Exploring Information Warehouse Management Systems
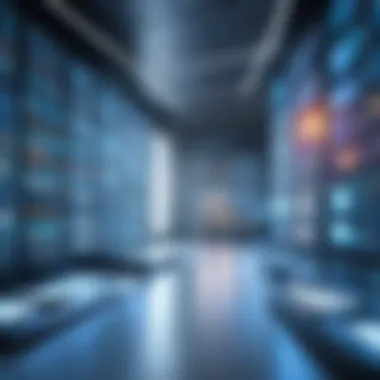

Intro
In the fast-paced world of modern business, managing data effectively is becoming a cornerstone of strategic success. Information Warehouse Management Systems (WMS) represent a crucial technological advancement, enabling companies to streamline their operations, enhance productivity, and utilize their data intelligently.
With the surge in available data, organizations are tasked with not just storing this information but also making sense of it. Warehouse Management Systems provide tools and frameworks that keep businesses agile, allowing them to pivot quickly and make informed decisions. From optimizing supply chains to ensuring compliance with regulations, WMS plays a multifaceted role in today’s business landscape.
In this article, we’ll unfold the complexities of WMS, providing a detailed examination of their components, relevance, and how they integrate with broader technological infrastructures. The goal is to shed light on how these systems can be leveraged for better operational efficiency and strategic advancement in diverse business sectors.
Preface to Warehouse Management Systems
In today’s fast-paced business landscape, Warehouse Management Systems (WMS) play a crucial role in streamlining operations. Understanding WMS is not just a trend, it's a necessity for businesses that aim to be competitive. These systems serve as the backbone of supply chain management, ensuring that goods are stored, picked, packed, and shipped with maximum efficiency.
A well-designed WMS contributes to the larger business goal by enhancing accuracy in inventory tracking and improving order fulfillment times. Decisions made based on real-time data from WMS can lead to significant cost savings and customer satisfaction. With e-commerce continuing to grow, many enterprises find that inadequate warehouse operations can stifle growth or lead to lost sales. Thus, comprehending the importance of Warehouse Management Systems becomes essential as businesses react to changing demands and strive for operational excellence.
Defining Warehouse Management Systems
Warehouse Management Systems (WMS) are software solutions designed to support and optimize warehouse functionality and distribution center management. This definition is straightforward, yet the implications are vast. At their core, WMS allow for the detailed management of inventory, which means that every item in stock can be tracked at any time. They automate various processes—everything from receiving and storing goods to picking and shipping them out.
A robust WMS provides:
- Real-time inventory tracking, minimizing losses through potential mismanagement.
- Order processing capabilities, ensuring that customer orders are handled efficiently.
- Reporting tools for data analysis, allowing managers to make informed decisions.
In essence, WMS acts like the central nervous system of warehouses, providing vital information almost instantaneously, which helps businesses to react swiftly to customer needs.
Historical Context of WMS Evolution
The world of warehouse management has witnessed a dramatic evolution over the years. Initially, warehouses operated with basic barcoding systems and manual processes. As businesses grew, there was an increasing demand for improved efficiency and accuracy, leading to the first-generation WMS in the late 20th century.
As technology progressed, so did WMS. The advent of RFID and voice recognition technology helped in automating processes, greatly reducing human error and speeding up operations. The introduction of cloud computing shifted the landscape further, allowing businesses of all sizes to access sophisticated systems that were once only available to large corporations.
Today, modern WMS not only manage inventory but also integrate seamlessly with various technologies like AI and machine learning, predicting trends and optimizing operations on a whole new level. Understanding the historical context of WMS not only provides insight into current technologies but also sheds light on the future potential of these systems in evolving business landscapes.
Core Components of WMS
Understanding the core components of Warehouse Management Systems (WMS) is crucial for any business aiming to enhance its operational practices. Each of these components plays a significant role in streamlining processes, reducing errors, and improving overall efficiency. When businesses grasp the function and integration of these core elements, they can make informed decisions that lead to a more agile and competitive operation.
Inventory Management
Inventory management lies at the heart of any effective WMS. It's about more than just knowing what's in stock. This component includes tracking inventory levels, managing storage locations, and ensuring data accuracy concerning stock on hand. A sophisticated inventory management system enables businesses to optimize their inventory turnover rates, reducing excess stock and minimizing holding costs. It also supports businesses in forecasting demand more effectively, leading to smarter purchasing decisions.
For example, imagine a retail business that experiences seasonal fluctuations. With a solid inventory management system, this retailer can adjust its stock levels in anticipation of an increase in demand during festive seasons, thereby avoiding stockouts or overstock situations that lead to unnecessary expenses.
Order Fulfillment
Order fulfillment is another integral component of WMS that directly affects customer satisfaction. It involves every step from receiving incoming orders to processing and dispatching them. An effective order fulfillment system ensures that orders are picked, packed, and shipped efficiently, which significantly boosts customer experience. When orders are fulfilled accurately and promptly, it directly contributes to brand loyalty and customer retention.
One key aspect of order fulfillment is the ability for businesses to automate processes. Rather than relying on manual labor, integrating automation tools can enhance accuracy and speed. For instance, using barcode scanners for order picking doesn't only reduce human error; it also accelerates the entire fulfillment process.
Shipping and Receiving Management
Shipping and receiving management focuses on the logistics of inbound and outbound shipments. It ensures that efficient practices are in place for receiving goods and dispatching orders. This component encompasses everything from scheduling shipments to tracking deliveries.
Start-ups to large enterprises can benefit from optimizing these processes. Consider a scenario where a company integrates real-time tracking capabilities into its shipping management. This enables both the business and its customers to monitor shipments throughout the delivery journey, resulting in enhanced transparency and trust in service.
Reporting and Analytics
In an age dominated by data, the reporting and analytics component of WMS can't be overlooked. This aspect provides businesses with actionable insights into their operations. By analyzing data regarding inventory levels, order processing times, and shipping schedules, decision-makers can spot trends and identify areas needing improvement.
For instance, a company might discover through analytics that certain products are consistently delayed in shipping. This insight allows them to reassess their supply chain, adjust processes, or negotiate better terms with suppliers, leading to a more streamlined operation.
"Informed decisions driven by data lead to improved warehouse operations and higher customer satisfaction."
Benefits of Implementing WMS
The concept of implementing a Warehouse Management System (WMS) is often seen as a significant step forward in warehouse operations. This section delves into the different ways a WMS can enhance business efficiency, aid in better inventory management, and ultimately lead to an uplift in customer satisfaction. These benefits are not merely theoretical; they translate into tangible improvements that can transform the logistics sector.
Enhanced Operational Efficiency
One of the most vital advantages of a WMS is its ability to improve operational efficiency. In the day and age where time is money, speeding up processes can yield substantial savings. For instance, with a WMS in place, tasks such as picking, packing, and shipping can be streamlined. Workers can find items faster, as the system directs them to the most efficient paths within the warehouse. This not only saves time but also minimizes the chances of human error.
- Using barcodes or RFID scanning integrated with WMS speeds up order processing.
- Automating repetitive tasks reduces the burden on staff, allowing them to focus on more complex duties.
This magic of efficiency means that warehouses can handle more orders simultaneously, thus scaling operations without requiring a linear increase in manpower. Companies can achieve better throughput, which means fulfilling customer orders more quickly and accurately.
Accurate Inventory Control
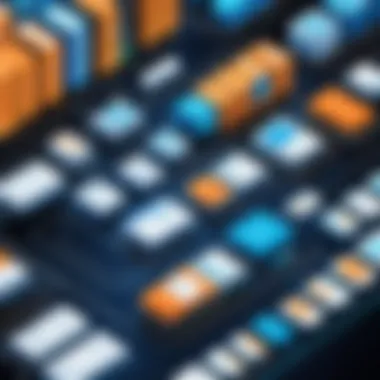
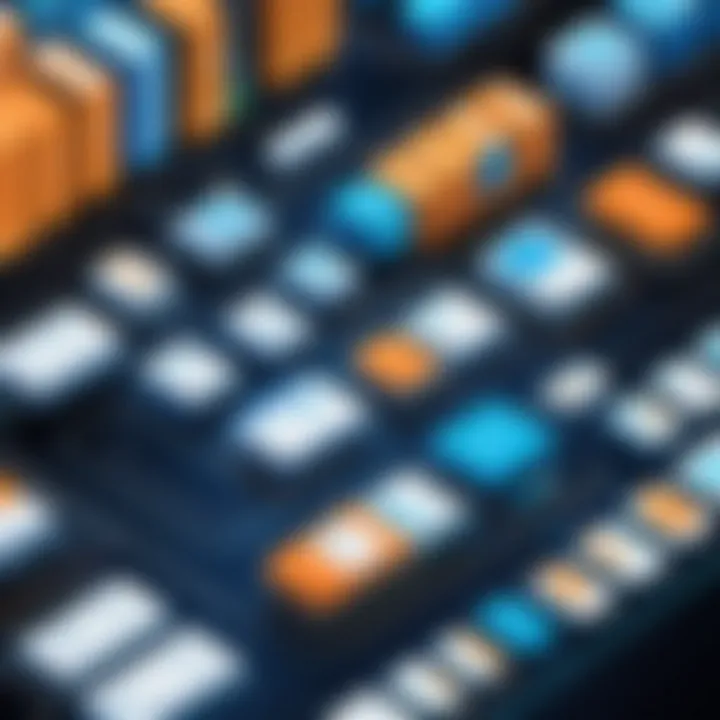
Another cornerstone of WMS implementation is the improvement of inventory control. Traditional inventory management can often lead to miscalculations and discrepancies. The WMS utilizes real-time data that helps keep track of stock levels, which translates into more accurate forecasting and reduced instances of overstock or stockouts.
- A well-implemented WMS updates inventory levels automatically. This real-time tracking prevents discrepancies that could lead to costly errors.
- Enhanced visibility into inventory allows businesses to make data-driven decisions. This means ordering supplies just in time to meet current demands.
Because an effective WMS integrates seamlessly with other data systems, it allows businesses to analyze and make sense of large volumes of data. Hence, organizations can maintain optimal inventory levels and improve supply chain relationships, all while reducing carrying costs.
Improved Customer Satisfaction
In a fiercely competitive marketplace, customer satisfaction can set businesses apart. A robust WMS leads to fewer errors, quicker deliveries, and more reliable service. When orders are filled accurately and shipped on time, customers notice—positively impacting a company’s reputation.
- Accurate order fulfillment means customers receive what they ordered, reducing return incidents and boosting trust.
- Efficient shipping can result in faster delivery times, which enhances customer experience. People love knowing exactly when their orders will arrive!
Ultimately, when customers are satisfied, they tend to return for future purchases. Hence, targeting a better warehouse management system can lead to more repeat business, positively impacting the company's bottom line.
"In today’s fast-paced world, efficiency isn’t just a luxury; it’s a necessity for success."
By recognizing the benefits that come with implementing a WMS, businesses can sidestep potential pitfalls and focus on what truly matters—delivering value to their customers. The trick is knowing how to reap these rewards while also navigating the operational challenges that come with adopting such systems.
Challenges in WMS Adoption
Adopting a Warehouse Management System (WMS) can be a game-changer for businesses. However, it’s akin to navigating a minefield; understanding the challenges involved is crucial for ensuring a successful implementation. Ignoring these hurdles may lead to disruptions, inefficiencies, and a morale dip among employees. In this article segment, we dive into the nitty-gritty of the challenges faced during WMS adoption, particularly focusing on the specific aspects of cost, integration with existing systems, and the often-overlooked resistance to change.
Cost of Implementation
When considering a WMS, the elasticity of a company’s budget becomes quite apparent. The initial investment can be staggering. Not only are there upfront costs related to software purchases or licenses, but also expenses tied to hardware, infrastructure upgrades, and training sessions for personnel.
For instance, a mid-sized company might find itself shelling out tens of thousands of dollars just to get the system up and running. But that’s just the tip of the iceberg. Ongoing maintenance, updates, and potential costs for additional features or modules must also be considered.
- Understanding Total Cost of Ownership:
- Initial Costs: Software, Hardware, Training
- Recurring Costs: Maintenance, Upgrades
- Hidden Costs: Downtime during implementation
While a WMS can lead to long-term savings and efficiency, the initial burden can be daunting. Companies need to conduct a thorough cost-benefit analysis to determine whether the benefits outweigh these initial sticker shocks.
Integration with Existing Systems
Integrating a WMS with pre-existing systems often turns into a jigsaw puzzle—pieces that should fit together seamlessly but frequently don't. For many businesses, legacy systems and outdated processes create barriers that complicate the integration process.
A WMS typically needs to work with various enterprise systems, like Enterprise Resource Planning (ERP) and Customer Relationship Management (CRM). Without proper synchronization, the flow of information can become chaotic, leading to inefficiencies and mistakes.
- Common Integration Hurdles:
- Data Inconsistencies: Differences in data formats can lead to syncing errors.
- Technical Compatibility: Older systems might not support new capabilities.
- Lack of Skilled Personnel: Need for staff who understand both systems to bridge the gap.
Such integration challenges can consume valuable time and resources, which some organizations may not have in abundance.
Resistance to Change within Organizations
Resistance to change is often more than just a bump in the road; it can be a significant obstacle. Employees might feel apprehensive about adjusting to a new system, especially if they’ve grown comfortable with older processes. This reluctance can stem from various elements, including fear of job loss, user uncertainty regarding the new technology, or a general dislike for changing established workflows.
- Factors Influencing Resistance:
- Lack of Involvement in the Decision-Making Process: If employees weren’t part of the selection process, they might not be fully onboard.
- Insufficient Training: Employees need proper training to feel confident in using the new system.
- Cultural Hurdles: Workplace culture that is averse to change will amplify resistance.
Creating an environment conducive to change adoption requires clear communication, regular feedback, and, perhaps most importantly, buy-in from all levels of the organization. Education on how a WMS can positively affect workplace efficiency and job roles is key to alleviating fears.
"The secret of change is to focus all of your energy, not on fighting the old, but on building the new." - Socrates
Understanding these challenges is vital for any organization contemplating a WMS implementation. Every barrier encountered offers a lesson, often shaping a company’s growth and adaptability in the long run.
Key Features of an Effective WMS
In today's fast-paced business landscape, an effective Warehouse Management System (WMS) isn’t just a nice-to-have; it's critical for operational success. The following features stand out as essential for any WMS aiming to elevate warehouse performance.
Real-time Data Processing
One of the cornerstones of an effective WMS is real-time data processing. This means that updates to inventory levels, order statuses, and shipment tracking happen instantly, allowing for immediate decision-making. With real-time data, businesses can respond to stock fluctuations and customer demands as they occur. For instance, if a shipment is delayed, the system automatically alerts warehouse managers and customers, preserving transparency. In essence, such immediacy ensures that all operations are aligned and responsive, reducing the chances of errors that might arise from outdated information.
Some benefits of real-time data processing include:
- Improved Accuracy: By minimizing the lag between actions and updates, the risk of discrepancies in inventory data is significantly reduced.
- Increased Agility: Companies can pivot quickly in response to market changes or unexpected events, maintaining a competitive edge.
"Real-time data is like having a pulse on the warehouse – it enables quick shifts and adaptations to keep everything running smoothly.”
User-friendly Interfaces
A WMS can have the most robust features, but if its interface isn’t user-friendly, it’s not going to be much help. User-friendly interfaces ensure that employees can navigate the system with ease, reducing training costs and time. A well-designed interface often includes intuitive workflows, easy access to frequently used features, and clear visual cues, which can greatly enhance productivity.
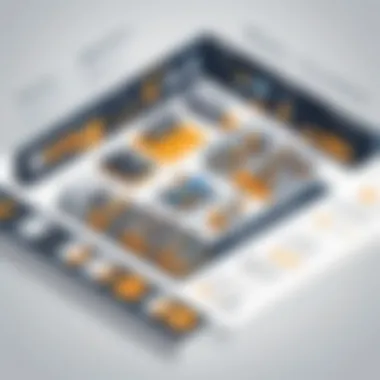
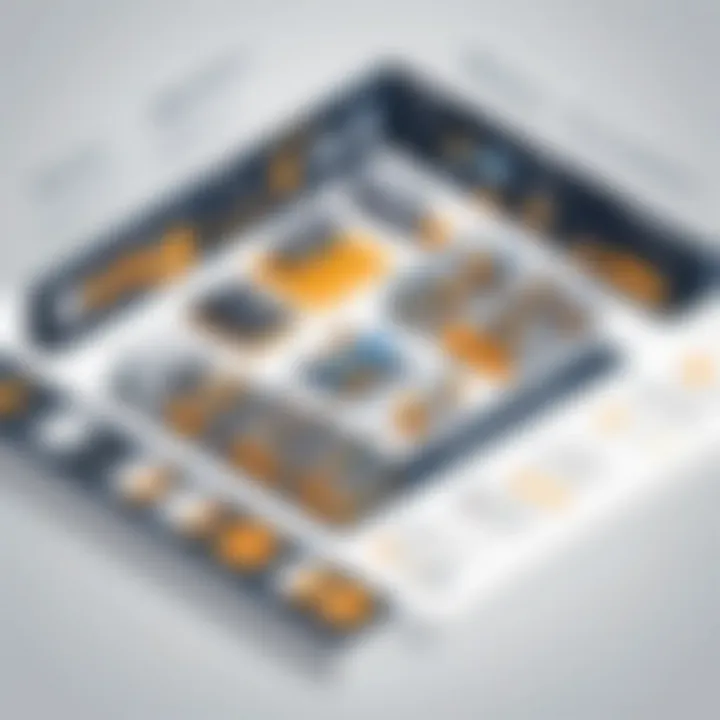
Key aspects of user-friendly interfaces include:
- Customizable Dashboards: Ability for users to create dashboards that cater to their specific roles, enabling quick access to the information they need.
- Mobile Compatibility: With many operations occurring on the floor, mobile access allows staff to manage tasks without being tethered to a desktop.
The importance of a seamless user experience cannot be overstated; it directly impacts how well a team adapts to the system.
Scalability and Flexibility
Finally, an effective WMS must be scalable and flexible enough to adapt to changing business needs. As businesses evolve, their inventory and order fulfilment demands may grow or shift. A WMS that can scale up operations without a hitch enables a company to expand its services or responsiveness. Moreover, flexibility to integrate with other tools or technologies—like ERP or CRM systems—ensures that a WMS can evolve alongside a business.
Consider these points regarding scalability and flexibility:
- Future-proofing Investments: Opting for a modular design means businesses can add or remove functionalities as needed without overhauling the entire system.
- Adapting to Market Changes: Flexibility enables a warehouse to quickly pivot towards new processes or workflows, which can be crucial during market shifts or during times of disruption.
Integrating WMS with Other Technologies
Integrating Warehouse Management Systems (WMS) with other technologies is a pivotal component in modern logistics and supply chain management. It enhances the visibility, efficiency, and usability of data across different operational frameworks. When systems work in harmony, the potential for optimizing processes and improving decision-making escalates significantly.
The reasons to integrate WMS range from enhancing workflow automation to facilitating real-time data sharing. This integration is not merely a technical necessity; it shifts the whole operation into a more cohesive unit, enabling companies to respond promptly to market changes. Whether it's adapting to flash sales or managing unexpected demand spikes, integrated systems allow for agile responses, offering a competitive edge in a bustling marketplace.
Enterprise Resource Planning Systems
Enterprise Resource Planning (ERP) systems are integral to the business's backbone, managing various functions like finance, procurement, and human resources. Integrating WMS with ERP systems creates a symbiotic relationship that significantly enhances operational visibility. Such integration allows for:
- Streamlined Data Flow: Rather than siloed information, data can move seamlessly between inventory, finance, and order management.
- Real-time Insights: With data flying in the same direction, decision-makers gain clearer, more accurate insights into inventory levels and order statuses.
- Cost Reduction: By automating processes like order entry or inventory replenishment, businesses can reduce labor costs and administrative errors.
For example, a distribution center equipped with an integrated WMS and ERP can adjust quickly to stock outages by reordering, depending on real-time consumption data, optimizing inventory levels without delay.
Customer Relationship Management Systems
Customer Relationship Management (CRM) systems are crucial for managing company interactions with current and potential customers. When integrated with WMS, marketers and sales teams gain unparalleled insights into order histories and inventory availability. This interaction fosters:
- Personalized Customer Experiences: With accurate data, companies can tailor their offerings based on purchasing behaviors or previous interactions.
- Improved Sales Forecasting: By monitoring order cycles, CRM-integrated WMS can predict future sales trends more effectively, allowing for informed planning.
- Increased Customer Satisfaction: Accurate inventory data ensures that promises made to customers regarding delivery and stock levels can be met reliably.
Take for instance a retail business that utilizes both CRM and WMS: They could automatically notify customers about updated order statuses or suggest complementary products based on purchase patterns.
Artificial Intelligence in WMS
AI's role in optimizing operations cannot be emphasized enough, especially regarding WMS. Integrating AI technologies with WMS elevates operational efficiencies through:
- Predictive Analytics: AI can analyze historical data to forecast demand, helping businesses prepare for fluctuations in inventory.
- Automated Replenishment: With intelligent algorithms, systems can suggest when to reorder stock, which alleviates manual monitoring.
- Enhanced Decision-Making: AI tools can deliver actionable insights, helping managers fine-tune logistics through smarter supply chain strategies.
For example, utilizing machine learning algorithms within a WMS can drastically improve space management within warehouses, optimizing storage assignments based on patterns over time.
"Ultimately, the magic of integrating WMS with various technologies lies in improving not just efficiency but also agility. This promises a responsive operation ready to take on the complexities of today's market."
Future Trends in Warehouse Management
As the landscape of logistics and supply chain management continues to evolve, it's vital to keep an eye on the horizon for emerging trends. The future of Warehouse Management Systems (WMS) is shaped by advancements in technology and shifts in consumer demands. Understanding these trends is not just a matter of curiosity; it’s essential for businesses aiming to stay competitive and efficient.
The integration of cutting-edge technologies will allow businesses to enhance their operational practices, improve customer satisfaction, and streamline processes. Embracing future trends will enable organizations to adapt to changes in the market, ensuring they remain agile and relevant.
The Rise of Automation and Robotics
In recent years, automation and robotics have become buzzwords within the warehousing sector. These technologies promise to revolutionize how goods are stored, processed, and dispatched. Automation can significantly reduce the labor required for specific tasks, such as picking and packing. For example, using automated guided vehicles (AGVs) to transport items across a warehouse cuts down on time and human error.
Moreover, robots can operate around the clock, maximizing output and minimizing delays. As the cost of robotics technology decreases, it’s becoming more accessible for small- and medium-sized enterprises.
- Advantages of Automation and Robotics:
- Increased efficiency and reduced operational costs.
- Enhanced accuracy in inventory management.
- Improved worker safety by reducing repetitive tasks.
Automation isn’t just about machines assuming the workload; it's also about integrating these systems seamlessly with existing WMS. In doing so, companies can better track inventory and optimize storage methods and order fulfillment processes.
"The integration of robotics in warehouse management transforms operations into a high-efficiency battleground, where speed and precision reign supreme."
Cloud-based WMS Solutions
The cloud continues to alter the landscape of many sectors, and warehouse management is no exception. With cloud-based WMS solutions, businesses can operate with greater flexibility and scalability. These systems allow for real-time data access, meaning decisions can be based on the most accurate and current information without the hassle of traditional server setups.
Using cloud-based systems can also lead to lower operational costs, as organizations can avoid substantial investments in hardware. This model makes WMS solutions more appealing to startups and smaller players looking to optimize their warehouse operations without breaking the bank.
- Key Benefits of Cloud-based WMS:
- Accessibility from any location, fostering remote management and monitoring.
- Enhanced collaboration across teams and departments.
- Continuous updates and improvements without significant downtime.
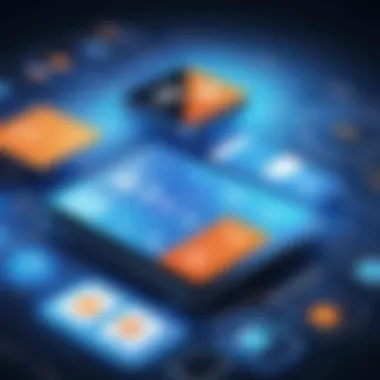
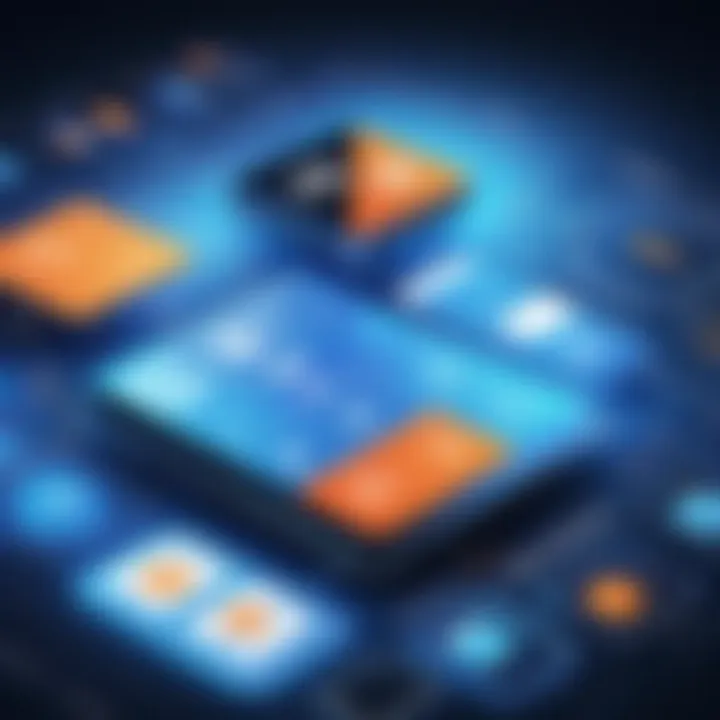
As organizations expand, cloud-based solutions offer the agility that on-premises systems cannot match. This makes them ideal for businesses looking to scale operations quickly and efficiently.
Data Analytics and Predictive Insights
Data is king in today's digital world, and warehouses are starting to reap the benefits of advanced analytics. Predictive analytics embedded in WMS can provide invaluable insights into inventory trends, seasonal fluctuations, and consumer behavior. By leveraging historical data, businesses can forecast demand more accurately than ever.
This capability doesn't merely aid in stock management; it can also inform strategic decision-making across the organization. Having real-time analytics allows for on-the-fly adjustments to inventory levels, potentially preventing stock-outs and ensuring a more responsive approach to customer demands.
- Benefits of Data Analytics in WMS:
- Improved inventory turnover and reduced holding costs.
- Enhanced demand forecasting and supply chain planning.
- Ability to implement proactive rather than reactive strategies.
The evolution towards data-driven insights means that businesses will not only react to problems as they arise but will anticipate issues before they manifest, driving increasingly efficient operations.
As we look forward, it’s crucial to embrace these developments in warehouse management. By preparing for automation, leveraging cloud-based solutions, and harnessing the power of data analytics, organizations can position themselves for success in a rapidly evolving marketplace.
Selecting the Right WMS for Your Business
Choosing the right Warehouse Management System (WMS) is crucial to the success of your business. A well-selected WMS streamlines operations, boosts inventory accuracy, and enhances customer satisfaction. As companies grow and adapt, their warehousing needs evolve, making this selection process even more vital. While it might seem like just another tech decision, the implications reach far and wide, touching everything from your bottom line to your market reputation.
Assessing Your Business Needs
Before diving into the myriad of options, take a moment to gather your thoughts on what exactly your business needs. You wouldn’t buy a suit without knowing your measurements and style preferences; the same principle applies to a WMS. Consider the scale of your operations. Are you managing thousands of SKUs or just a handful? The complexity of your inventory is often a key driver in this decision.
Think about your current processes. Are you maximizing the efficiency of your existing setup? Mapping out workflow patterns can reveal pain points and redundancies which a new system could address.
- Inventory Volume: How much product do you handle?
- Operational Complexity: Is your workflow straightforward or intricate?
- Growth Plans: Are you expecting to scale up in the near future?
Ultimately, grasping your needs firmly grounds you in the selection journey.
Evaluating Vendor Offerings
Once you've assessed what you require, turn your attention toward potential vendors. Not all WMS solutions are created equal, and evaluating them against your specific needs is the next logical step. Look for vendors that not only showcase their technology well but also demonstrate an understanding of your industry.
Consider these key points:
- Functionality Fit: Does the vendor’s product cover all necessary functionalities? You need features like inventory tracking and reporting capabilities, but maybe something like returns processing is also crucial for your operation.
- User Experience: Scheduling demos can provide insight into how user-friendly a system is. If your staff have to struggle with obtuse interfaces, it won't matter how powerful the system is.
- Vendor Reputation: A company with a track record of successful implementations is usually a safe bet. Check out reviews or speak to references to gauge their reliability.
By honing in on these aspects, you can find a vendor that fits your business like a glove.
Considerations for Custom Solutions
In some instances, off-the-shelf solutions may not adequately meet your unique needs. When off-the-shelf products miss the mark, tailor-made options come into play. Custom solutions can be a double-edged sword, though; they are often more expensive and complex to implement.
Nonetheless, if you find yourself needing features that mainstream systems simply can’t offer, this path might be worth exploring. Here are some aspects to evaluate:
- Cost-Benefit Analysis: Can your budget sustain the increased costs of a custom solution? Weigh the investment against potential returns.
- Timeline for Implementation: Custom builds typically take longer. Consider how that affects your operational continuity.
- Future-proofing: Will the custom solution be easy to adapt as your operations evolve? Flexibility and scalability are crucial considerations.
By informing yourself about these elements, you're setting the stage for a successful WMS selection that ideally matches both your current requirements and future ambitions.
"Investing in the right WMS can be the difference between operational chaos and seamless efficiency."
With careful thought and analysis, you can navigate the complexities of selecting a WMS that not only meets your present needs but also supports growth over the years.
Best Practices for WMS Implementation
Implementing a Warehouse Management System (WMS) is not just a technical exercise; it necessitates strategic planning and foresight. Best practices for WMS implementation lay a foundation that can harness the full potential of these systems, enabling organizations to streamline operations and enhance productivity. Understanding these practices is crucial for professionals seeking to navigate the complexities of modern warehouse management.
Developing a Clear Implementation Plan
A solid implementation plan acts as a roadmap guiding the journey of integrating a WMS into existing operations. It is essential to begin with a detailed analysis of current workflows, identifying the specific pain points that the WMS will address. This requires collaboration among various stakeholders, from warehouse personnel to IT staff, ensuring that everyone’s insights are factored into the planning stage. A well-structured plan can include:
- Goal Definition: Clearly outline the objectives of implementing the WMS. Whether aiming for improved accuracy or increased speed of order fulfillment, defining these goals is foundational.
- Timeline Creation: Establish realistic timelines for each phase of the implementation. A rushed deployment can lead to mistakes that compound challenges down the road.
- Budget Allocation: Carefully evaluate costs associated with software, hardware, and potential training programs. This helps in avoiding unpleasant financial surprises later on.
Ultimately, a meticulous plan not only minimizes disruptions during the transition but also sets the stage for realizing ongoing benefits from the WMS.
Training and Support for Users
Training is arguably one of the most critical components of WMS implementation. Without proper user training, even the best system can falter. Employees need to be comfortable and adept at using the new tools at their disposal. To effectively prepare them:
- Customized Training Sessions: Tailor training to different user groups. For instance, the needs of pickers differ from those of inventory managers, and training should reflect these differences.
- Hands-on Experience: Providing opportunities for hands-on training helps users gain confidence. Simulated scenarios enable users to familiarize themselves with the system without the pressure of real-time operations.
- Ongoing Support: Everyone knows that no system is perfect. It’s vital to have a support mechanism in place, like a dedicated help desk or regular check-ins post-implementation, to address any questions or concerns that arise after deployment.
By creating a robust training and support framework, organizations can significantly boost user adoption rates, minimizing resistance and maximizing efficiency.
Continuous Monitoring and Improvement
After the deployment of a WMS, the journey doesn't end; it’s only just begun. Continuous monitoring of system performance is vital to identify areas that might need adjustment. Regularly evaluating how well the WMS meets business objectives keeps the organization agile and responsive. Key aspects to focus on include:
- Performance Metrics: Utilize key performance indicators (KPIs) that correlate with operational goals, such as order fulfillment times, inventory accuracy, and system uptime.
- User Feedback: Conduct periodic surveys or feedback sessions with users to gather insights on system performance and areas for improvement. This user-centered approach can reveal issues that metrics alone might not illustrate.
- Iterative Updates: Technology changes fast. Staying informed about new features and updates from your WMS provider allows the organization to take advantage of enhanced functionalities.
Being proactive about monitoring and optimizing your WMS can lead to sustained improvements and a better competitive edge over time.
In summary, following best practices in WMS implementation ensures a smooth transition and fosters an environment that encourages continuous growth and optimization. These foundations will not only enhance today’s operations but also empower businesses to adapt to ever-evolving demands.