Maximizing Production with Visual Manufacturing ERP Software

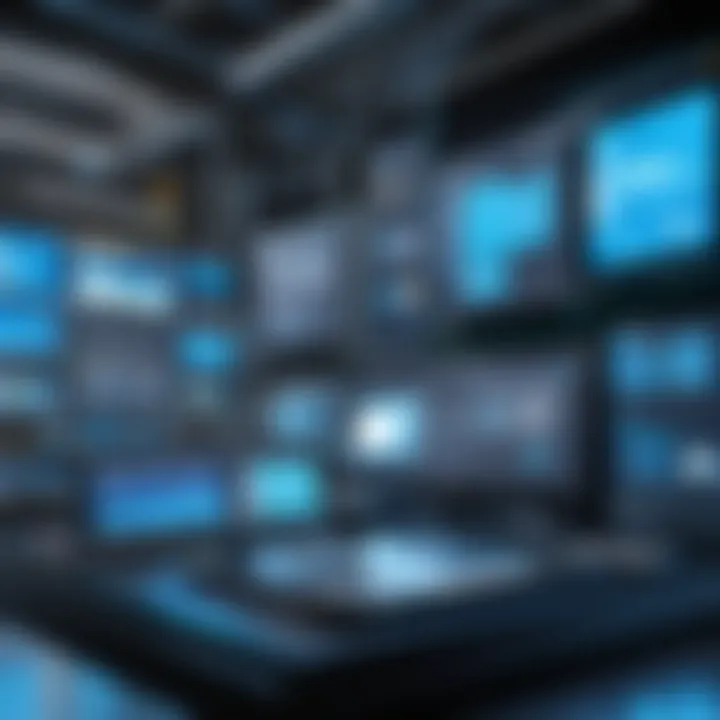
Intro
In an era where agility and precision define organizational success, visual manufacturing ERP software has started to become a core asset for industries seeking to optimize their production strategies. As businesses grapple with increasing demands for transparency and efficiency, such tools provide a bridge—aligning diverse manufacturing components from supply chain management to operational workflows. This article explores the nuances of these software solutions, breaking down their roles in enhancing decision-making and driving overall performance.
Technological Research Overview
Recent Technological Innovations
Visual manufacturing ERP solutions are not just about tracking inventory or managing resources anymore. Recent advancements include the integration of augmented reality (AR), which facilitates real-time data visualization on factory floors. This shift allows workers to access critical information—like machine performance metrics—without flipping through stacks of paperwork or navigating complex software interfaces. Besides AR, innovations such as IoT connectivity enable seamless communication among machines, leading to smarter production systems that can self-diagnose failures before they disrupt workflow.
Impact on Business Operations
The integration of visual manufacturing ERP tools is reshaping business operations profoundly. Companies that adopt these solutions often see a decrease in production errors and a notable increase in efficiency. For example, rather than depending solely on manual inputs, organizations can now harness automated data collection, translating into real-time insights. As a result, decision-makers can swiftly pinpoint bottlenecks in the production line and implement corrective measures almost instantaneously.
Future Technological Trends
Looking ahead, there’s a growing inclination toward employing machine learning algorithms to predict maintenance needs, thereby extending the lifecycle of machinery. As cyber-physical systems evolve, the manufacturing landscape is also expected to witness an increase in cloud-based ERP solutions. These platforms provide scalability and flexibility, enabling organizations to adapt quickly to market changes without overhauling their systems completely.
Data Analytics in Business
Importance of Data Analytics
Data is undoubtedly the lifeblood of modern manufacturing. With visual ERP systems, companies gain a foothold in sophisticated data analytics. Such capabilities allow businesses to sift through vast amounts of operational data, identifying trends that can drive better strategic decisions. By analyzing production histories, organizations can enhance forecasting accuracy, thus minimizing waste and optimizing resource allocation.
Tools for Data Analysis
Numerous tools have emerged to support businesses in their data-centric ventures. Tableau and Power BI are prominent examples that provide intuitive dashboards for sourcing insights from various data points. Such tools not only enhance visibility but also foster a culture of informed decision-making across the organization. Successful businesses embrace these analytical tools to glean actionable insights that can guide their next steps.
Case Studies on Data-Driven Decisions
Take, for instance, a leading automotive manufacturer that adopted advanced data analytics in their operational processes. By systematically collecting and analyzing performance data from production lines, management was able to reduce downtime by nearly fifteen percent. This data-driven culture propelled the company toward achieving significant operational milestones and provided a framework others aspire to emulate.
Cybersecurity Insights
Threat Landscape Analysis
In the age of digitalization, the manufacturing sector faces unique cybersecurity threats. With the increasing reliance on interconnected systems, cyberattacks have grown both in sophistication and frequency. Vulnerabilities can arise from weak links in the supply chain, such as third-party contractors. Hence, understanding the threat landscape is crucial for manufacturers aiming to safeguard their operations.
Best Practices for Cybersecurity
To counter these threats, organizations should adopt multiple layers of security. This includes establishing a robust framework of firewalls, anti-virus programs, and intrusion detection systems. Moreover, implementing regular training sessions can ensure that employees are equipped with knowledge on recognizing and counteracting potential threats, creating a more secure operational environment.
Regulatory Compliance in Cybersecurity
As manufacturers invest in these technologies, they must also navigate a complex web of regulations and compliance frameworks. Adhering to standards like ISO 27001 not only enhances security postures but can also boost customer confidence. A strong reputation in cybersecurity thus becomes a competitive advantage, setting organizations apart in an increasingly crowded marketplace.
Artificial Intelligence Applications
AI in Business Automation
The role of artificial intelligence in visual manufacturing ERP systems cannot be overstated. AI algorithms improve productivity by automating repetitive tasks, leaving employees free to focus on more strategic initiatives. This type of automation results in not only cost savings but also enhances overall output quality, ensuring customer satisfaction remains a priority.
AI Algorithms and Applications
Companies are incorporating AI in various ways, from predictive maintenance to supply chain optimization. For instance, machine learning algorithms can forecast demand fluctuations. When integrated into a visual ERP system, this predictive capability allows businesses to allocate resources more efficiently—preventing overproduction and understocking situations.
Ethical Considerations in AI
Despite these advantages, organizations must also navigate the ethical implications surrounding AI. Employment concerns often surface when companies embrace robust AI solutions. Thus, while enhancing efficiency, it’s essential that decision-makers maintain transparent communication with employees about roles and responsibilities, fostering a collaborative approach to technological advancements.
Industry-Specific Research
Tech Research in Finance Sector
The finance sector has seen a considerable impact from technological collaboration with visual manufacturing ERP. Finance professionals are employing data analytics to develop risk assessment frameworks that inform lending decisions or investment strategies. As such, these systems present an avenue for cross-industry learning, sharing insights on data management practices.
Healthcare Technological Advancements
In healthcare, integrating visual manufacturing ERP systems streamlines supply chains for critical medical supplies. As medical demands fluctuate, having access to real-time inventory data helps healthcare providers maintain adequate stock, ultimately ensuring patient safety and maintaining operational resilience.
Retail Industry Tech Solutions
In retail, companies are evolving their operational models by integrating visual ERP systems that provide a clear view of inventory across diverse locations. This visibility allows for immediate corrective actions, like adjusting stock levels according to consumer behavior. Those that adapt quickly not only stay relevant but often thrive in this dynamic environment.
Visual manufacturing ERP tools are not just an operational necessity; they are a strategic enabler for businesses aiming to achieve sustainability, efficiency, and resilience in an ever-complex production landscape.
Prologue to Visual Manufacturing ERP Software
In today’s fast-paced and ever-evolving manufacturing landscape, the integration of visual manufacturing ERP software emerges as a game-changer, leaving a notable footprint on production efficiency. Let’s face it, as the demands for faster production cycles and better quality control continue to mount, manufacturers find themselves under the proverbial gun to adapt. This is where visual manufacturing ERP software comes into play, providing not just tools, but a comprehensive framework that redefines how production units operate.
The core importance of visual manufacturing ERP software lies in its ability to synthesize various manufacturing processes into a cohesive unit. This software isn’t merely a helping hand; it's a central nervous system that allows for better management across different stages of production—from procurement of materials to the shipping of final goods. The software enhances visibility into operational metrics, enabling decision-makers to monitor performance in real time, rather than relying on outdated reports that may have missed the mark.
Specific Elements of Visual Manufacturing ERP Software
- Real-Time Monitoring: The essence of manufacturing is often in how swiftly issues can be detected and rectified. With real-time data visualization features, stakeholders can pinpoint hiccups in production as they happen, rather than waiting until end-of-day reports. If a machine experiences downtime, it can trigger alerts, allowing for immediate interventions.
- User-Friendly Dashboards: Gone are the days when deep dive analytical reports required specialized skills to decipher. The visual dashboards cater to everyone in the organization, from the floor manager to the executive suite. They can make sense of complex data in digestible formats, simplifying decision-making.
- Interactive Reporting Tools: Manufacturing professionals thrive on actionable data. The software's interactive reporting capabilities enable engineers and managers to manipulate data sets and gather insights specific to their needs.
"In manufacturing, the ability to see clearly and make informed choices is what sets successful enterprises apart from their competitors. Visual ERP software is not just an enhancement; it's a necessity in an era of rapid change."
Additional Benefits to Consider
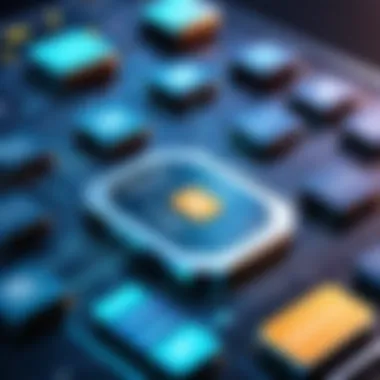
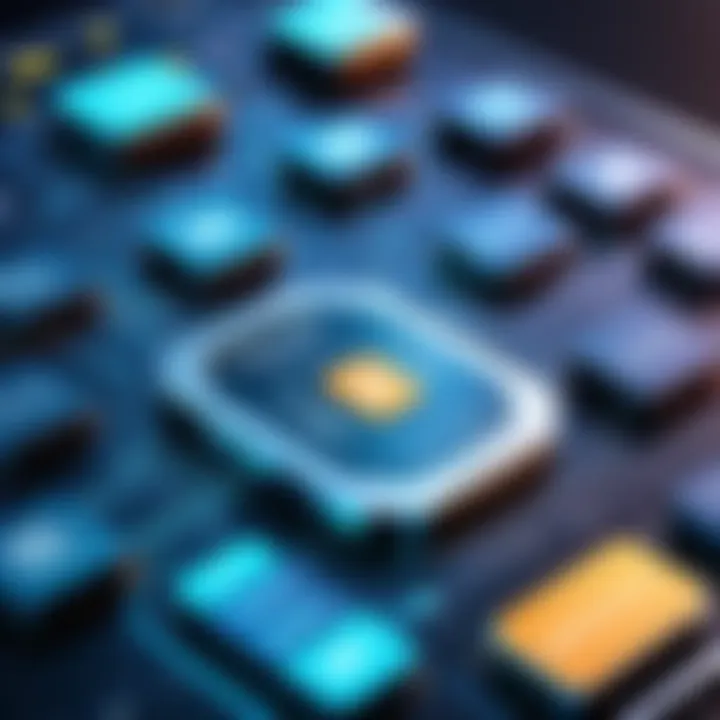
Integrating visual manufacturing ERP software brings along a treasure trove of benefits. Beyond improving decision-making and operational efficiency, it fosters a culture of transparency within organizations. When information flows freely, collaboration thrives, allowing departments to synchronize efforts and attain common objectives. As businesses evolve, the ability to pivot in response to market demands hinges largely on the internal ecosystems constructed by such software.
Moreover, embracing this technology can lead to significant cost savings by minimizing waste and optimizing resource allocation. Manufacturers often find that they can do more with less when they have access to real-time data and insights, ultimately leading to better profit margins.
Overall, visual manufacturing ERP software is not just a tool; it’s a strategic leap towards a more organized and efficient manufacturing process. Engaging with this technology signifies an understanding of current market demands and a proactive approach to staying competitive.
Understanding the Concept of ERP in Manufacturing
When diving into the intricate world of manufacturing, it's crucial to grasp the essence of Enterprise Resource Planning (ERP). This understanding lays the groundwork for comprehending the role of visual manufacturing ERP software, which doesn’t simply serve as an operational tool but as a transformative force within modern production environments.
Definition and Scope of ERP
Enterprise Resource Planning, commonly referred to as ERP, represents an integrated approach to managing core business processes. At its heart, ERP is about breaking down silos within an organization, allowing for seamless communication across departments. In manufacturing, this means streamlining inventory management, production schedules, and supply chain logistics into a cohesive framework.
The scope of ERP in the manufacturing sector covers a broad spectrum, including:
- Financial Management: Keeping tabs on costs, budgeting, and accounting to ensure profitability.
- Supply Chain Management: Monitoring goods from supplier to customer, enhancing visibility and control.
- Production Planning: Mapping out production schedules that align with demand forecasts.
- Human Resources: Managing workforce needs and analytics.
By integrating these functions, ERP systems create a central repository of information that can be accessed in real-time. This fosters better decision-making and ultimately leads to increased efficiency and reduced operational costs.
Historical Evolution of ERP Systems
The journey of ERP systems is fascinating, reflecting technological advancements and the shifting needs of businesses. Initially, ERP systems were merely focused on automating accounting functions. In the 1960s and 70s, they evolved with the advent of Material Requirements Planning (MRP), aimed at optimizing inventory levels based on production schedules.
As technologies grew more sophisticated, so did ERP. The 1990s saw the introduction of ERP as we recognize it today, combining various functionalities to provide holistic business solutions. The emergence of the internet further accelerated this evolution, leading to cloud-based ERP solutions that increased accessibility and scalability for manufacturers.
Fast forward to the present day, and we’re witnessing the integration of cutting-edge technologies like artificial intelligence, machine learning, and the Internet of Things (IoT) into modern ERP systems. This not only makes ERP more versatile but also crucial for real-time decision-making in manufacturing processes. The historical evolution of ERP systems underscores their increasing complexity and the vital role they play in enhancing production efficiency today.
"A well-implemented ERP system can serve as the backbone of a manufacturing enterprise, supporting everything from supply chain logistics to customer relations."
In summary, understanding the concept of ERP in manufacturing is not just about knowing what it is; it’s about recognizing how it shapes the future of production efficiency. With its expansive reach and continuous evolution, ERP serves as an essential toolkit for tackling modern manufacturing challenges.
The Role of Visual Manufacturing ERP Software
In today’s fast-paced manufacturing landscape, organizations must sift through a lot of data, processes, and workflows to keep their operations running smoothly. This is where visual manufacturing ERP software emerges as a game-changer. The real beauty of this software lies in its ability to simplify complex manufacturing processes through visualization, enabling better coordination, enhanced decision-making, and even greater efficiency.
When you think about manufacturing, it’s clear that it’s not just about machinery and products; it’s about managing people and processes effectively. Visual tools allow manufacturers to grasp what’s happening on the shop floor instantly. By graphically representing data and processes, these tools help stakeholders—from operators to executives—understand key performance indicators at a glance.
The Need for Visual Tools in Manufacturing
As manufacturing becomes increasingly complicated due to globalization, market competition, and technological advances, the demand for visual tools becomes more pronounced. Traditional data reporting methods often bury critical information in spreadsheets, making it easy to miss vital insights. Visual manufacturing ERP software addresses this issue head-on. It transforms raw data into meaningful visualizations, enabling manufacturers to:
- Quickly identify bottlenecks in production.
- Monitor performance metrics in real time.
- Engage teams with interactive data presentation.
Visual tools bridge the communication gap between departments. For instance, let’s say a production line is running slower than expected. A well-placed visual can immediately depict this issue, prompting a response before the slowdown affects overall productivity.
Key Features of Visual Manufacturing ERP Software
The effectiveness of visual manufacturing ERP software is largely attributed to its core features, each designed to make data more accessible and actionable.
Real-time Data Visualization
Real-time data visualization is a cornerstone of visual manufacturing ERP solutions. This feature displays live updates on critical metrics such as production output, equipment performance, and inventory levels. The immediate availability of this information helps decision-makers to respond swiftly to changes and make informed decisions without delay.
One of its standout characteristics is the capability to track various operational metrics in real-time through visual dashboards. This fosters a proactive approach to problem-solving. The unique aspect of real-time data visualization is its capacity to highlight deviations from accepted norms instantly. For instance, if a machine's output falls below expectations, alerts can be issued immediately, helping mitigate potential downtime.
While real-time visibility is a distinct advantage, it comes with the need for consistent internet connectivity and may require significant investment in IT infrastructure to maintain data accuracy and security. An inefficient setup could lead to reporting errors, undermining the very benefits it aims to provide.
Integrated Dashboards
Integrated dashboards serve as a hub for consolidating information from diverse manufacturing functions—production, supply chain, quality control, and finance—into a singular visual platform. This all-in-one feature promotes a synergized view of operations enabling various teams to collaborate seamlessly.
The essential characteristic here is interlinkage; dashboards connect various data points so that changes in one area can quickly be observed in another. For instance, if raw materials are delayed, the dashboard can show how this impacts production schedules and overall throughput in real time.
However, creating effective dashboards does require time and input from multiple departments to ensure they reflect the right metrics. Plus, with an overload of data, teams might experience "analysis paralysis," where too much information can cause confusion rather than clarity.
Interactive Reporting Tools
Interactive reporting tools take data analysis a step further by allowing end-users to manipulate datasets visually to access deeper insights. Users can drill down into specific data segments to understand trends, make comparisons, and simulate various scenarios.
A key feature here is user-friendliness. The intuitive layout of these tools means that even those with minimal technical know-how can engage meaningfully with the data. This democratization of data is crucial in a manufacturing setting where timely decisions must often be made by personnel at all levels.
Nonetheless, interactive tools can sometimes lead to oversimplified conclusions. Users may miss the bigger picture if they focus too heavily on granular data analysis. Hence, it’s crucial to foster a culture that understands the importance of both high-level and detailed insights when navigating these tools.
The essence of visual manufacturing ERP software is its fusion of technology and transparency. By making data visual, it converts complexity into clarity.
Combining these features paints a vivid picture of a manufacturing operation in motion, allowing for quick adjustments and keeping teams aligned toward common goals. By leveraging visual manufacturing ERP software, businesses can truly harness the power of their data, leading to enhanced efficiency and growth.
Benefits of Implementing Visual Manufacturing ERP Software
The deployment of visual manufacturing ERP software stands as a pivotal moment for organizations keen on refining their production processes. This technology offers a multifaceted approach to manage operations, combining visualization tools with essential manufacturing functions. The benefits of implementing such a system are not merely superficial; they delve deep into enhancing productivity and efficacy. By harnessing this software, organizations can expect notable advantages that resonate across various operational levels.
Enhanced Decision-Making Capabilities
One of the foremost advantages of visual manufacturing ERP software lies in its capacity to bolster decision-making processes. In a manufacturing environment, where choices often dictate the pace and efficiency of operations, having access to real-time data visualizations becomes indispensable. Decision-makers can monitor production metrics at a glance, transforming complex data sets into actionable insights. For instance, when a sudden spike in production demand occurs, managers can swiftly assess resource availability and team workloads, allowing for agile responses.
Here are some specific elements that enhance decision-making through visual manufacturing ERP tools:
- Real-time Analytics: The ability to analyze production data as it happens ensures that no opportunity or risk goes unnoticed.
- Data-Driven Insights: Patterns and trends emerge more effectively when visualized, enabling predictive analytics that guide future decisions.
- Collaborative Platforms: These tools often facilitate better communication between teams, allowing diverse perspectives to coalesce around strategic choices.
"With the insights gained from visual manufacturing ERP systems, companies can navigate uncertainties with confidence, turning challenges into opportunities."

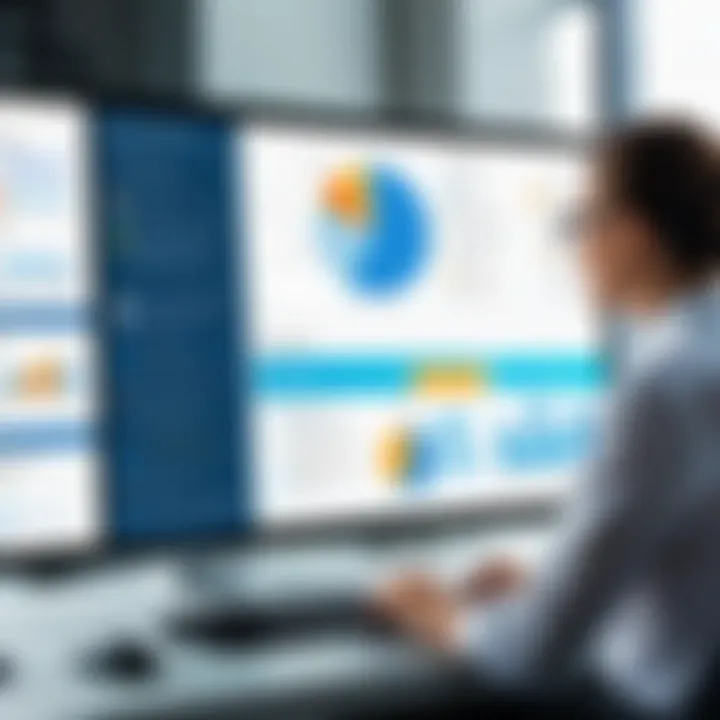
Streamlining Production Processes
In the manufacturing world, the heat is often on to optimize processes. Visual manufacturing ERP software plays a critical role in streamlining these processes, minimizing bottlenecks and inefficiencies. The software provides a comprehensive view of the entire production line, making it simpler to identify areas needing attention. This visibility can lead to significantly reduced downtime and improved workflow.
Key factors in streamlining production processes include:
- Workflow Automation: Manual tasks can be automated, freeing up resources and giving employees the chance to focus on higher value tasks.
- Resource Management: Optimizing the use of materials and machinery is simpler when all elements of production are monitored in real-time.
- Error Reduction: Visual cues and alerts help to catch potential mistakes early, preventing further complications down the line.
Improved Operational Efficiency
Operational efficiency hinges on a company’s ability to produce at lower costs while maintaining quality. Integrating visual manufacturing ERP software aligns efforts toward this goal seamlessly. The software aids in fine-tuning operational efforts by making key data accessible across the organization, guiding every facet of production from initial design to final assembly.
Main contributors to improved operational efficiency are:
- Performance Metrics Tracking: Ongoing monitoring of productivity levels generates actionable insights that optimize performance continuously.
- Cost Savings: Streamlined processes often translate directly to reduced operational costs, whether it be through material savings or time efficiency.
- Enhanced Quality Control: Visual tools can highlight discrepancies in real time, allowing for quick corrective measures that uphold product standards.
Through these benefits, it’s evident that implementing visual manufacturing ERP software can significantly alter the landscape of production efficiency. Companies looking to thrive must consider these elements critical in an increasingly competitive marketplace.
Challenges in Visual Manufacturing ERP Software Adoption
Adopting visual manufacturing ERP software is not just about choosing the right system; it’s a multifaceted process that can throw quite a few curveballs. Organizations might think that once they choose software, the hard work’s done. However, challenges such as resistance to change, integration with current systems, and training needs can make the road bumpy. Understanding these obstacles can help companies adopt ERP more smoothly and reap the benefits without heartburn.
Resistance to Change in Organizations
People don’t always like change. This is a universal truth, but it hits especially hard in manufacturing environments. Employees might be used to old methods. They feel comfortable with the way things are done, even if they’re not the most efficient. Visual manufacturing ERP introduces new workflows that often require a shift in mindset.
One of the main sticking points is that workers may fear that new technology will threaten their jobs. This fear can lead to pushback against the new system, making implementation harder. Companies must address this concern head-on, emphasizing that visual ERP is not designed to replace jobs but to enhance productivity and job satisfaction.
Engaging personnel from the start is crucial. When employees feel part of the process, they are more likely to embrace change. Leaders must communicate the ‘why’ behind the transformation and share helpful data that outlines expected improvements. Regular feedback loops can also play a significant role in making employees feel heard during the transition.
"Change is hard at first, messy in the middle, and gorgeous at the end."
– Robin Sharma
Integration Issues with Existing Systems
Yet another hurdle comes from trying to make the new visual manufacturing ERP software play nice with the systems already in place. Many companies have older software or stand-alone systems that don't easily connect with modern ERP solutions. This can lead to data silos or discrepancies that can create more issues than they solve.
Successful integration is no small feat; it often requires thorough planning and a robust understanding of both the new and existing systems. Companies should conduct a comprehensive audit of all current systems before proceeding with ERP implementation. This ensures they know what data needs to be migrated, what can be integrated, and what processes might need to be rethought entirely.
Furthermore, enlisting IT specialists and involving them in the planning phase can help identify potential integration issues long before they arise. Being proactive instead of reactive saves time and resources down the line.
Training and Skill Development Needs
Finally, let’s not forget the importance of training and skill development. Even if the new visual manufacturing ERP system is a game changer, its success depends on how well employees understand and utilize it. Unfortunately, many organizations neglect this aspect and assume that employees will automatically know how to navigate new software.
This approach can lead to frustration and ineffective use, undermining the potential benefits of the system. Instead, a tailored training program should be designed that meets the specific needs of different user groups. Hands-on workshops, online courses, and easy-to-access documentation can make a world of difference.
Significant time and investment in employee training can also foster a sense of ownership among the team, leading to higher morale and job satisfaction. When employees feel capable and confident using the new tools, the entire organization stands to benefit.
Criteria for Choosing Visual Manufacturing ERP Solutions
When delving into the domain of visual manufacturing ERP systems, selecting the right solution isn't just a minor decision — it's a critical one that can mold the operational landscape of a manufacturing enterprise. The choice of an ERP system has implications that stretch beyond mere software installation; it affects workflow efficiency, data management, decision-making processes, and ultimately, the bottom line. This section discusses essential criteria to consider when choosing a visual manufacturing ERP solution that meets the unique needs of an organization.
Assessing Business Needs and Objectives
Understanding one’s own business needs is the first cornerstone in selecting the right ERP software. Companies must take a hard look at their unique operational processes. Considerations here include the scale of production, the volume of data required for analysis, and the specific types of outputs needed for effective decision-making.
For instance, a custom machine shop might need a highly flexible ERP system that allows for quick adjustments, while a large, assembly-line manufacturer might prioritize integration capabilities with existing machinery. A good approach is to list requirements based on priorities. This could look like:
- Scalability: Can the system grow with the business?
- User Experience: Is the software intuitive for operators at different levels?
- Integration: Will it mesh well with tools already in place?
An in-depth SWOT analysis — exploring strengths, weaknesses, opportunities, and threats regarding current operations — can highlight areas where an ERP might add value. A clear set of objectives aligned with business goals, such as improving production time or reducing waste, will guide the selection process significantly.
Evaluating Vendor Capabilities
Once business needs are well defined, the next step involves filtering potential vendors. Not all ERP solutions are created equal; some might shine in certain areas while falling short in others. Critical evaluation of vendor capabilities includes looking into their track record, support services, and flexibility of their offerings.
A savvy approach could involve:
- Researching Reviews: Checking platforms like Reddit or dedicated forums for real-world user experiences.
- Requesting Demos: This allows for firsthand evaluation of software in action.
- Assessing Customer Support: How responsive is the vendor? A partner with excellent after-sales support can make a world of difference.
Additionally, exploring how often the vendor updates their solutions can help gauge their commitment to keeping pace with technological advancements. A forward-thinking vendor will keep integrating innovative features like AI and real-time data analytics to stay relevant.
Cost Considerations in ERP Selection
Although it might be tempting to base the decision solely on initial costs, a more comprehensive cost analysis is essential. A thorough evaluation should include:
- Initial Investment: The upfront cost of software, licensing, and installation.
- Ongoing Costs: Monthly/annual subscriptions, maintenance fees, and possible upgrades.
- Training Costs: Personnel training on the new system.
Here, it's important to factor in the potential ROI. An informative practice is to project potential gains from efficiency improvements against the total cost of ownership of the ERP solution. In many scenarios, investing in a slightly more expensive ERP with robust functionality can yield greater returns in the long run.
"A wise investment in technology today can translate into unparalleled advantages tomorrow."
Lastly, utilizing methods like TCO (Total Cost of Ownership) analysis can help map out the financial landscape of each option.
Implementation Strategies for Visual Manufacturing ERP
Effectively incorporating visual manufacturing ERP software into existing business infrastructures hinges on well-structured implementation strategies. It’s like laying the groundwork for a house—without a solid foundation, everything built on it risks being unstable and inefficient. This section delves into the nuances of implementation, outlining the critical steps needed to ensure the successful integration of visual ERP solutions in manufacturing contexts. Solid strategies not only improve operational workflows but also lead to significant boosts in overall productivity.
Defining an Implementation Roadmap
Creating a defined implementation roadmap is crucial when approaching visual manufacturing ERP integration. This roadmap serves as a detailed guide that outlines the journey from initiation to full-fledged use of the system. It’s essential to begin with a comprehensive assessment of the current systems and processes in place. Doing this helps identify gaps and areas for improvement.
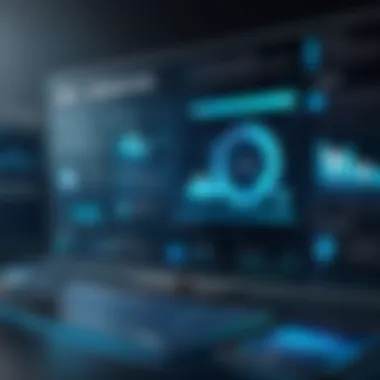
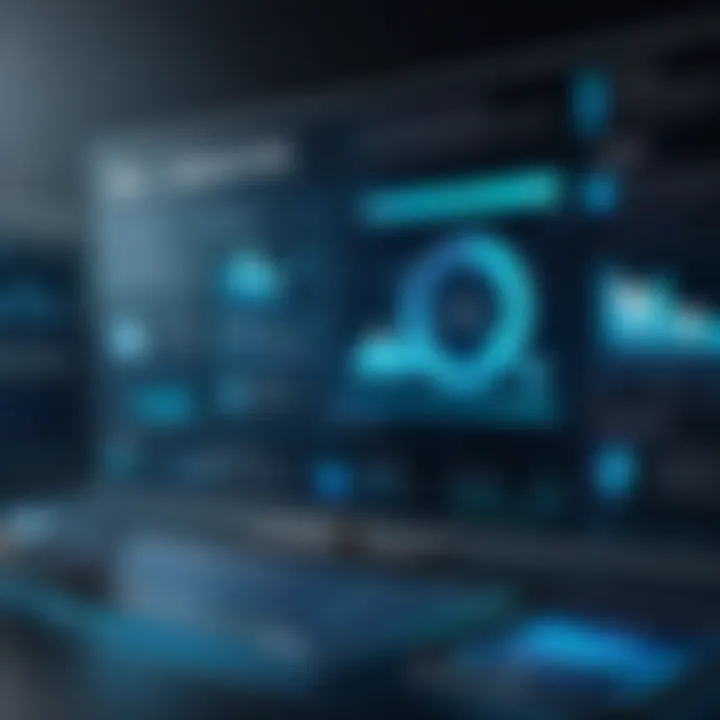
Key components of the roadmap include:
- Timeline: Establishing a realistic timeframe for each phase—analysis, planning, implementation, and evaluation.
- Milestones: Setting specific, measurable objectives at each phase helps to track progress and maintain momentum.
- Resource Allocation: Determining the budgetary and human resources required ensures that the project is adequately supported.
Having this roadmap not only keeps the implementation on track but also aligns the various stakeholders toward common goals. This way, everyone knows what to expect and what is expected of them, making for a more harmonious rollout experience.
Engaging Stakeholders During the Process
When it comes to implementing visual manufacturing ERP software, engaging stakeholders is like assembling a team for a big project—everyone has a role to play. Stakeholder involvement is paramount for a smooth transition because it fosters an environment of open communication and shared responsibility.
To effectively engage stakeholders, consider the following approaches:
- Identify Key Players: Determine who in the organization will be affected by the new system and involve them from the start. This may include department heads, IT specialists, and even end-users.
- Regular Updates: Keep stakeholders informed with frequent updates about the implementation process. Transparency builds trust.
- Feedback Loops: Create opportunities for stakeholders to provide input and raise concerns. Their insights can reveal potential issues before they become problematic.
- Change Management Training: Educate stakeholders on how to use the new system and its benefits. When they feel knowledgeable and confident, acceptance rates soar.
Engaging these key figures not only smooths out the wrinkles during implementation but also cultivates buy-in for the changes being made.
Ongoing Support and Maintenance
Implementing visual manufacturing ERP software is not a one-off activity; it’s the start of an ongoing journey. Just as a car needs regular maintenance to ensure it runs smoothly, your ERP system requires consistent support and updates to function at peak efficiency.
The following elements are necessary for effective ongoing support and maintenance:
- Dedicated Support Team: Establish a team for technical support that users can reach out to when difficulties arise. This accessibility promotes user confidence in the system.
- Regular Updates: Continuously assess the software version in use and ensure it is updated to incorporate new features and security patches. Keeping the software current reduces vulnerabilities and enhances functionality.
- User Training Sessions: Conduct regular training workshops to help users remain proficient in utilizing the software’s features effectively.
- Performance Metrics: Implement metrics to evaluate the system's performance. These insights can identify any problems early, allowing for prompt resolutions.
By focusing on these support and maintenance strategies, organizations can uphold their investment in visual manufacturing ERP software over time, ensuring it continues to meet both current and future operational needs.
"Implementation is not an end but a beginning—embracing support and maintenance ensures that the journey is sustainable".
Case Studies: Successful Implementation of Visual Manufacturing ERP
When discussing visual manufacturing ERP software, theoretical exploration is essential, but real-world case studies illuminate its practical applications and impact. By analyzing specific implementations, professionals can gain insights into how these systems can enhance productivity and streamline operations. Case studies serve as a roadmap, showing how different organizations have navigated challenges, adopted solutions, and ultimately benefited from this technology. They not only highlight the versatility of visual manufacturing ERP but also demonstrate the effectiveness of these systems in driving tangible results.
The benefits of studying successful implementations include:
- Real-life Evidence: Understanding how companies leverage visual manufacturing ERP leads to better decision-making in similar environments.
- Strategic Insights: Each case study reveals unique strategies that resulted in success, providing frameworks for others.
- Learning from Challenges: They often highlight pitfalls and obstacles which can prepare others for their journey towards implementation.
As we explore these case studies, we will focus on the significance of setting clear objectives, understanding the organizational culture, and the importance of seamless integration with existing systems. Now, let's look into two specific examples that showcase successful implementations.
Case Study One: Manufacturer of Precision Tools
The first case involves a manufacturer known for their precision tools, a company that faced significant challenges in meeting rising customer demands while maintaining quality standards. With production processes lagging and reporting systems providing minimal insights, this organization decided to implement a visual manufacturing ERP solution.
The major factors that contributed to their successful implementation include:
- Clear Objectives: The management established specific goals, such as reducing downtime and improving production scheduling.
- User-friendly Visualization Tools: The selected system featured interactive dashboards that allowed managers to monitor operations in real-time, leading to quicker decision-making.
As a result, within a year's time, they saw a marked improvement. Not only did productivity increase by 30%, but also employee morale improved as the tool simplified their workflows. Workers could visualize data and track their output easily, making them feel more in control of their processes. It was a win-win situation.
Case Study Two: Automotive Component Supplier
The second case looks at an automotive component supplier that struggled with inventory management and supplier integration. They turned to visual manufacturing ERP software in hopes of enhancing their supply chain efficiency. The following aspects were crucial to their success:
- Metrics-Driven Approach: This company emphasized data-driven decision-making from the start, ensuring that every decision was backed by solid analytics.
- Collaboration Tools: The ERP system included features that promoted coordination with suppliers, enabling seamless communication about inventory levels.
The outcome was remarkable: inventory carrying costs dropped by 25%, and lead times were shortened by 40%. The visual tools allowed decision-makers to anticipate inventory needs better and respond proactively to market demands. It transformed the way they operated, adopting a more agile and responsive business model.
These case studies highlight that the adoption of visual manufacturing ERP software can lead to substantial operational improvements when done thoughtfully and strategically.
Both organizations exemplified how a clear vision, combined with the right tools, can maximize production potentials while minimizing inefficiencies. By employing tailored strategies and paying attention to both technological and human factors within their organizations, they effectively transformed their production environments and set a benchmark for others in the industry wanting to follow suit.
Future Trends in Visual Manufacturing ERP Software
As we gaze into the future of manufacturing, it's evident that technologies continue to evolve, pushing industries towards unprecedented levels of efficiency and innovation. Visual manufacturing ERP software stands at the forefront of this transformation, adapting to new trends that shape not just production processes but also strategic decision-making. These advancements are not mere add-ons; they become integral to enhancing operational workflows, data management, and ultimately, productivity.
Emergence of Artificial Intelligence and Machine Learning
Artificial intelligence and machine learning are no longer the stuff of science fiction; they have seamlessly woven into the fabric of manufacturing ERP systems. The infusion of AI enables the analysis of vast amounts of data at lightning speed, which fuels more informed decision-making. For instance, predictive analytics can anticipate machinery failures before they happen, allowing companies to enact maintenance schedules proactively instead of reactively. This shifts the paradigm from merely responding to issues to preventing them altogether.
Also, machine learning algorithms adapt continuously as they process new data, enhancing their accuracy over time. As such, businesses employing these smart technologies can better tailor their operations to actual needs rather than relying on historical patterns alone. The takeaway? Embracing AI and machine learning within visual manufacturing ERP enhances responsiveness to real-time conditions, drastically improving the agility of production operations.
Integration with IoT Technologies
The Internet of Things (IoT) has distinguished itself as a crucial element of modern manufacturing, allowing for greater connection between machines, systems, and even human workers. Visual manufacturing ERP software is being designed to harness the data generated from IoT devices. This connectivity plays a vital role in informing decision-making processes, as data from floor machines can now be fed directly into the ERP system for immediate analysis.
Imagine a scenario where sensors on a production line actively monitor the temperature, speed, and performance of machinery. This live data can alert managers about potential bottlenecks or issues right as they arise. Further enhancing operational insight, IoT integrations facilitate more streamlined communication across departments, uncovering insights that were previously hidden.
As industries embrace IoT technologies, the synergy created with visual manufacturing ERP transforms factories into connected ecosystems, fostering a culture of proactive management and continuous improvement.
In summary, the trends leading us into a future powered by artificial intelligence, machine learning, and IoT technologies are reshaping visual manufacturing ERP solutions. They promise not only to enhance productivity and efficiency but also to cultivate a responsive and adaptable manufacturing environment. For professionals and leaders in the field, understanding these trends is not optional; it is essential for staying ahead of the curve.
End: The Impact of Visual Manufacturing ERP on Industry Growth
As we wrap up this exploration of visual manufacturing ERP software, it becomes clear that these systems are not just a passing trend; they are reshaping the manufacturing landscape in profound ways. The integration of visual tools within ERP software serves several critical functions that contribute to the overall growth of industries focused on production.
One significant impact stems from the ability of visual manufacturing ERP software to enhance decision-making. When decision-makers have access to real-time data and interactive visualizations, they can react quickly to changing circumstances on the floor. Traditional methods might have required days to gather data and make informed decisions, while this software can cut that time down to minutes or even seconds. This immediacy enables manufacturers to respond to market demands swiftly, ensuring that they stay competitive.
"With visual manufacturing ERP, businesses don’t just keep up; they leapfrog their competition."
In addition, visual manufacturing ERP aids in streamlining operations. By providing an integrated view of all production components, these systems allow planners to optimize workflows, monitor inventory levels, and manage resources more efficiently. This not only boosts productivity but also reduces waste, which is a primary concern in today’s environmentally-conscious world. Companies that harness these capabilities can achieve substantial cost savings and contribute to sustainability—both of which are critical considerations for modern consumers and shareholders.
Moreover, the flexibility of visual manufacturing ERP systems ensures they can adapt to various industry needs. Manufacturers are not limited to a one-size-fits-all approach; they can tailor the software to suit their specific processes, which is critical when dealing with diverse operations or unique product lines. This adaptability ultimately supports business growth, as organizations can pivot quickly in response to new challenges or opportunities, whether they arise from local market changes or global economic shifts.
It's also essential to reflect on the way this software fosters collaboration among teams. Visual tools facilitate clearer communication and a shared understanding of objectives. Whether in cross-departmental initiatives or project-based teams, having a centralized source of information that presents data visually can bridge gaps that often lead to misunderstandings or inefficiencies. This collaborative spirit is vital in an age where agility and innovation often dictate success in the manufacturing sector.
In summary, the impact of visual manufacturing ERP on industry growth is far-reaching. The software not only enhances efficiency and productivity but also positions organizations to stay ahead of the curve. As we look to the future, businesses that invest in this technology will likely find themselves reaping the rewards, not just in terms of operational metrics but also in their ability to adapt and thrive in a dynamic environment.
In consideration of these factors, one might conclude that visual manufacturing ERP is not merely an upgrade; it is an essential cornerstone for any manufacturing entity looking to grow and sustain its operations in a fast-paced marketplace. The alignment of technology and strategy will prove invaluable as visual manufacturing ERP takes center stage in defining the future of production.