Essential Strategies for Gardner Denver Maintenance Reset
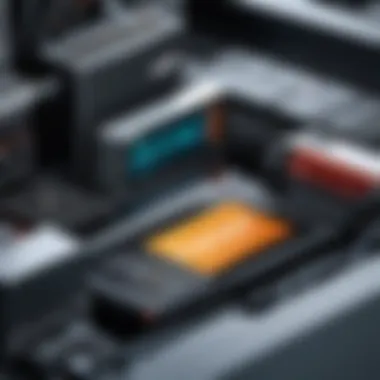
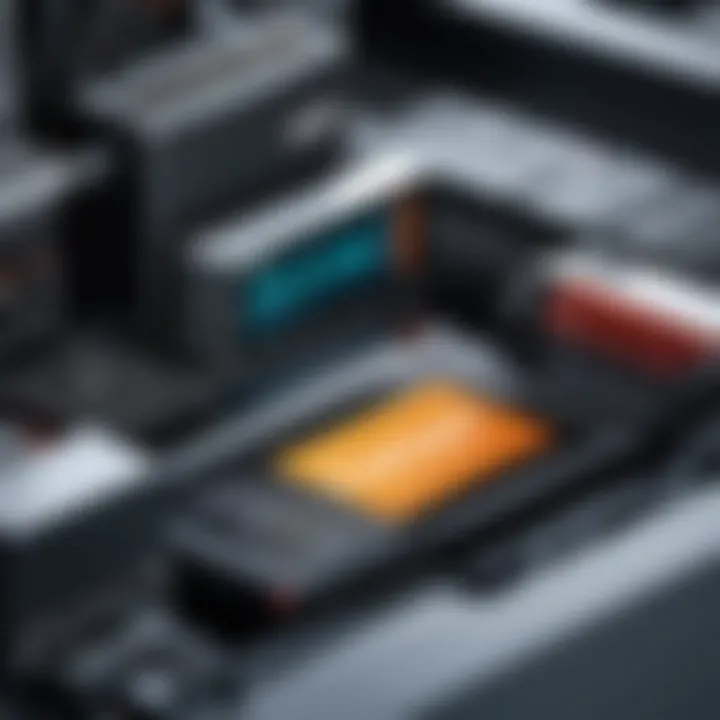
Intro
Maintaining Gardner Denver equipment is vital for ensuring operational efficiency and minimizing downtime. The maintenance reset process constitutes a critical element within this maintenance framework. Understanding this process is essential for maximizing the performance and lifespan of any gardening denver machinery.
This article outlines the key aspects of the Gardner Denver maintenance reset procedure, emphasizing its importance in the larger domain of maintenance strategies. In turn, it synthesizes the diverse components involved in effective reset execution through adept troubleshooting and regular maintenance practices. Ultimately, the goal here is to unlock the full potential of Gardner Denver equipment while upholding optimal workflows and robust productivity.
Technological Research Overview
Recent advancements in technology deeply influence the maintenance landscape. For Gardner Denver equipment, these innovations enhance predictive capabilities and equip users with better tools for ongoing maintenance tasks.
Recent Technological Innovations
From remote diagnostics to real-time monitoring, technological innovations play a significant role in preventative maintenance. Integration of IoT sensors allows operators to remotely contrast data and gain insights into equipment performance. These tools reduce the necessity for manual assessments, thus enabling faster decision-making upon data analysis.
Impact on Business Operations
These improvements positively affect business operations by fostering improved operational efficiency. Reduced downtime and faster issue resolution allow businesses to focus on productivity instead of merely reacting to unforeseen equipment failures. Such processes ultimately enhance profitability.
Future Technological Trends
Anticipated trends indicate a growing reliance on automation and advanced data analytics. Artificial Intelligence’s role is likely to escalate, optimizing not only only maintenance procedures but also influencing strategic decisions for future equipment investments.
"Innovation in maintenance reset procedures does not merely prolong equipment life; it transforms operational capacity at a foundational level."
Stride Towards Enhanced Maintenance Practices
As the industry evolves, maintaining Gardner Denver equipment requires a proactive approach rather than getting bogged in reactive modes. Understanding typical challenges operators face will illuminate better strategic execution throughout its service lifecycle.
By leveraging modern practices and embracing technological innovations, organizations can enhance their operational structure for Gardner Denver equipment integration.
Keywords: Gardner Denver, Maintenance Reset, Operational Efficiency, Technological Innovations
Understanding Gardner Denver Equipment
Understanding Gardner Denver equipment is essential for those who will be involved in its maintenance and operation. This knowledge helps ensure that the equipment operates efficiently and lasts longer.
Overview of Gardner Denver
Gardner Denver has a rich history in providing high-quality industrial equipment. It is renowned for its innovative solutions in compressor and pump technologies. The company's equipment is robust and designed to handle rigorous industrial demands. This reliability is crucial in applications across sectors like oil and gas, chemical, and manufacturing. Familiarizing oneself with Gardner Denver’s offerings promotes optimal use and enhances performance.
Essential aspects often examined in an overview include the engineering principles behind their machines, the adoption of modern technology, and the durability of materials used in their construction. Maintenance strategies rely heavily on comprehending these features.
Key Equipment Types
Gardner Denver supplies various equipment types, each meeting distinct operational needs. Some key types include:
- Rotary Screw Compressors: Known for their efficiency, they are widely used due to their continual airflow and quiet operation.
- Reciprocating Compressors: These are essential for high-pressure applications and provide precision.
- Blowers: Employed in aeration processes, they enhance gas emissions control in many industries.
- Vacuum Pumps: Crucial in creating vacuum levels needed in laboratories and manufacturing scenarios.
In-depth familiarity with these types of equipment allows users to make better decisions regarding maintenance. Knowing specific machinery requires more frequent servicing or has particular vulnerabilities is vital for a successful maintenance strategy. Each type also has its own set of performance metrics, maintenance schedules, and operational recommendations that can impact overall efficiency and longevity of use.
Maintenance Fundamentals
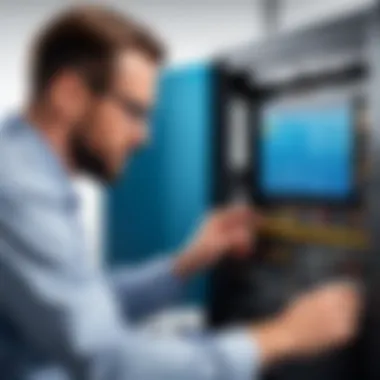
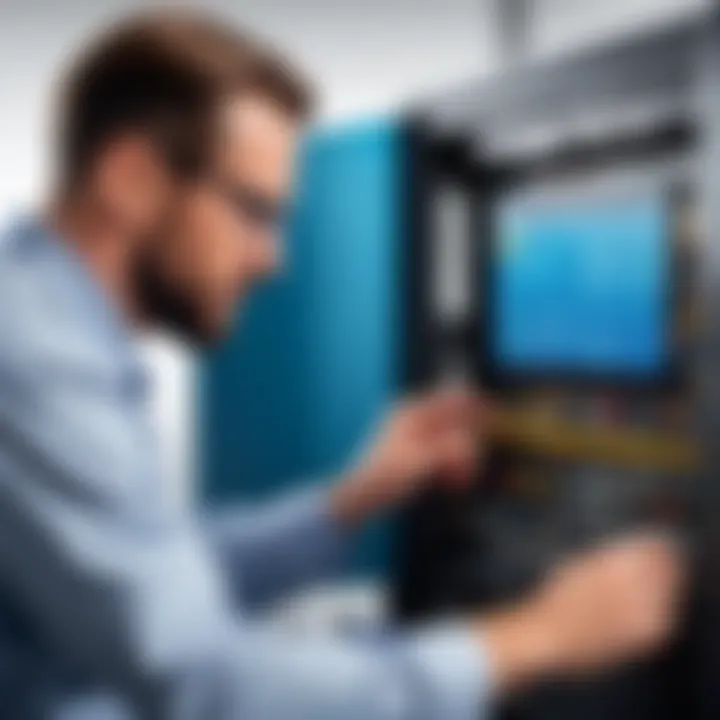
Importance of Maintenance
In any industrial setting, maintaining equipment is not merely a matter of preference; it is a fundamental requirement for operational success. The importance of maintenance for Gardner Denver equipment cannot be overstated. Each piece of equipment works under considerable stress, and neglect can lead to significant operational delays and expenses. Regular maintenance checks help in averting breakdowns that could halt production. They ensure the machinery operates at peak efficiency, driving productivity and reducing the total cost of ownership.
A well-maintained system reduces risks associated with failures, protects the investment in the equipment, and heightens safety in the workplace. From air compressors to blowers, ensuring the mechanical and operational wellness of machinery is vital. Proactive rather than reactive approaches to maintenance guarantee organizations can respond to small issues before they escalate.
Long-term Benefits of Regular Maintenance
Regular maintenance yields multiple long-term benefits that resonate well beyond immediate operational needs. Firstly, it extends the lifespan of the equipment by maintaining its parts in optimal condition. Regular checks and servicing carry the potential to identify wear or faults early. When addressed in time, these issues can often be remedied without requiring extensive replacements, thereby preserving capital.
Moreover, there is enhanced reliability and performance precision. With consistent upkeep, equipment can provide sustained and efficient performance, reducing downtime significantly. Improvement metrics, such as efficiency rates and output quality, can be noticeably observed. Consistency leads to stronger customer satisfaction and reliability.
The business gains far broader advantages with diligent maintenance practices, impacting reputation and competitive standing within the industry. Overall, organizations recognize that investing time and resources in a disciplined maintenance program pays dividends in operational capacity and maintained trustworthiness.
What is a Maintenance Reset?
A maintenance reset serves as a crucial juncture in the lifecycle of Gardner Denver equipment. It refers to a systematic reassessment and, if necessary, recalibration of service indicators, operational settings, and performance metrics post-maintenance check. This procedure ensures that the machinery always operates at an optimal level, contributing to longevity and reliability.
Incorporating the maintenance reset into standard operating procedures aids in identifying both existing and potential operational drawbacks. Neglecting this practice can lead to increased wear and tear, compounded downtime, and excessive repair involvement, owning to unmet machinery specifications. Thus, its relevance cannot be overstated.
Definition of Maintenance Reset
A maintenance reset is more than simple upkeep; it's essentially a comprehensive review and calibration process instituted immediately after routine or emergency maintenance has taken place.
This process comprises:
- Re-evaluation of Performance Metrics: The core performance criteria of the equipment may need reassessment to align with current operational capacities.
- Adjusting Service Period Indicators: Indicators for future services or check-ups are often reset to appropriate levels, preventing misinformed operational beliefs.
Implementing a consistent maintenance reset not only champions performance but also inspires a proactive approach toward using Gardner Denver's equipment, thus aligning practical use with industry standards.
Triggers for a Maintenance Reset
Understanding when to perform a maintenance reset is intrinsic to equipment management standards, particularly for those frequently reliant on Gardner Denver products. Various triggers can initiate this resetting process, including:
- Completion of Scheduled Maintenance: Regular systematic checks should prompt a reset, ensuring that equipment is ready for the next operational cycle.
- Outreach for Technical Indicators: Certain alarms or performance indicators might signal a reset cycle.
- Change in Workload or Environment: Drastic variations can necessitate adjustments in performance settings, highlighting the need for a recalibration of machinery settings.
Recognizing and acting on these triggers optimizes performance and eliminates disruptions caused by the oversight of essential technical indications.
Executing a Maintenance Reset
Executing a maintenance reset is a critical component in the effective management of Gardner Denver equipment. The primary objective is to ensure that the machinery remains operational at its best capacity while minimizing issues that develop from wear and usage over extended periods. This section emphasizes the key elements of a maintenance reset, highlights its numerous benefits, and outlines vital considerations that one must keep in mind during the execution of the reset process.
A maintenance reset serves multiple purposes. First, it helps restore the specific conditions under which the equipment operates optimally. Many components of the machines have predefined thresholds, and once these are crossed, performance can decline. Performing a maintenance reset pushes these thresholds back to a starting point, providing a fresh baseline for future monitoring and measurements.
Additionally, a maintenance reset can trigger diagnostic checks and recalibrate settings for machinery, ensuring efficiency in the operating process. Addressing issues proactively through a reset not only saves time but often can avert more significant problems down the line.
Step-by-Step Guide
When preparing to execute a maintenance reset, a systematic approach is paramount. Below is a general step-by-step guide that provides clarity on how to effectively carry out this process.
- Review Operational Manuals: It's critical to familiarize yourself with the specific guidelines provided by Gardner Denver for the equipment you're handling. Make sure to access the manual beforehand.
- Document Current Equipment State: Recording existing settings prior to reset allows for a clear comparison post-execution, also acting as a safety net if unexpected results occur.
- Perform Preliminary Inspections: Check for any visible issues prior to proceeding. This includes inspecting for leaks, unusual noise, or excessive wear.
- Shut Down the Equipment: Ensure that all machinery is safely turned off, and appropriate isolation procedures are in place.
- Engage the Reset Procedure: Use the equipment's specific settings or interface to engage the maintenance reset, aligning to the guidance of the operational manual.
- Monitor Each Step: After initiating the reset, observe parameters closely to ensure they align with expected results. Note any anomalies for further review.
- Calibrate Settings as Needed: Adapt settings if any readings indicate that the equipment isn’t functioning within optimal parameters following the reset.
- Conduct Post-Reset Testing: After completing the reset, conduct tests to verify performance. %Quality checks are critical at this stage.%
- Record Final Adjustments & Observations: Document all changes made during the reset. Including the initial findings will give insighful data for future maintenance sessions.
Tools and Equipment Needed
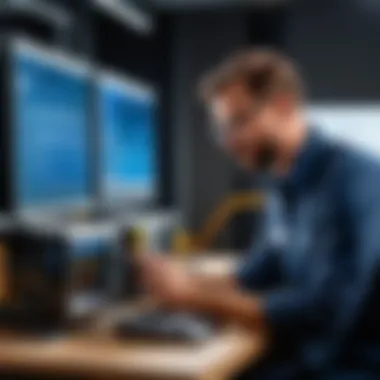
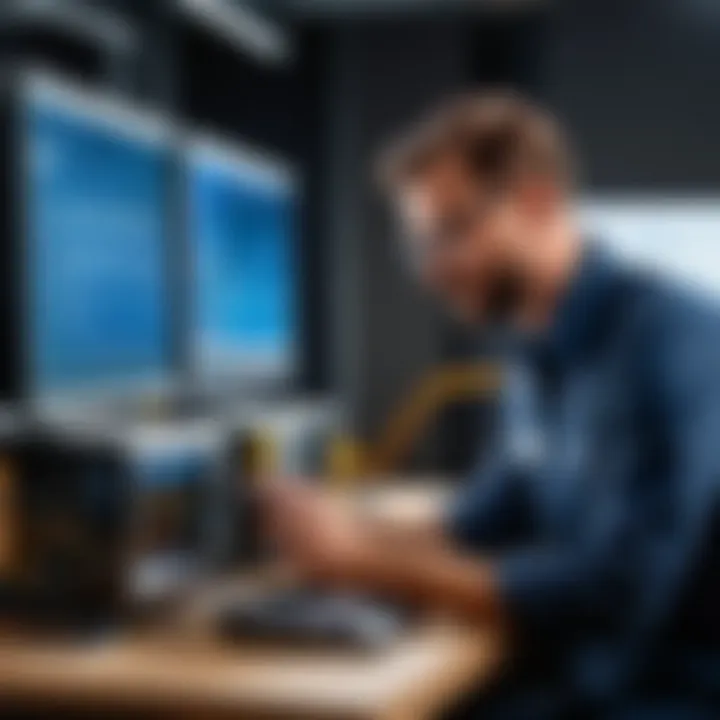
To successfully execute a maintenance reset, there are various tools and types of equipment necessary, tailored to the unique needs of Gardner Denver systems. Typically, these include:
- Hand Tools: Wrenches, screwdrivers, and pliers for minor adjustments.
- Diagnostic Tools: Equipment like multimeters or diagnostic software essential to monitor and evaluate the machinery's state.
- Safety Gear: Personal protective equipment like gloves, goggles, and earmuffs is vital for ensuring personal safety.
- Documentation Tools: For proper recording and documentation, tools such as a notebook or software applications assist in tracking details.
Common Challenges During Maintenance Reset
Addressing the potential challenges encountered during a maintenance reset is critical for operational success. A clear understanding of these challenges helps clear roadblocks and improves performance. Recognizing what can go wrong and being ready to formulate effective solutions allows for smoother
Importance of Regular Monitoring
Regular monitoring is an indispensable component of successful maintenance for Gardner Denver equipment. Properly managed monitoring of systems ensures not only the operational efficiency but optimizes the lifespan of the machinery. Failing to institute a structured monitoring process can result in undetected malfunctions, costly downtimes, and ultimately, loss of productivity.
Understanding the metrics that define performance is critical. Regular monitoring allows maintenance teams to track parameters that signal potential failures. By keeping an eye on temperature, pressure, flow rates, and other indicators, we establish a preventive approach rather than a reactive one.
Advantages of maintaining a solid monitoring system include:
- Enhanced Efficiency: Continuous observation prevents minor issues from escalating into more severe, costly problems.
- Cost Savings: Identifying and addressing concerns early leads to lower repair costs, reducing financial strain on operations.
- Consistency and Reliability: Equipment that is diligently monitored operates within specified parameters, improving overall reliability.
Overall, consistent monitoring is more than a best practice; it is a prerequisite for sustaning an operational framework that seeks to benefit from the advanced capabilities that Gardner Denver products deliver.
Establishing Monitoring Protocols
To create effective monitoring protocols, one must start by identifying key performance indicators relevant to specific machinery. This could mean designing a tailored metric system based on the operational requirements of the equipment. Protocols should clearly define what must be monitored and how often. For instance,
- Setting daily, weekly, or monthly checks, depending on operational activity, is a good starting point.
- Document all observations, create a regular feedback loop, and ensure this information get passed on to equipment operators.
Integration of human elements is essential. Educating staff on the importance of monitoring can ensure they remain vigilant and proactive. Well-informed employees can help contribute greatly to the completeness and accuracy of monitoring data.
Leveraging Technology for Monitoring
The advent of technology provides innovative opportunities for effective monitoring of Gardner Denver equipment. Implementing smart technologies diversifies the approach beyond manual checks. The following digital tools can significantly enhance monitoring efforts:
- Remote Monitoring Systems: These systems offer real-time insights into equipment status, helping to detect irregularities from any location.
- Data Analytics Software: Analyzing historical data can yield predictive insights important for maintenance planning.
- Mobile Applications: Providing up-to-the-minute updates directly to maintenance teams on their mobile devices helps streamline communication and response standards.
Incorporating technology not only enhances monitoring practices but also leads to better decision making based on documented historical performance.
In summary, elevating the processes into a continuous loop of monitoring and feedback cultivates an environment where equipment health can thrive, ultimately leading to improved performance and reduced breakdown risks.
Industry Best Practices for Maintenance
Establishing industry best practices for maintenance is crucial for the reliability and efficiency of Gardner Denver equipment. This framework is not merely procedural; it is a philosophy that aims to enhance equipment longevity and performance while minimizing downtime. Best practices are integral to structuring a sustainable approach to operational excellence. Effectively implementing these practices ensures the machinery performs seamlessly and helps organizations maintain their competitive edge.
Standard Operating Procedures
Standard Operating Procedures (SOPs) serve as the backbone of maintenance operations. These are detailed written instructions designed to achieve uniformity in tasks. In accordance with Gardner Denver standards, SOPs mitigate the risk of human errors that often lead to malfunctions or unexpected downtimes.
SOPs should specify:
- Routine Inspections: Schedule and execute systematic assessments of the equipment to catch issues before they escalate.
- Maintenance Frequencies: Timing guidelines for regular servicing and parts replacement to maximize the components' efficient lifespan.
- Safety Protocols: Clear protocols to ensure safety during maintenance activities reduce the risk of accidents and injuries.
- Documentation Practices: Maintain records of completed maintenance and repairs for accountability. These records inform future strategy adjustments and compliance needs.
By adhering to SOCs, organizations make informed decisions, cultivate proactive management, and cut costs related to repairs and consequential downtime.
Training and Skill Development
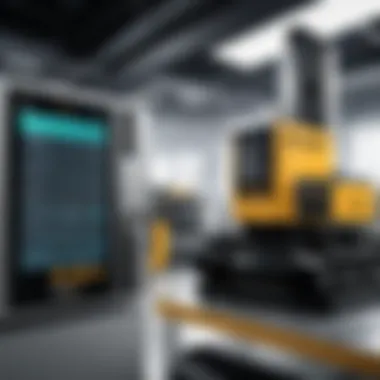
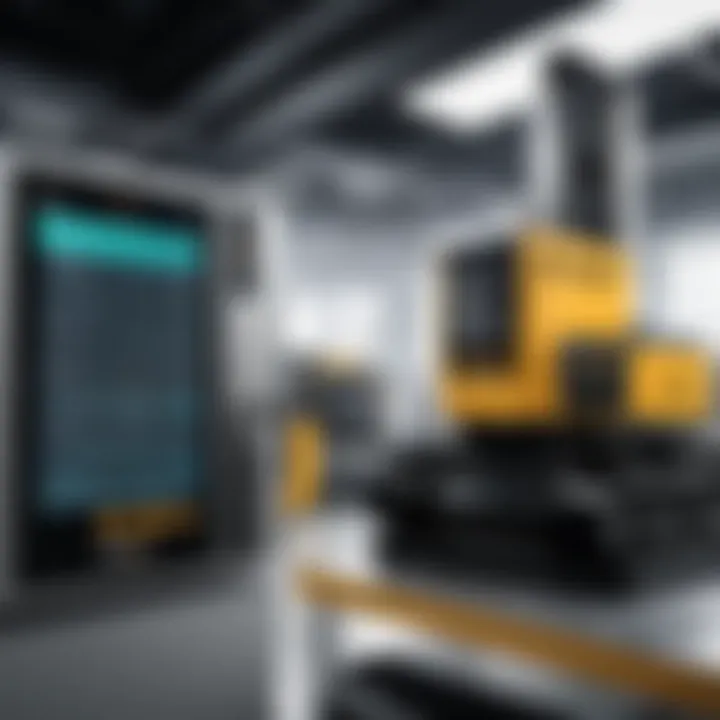
Continuously enhancing the competency levels of maintenance personnel is a cornerstone of successful operation. Training and skill development are not only pivotal; they are essential for overseeing complex maintenance tasks with expertise.
Organizations ought to invest in:
- Crew Training Programs: Regular workforce training ensures staff are current with the latest technologies and practices. Up-to-date knowledge reduces errors and enhances maintenance precision.
- Certification Incentives: Encouraging employees to gain certifications enhances professionalism in maintaining Bloom products. Recognition through certifications builds a sense of achievement that motivates staff.
- Workshops and Seminars: Participation in relevant workshops allows personnel to collaborate and share insights regarding emerging industry trends and technological advancements.
Market analysis reports underscore the direct correlation between a skilled workforce and lowered operation costs. Highly skilled technicians minimize errors, leading to fewer work interruptions and healthier net profit margins. All of nurturing this talent has long-term lucrative payoffs into the investment of worse systems.
It is essential to foster a culture of learning within the maintenance teams, as the knowledge gained translates into broader organizational success.
Evaluating Maintenance Effectiveness
Evaluating maintenance effectiveness is crucial for ensuring that Gardner Denver equipment operates at its peak potential. Regular assessment enables operators to identify how well maintenance strategies are working and what impacts they have on equipment functionality. This evaluation process includes both quantitative and qualitative measures that facilitate ongoing improvement.
One primary benefit of assessing maintenance effectiveness is the ability to optimize maintenance schedules, which can reduce downtime and repair costs. When effectiveness is measured accurately, operators can allocate resources more efficiently and can decide when to perform preventive maintenance versus reactive maintenance. Long-term success relies on making informed decisions based on these evaluations.
Moreover, by concentrating on maintenance effectiveness, companies can enhance their operational efficiencies. With insights drawn from data, teams can pinpoint recurring issues and recognize necessary modifications in their procedures. The end goal is to ddreepentaine a workflow that minimizes disruptions.
Case Studies in Successful Maintenance
Case studies serve as a valuable resource for understanding the practical applications of maintenance strategies. By examining specific instances where equipment, particularly Gardner Denver machinery, underwent effective maintenance resets, we can derive lessons and adapt best practices for future considerations. These studies highlight the significance of well-executed maintenance approaches, showcasing how they can enhance operational efficiency and reduce downtime.
Real-World Examples
There are several instances where companies utilizing Gardner Denver equipment benefitted from maintenance resets. One notable example involves a manufacturing facility in the Midwest that regularly faced issues with pump performance due to neglecting maintenance practices. The facility decided to implement a structured maintenance reset strategy. This approach included a thorough evaluation of all monthly, quarterly, and annual maintenance schedules. Over the course of this operation, the facility saw a significant increase in the efficiency of their pumps, reducing downtime by nearly 25%.
Another example comes from a logistics company that relied heavily on Gardner Denver compressors. Ten months post-integration of a maintenance reset procedure, the company recorded fewer incidents of equipment failure. They documented their findings and attributed the reduction in operational risks to timely inspections and part replacements, highlighting the benefits of effective maintenance planning.
Lessons Learned
The outcomes of these case studies underline the importance of developing a proactive maintenance culture where employees prioritize equipment wellness. Several key lessons are evident:
- Regular Monitoring: Consistent oversight of equipment performance is crucial. It helps identify wear and tear before they lead to failure.
- Documentation: Keeping detailed records of maintenance activities and outcomes provides analytical insight for continuous improvement. This practice clarifies what works and allows for adjustments to maintenance strategies when necessary.
- Employee Training: Staff education is imperative. By ensuring that employees understand both the equipment and the maintenance reset processes, companies can greatly improve the efficiency of these procedures.
- Adaptability: Every facility is different. Tailoring maintenance reset efforts to meet the specific needs of the operation is vital.
A maintenance culture that emphasizes foresight and preparation can not only prolong equipment lifespan but also enhance productivity.
These case studies illustrate the serious advantages of adhering to rigorous maintenance protocols. They reinforce the notion that successful maintenance is not just about following procedures; it involves creating systems that foster continuous learning and adaptation.
Epilogue
In any technical context, understanding the importance of a thorough conclusion cannot be underestimated. Within this article, the concluding section draws together threads discussed through various facets of maintaining Gardner Denver equipment, particularly focusing on the maintenance reset protocol. This final evaluation ensures that the reader comprehends key insights and strategies uncovered throughout the discourse.
Recap of Key Points
A concise overview of the major points reaffirms essential knowledge:
- The maintenance reset is critical for optimal operation.
- Early and repeatable care ensures longevity of the equipment.
- Identifying and addressing issues proactively can minimize downtime.
- Employing industry best practices enhances operational efficiency.
- Continuous monitoring coupled with relevant technology underpins effective maintenance.
By muscling through to these highlights, professionals can move confidently forward in employing these strategies to maintain their Gardner Denver equipment effectively.
Future Perspectives on Maintenance Practices
As technology progresses, the landscape of maintenance practices is also evolving. The integration of artificial intelligence and IoT devices presents distinct opportunities for organizational efficiency and machine longevity. Future foresight might focus on:
- Predictive Maintenance: Transitioning from reactive to proactive strategies can bolster availability.
- Data-Driven Decisions: Utilizing metrics captured by software for real-time analysis can drastically improve workflow.
- Sustainable Operations: Emphasizing efficiency also aligns with responsible resource management, a growing demand in today’s industries.
The path ahead for maintenance practices is marked by innovation. Implementing these forthcoming shifts ensures not just adherence to standards, but also augments profitability.
In summary, the commitment to a well-structured maintenance approach is pivotal. This responsibility doesn't stop with resetting protocols; it instills a culture of continuous improvement.