Transforming Manufacturing: The Impact of Information Technology
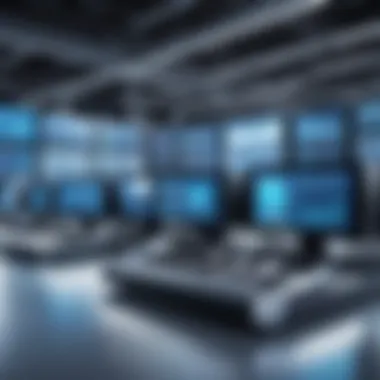
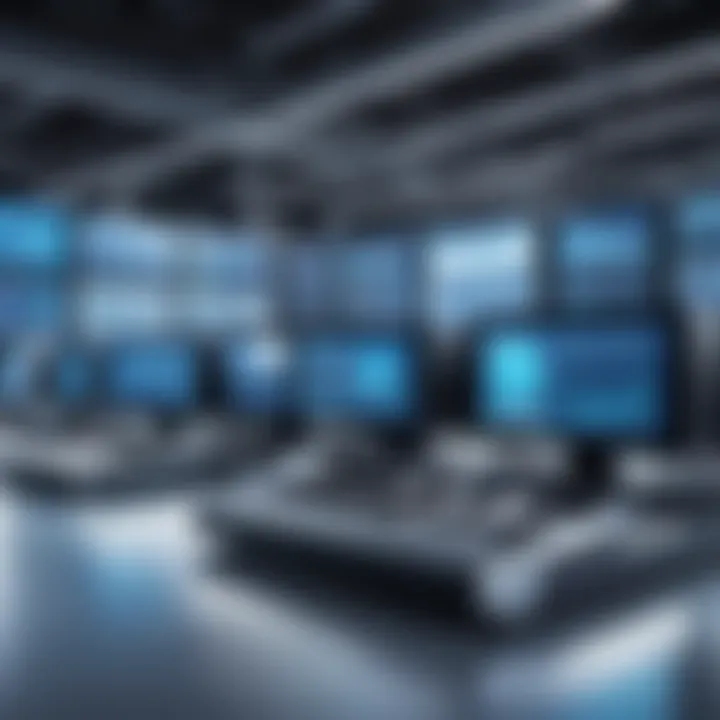
Intro
Information Technology (IT) serves as the backbone of modern manufacturing. As industries evolve, the integration of IT into manufacturing processes has proven vital for companies seeking to stay competitive. This article delves into how technology streamlines operations, facilitates enhanced productivity, and promotes innovative solutions that fundamentally reshape the manufacturing landscape.
Technological Research Overview
The intersection of technology and manufacturing is rich with opportunities. Understanding technological advancements can provide insights into how organizations can make informed movements within the rapidly changing market.
Recent Technological Innovations
Innovations in IT have transformed traditional manufacturing methods. Significant advancements include:
- Automation frameworks: Implementing robotic systems enhances speed and precision.
- IoT (Internet of Things): Facilitates real-time data collection, improving object tracking and inventory management.
- Cloud computing: Offers scalable solutions for data storage and processing needs.
This integration positions organizations to operate more efficiently and effectively.
Impact on Business Operations
Enhancement in manufacturing is primarily driven by optimized processes. By adopting new technologies, businesses can gain a clearer picture of their operations. This clarity affects various levels such as:
- Resource management: Improved allocation results in reduced waste and costs.
- Quality control: Continuous monitoring leads to consistent product quality.
- Supply chain management: Refined tracking ensures a more responsive supply chain.
Future Technological Trends
As we look ahead, several trends stand out in the IT-manufacturing relationship:
- Rise of additive manufacturing.
- Expanded use of machine learning to refine processes.
- More extensive implementation of blockchain technology for transparency.
These trends signal a shift toward more integrated and intelligent operational frameworks.
Data Analytics in Business
The vast amounts of data generated in manufacturing processes offer valuable insights. Data analytics is essential in identifying patterns and informing decisions.
Importance of Data Analytics
Harnessing data allows for:
- Improved decision-making.
- Enhanced operational efficiency.
- Comprehensive customer insights.
Tools for Data Analysis
Several tools facilitate effective data analysis, including:
- Microsoft Power BI: Offers dependable reporting solutions.
- Tableau: Provides data visualization for easier understanding.
- Google Analytics: Helps monitor customer interactions with products.
Case Studies on Data-Driven Decisions
Notable companies have successfully utilized data for decision-making. For instance, Ford leverages data analytics to assess efficiency in assembly lines, leading to better allocation of human resources and machinery.
Cybersecurity Insights
With increased IT adoption in manufacturing, cybersecurity cannot be overlooked. The digitalization of processes does present threats that must be managed adequately.
Threat Landscape Analysis
Potential threats include:
- Ransomware attacks.
- Phishing to gain unauthorized access.
- IoT vulnerabilities.
Best Practices for Cybersecurity
Implementations for mitigating these threats incorporate:
- Regular software updates.
- Worker training on security protocols.
- Establishing a response plan for breaches.
Regulatory Compliance in Cybersecurity
Additionally, organizations must adhere to regulations such as GDPR, safeguarding user data while maintaining trust.
Artificial Intelligence Applications
Artificial Intelligence shapes the future of manufacturing through automation and analytics.
AI in Business Automation
By deploying AI, companies can:
- Automate routine tasks.
- Predict maintenance needs.
- Optimize logistics.
AI Algorithms and Applications
Common AI applications transform operations. For example:
- Predictive maintenance models using algorithms reducing downtime.
- AI-driven demand forecasting supporting production planning.
Ethical Considerations in AI
As AI expands in manufacturing, ethical concerns must be addressed. Issues like job displacement and transparency in decision-making warrant conversation among industry leaders.
Industry-Specific Research
Technological advancement is industry-specific. Each sector possesses distinct needs and benefits.
Tech Research in Finance Sector
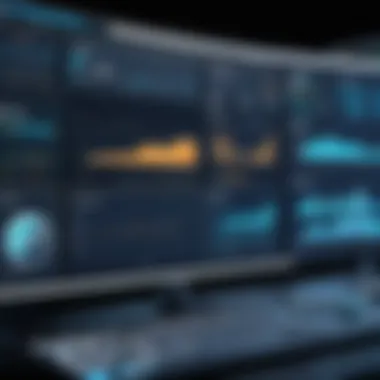
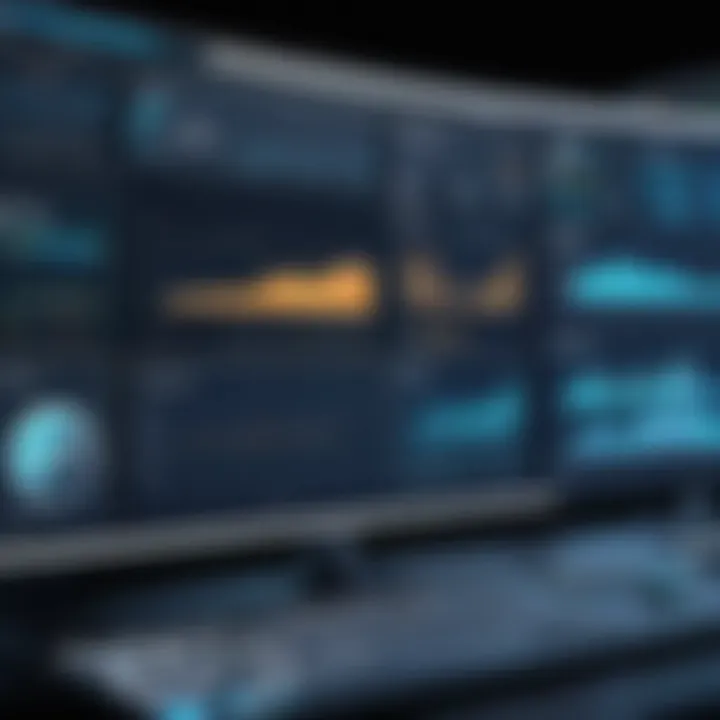
Financial technologies simplify transactions and risk management. Companies utilize advanced algorithms for fraud detection.
Healthcare Technological Advancements
Manufactured medical devices feature reliable sensors and connectivity for patient monitoring, enhancing care efficiency.
Retail Industry Tech Solutions
The retail sector often implements IT for inventory and supply chain management. Helpful processes include mobile checkout systems and predictive inventory analytics.
The integration of information technology into manufacturing prepares companies for sustainable growth. Focusing on efficiency and data-driven decisions while considering future trends promotes resilience in a dynamic environment.
Prolusion to Information Technology in Manufacturing
In today's rapidly evolving industrial landscape, the role of information technology (IT) in manufacturing is undeniable. As companies push the boundaries of productivity and innovation, IT emerges as a key enabler. It fundamentally transforms traditional manufacturing processes by streamlining operations, facilitating real-time decision-making, and supporting data-driven strategies. Without integrating IT effectively, manufacturers risk falling behind in a marketplace where agility and responsiveness are critical.
The importance of understanding the role of IT extends beyond mere implementation. Organizations must grasp how it integrates into their day-to-day functions, offering solutions to complex challenges. Furthermore, valuing IT not only raises operational efficiency but also leads to better management of resources, ultimately resulting in enhanced competitive advantages. Manufacturers who leverage IT gain insights into customer demand, optimize supply chain workflows, and drive continuous improvement in product quality.
Definition and Scope
Information technology in manufacturing can be defined as the use of computer systems, software, and networks to manage, analyze, and optimize the various processes involved in manufacturing. This field encompasses a wide range of practices from enterprise resource planning systems that manage assets to advanced data analytics tools that predict market trends. The scope of IT in manufacturing also includes facets such as automation, integration of IoT devices, and implementation of machine learning for predictive maintenance.
As innovation progresses, IT continues to adapt. It is no longer a supportive element but the backbone of modern manufacturing operations. In robust productions, distinguishing narrow definitions becomes less relevant, as the vital intersections between data gathering, processing, and actionable insights widen effectively.
Historical Context
To appreciate the current impact of IT on manufacturing, it is necessary to consider its historical evolution. The manufacturing sector has undergone significant transitions over time. From the inception of mechanization in the 18th century to the advent of automation in the 20th century, each shift in technology set the stage for the next wave of efficiency improvements.
Initially, the introduction of simple machinery automated repetitive tasks. Then, the advent of computing technology led to significant optimization of operations. The late 20th and early 21st centuries saw the rise of complex systems that generated enormous amounts of data. This accumulation opened doors to what we term Industry 4.0, where connectivity between machines and IT creates a foundation for enhanced production capacity.
Understanding this progression offers insight into the potential of IT solutions today. A historical perspective enables manufacturers to recognize both the challenges overcome and the new landscapes that emerge with the adoption of innovative technologies.
Modern Manufacturing Techniques
Modern manufacturing techniques exemplify how information technology (IT) can reshape production environments. These techniques focus on efficiency and adaptability, utilizing advancements to streamline operations and reduce waste. Companies that embrace these methodologies find they can improve output quality and maintain competitive pricing. As IT integrates into manufacturing, the potential to not only meet but exceed market demands becomes more pronounced.
Lean Manufacturing
Lean manufacturing aims to maximize customer value while minimizing waste. It utilizes processes that promote efficiency, emphasizing continuous improvement and respect for people. Organizations adopt lean concepts to produce goods with less effort and fewer resources. This systematic approach enables manufacturers to streamline operations and cut unnecessary costs.
Some notable principles of lean manufacturing include:
- Value Stream Mapping: Identifying all the actions in a value stream to determine which ones add value.
- 5S Methodology: Sort, Set in order, Shine, Standardize, and Sustain approaches help maintain a clean and organized workspace.
- Kaizen: This philosophy encourages small, continuous improvements rather than large changes at once.
Implementing lean strategies can lead to higher productivity and lower operational costs. Manufacturers showcasing lean practices often see improvements in customer satisfaction through quicker response times and enhanced product quality.
Flexible Manufacturing Systems
Flexible manufacturing systems (FMS) enable a factory to machine a variety of parts without a loss of efficiency. Such systems rely on information technology to link machines, manage processes, and result in a highly adaptable production floor.
Key benefits of FMS include:
- Product Variety: Companies can produce different products simultaneously, enabling better responsiveness to market shifts.
- Reduced Setup Times: Quick reconfiguration processes enable manufacturers to switch from one product to another swiftly, minimizing downtime.
- Initialization and Engineering: IT allows for easy programming of machinery, which enhances the initial setup process and reduces the need for skilled labor on the factory floor.
Through flexible manufacturing, businesses can efficiently adapt to changing demands, significantly boosting overall flexibility and productivity.
Just-in-Time Production
Just-in-time production (JIT) is a strategy that aligns inventory levels with production schedules. This system minimizes waste by receiving goods only as needed. By reducing inventory holding times, JIT improves cash flow and decreases storage costs. Moreover, it synchronizes production with demand, preventing overproduction and excess inventory.
The main features of JIT include:
- Demand-Driven Approach: Goods are produced based on current demand, which aligns production closely with customer needs.
- Strong Supplier Relationships: JIT requires reliable suppliers who can deliver materials on schedule.
- Focus on Quality: Consistently monitoring production processes leads to improvements in quality, as defects can be identified more rapidly.
JIT can drastically improve a company's accuracy in forecasting and can elevate their operational efficiency, thus delivering products faster to the market.
Implementing modern manufacturing techniques enhances operational efficiency and realizes robust cost savings. Companies adopting these approaches are better positioned for future profitability and growth.
Key Technologies in IT for Manufacturing
Information technology is reshaping the manufacturing landscape. Key technologies play a vital role in this transformation. They not only streamline operations but also enable manufacturers to respond to market demands more rapidly. As companies face increasing pressures to improve efficiency and reduce costs, adopting these technologies becomes crucial. It’s important to understand these technologies, their benefits, and their application in production systems.
Automation and Robotics
Automation is essential in modern manufacturing. It refers to using control systems for machinery to operate processes with minimal human intervention. Today, robotics is integrated in various facets of this industry. Robotic arms, for instance, assemble, paint, and package products effectively.
The benefits of automation androbotics include:
- Improved precision and consistency in production.
- Faster production times, enhancing overall throughput.
- Reduction in labor costs, allowing companies to reallocate resources.
However, implementation is not without considerations. High costs of purchasing and maintaining these technologies can be a barrier. Additionally, companies need to ensure their workforce is appropriately trained to work alongside these systems.
Internet of Things (IoT)
The Internet of Things has elevated manufacturing capabilities by connecting devices and collecting real-time data for analysis. IoT sensors are deployed across various operations, providing insights into equipment performance, inventory levels, and overall conditions.
The importance of IoT lies in:
- Enhancing predictive maintenance; reducing unplanned downtimes
- Optimizing resource usage, leading to lower operational costs
- Supporting better decision-making through real-time data
Data from IoT devices creates an interconnected system that benefits manufacturers greatly. Those who leverage these tools position themselves ahead of competitors.
Big Data and Analytics
Big data is not just a buzzword; it is a cornerstone of modern manufacturing. Large volumes of data are generated every minute, necessitating robust analytics tools to leverage this information effectively.
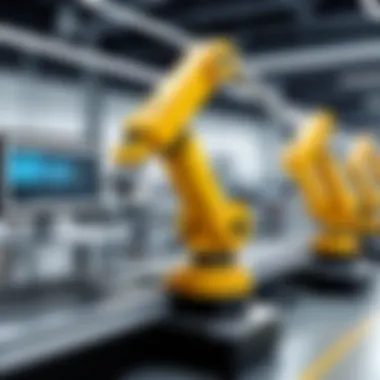
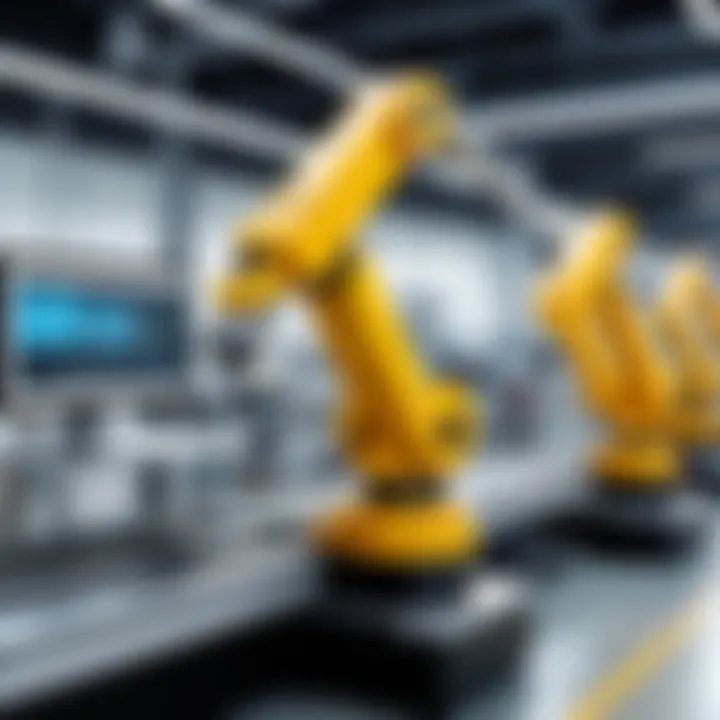
Engaging in analytics tools allows businesses to:
- Identify inefficiencies in production processes.
- Improve forecasting and planning by analyzing historical and real-time data.
- Enhance product quality through consistent monitoring of product specifications.
Manufacturers who incorporate big data can achieve significant competitive advantage. Their ability to respond quickly to market changes leads to heightened flexibility and customization capabilities.
Cloud Computing
Cloud computing provides a valuable platform for storing and sharing massive amounts of data. It enables remote access to information and applications, facilitating collaboration among teams regardless of geographical limitations.
The benefits offered by cloud computing are manifold:
- Scalability: Companies can adapt their computing needs based on operational changes.
- Cost-effectiveness: Deferred capital expenditures and reduced maintenance costs.
- Enhanced disaster recovery options to secure data integrity
Given the central role of data in manufacturing, utilizing cloud technology effectively becomes a necessity.
Artificial Intelligence and Machine Learning
Artificial intelligence and machine learning empower systems to learn from data and improve operations over time. These technologies drive intelligent decision-making processes that optimize every aspect of manufacturing.
Key aspects of AI and machine learning include:
- Automation of complex processes that respond to real-time variables.
- Advanced analytics capabilities that forecast trends more accurately.
- Enhanced human-machine collaboration, reducing risk of errors
Incorporating AI and machine learning creates smarter manufacturing processes that can predict issues before they arise. Consequently, businesses will become adaptable and stay relevant.
All these technologies collectively contribute to a paradigm shift in manufacturing, improving output while reducing costs.
Impact of IT on Manufacturing Efficiency
The integration of information technology (IT) into manufacturing processes has fundamentally shaped the operations of modern factories. Achieving high manufacturing efficiency is crucial for staying competitve in an ever-evolving marketplace. Manufacturing firms harness IT to optimize manufacturing processes, thus enhancing overall operational performance.
“IT transforms activity in the manufacturing industry enabling cost reduction, faster response times, improved quality, and supports a more sophisticated production framework.”
Enhancing Productivity
IT plays a key role in boosting productivity. Automation systems reduce the repetitive workload on human workers, allowing them to focus on higher-level tasks. Technologies such as robotics have increased assembly speed and consistency while minimizing human error. Furthermore, using data analytics provides managers valuable insights into worker performance and machinery effectiveness. This enables informed decision-making about workflow improvements.
Additional strategies such as real-time monitoring through IoT devices permit proactive maintenance, promoting a seamless operational flow. When employees have access to accurate data fueled by IT infrastructures, they can perform tasks more effectively and significantly increase output levels.
Reducing Downtime
Downtime is a manufacturer’s Achilles' heel. Unplanned halts not only disrupt production but also inflate costs. IT solutions can effectively mitigate this issue. Through predictive maintenance analytics, manufacturers foresee equipment failures that impede progress. Additionally, software tools are available to track operational performance and identify bottlenecks. By addressing these promptly, organizations cut potential downtime and ensure continuous manufacturing.
Regularly scheduled maintenance guided by IT systems prevents unexpected interruptions. As efficiency increases, plants become transformed into environments with reliable uptime metrics, promoting overall effectiveness in manufacturing strategies.
Optimizing Supply Chains
Today's supply chains are intricate networks reliant on precise logistics and information flow. IT provides the frameworks needed for this complexity. By employing blockchain, manufacturers track real-time inventory, providing transparency for all stakeholders. Areas of potential inefficiency become easily identified.
Moreover, analytics platforms allow firms to analyze supply chain data. Through this, they adjust operations based on customer demand and market variations. Just-in-time methodologies further support optimization, aligning inventory closely with production schedules. When the information circulates seamlessly from suppliers to manufacturers, the feedback loops minimize waste and maintain lean practices.
In summary, maximizing IT integration leads to remarkable enhancements across production levels in manufacturing firms. By recognizing and capitalizing on these advantages, companies will remain agile and competitive, in future-focused landscapes.
Challenges in Implementing IT in Manufacturing
Implementing information technology in manufacturing offers numerous advantages, but it is not without significant challenges. Understanding these hurdles is critical for minimizing risks and maximizing potential benefits. Firstly, businesses wo not only deal with upping control over operational costs and efficiency but also manage transitions that leverage new technologies. An awareness of these chilling problems helps position organizations for successful growth and adaptability.
High Initial Costs
The significant investment required for IT infrastructure can be a leading question among manufacturers. Buying hardware and software might not seem to much of a big deal individually, but combined together — plus eventual maintenance and upgrades — the costs mount steeply. Many companies may struggle to justify these expenses against their immediate needs, especially in the light of slim profit margins. Implementing solutions such as machine learning systems or advanced analytics may confer distribution advantages, but undertaking requests a careful budgeting strategy from initiation to execution. This does not explain certain tools but can span longer implementation times
To avoid overwhelming a budget, companies can consider alternatives such as:
- Phased implementation that allows a series of gradual improvements.
- Leasing equipment instead of purchasing outright.
- Government grants or loans specifically designed for technology upgrades.
The financial sacrifice today may lead to efficiency gains tomorrow.
Workforce Resistance
The integration of IT fundamentally changes workplace procedures, often creating resistance among employees accustomed to past methods. Fear of job loss, complexity of new tools, and stress about adapting can all contribute to reluctance. In this realm, employee education becomes particularly critical. Having constructive dialogues that underline benefits and enhance trust could potentially soothe fears. Training cannot be neglected, as knowledgeable staff would bridge the divide between old practices and the newly adopted industry standards.
An effective strategy to manage resistance might include:
- Engaging workers early in the implementation process to gather their insight.
- Providing comprehensive and interactive training sessions.
- Establishing continuous support mechanisms to ease adaptation.
Cybersecurity Risks
As manufacturers embrace greater connectivity, uncertainties surrounding cybersecurity arise. The adoption of advanced digital tools introduces more entry points that could be exploited, and protecting sensitive information is paramount. A single security breach could compromise large amounts of critical operational and personal data, leading to possibly severe repercussions.
Not only are manufacturers tasked with safeguarding against potential breaches, but they also need to ensure compliance with regulations, further complicating their imperative. Implementing robust security measures before, during, and after the adoption of IT solutions is a necessary step for reliance and trust in their processes.
Essential safeguards involve:
- Conducting regular vulnerability assessments.
- Implement software solutions focused on cybersecurity, such as firewalls and intrusion detection.
- Training employees about best practices for digital security.
By comprehensively addressing these challenges in successfully incorporating IT within the manufacturing landscape, organizations can create resilient strategies that focus on not only overcoming obstacles but ultimately achieving efficiency, productivity, and cybersecurity.
Future Trends in IT for Manufacturing
Understanding the future trends in information technology for manufacturing is crucial for any professionals or businesses aiming to remain competitive. The manufacturing sector is increasingly defined by its technological capabilities. As industries embrace these changes, it's vital to identify emerging trends that hold the potential to transform operations both in the short and long term. Through innovations such as sustainable practices, Industry 4.0 advancements, and augmented reality integratio, manufacturers can enhance productivity while navigating complexities of the modern economy.
Sustainable Manufacturing Practices
Sustainable manufacturing practices focus on minimizing negative impacts to health and environment while enhancing economic sustainability. These practices often encompass the adoption of green technologies and eco-friendly materials in production processes.
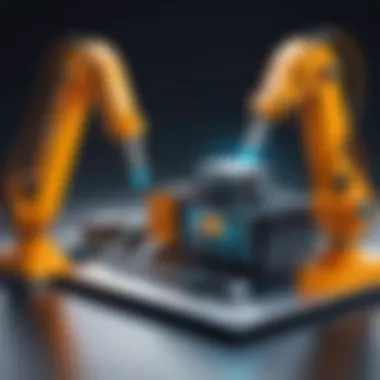
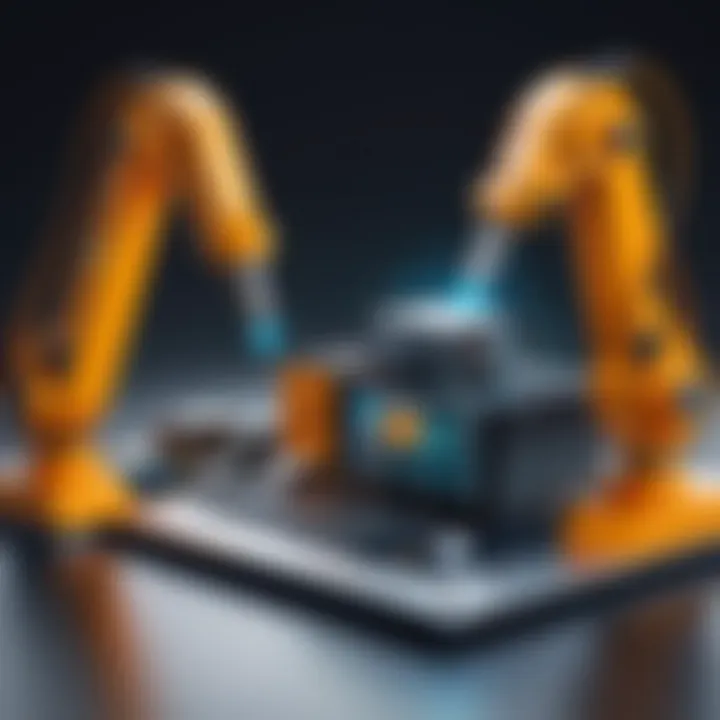
A key benefit includes reduced waste and energy consumption, which directly contributes to cost savings. Moreover, complying with regulations related to sustainability is becoming increasingly essential. By embracing sustainable practices, companies not only revamp their operational frameworks but also enhance their brand image, appealing to environmentally conscious consumers.
Successful sustainable initiatives often involve:
- Investments in energy-efficient machinery
- Utilization of renewable energy sources like solar or wind
- Implementing closed-loop systems to recycle waste materials
It's clear that sustainable manufacturing is not just a moral imperative; it is becoming a competitive advantage.
Advancements in Industry 4.
The term Industry 4.0 embodies the fourth industrial revolution, characterized by the merging of the physical and digital worlds. Significant advancements under this category revolve around technologies like IoT, big data, and cloud computing.
Impact from Industry 4.0 is overarching. Real-time data availability empowers dynamic decision-making, streamlining processes significantly. Automation systems work in conjunction with human effort to optimize production cycles specializing on quality control and defect detection.
Some benefits of Industry 4.0 adoption include:
- Enhanced flexibility in operations
- Improved supply chain management through connectivity
- Higher product customization capabilities leading to increased customer satisfaction
Integrating Industry 4.0 principles aligns a company’s operational capabilities with current and future market demands, presenting an opportunity to innovate continuously.
Integration of Augmented Reality
Augmented reality (AR) is an exciting frontier in manufacturing information technology. It presents real-time data visualization through overlays on the natural world. For manufacturers, this means higher operational efficiency and enhanced training methods.
Through AR, workers can learn complex assembly tasks or repairs with digital overlays, fostering a quicker learning curve and reduced errors during production. In addition, AR can improve remote assistance in troubleshooting by enabling experts to see exactly what onsite personnel experience without traveling.
Factors supporting the growing utilization of AR in manufacturing include:
- Enhancement of training protocols leading to improved safety
- Reduction of machinery downtime via real-time fault diagnosis
- Immediate access to operational data and support materials
A manufacturing environment integrating AR promotes not just productivity but also employee engagement, preparing personnel for future work tasks in a technologically advanced surroundings.
"As technology evolves, so too does the potential for how decisions can be informed,222222ee234 which ensures that manufacturing practices remain robust and forward-thinking."
Case Studies of Successful IT Implementation
The analysis of real-world case studies serves a critical role in understanding the practical benefits of information technology (IT) in manufacturing. Businesses worldwide have integrated various technologies to enhance their operations. These examples provide tangible evidence of how IT transformation can streamline processes, reduce costs, and create competitive advantage.
Examples from diverse sectors reveal various successful strategies and implementations that underscore the pivotal role technology plays. By examining specific instances, manufacturers can discern best practices and common pitfalls, identifying pathways to optimize their technology adoption strategies.
Leading Automotive Manufacturers
Automotive manufacturers have often been at the forefront of tech implementation in the manufacturing arena. Industry leaders like Toyota, Ford, and Tesla have shown the way towards integrating advanced IT solutions.
- Toyota Production System (TPS):
Toyota has long been known for its revolutionary management philosophy. Their TPS employs a variety of IT systems focused on lean manufacturing, helping reduce waste andstreamline processes. Digital tools monitor supply chains and shop floor operations. The use of real-time data analytics improves decision-making across all levels. - Ford Motor Company:
Ford has integrated smart factory technologies to refine its production lines. The employment of automation robotics in assembly lines has visibleitbly increased efficiency. Also, Ford’s extensive IoT implementation allows for seamless communication between vehicles and the manufacturing process, ensuring quality and performance. - Tesla’s Innovation:
Tesla’s factories utilize artificial intelligence for predictive maintenance synchronizing vehicles with data-driven decisions to enhance production capability. The use of advanced robotics combined with software tools reduces time and increases output.
These examples suggest that the auto sector not only embraces IT but also capitalizes on advancements to produce superior-quality products efficiently. Thus, as global competition rises, lessons learned from these leading manufacturers provide invaluable insights.
Electronics Industry Innovations
In the electronics industry, companies like Samsung and Intel have showcased cutting-edge applications of IT that fundamentally reshape manufacturing landscapes.
- Samsung:
Samsung has continually adopted predictive analytics to ascertain consumer trends. Their factories employ smart devices linked through the internet, which optimize assembly processes. For instance, data collected during manufacturing helps optimize logistics, therefore saving time and resources while adapting to changing demands. - Intel:
With their movement towards smart factories, Intel has embraced comprehensive automation solutions involving digital twins of production lines. These representations allow real-time tweaks that improve precision. Their application of big data analytics provides insights on failure points in production before they occur.
As these examples illustrate, the electronics sector highlights substantial benefits from the integration of IT in their manufacturing processes, showcasing significant advancements. These case studies not only demonstrate technological possibilities but serve as powerful educational tools for manufacturers seeking successful adaptation strategies.
Real-world implementations provide insight and roadmap for businesses wishing to adopt IT capabilities effectively.
In summary, while case studies illustrate the functionality of IT in enhancing manufacturing sectors, they simultaneously act as learning narratives about each entity's journey. The exploration of these case studies provides practical insights and can guide businesses towards optimizing their IT strategies.
The Role of Education and Training in IT Adoption
The integration of information technology in manufacturing processes demands not only the tech itself but also a workforce that is equipped to leverage its full potential. Education and training are crucial for successful adoption of IT in this sector. Understanding new tools and policies in the realm of digitization allows employees to maintain productivity while navigating the changes brought by IT advancements.
Companies must recognize that investing in education goes beyond just technical skills; it includes fostering a culture of continuous learning and adaptability. As the applications of IT develop, they attach new kinds of knowledge and competencies that are essential for a modern workforce.
Importantly, effective education enhances job satisfaction. Employees are more likely to be engaged and committed when they feel competent in their skills. Upskilling reduces resistance to new technologies, easing the transition within organizations. When employee confidence and expertise align with technological requirements, overall performance improves markedly.
Education and training are not a one-off initiative but an ongoing process that requires adaptation to technological advancements.
Upskilling the Workforce
Upskilling the workforce is more than just upgrading technical skills. It also involves transitioning mindsets, enabling workers to anticipate futures demand of technology integration. Training programs can use simulations and hands-on Dual Training; they present practical scenarios where workers can implement learned skills in real-time applications. This practical orientation helps to holistically integarte schooling with on-the-job experience.
Furthermore, employers can design tailored learning paths that equip teams specifically for the technologies they will encounter. Assume a manufacturer implements IoT capabilities. Workers would uniquely benefit from training targeted towards data analytics, predictive maintenance, or network security, depending on their role in production.
Additionally, e-learning platforms facilitate a flexible approach. Workers can engage with materials outside standard working hours, allowing upskilling to mesh better with their work commitments. Consistent training helps keep employees current with industry trends and techniques. Thus, the workforce becomes a crucial driver behind the efficient use of IT.
Collaborations with Educational Institutions
Collaboration between manufacturers and educational institutions strengthens the workforce pipeline. These partnerships are essential because they ensure curriculum relevance and alignment with industry demands. Educational institutions that work with manufacturing addressing says firms’ actual needs can innovate their training methods. This aids not only student transition into the workforce but also immediate applicability. Mutual sharing of resources offers a practical aspect to learning.
Cooperative programs combine academic rigor with real-world expertise, which also benefits institutions; it enables them to heighten visibility and thereby boost enrollment in targeted technology programs. Designed internships help cultivate industry-ready graduates. Furthermore, established mentorship programs facilitate an ongoing relationship between companies and young professionals, encouraging knowledge transfer and fostering leadership within the industry.
Ending and Recommendations
The incorporation of information technology in the manufacturing sector represents a significant leap towards enhancing operational efficiency and competitiveness. This article has examined various facets of the relationship between IT and manufacturing, highlighting the transformational effects these technologies bring. Understanding the key themes of urgency in adopting advanced IT systems can position companies favorably amid rapid industry changes.
Summary of Key Points
In reviewing the engagement of IT with manufacturing, several salient themes emerge:
- Enhancement of productivity: Automation tools streamline operations, reducing manual intervention and expediting production cycles.
- Data-Driven Decision Making: Big data analytics provides actionable insights, aiding strategic decisions in real-time.
- Supply Chain Optimization: Enhanced communication through IoT dramatically improves logistics and inventory management.
- Workforce Development: Education and training enable employees to leverage new systems effectively, integrating technology meaningfully across processes.
- Future Trends: Observing the rise of Industry 4.0 concepts and sustainable practices illustrates direct company adaptations to social expectations and ecological considerations.
Strategic Next Steps for Manufacturers
Manufacturers must develop a clear plan to navigate the integration of information technologies into their operations. Here are several practical considerations:
- Conduct a Technology Audit: Evaluate existing technologies to identify gaps and areas for enhancement.
- Invest in Employee Training: Continuous upskilling programs will prepare the workforce for adopting emerging technologies, bridging skills gaps.
- Foster Collaborative Partnerships: Build relations with technology vendors and academic institutions for access to the latest innovations and training solutions.
- Prioritize Cybersecurity Measures: As reliance on digital tools rises, revising security protocols to safeguard company data becomes imperative.
- Monitor Industry Trends Continuously: Stay informed on advancements in IT related to manufacturing, such as developments in AI and predictive analytics, to retain competitive edge.
The successful adoption of information technology in manufacturing not only hinges on understanding the available tools but also highlights the necessity of cultivating a culture that embraces change and innovation.
By implementing these steps and prioritizing education within operational frameworks, manufacturers can drive their technological adoption strategically and effectively.