eco-friendly practices. However, challenges such as initial investment costs and restructuring operational processes may pose as disadvantages for some manufacturers exploring this avenue.
Recycling Programs:
In conjunction with reducing carbon footprint, implementing recycling programs represents another cornerstone of sustainable manufacturing practices. By incorporating recycling across production cycles, manufacturers can minimize waste generation, promote resource efficiency, and reduce environmental impact significantly. Recycling programs are characterized by their ability to convert waste materials into reusable resources, thereby closing the loop on resource consumption and waste generation. This upcycling strategy is not only beneficial for the environment but also contributes to cost savings and long-term sustainability for manufacturers. While the advantages of recycling programs are substantial in promoting a circular economy, logistical challenges and initial setup costs may hinder widespread adoption within the industry.
Circular Economy Principles
Resource Optimization:
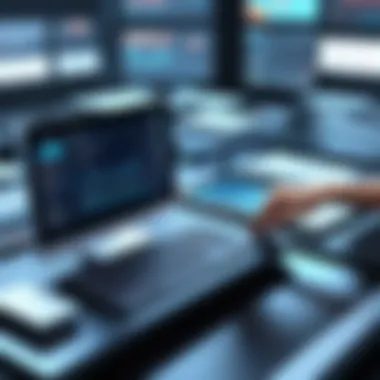
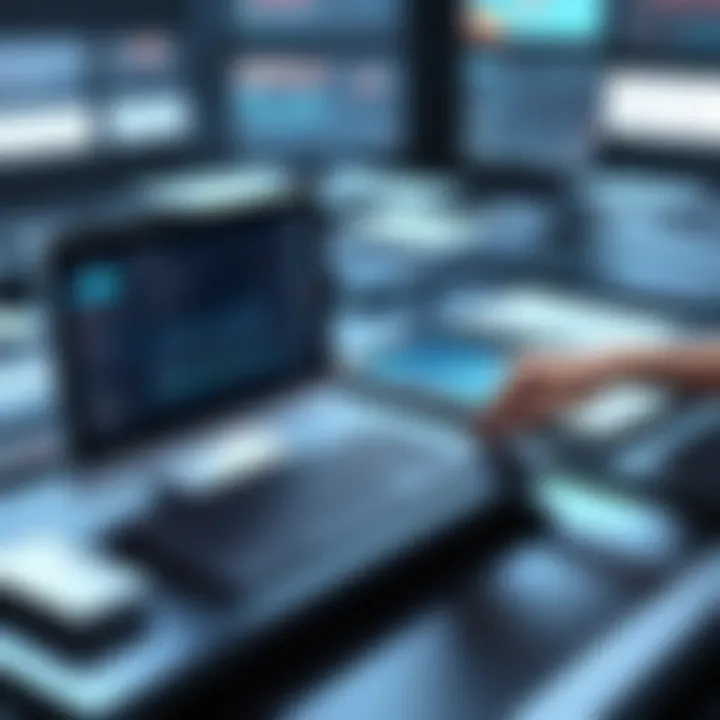
Resource optimization forms a critical aspect of circular economy principles in manufacturing. By maximizing the usage of materials throughout the production process, manufacturers can minimize resource wastage and enhance operational efficiency. The key characteristic of resource optimization lies in its ability to streamline production processes, reduce costs, and promote sustainable resource management. This approach is popular among manufacturers seeking to boost profitability while reducing their environmental footprint. However, the complexity of tracking and optimizing resources across the supply chain may present challenges for some firms looking to implement this strategy.
Waste Reduction Strategies:
Complementing resource optimization, waste reduction strategies play a vital role in bolstering sustainability within manufacturing operations. By minimizing waste generation, enhancing recycling efforts, and implementing efficient disposal methods, manufacturers can significantly reduce their environmental impact and operational costs. Waste reduction strategies are characterized by their focus on minimizing inefficiencies, enhancing resource recovery, and promoting a circular production model. While the advantages of waste reduction strategies are substantial in promoting sustainability, operational changes and employee training may be required, posing initial challenges for firms transitioning towards a zero-waste manufacturing model.
Challenges Faced by Manufacturers
In the complex landscape of supply chain management, manufacturers encounter various challenges that significantly impact operations. These challenges are pivotal in understanding the resilience and adaptability required in the manufacturing sector. Manufacturers face a multitude of obstacles ranging from global supply chain disruptions to internal quality control issues and regulatory compliance.
Global Supply Chain Disruptions
Global supply chain disruptions present a critical challenge for manufacturers, threatening the seamless flow of goods and services. Among these disruptions, pandemics and natural disasters stand out as major disruptors that can have catastrophic effects on manufacturing operations.
Pandemics
Pandemics, such as the recent COVID-19 outbreak, have showcased the vulnerability of global supply chains to health crises. The outbreak of a pandemic can lead to widespread disruptions in production, transportation, and workforce availability, causing a ripple effect across the entire supply chain. Manufacturers must devise contingency plans to mitigate the impact of pandemics, focusing on business continuity and supply chain robustness.
Natural Disasters
Natural disasters like earthquakes, tsunamis, and hurricanes pose significant challenges to manufacturers worldwide. These unpredictable events can result in factory closures, infrastructure damage, and supply chain delays. Manufacturers must implement risk management strategies to prepare for such contingencies, including diversified sourcing, resilient infrastructure, and disaster recovery protocols.
Quality Control Issues
Maintaining high quality standards in manufacturing processes is paramount to ensuring customer satisfaction and operational efficiency. Quality control issues, such as defects and product recalls, can tarnish a manufacturer's reputation and lead to financial losses.
Defects
Defects in products can occur at any stage of the production process, compromising product quality and safety. Manufacturers need to implement robust quality control measures to detect and rectify defects promptly. By investing in advanced testing technologies and quality assurance protocols, manufacturers can enhance product reliability and brand reputation.
Product Recalls
Product recalls due to safety concerns or manufacturing defects can have far-reaching consequences for manufacturers. Recalls not only incur significant costs but also erode consumer trust and loyalty. Manufacturers must proactively address product quality issues, conduct thorough inspections, and implement corrective actions to prevent costly recalls.
Regulatory Compliance
Adhering to regulatory standards and environmental regulations is non-negotiable for manufacturers operating in a global marketplace. Compliance with industry-specific regulations ensures ethical practices, sustainability, and legal adherence.
Adherence to Standards
Conforming to industry standards and certifications is essential for manufacturers to uphold product quality and safety. Adherence to standards demonstrates a commitment to excellence and consumer protection. Manufacturers must stay abreast of evolving standards and regulatory requirements to maintain compliance and boost market credibility.
Environmental Regulations
Compliance with environmental regulations is imperative for manufacturers to minimize ecological impact and promote sustainability. Regulations governing waste management, emissions control, and resource conservation necessitate eco-friendly manufacturing practices. By embracing green technologies, recycling initiatives, and renewable energy sources, manufacturers can align with environmental regulations and foster eco-responsibility.