Exploring Quality Management System Tools for Success
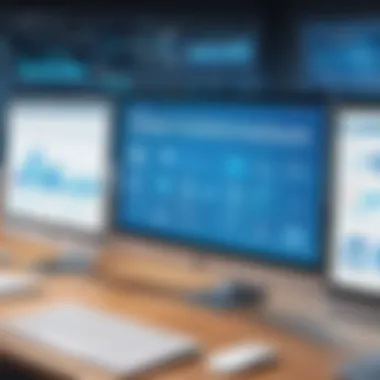
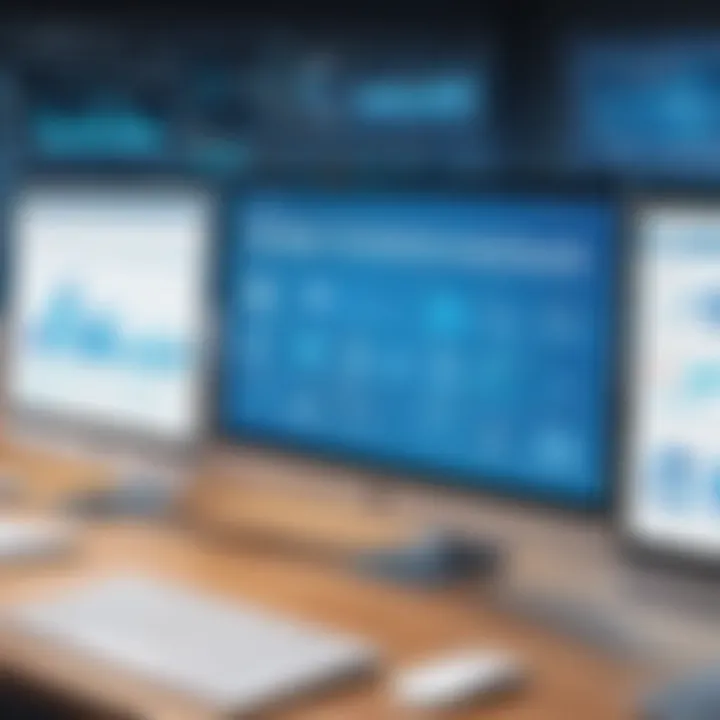
Intro
Quality Management Systems (QMS) play a crucial role in the operational success of modern organizations. As businesses evolve, so do their needs for efficient management tools and methodologies. Understanding the landscape of QMS tools not only helps in enhancing product quality but also streamlines processes and improves overall organizational performance. This article explores essential QMS tools, categorizing them by their functionality and discussing their relevance in today’s complex business environment.
Technological Research Overview
Recent Technological Innovations
In the realm of quality management, various technological advancements have emerged recently. These innovations empower organizations to improve their efficiency through tools like cloud computing, artificial intelligence, and predictive analytics. Cloud-based systems allow for easier access to quality data while AI assists in automating processes and reducing human errors.
Impact on Business Operations
The integration of these tools alters the dynamics of business operations. Enhanced data visibility and better communication through collaborative tools like Microsoft Teams or Asana make it simpler to track project progress and quality metrics. Decisions can be based on real-time data which contributes significantly to strategic planning and execution.
Future Technological Trends
Several trends could shape the future of QMS technologies. The Internet of Things (IoT) is gaining traction in quality management as it allows continuous data collection from devices and systems. Similarly, advancements in machine learning hold potential for identifying patterns that improve product quality. It is safe to predict these technologies will persist in transforming standard practices in quality management.
Data Analytics in Business
Importance of Data Analytics
Data analytics has become a cornerstone of modern business strategies. Qualitative and quantitative insights derived from data guide decision-making processes in organizations. By interpreting complex data trends, firms can uncover opportunities, anticipate challenges, and optimize their operations.
Tools for Data Analysis
Utilizing various tools enhances the ability to perform effective data analysis. Software solutions like Tableau, Microsoft Power BI, and Google Analytics provide essential insights into performance metrics. These applications serve to tailor data presentation, highlighting crucial findings
Case Studies on Data-Driven Decisions
Organizations leveraging data analysis for decision-making offer numerous insights. For instance, Amazon uses data-based strategies to enhance customer satisfaction and streamline inventory management. Such case studies illustrate the compelling outcomes possible with informed decision-making.
Cybersecurity Insights
Threat Landscape Analysis
The interdependence of technology and quality management systems can pose cybersecurity risks. Understanding current threats, including hacking and data breaches, is vital for protecting an organization's integrity and service quality.
Best Practices for Cybersecurity
Adopting a multi-layer approach to cybersecurity pays dividends. Some established best practices include:
- Regularly updating software and systems
- Conducting risk assessments and audits
- Training employees on security awareness
Regulatory Compliance in Cybersecurity
Moreover, organizations must be cognizant of regulatory compliance that governs data protection, such as GDPR or HIPAA. Adhering to these regulations not only shields the company from penalties but also bolsters trust among clients and partners.
Artificial Intelligence Applications
AI in Business Automation
Artificial intelligence optimizes processes effectively within a QMS framework. Automating routine tasks mitigates errors while freeing personnel to focus on higher-level activities. Fine-tuning repetitive tasks leads to improved efficiency and quality delivery.
AI Algorithms and Applications
Additionally, companies deploy AI algorithms for preventative maintenance in manufacturing processes. Algorithms can evaluate machine conditions in real time, predicting potential failures prior to production halts.
Ethical Considerations in AI
While adopting AI enhances productivity, ethical conscience must not be neglected. Transparency in AI decision-making processes strengthens stakeholder trust and quickens the adoption of these technologies.
Industry-Specific Research
Tech Research in Finance Sector
In the finance sector, QMS tools integrate compliance tracking and risk management efficiently. Tools like SAS Risk Management and MQM play vital roles in maintaining quality amidst regulatory pressures.
Healthcare Technological Advancements
The healthcare industry's complexity demands precise quality management. Innovations like Electronic Health Records (EHR) not only boost operational efficiency but enhance patient care quality.
Retail Industry Tech Solutions
Similarly, in retail, tools such as inventory management platforms can sustain quality while ensuring smooth supply chain operations. An approach focused on fulfilling customer demands without fail is essential in this sector.
Organizations prioritizing quality management tools substantially boost performance.
Navigating the landscape of QMS tools requires comprehensive insight into various sectors, their inherent challenges, and respective technological responses. This article is an affirmative step towards assisting decision-makers in cultivating robust quality management strategies, fostering informed choices.
Intro to Quality Management Systems
Quality Management Systems (QMS) are essential frameworks employed by organizations to manage quality in their processes, products, and services. The global market today is highly competitive, and the pursuit of quality plays a significant role in achieving operational excellence. As such, understanding QMS is crucial for businesses to meet customer expectations and regulatory requirements.
Definition and Purpose of QMS
A Quality Management System is a structured system that document procedures, processes, and responsibilities for achieving quality policies and objectives. The objectives of a QMS include:
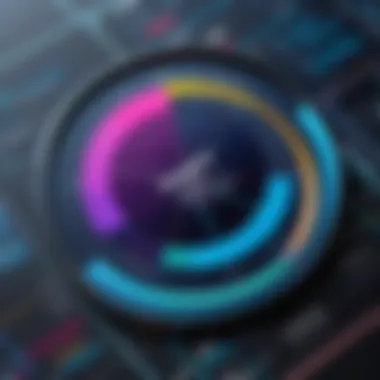
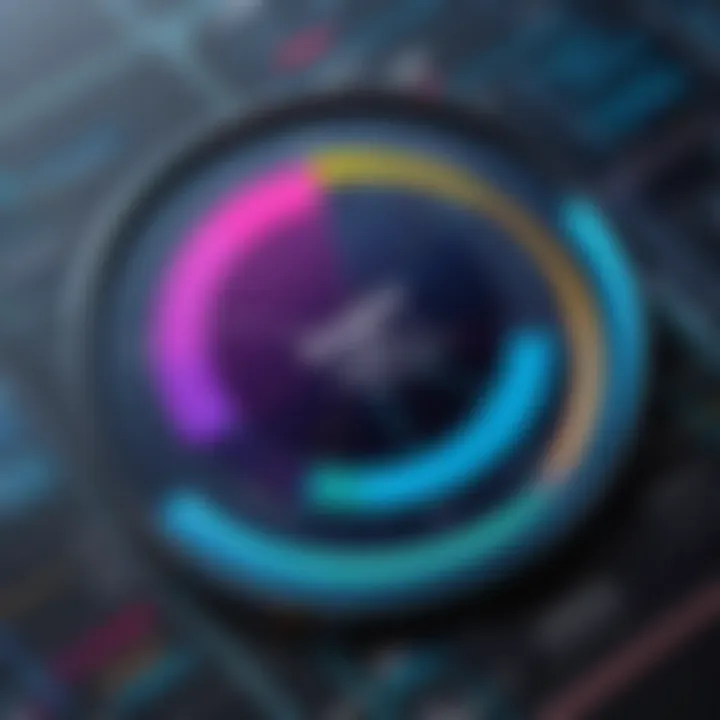
- Consistent quality in products and services.
- Identification and mitigation of risks.
- Improvement of procedures based on empirical evidence.
- Increased operational efficiency and customer satisfaction.
The primary purpose of QMS is to enhance customer satisfaction by ensuring that organizations meet both legislation and quality standards through systematic improvement processes. Whether through the implementation of ISO 9001 standards or other tailored approaches, QMS serves as a strategic asset.
Significance in Modern Business
In the context of contemporary business climates, the significance of QMS cannot be overstated.
Companies that implement effective quality management systems experience:
- Improved Customer Loyalty: By prioritizing quality, businesses signal to customers their commitment to excellence, which fosters loyalty.
- Enhanced Operational Efficiency: A QMS streamlines operations and reduces waste, leading to cost savings.
- Focus on Continuous Improvement: Structures in QMS encourage organizations to seek and implement improvements consistently.
- Better Compliance with Standards: In an era of strict regulations, having a QMS helps companies stay compliant with industry benchmarks.
Core Components of a Quality Management System
In the expansive landscape of quality management systems, identifying and understanding the core components is crucial. These elements operate together, ensuring consistent performance, enhancing efficiency, and ultimately leading to improved customer satisfaction. A well-implemented QMS does not only aim for adherence to standards but also establishes a framework for continuous improvement.
Quality Planning
Quality planning lays the groundwork for achieving organizational quality goals. It involves setting objectives, determining the resources needed, and defining the processes that will be utilized. Companies must ensure regulatory requirements and customer expectations are met. Effective quality planning can reduce risks and enhance operational performance by aligning quality initiatives with business strategies.
Key aspects of quality planning include:
- Setting Quality Objectives: Formulate clear and measurable objectives to assess the effectiveness of quality efforts.
- Resource Allocation: Identify and allocate the necessary resources for achieving the quality objectives.
- Process Definition: Specify processes required for compliance and customer satisfaction by utilizing appropriate standards and best practices.
By consolidating these elements during the quality planning phase, organizations can achieve more focused and efficient operations.
Quality Control
Quality control encompasses the specific methods and activities used to measure quality within a production process. The primary objective is to identify defects or irregularities in production before products reach the customer. These preventative measures not only minimize waste but also enhance customer experience.
Some common quality control techniques include:
- Inspections: Regular reviews and evaluations at various stages of production help in the early identification of faults.
- Testing: Implementing rigorous product testing ensures that only products that meet quality standards get through.
- Corrective Actions: When defects are found, prompt corrective actions must be executed to avoid recurrence.
By incorporating these practices, businesses can ensure consistency in the quality of their output.
Quality Assurance
Quality assurance focuses on the entire process of generating products or services while ensuring quality is integrated into every step. This is proactive, aiming to prevent issues before they occur. Implementing comprehensive quality assurance programs streamlines operations and positively impacts performance and customer trust.
Key activities involved in quality assurance include:
- Documentation Review: Ensuring that all processes are adequately documented, which facilitates adherence to policies.
- Training and Development: Ongoing training equips employees with necessary skills to maintain quality standards.
- Audits: Regular internal and external audits help sustain compliance, uncover potential areas for improvement, and validate system efficiency.
Following these processes, quality assurance ensures that products and services consistently meet or exceed customer expectations, reflecting the organization's ethos of quality management.
Quality Improvement
The commitment to quality does not conclude with quality planning, control, or assurance. Instead, organizations must establish a continuous quality improvement culture. This involves initiatives actively geared toward elevating processes, products, and services over time. Recognizing areas that require advancement leads to innovation and the capability to respond to changing market demands.
Various tools used for quality improvement include:
- Plan-Do-Check-Act (PDCA): This iterative approach allows organizations to formulate and assess experiments before making larger changes.
- Root Cause Analysis: Identifying and eliminating the fundamental causes of issues contribute to long-term solutions.
- Performance Metrics: Utilizing key performance indicators to monitor and gauge success is vital to determine the impact of improvement initiatives.
In essence, quality improvement is an active pursuit, driving innovation and promoting agility within businesses.
Categories of Quality Management Tools
Quality management tools play a crucial role in achieving organizational goals. Understanding these tools is essential for any company that aspires to adhere to excellence standards. The right category of tools can aid in analyzing performance, maintaining customer satisfaction, and constantly improving processes. Each tool serves a specific purpose in the overall system, ensuring that businesses can manage and enhance their quality control mechanisms efficiently.
Statistical Tools
Statistical tools often help in quantifying performance and productivity sectors. When organizations rely on objective methods for measuring their processes, they can select best practices for increasing quality. Statistically sound tools support credible decision-making based on data-related insights.
Descriptive Statistics
Descriptive statistics is focused on summarizing or describing characteristics of a data set. For many, it is the first step in dealing with quantitative data.
This aspect is valuable in determining means, medians, and modes, providing clarity to complicated datasets. The key characteristic of descriptive statistics lies in its ability to simplify large amounts of data into understandable information. Many professionals benefit from their approachable nature for beginners in data analysis.
A distinctive feature of descriptive statistics is it does not deal with uncertainty or prediction; it presents a clear depiction of the current situation. Thus, it can sometimes feel limiting, not providing predictive insights for further decision-making.
Control Charts
Control charts monitor changes in processes over time and help in identifying variations. They are essential for maintaining a state of control within processes.
Control charts stand out due to their graphical representation of data and its components. By representing variations, they pinpoint issues in the production process quickly. Their widespread acceptance is due to this efficiency in visual monitoring.
However, understanding control charts might come with a learning curve, sometimes discouraging less technical professionals.
Process Capability Analysis
Process capability analysis evaluates how much a process meets specifications. Companies utilize this tool to quantify a process's output relative to its expected behavior.
The main advantage is its quantifiable nature, enabling businesses to make data-driven decisions regarding process enhancements. A key characteristic is that it focuses on both performance and regulation adherence, making it multifaceted.
The downside might be the complexity behind the metrics involved, which may hinder its practical application without proper expertise.
Process Improvement Tools
Process improvement tools are integral to enhancing productivity and efficiency. Implementing these tools helps in fine-tuning operations and ultimately leads to customer satisfaction.
Lean Techniques
Lean techniques aim for waste reduction and enhancing value for the end consumer. Their effectiveness is rooted in fostering organized workflows.
A noteworthy aspect of lean techniques is their emphasis on continuous improvement through direct analysis of consumer requirements. The elegance in their straightforward approach contributes to their popularity.
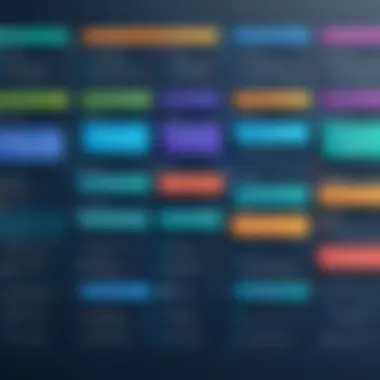
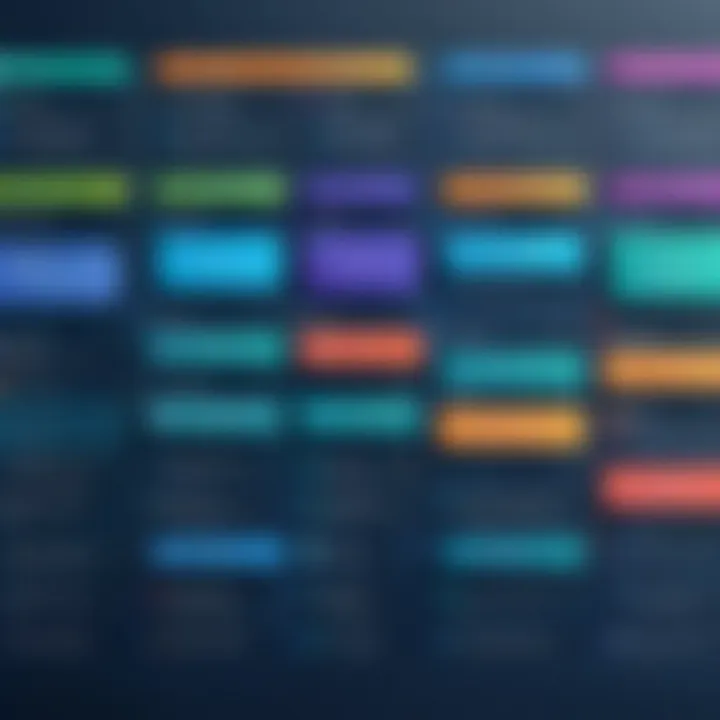
Lean techniques main feature is focusing on process aspects to ensure maximum efficiency. Though these methods offer transformations, they may encounter resistance from personnel accustomed to traditional processes.
Six Sigma Methodology
Six Sigma is a systematic approach aimed at improving processes through data analysis. It has gained prominence due to its effectiveness in quality enhancement.
The fundamental objective embodies minimizing defects in output. Thus, understanding the principles can lead to higher achievement levels, lower costs and enhanced customer satisfaction. An intricate feature of Six Sigma is the application of statistical analysis, thereby elevating the decision-making process.
Valuable, yet it may come across as too rigorous or complex, discouraging those who are less technical as it requires dedicated training.
Value Stream Mapping
Value stream mapping is a lean management tool representing the flow of materials and information. This represents a comprehensive snapshot all along the process.
The primary benefit revolves around identifying bottlenecks and wasteful activities, in a detailed manner. Value stream mapping allows companies to visualize their entire process, which stands out as a unique feature.
Still, mapping might require some time investment and regular updates, particularly in dynamic industries. The effort is worth it as it leads to improved throughput and streamlining processes.
Documentation Tools
Documentation tools are essential in maintaining operational consistency, providing standards necessary for effective quality management. Quality manual, audit checklist and standard operating procedures contribute to widespread understanding across the organization.
Standard Operating Procedures
Standard operating procedures (SOPs) illustrate step-by-step processes necessary for routine tasks within the organization. These provide clarity and a standardized method to train staff effectively.
A key component of SOPs is that they encode organizational knowledge and wisdom. For those new to tasks, these documents are invaluable aids, presenting step-by-step guidelines. The limitation potentially includes them being considered overly bureaucratic.
Quality Manuals
Quality manuals encapsulate policies detailing the organization's commitment to quality and providing guidance.
These documents ensure employees can relish an overview of expectations regulated across departments, serving as beneficial reference points. The unique characteristic here is it fuels a culture around quality. However, when poorly crafted, they could also become too vague or unaccountable, failing to define clear procedures.
Audit Checklists
Audit checklists facilitate evaluations of processes to identify any non-conformance with set standards.
They act as feasibility instruments during assessments, acting as a framework where important elements are evaluated. This form of documentation looks easy but it may not ensure rigorous audits when used incorrectly, which could undermine its potential.
Digital Tools for Quality Management
Digital tools are becoming essential in the framework of quality management systems. They provide efficiency, accuracy, and continuity within various operations. The integration of these tools simplifies processes and enhances data-driven decision-making. Businesses investing in these technologies often notice significant improvements in their operational frameworks and customer satisfaction.
Software for QMS
Cloud-Based Solutions
Cloud-based solutions offer versatile platforms for businesses looking to enhance their quality management systems. One key aspect is their accessibility; users can access the software from anywhere with internet connection. This flexibility eases collaboration among teams, no matter where they are situated. Notably, the automatic updates ensure that all users benefit from the latest features without extra input or expenses. Talking about benefits, the cost-effectiveness makes it a popular choice among smaller companies that may not have extensive resources.
However, there are disadvantages too. Concerns about data security and privacy are prominent, as sensitive information is stored externally. Organizations must prioritize strong security measures for adaptagen those risks.
Enterprise Resource Planning Systems
Enterprise Resource Planning (ERP) systems integrate various functions into one complete system to streamline processes and information across the organization. A significant characteristic is their ability to centralize data, allowing diverse department functions like finance, production, and customer service to communicate efficiently. Some ERP systems offer built-in quality management functions which assist teams in preserving standards throughout their operations. Many companies opt for some ERP featuring quality modules as they provide an all-in-one solution tailored to overarching business needs.
Yet, the complexity and costs involved in implementing ERP can lead to challenges. Proper training for users and possible disruptions during the transition phase must be considered. In addition, selecting a suitable ERP can overwhelm businesses with many available options.
Document Management Systems
Document management systems play a crucial role in managing critical files within a quality management system. They integration well in compliance processes. A key feature is that they enable easy document retrieval, ensuring that relevant files are accessible at any moment. This capability greatly benefits organizations that require strict adherence to regulations or must conduct audits regularly, allowing them to present documentation quickly and efficiently. Popular among various sectors, this kind of software supports maintaining quality standards throughout the document lifecycle.
However, the initial setup can be time-consuming, requiring significant effort to digitize and organize existing paperwork. Therefore, planning and resource allocation are essential for a successful transition to using these tools.
Data Analytics and Reporting
Data analytics and reporting are integral to understanding quality management. By analyzing data, organizations derive meaningful insights that guide their improvement endeavors. A significant aspect of data-driven quality management is continuous improvement, achieved by utilizing these analytics effectively.
Business Intelligence Tools
Business intelligence tools empower decision-makers with actionable insights derived from data analysis. The main characteristic of these tools is rich functionality combined with user-friendly interfaces boosting adoptability across various teams. Businesses favor them because they facilitate quick data analysis and enhance strategic planning. Users can create comprehensive reports and streamline processes easily, making these tools critical in modern operations.
Nonetheless, the challenge lies in ensuring employees are trained. Without adequate user knowledge, these tools can often return underutilized, limiting their full potential.
Predictive Analytics
Predictive analytics has reshaped how organizations approach quality management. By loading large quantities of historical data into predictive models, businesses can foresee potential quality issues before they arise. This proactive approach is advantageous as it saves resources and mitigates risks.
The productivity benefit is a key reason for popularity amongst industries experiencing high variability. On the downside, reliance on predictive methods might overlook important qualitative factors that data alone can't represent. Organizations should use this alongside other traditional methods for best results.
Dashboards and Reporting Tools
Dashboards provide an effective way to visualize Key Performance Indicators (KPIs) for the quality management process. These tools allow for real-time monitoring of quality metrics, making it easier to assess performance. An essential characteristic is vivid graphical representations boosting rapid interpretation by all data levels. Therefore, whether to evaluate production processes or compliance levels, dashboards deliver clarity.
However, possess attention is needed as selecting appropriate metrics to monitor is crucial; irrelevant data misinterpretations can mislead decisions negatively. In addition, investing in software with customizability features ensures dashboards remain relevant as requirements change.
Conclusion: Investing in digital tools for quality management is advantageous. They provide myriad benefits, but the challenge is ensuring effective implementation and user engagement.
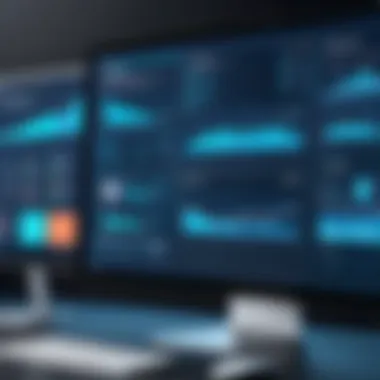
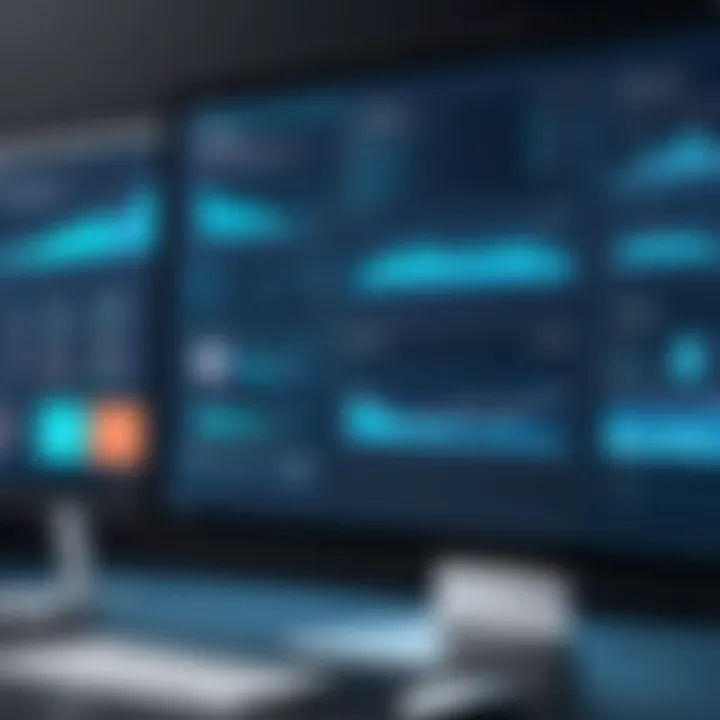
Implementing Quality Management Tools
The significance of implementing quality management tools within organizations extends far beyond mere compliance and efficiency. These tools are crucial for creating a systematic approach to managing and improving quality processes. Proper implementation can lead to enhanced performance, reduced costs, and improved customer satisfaction, essential in today’s competitive landscape.
Benefits of Implementing Quality Management Tools:
- Improved product and service quality.
- Increased stakeholder confidence.
- Better process control and efficiency.
- Enhanced decision-making capabilities supported by data.
- Increased employee engagement through structured processes.
However, the true potential of these tools can only be realized when they are effectively integrated into the organization’s existing processes and culture. This brings about a need for careful planning, adequate training, and alignment of quality objectives with overall business goals.
Steps for Effective Implementation
Implementing quality management tools is a structured process involving several key steps:
- Assessment of Current Processes:
Begin by evaluating existing quality management practices to identify gaps and areas for improvement. This analysis will facilitate decision-makers in pinpointing what tools may need to be adopted. - Defining Quality Objectives:
Clearly outline quality goals aligned with the organization’s strategic vision. Specific and measurable targets will guide the tool’s implementation and enable performance tracking over time. - Selecting Appropriate Tools:
Analyze available quality management tools that match the defined objectives. Consider the unique needs of your organization when finalizing selections, such as Statistical Process Control, Six Sigma, or Document Management Systems. - Training and Involvement:
Facilitating training sessions for employees ensures that everyone is competent in using the tools. Engaging staff during implementation fosters a culture of quality and ownership. - Continuous Monitoring and Adjustment:
Once implemented, have a system in place for ongoing assessment of effectiveness. Monitoring outcomes and soliciting feedback will provide valuable insights and guide necessary adjustments.
Challenges in Implementation
While the implementation of quality management tools is essential,Several challenges could hinder success:
- Resistance to Change: Employees might resist new tools or processes, preferring familiar methods. Involving them in the change process can help ease this transition.
- Insufficient Training: Without adequate knowledge and skills, employees may struggle with new tools. Comprehensive training and support at all organizational levels can mitigate this risk.
- Resource Limitations: Some organizations might not allocate enough budgetary or personnel resources for effective implementation, while operators often overschedule projects, leading to rushed or inadequate installations.
- Lack of Leadership Support: Without an organizational commitment from management, implementing quality management tools might not be prioritized, making progress slow.
Overcoming these challenges requires diligent planning and proactive management strategies, paving the way for better-quality outcomes.
Case Studies of Successful Implementation
Examining real-world applications helps illustrate successful implementations of quality management tools:
Example 1: Toyota’s Production System
Toyota successfully incorporated Lean and Six Sigma methodologies in its processes, dramatically improving operational efficiency and quality. By focusing on value-add components and eliminating waste, Toyota set benchmarks followed by industries worldwide.
Example 2: Boeing’s Quality Tools
Boeing leverages a mix of automation and quality analytics for enhancing their manufacturing accuracy. Utilizing specific tools, such as quality audits and software analytics, continues to enhance performance and maintain international standards.
Example 3: The Ritz-Carlton
With a focus on customer experience, The Ritz-Carlton employs quality management tools to ensure high service standards. Its effective training programs help inculcate a strong quality culture among employees, resulting in repeat business and brand loyalty.
These cases demonstrate that careful thought followed by necessary resources and training can significantly elevate quality management achievements across various industries.
Future Trends in Quality Management Tools
Understanding future trends in Quality Management Tools is vital for organizations striving for excellence. As demographics shift and technology evolves, a proactive approach will ensure that quality management remains relevant and impactful. This section highlights specific trends shaping the landscape of Quality Management Systems.
Integration of AI and Machine Learning
The integration of Artificial Intelligence and Machine Learning is transforming quality management disciplines significantly. These technologies enable deeper insights by analyzing complex datasets in less time. By automating repetitive tasks, they allow quality managers more capacity to focus on strategic decisions.
Algorithms are capable to predict defects even before they occur. Consistent use of such predictive analytics can lead to fewer quality issues and less wastage of resources.
Benefits of AI in Quality Management Include:
- Real-time data analysis. Faster decision-making is possible using real-time data feeds. This helps prevent issues occurring at stages of production.
- Anomaly detection. Machine learning algorithms can wear flags if expectations are not met. This enhances quality assurance initiatives.
- Cost savings. AI capabilities lower the amount of time spent on quality checks compared to humans, leading to lower operational costs and increased productivity.
The thought of employing AI requires approaching with careful planning. Companies should also prioritize training for staff to work alongside intelligent systems effectively.
Enhanced Data Visualization Techniques
Data visualization techniques play a crucial role in quality management. As the volume, variety, and velocity of data increase, relying solely on traditional reporting methods becomes insufficient. Enhanced techniques simplify complex information, conveying insights visibly and interactively.
Tools such as Tableau and Microsoft Power BI provide visual analytics to drill down into quality metrics quickly. Feature-rich dashboards allow decision-makers easier access to overview processes and current standings at a glans.
Key aspects of data visualization for quality management:
- Immediate insights. Issues become easier to spot with visual contexts often indicating problems quicker than numbers can demonstrate.
- Greater collaboration. Visual reports then promote discussions around quality and encourage collective problem-solving.
- User engagement. Presentations using visuals engage subject experts actively, compared to minimal participation in conventional discussion formats.
Shift Towards Agile Quality Management
The shift towards Agile Quality Management demands flexibility and rapid adaptation to changes. In today’s business environment, adjustments occur swiftly. Recognizing this urgency means embracing principles rooted in Agile methodologies.
Agile techniques enable teams to operate in iterative cycles. Testing products consistently is a methodic focus. This flexibility factors strongly into quality management approaches in an organization.
Elements in Agile Quality Management Include:
- Adaptability. Teams have the capacity to pivot quickly. Changing conditions or feedback instantly impact processes positively.
- Continuous improvement. Adjustment occurs at each stage. Input and learning assimilate through iterations to enhance the quality outcome.
- Customer-centric focus. Outcomes prioritize customer feedback, ensuring the produced goods align with expectations.
These trends are not just trends, but rather transformations. By embracing and understanding their implications, organizations can put themselves ahead, ready for future challenges in quality management. Investing time in learning about and employing these trends enhances organizational resilience and efficacy in quality outcomes.
Closure
In this article, the topic of conclusion serves a pivotal role in wrapping up the various facets of Quality Management Systems (QMS) tools. A well-rounded conclusion synthesizes insights from each section, thereby reaffirming the importance of quality tools in enhancing organizational performance. It provides a clear pathway for professionals to reflect on the implementation, advantages, and prognosis of quality management strategies.
Summary of Key Insights
Quality management tools streamline processes, improve efficiencies, and facilitate ongoing improvement within an organization. Some critical insights include:
- Diverse Categories: The continuoum of quality tools ranges from statistical and process improvement tactics to technical documentation methods.
- Consideration of Future Trends: The integration of AI and enhanced data visualization represents a turning point in quality management practices.
- Real-World Applications: Companies integrating an effective QMS show remarkable performance adaptations, which are evident from various case studies reviewed in this article.
When reflecting on these insights, professionals can recognize how these tools not only fulfill reporting needs but also influence overall business outcomes.
Call to Action For Businesses
Organizations should take deliberate steps towards embracing quality mngmnt tools. Some actionable recommendations are:
- Assess Current Systems: Evaluate existing quality processes to identify gaps.
- Invest in Training: Training staff on the use of new tools can drive successful implementation.
- Adapt Agile Practices: As highlighted, businesses should focus on iterative cycles of improvement, incorporating feedback in real time.
Fostering a strong quality management culture is not just advisable but essential in today's innovative landscape. By adopting these strategies, businesses will likely achieve significant growth and resilience in their operations.
Ultimately, recognizing the relevance of quality management tools leads to better strategic decisions and tuned operations.