Exploring the Role of SAP MES in Manufacturing Efficiency
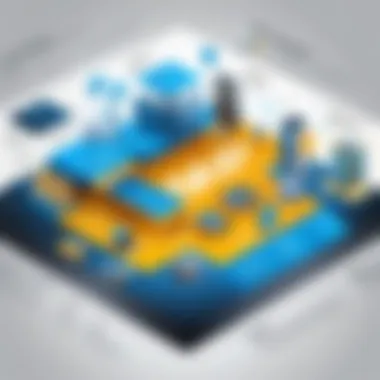

Intro
In the ever-evolving world of manufacturing, one concept stands tall as a vital component of success: the Manufacturing Execution System (MES). Specifically, SAP MES plays a pivotal role in how manufacturing businesses optimize their processes. Let’s face it—staying competitive is not just about producing goods but also about how effectively those goods are made. In this article, we'll dissect various aspects of SAP MES, exploring its functionalities and significance in today’s complex manufacturing environment.
Manufacturers are strapped with challenges such as meeting demand fluctuations, managing resources efficiently, and ensuring product quality. Here, SAP MES enters the chat. By linking the raw data from production to real-time monitoring and performance analysis, it has emerged as a game-changer. This discussion is tailored for professionals, entrepreneurs, decision-makers, and tech enthusiasts, all of whom stand to gain insights through a comprehensive understanding of this powerful tool.
From understanding the core components of SAP MES to its impact on day-to-day operations, this exploration aims to unpack the layers of complexity surrounding this system. We’ll also skim over the recent analytical trends impacting the business landscape, as data now drives informed decision-making. Along the way, we'll touch upon future advancements and how emerging technologies could mold the framework of operational efficiencies in manufacturing.
Let’s roll up our sleeves and delve into this comprehensive analysis.
Preamble to SAP MES
In the intricate and fast-paced world of manufacturing, the need for a robust system to manage and optimize production is paramount. This is where SAP Manufacturing Execution Systems (MES) comes into play, offering a thorough understanding of how operations can run more smoothly, efficiently, and effectively. These systems serve as the bridge connecting the plant floor with higher-level business operations, providing crucial insights that can drive better decision-making and enhance productivity.
Defining Manufacturing Execution Systems
Manufacturing Execution Systems are software platforms designed to monitor, manage, and optimize production processes. The purpose of an MES is to ensure that manufacturing operations are executed as efficiently and accurately as possible. At its core, an MES serves several key functions, such as:
- Scheduling Production: MES can create optimal schedules that improve throughput and reduce idle time.
- Tracking Work-in-Progress: With real-time visibility, managers can track the progress of products through various stages of production.
- Reporting: MES generates critical reports that provide insights into production efficiency, inventory levels, and machine utilization.
- Regulatory Compliance: It helps in maintaining compliance with industry standards by keeping meticulous records of production activities.
Effectively, businesses that deploy an MES can expect a more transparent view of their operations, which can directly translate into improved performance.
The Evolution of SAP MES
Over the years, the evolution of SAP MES reflects both advancements in technology and changing needs within the manufacturing sector. Initially, MES platforms were standalone solutions that required extensive customization and often struggled with integration into existing systems.
As the landscape has shifted, so have the capabilities of SAP MES. Today, these systems are designed with interoperability in mind, facilitating seamless integration with Enterprise Resource Planning (ERP) systems, Internet of Things (IoT) devices, and supply chain management tools. This harmonious integration allows for:
- Real-Time Data Access: Immediate data availability leads to quicker decision-making processes.
- Scalability: As manufacturing needs grow, SAP MES is adaptable enough to accommodate those changes.
- Advanced Analytics: Modern systems leverage big data and analytics for predictive insights, which can significantly enhance operational strategies.
The journey of SAP MES from isolated installations to integrated solutions illustrates the importance of technological adaptability in addressing the ever-evolving challenges of manufacturing. It stands as a cornerstone for businesses aiming to modernize their operations and refine their production practices.
Core Functions of SAP MES
Understanding the core functions of SAP Manufacturing Execution Systems (MES) provides vital insight into how this technology can significantly transform production processes within manufacturing environments. These functions are not simply features, they are interlinked elements essential for enhancing operational performance. From workflow management to real-time data collection and quality management integration, each component plays a pivotal role in ensuring that businesses maximize their efficiency and adapt to market demands swiftly.
Workflow Management
Workflow management is like the beat of a drum in the production symphony. It orchestrates how tasks are assigned, monitored, and completed in the manufacturing process. SAP MES facilitates this coordination, allowing manufacturing processes to run smoothly without unnecessary delays. By automating task allocations and tracking production stages, businesses can ensure that resources are used optimally.
Moreover, effective workflow management minimizes human error. When workers know what needs to be done at any given time, productivity naturally increases. Reports and logs generated through SAP MES enable managers to oversee operations in real-time, ensuring that everyone is singing from the same hymn sheet. Notably, organizations seeing an uptick in delivery consistency and timeliness often credit robust workflow systems as their backbone.
Real-Time Data Collection
In today’s fast-paced industry, having up-to-the-minute information is as crucial as having a reliable power supply. Real-time data collection through SAP MES allows organizations to gather, analyze, and act on data as it is produced on the shop floor. This feature transforms raw data into actionable insights, giving decision-makers the information they need at their fingertips.
This capability goes beyond mere numbers. For instance, consider a scenario where a machine component begins to fail. With real-time data tracking, alerts can be triggered automatically, allowing for immediate maintenance actions — significantly reducing downtime. Additionally, this continuous data flow helps identify inefficiencies in processes, enabling teams to pivot quickly and make informed decisions that align with business goals. Industries that leverage this function often find themselves ahead of competitors who rely on outdated methods of data collection.
Quality Management Integration
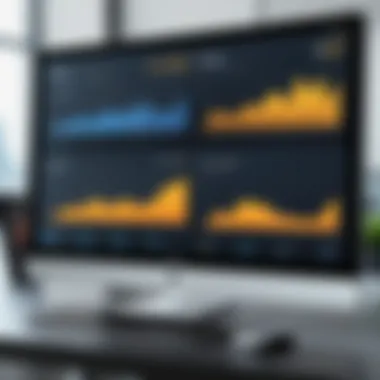

Quality management and production speed are often seen as opposing forces; however, SAP MES ensures they work hand in hand. The integration of quality management within SAP MES means that quality checkpoints become part of the production workflow rather than an afterthought. By embedding quality controls into every stage of manufacturing, businesses can catch defects early, reducing waste and rework significantly.
An example of this is defect tracking. If a production batch shows an anomaly, SAP MES can trace it back to specific processes or materials, facilitating root cause analysis. This proactive approach leads not only to improved product quality but also builds a culture of continuous improvement within the organization. As many high-performing manufacturers know, maintaining product integrity fosters customer trust and loyalty, which is invaluable in today’s market.
"A stitch in time saves nine" - this old saying rings especially true in the context of quality management within manufacturing.
Understanding these core functions of SAP MES is essential for anyone aiming to leverage its full potential. Workflow management, real-time data collection, and quality management integration provide a comprehensive toolkit for driving operational excellence. By mastering these elements, organizations position themselves to respond to industry demands and enhance their competitive edge.
Benefits of Implementing SAP MES
Implementing SAP Manufacturing Execution Systems (MES) brings several advantages to organizations aiming to enhance their manufacturing processes. These benefits not only streamline operations but also position the business as a competitive player in today’s market. Rather than diving into the tech-heavy details, it’s essential to keep an eye on how these systems practically influence production environments.
Enhanced Operational Efficiency
When it comes to operational efficiency, SAP MES shines like a beacon of hope for manufacturers. By centralizing information and providing real-time insights, businesses can adapt their workflows rapidly. This agility ensures that problems are addressed before they escalate, minimizing downtime.
Consider a factory floor where every minute counts—having a system that tracks machine performance and production metrics instantly can lead to better resource allocation, smoother process flows, and ultimately, higher output.
Moreover, by automating previously manual processes, companies reduce the risk of human error. An efficient operation doesn’t merely mean faster production; it often translates into less waste generated while producing goods. The result? A leaner operation that justifies investing in SAP MES.
Improved Product Quality
Quality might be a buzzword often thrown around in manufacturing talk, yet it’s the cornerstone to maintaining customer satisfaction. With SAP MES, manufacturers have the tools needed to uphold high-quality standards through integrated quality management processes. By implementing checks and balances at various stages of production, businesses can ensure that every product adheres to predetermined specifications.
This continual monitoring allows organizations to catch defects earlier in production cycles, thereby reducing the costs associated with recalls or customer dissatisfaction. Ultimately, improving quality raises customer trust, and winning repeat business becomes easier. Products manufactured under strict quality guidelines often distinguish themselves in the marketplace.
"A stitch in time saves nine." Ensuring quality from the outset often invites lesser hurdles later down the line.
Cost Reduction Strategies
Integrating SAP MES can lead to substantial cost reductions at multiple levels. Initial setup might seem daunting for some, but considering the long-term savings makes it worthwhile. By improving visibility into the production process, SAP MES allows for smarter decision-making regarding resource consumption.
For instance, with accurate data on machine utilization and employee efficiency, organizations identify bottlenecks—those pesky points where progress halts. Addressing these can lead to optimized staffing and machinery usage without the need for unnecessary investments.
Consider implementing strategies such as predictive maintenance, which entails predicting when equipment might fail and servicing it proactively. This not only saves costs on emergency repairs but also prolongs the life of expensive machinery.
Key Components of SAP MES
The heart of SAP Manufacturing Execution Systems (MES) resides in its key components, which collectively tune the overall efficiency of manufacturing processes. Understanding these components is vital because they integrate seamlessly to enhance production, making them indispensable for organizations seeking agility in their manufacturing operations. A deep dive into these elements reveals how they contribute to effective decision-making and operational clarity.
System Architecture
The system architecture of SAP MES is the framework that supports its functionalities. Often visualized as a layered structure, this architecture ensures that various components work together harmoniously. At its core, you'll find the database layer, where crucial data is stored. It’s not just a data repository; it’s the backbone that enables real-time data collection and analysis. Next, there's the application layer, which handles all the operational processes. This layer is crucial for executing business logic, managing workflows, and ensuring that information flows to and from the factory floor.
Without a robust architecture, the system would be like a house of cards – fragile and prone to collapse under pressure. The architecture also provides scalability. As manufacturing needs evolve, the system can be adjusted without needing a complete overhaul. Every organization can find comfort in knowing that it can adapt, rather than having to throw everything at the wall and hope something sticks.
User Interface
The user interface (UI) of SAP MES plays a crucial role in how intuitive and effective the system can be. A well-designed UI is not just about aesthetics; it directly affects user experience. Imagine a cluttered workspace with too many papers; things get lost easily, and tasks are harder to complete. The same goes for software. A clean and well-organized interface allows operators to monitor performance and make quick adjustments without feeling overwhelmed.
An interface that showcases real-time data in easy-to-read formats means operators can focus on what's important. Visual tools, like dashboards, present complex data simply, often eliminating the need for lengthy reports. Users can spot trends, identify issues quickly, and act decisively. Customization options within the UI allow companies to tailor views based on roles, ensuring that each user sees what’s vital for their responsibilities.
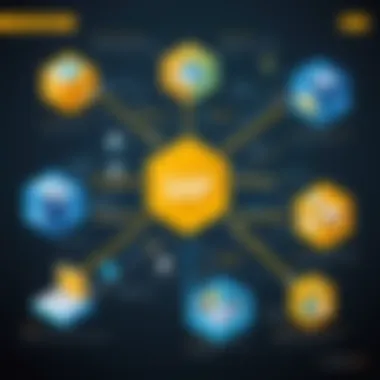

Data Integration Capabilities
In today's manufacturing landscape, data integration capabilities are non-negotiable. SAP MES doesn't just operate in isolation; it interacts with various systems, such as ERP and quality management systems. This interconnectedness allows for seamless data flow, creating a comprehensive ecosystem where information is readily available.
For instance, the ability to pull data from machines or sensors for real-time monitoring can drastically reduce downtimes and increase productivity. It also ensures more accurate reporting and analytics, paving the way for informed decision-making. Integration with IoT devices takes this a step further. With everything connected, it means better monitoring of equipment and the ability to predict failures before they occur.
"Data integration in SAP MES is like the glue that holds everything together, allowing for smooth transitions and communication across different systems."
Challenges Associated with SAP MES
Implementing a Manufacturing Execution System (MES) like SAP MES is not without its hurdles. While the benefits are manifold, organizations often face several challenges that can significantly impact the success of the deployment. These challenges demand attention and strategic planning. Understanding them is vital for making informed decisions along the journey.
Implementation Complexities
One of the primary concerns associated with SAP MES implementation is the inherent complexity of the system itself. Adopting MES requires a thorough analysis of existing processes, specialized knowledge, and sometimes significant adjustments to current workflows. The sheer scale of data and the number of stakeholders involved can complicate the implementation process. It's not just about plugging in software; it's about rethinking how a whole manufacturing environment operates.
For example, a medium-sized automotive supplier may have various production lines where every process influences others. Integrating SAP MES means ensuring that each machine, station, and worker can communicate effectively within the system.
Some key aspects include:
- Customization Needs: Every organization has unique processes, which necessitates customization during implementation. This requirement can lead to extensive development time and costly delays.
- Training Requirements: Staff must be well-versed in both the technology and operational processes. Without adequate training, employees may struggle to adapt, leading to poor system utilization.
- System Integration: Merging SAP MES with existing systems (such as ERP or production planning tools) adds another layer of complexity. Compatibility issues might crop up, causing disruptions in business operations.
Change Management Issues
Change is often met with resistance, and this is especially true when it comes to technology adoption within a workforce. When implementing SAP MES, change management becomes crucial. Employees often cling to familiar patterns and processes, which can impede engagement with the new system.
Effectively managing this transition requires an understanding of the cultural dynamics within an organization. Proactive communication can ease the transition by highlighting the benefits of the system for individual roles and the overall operational improvement.
Key considerations for successful change management include:
- Stakeholder Engagement: Involving key stakeholders early in the process helps promote buy-in. Addressing their concerns and incorporating their feedback can lead to a more seamless transition.
- Comprehensive Training Programs: Offering more than just a one-off training can lead to greater mastery of the system. Continuous training sessions can also help address issues as they arise.
- Support Systems: Establishing a support structure post-implementation can assist employees who may have questions or encounter difficulties with the new system.
By understanding the intricacies of implementation and fostering a positive change culture, organizations can navigate the challenges associated with SAP MES more effectively.
In summary, while SAP MES presents vast opportunities for enhancement in manufacturing environments, confronting the challenges of implementation and change management head-on is essential. Emphasizing these factors not only aids in smoother transitions but also sets a foundation for long-term success.
Comparative Analysis with Other MES Solutions
Comparative analysis stands as a fundamental pillar in understanding how SAP MES stacks up against its competition within the realm of Manufacturing Execution Systems (MES). The distinct functionalities offered by various MES platforms necessitate a closer examination. This scrutiny enables businesses to make informed decisions, especially when navigating the ever-evolving landscape of manufacturing technologies.
SAP MES vs. Generic MES Platforms
When comparing SAP MES to generic MES platforms, one quickly sees the difference in capability and adaptability. Generic systems often provide a one-size-fits-all solution, lacking the depth and customization options required by specialized manufacturing industries. SAP MES, on the other hand, caters to the intricacies of sector-specific requirements.
- Integration: SAP MES is designed to seamlessly integrate with existing SAP systems, facilitating smoother communication across various departments. Generic platforms? Well, they can struggle with integration, leading to data silos and inefficiencies.
- Scalability: SAP MES shines in scalability, powering organizations from small teams to large enterprises without much hassle. Generic MES solutions might impose limitations that can hinder growth as operations expand.
- Support: SAP offers robust customer support, providing businesses with access to a wealth of resources and expert advice. Customers of generic systems often find themselves in a bind without sufficient support.
This comparative analysis hints at why more and more organizations are gravitating toward SAP MES, as they seek out tools that align with their operational goals without losing sight of the unique demands of their industry.
Customization and Flexibility
Another critical factor to consider is customization and flexibility within MES solutions. SAP MES excels when it comes to tailorable functionalities that fit the precise needs of a business.
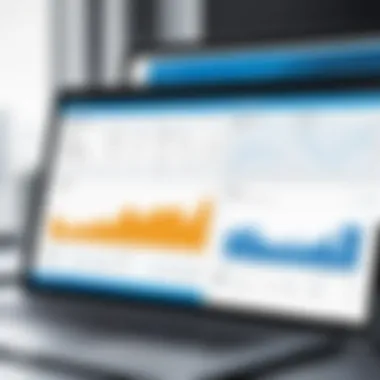

- Tailored Workflows: Businesses can create workflows that match their specific processes, rather than adapting to the rigid structures of generic systems. This capability allows for optimization and fosters efficiency.
- User-Focused Design: With the flexibility to modify the interface, organizations can enhance user experience and reduce training time. Generic platforms may lack this degree of personalization, resulting in a steeper learning curve for employees.
- Feature Enhancement: SAP MES can evolve alongside company goals. New functionalities can be introduced as needed, unlike generic solutions where updates might feel like pulling teeth.
The takeaway here is clear: a bespoke approach in execution systems can translate directly to production efficiency, providing a competitive edge that is hard to replicate with cookie-cutter solutions.
"In a world where every second counts, the ability to customize a system can mean the difference between success and failure in production."
In summary, the landscape of MES solutions is robust and diverse. By assessing the distinct features and capabilities of SAP MES in comparison to generic platforms, organizations can develop strategies tailored to their operational needs, ultimately leading to smarter investments and heightened manufacturing performance.
Future Trends in SAP MES
The landscape of Manufacturing Execution Systems is constantly evolving, driven by technological advancements and changing market demands. Understanding the future trends in SAP MES is crucial for organizations looking to maintain their competitive edge. As industries push towards digitization, the integration of new technologies within SAP MES paves the way for enhanced efficiency, flexibility, and data-driven decision-making. This section delves deep into the pivotal trends that shape SAP MES and how they impact manufacturing processes.
Integration with IoT
The Internet of Things (IoT) is revolutionizing how manufacturing operations are conducted. With IoT, we witness a step-change in connectivity that offers vast opportunities for manufacturers to improve processes, reduce costs, and elevate product quality. By integrating IoT with SAP MES, real-time data streaming from machines becomes a possibility. This means sensors can gather minute details about production in a factory floor, transmitting data instantly to the MES.
The benefits include:
- Real-time Monitoring: Operators can monitor equipment conditions and production data in real-time, enabling immediate adjustments to operations. For example, if a machine shows signs of overheating, corrective action can be taken before breakdown, thus minimizing downtime.
- Predictive Maintenance: IoT devices can analyze trends to forecast potential failures, allowing maintenance to be scheduled proactively. It’s like having a crystal ball for maintenance schedules!
- Enhanced Resource Management: With improved visibility of resource usage, companies can optimize their inventory levels and reduce waste.
By tapping into IoT capabilities, firms can enhance their operational agility, ensuring that they remain responsive to changes in demand or production capacity.
Artificial Intelligence Applications
Artificial Intelligence (AI) is another critical trend that’s reshaping how SAP MES is utilized in manufacturing. The infusion of AI into MES extends operational capabilities and enriches decision-making processes. Machine learning algorithms can process large datasets, revealing insights that were once hidden in the noise of data.
Key applications of AI in SAP MES include:
- Data Analysis: AI can sift through production data to identify inefficiencies and suggest areas for improvement. With AI, analyzing complex datasets becomes fast and straightforward, enabling quicker, more informed decision-making.
- Quality Control: Implementation of AI technologies can enhance quality management systems. For instance, image recognition technologies can identify defects on production lines, significantly increasing accuracy compared to human inspection.
- Workflow Automation: By automating routine tasks, businesses can free up human resources for more strategic initiatives. Repetitive jobs like data entry and scheduling can be managed effectively, reducing errors and improving efficiency.
As AI technology matures, its integration within SAP MES will likely become standard practice, ensuring that manufacturers can leverage data effectively to achieve operational excellence.
"Integrating IoT and AI within SAP MES is not just forward-thinking; it's essential for any organization aiming to thrive in a digital landscape."
Closure and Strategic Recommendations
As the saying goes, "It’s not the destination, it’s the journey." In the realm of manufacturing, the journey through implementing SAP MES is pivotal for sustainable success. This section emphasizes the importance of making well-informed choices in relation to SAP MES and posits strategic recommendations that can enhance a company’s manufacturing prowess.
Making Informed Decisions
When delving into the world of SAP MES, decision-makers must prioritize a thorough understanding of their organization’s unique needs. This isn’t a one-size-fits-all scenario—different businesses face diverse challenges. Here are some key aspects to consider:
- Align Goals with Capabilities: Understand the full suite of functionalities that SAP MES offers. Align these capabilities with your operational goals to ensure a clear path toward achieving desired outcomes.
- Assess Current Infrastructure: Evaluate existing systems and processes. This can illuminate integration challenges and reveal areas where SAP MES can fill gaps or enhance current practices.
- Stakeholder Engagement: Get the team on board early. Engage employees from various departments; they might provide insights that influence the decision-making process significantly.
- Pilot Programs: Before moving full steam ahead, conducting pilot tests can provide invaluable feedback. This iterative approach allows for adjustments before wider implementation.
Making thoughtful choices about SAP MES not only maximizes investments but also lays a solid foundation for the longevity of the system within the organization.
Leveraging SAP MES for Competitive Advantage
The competitive landscape is no cakewalk. Harnessing the functionalities of SAP MES can propel a business well ahead of the pack. Here’s how:
- Enhance Visibility: SAP MES offers real-time data, allowing businesses to monitor operations closely. This immediacy not only fosters proactive management but also aids in identifying bottlenecks before they escalate.
- Data-Driven Decisions: With advanced analytics capabilities, companies can draw insights from historical and operational data. Strategic decision-making grounded in quantitative analysis provides a clearer path through the haze of competition.
- Agility in Processes: In today’s fast-paced market, adaptability is crucial. SAP MES allows agile responses to changes in demand or production constraints, allowing businesses to pivot quickly without losing momentum.
- Quality Control: The integration of quality management features means that potential defects can be identified and addressed swiftly. This accelerates corrective actions and minimizes the financial impact of rework and returns.
Ultimately, when businesses capitalize on SAP MES effectively, they don’t merely survive—they thrive. This strategy not only contributes to operational excellence but positions the organization as an industry leader.
"The competition isn't just keeping pace anymore; they're speeding ahead. Each decision must be deliberate and strategic to not just keep up but to outshine others."
Through the strategic recommendations laid out in this section, organizations can make informed choices regarding SAP MES, enhancing their overall operational efficiency and cementing a robust competitive edge in the manufacturing domain.