Understanding MRP Systems and Their Business Impact
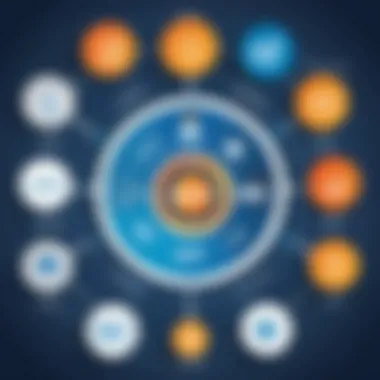
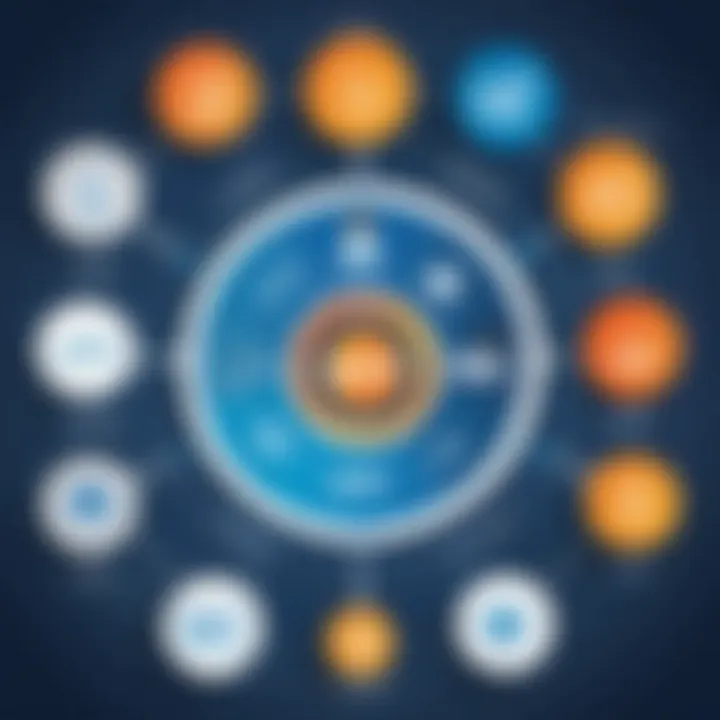
Intro
Understanding the Manufacturing Resource Planning (MRP) system is essential for navigating today's complex business landscape. MRP is not just a tool; it's a framework that allows organizations to manage their production processes effectively and efficiently. In a world where resources are often limited, and customer expectations are ever-increasing, businesses need to harness the power of MRP to remain competitive. This article will explore the intricate components of MRP, how it integrates with other systems, and the implications of its implementation on overall business performance.
As the saying goes, "a stitch in time saves nine." In this context, timely and accurate resource planning can save companies from costly production delays and inventory shortages, making them more agile and profitable. We'll delve into how MRP systems function, the technological innovations shaping their evolution, and the data-driven decisions that fuel their effectiveness. One crucial point to remember is that although MRP systems can provide significant advantages, there are also challenges and limitations to consider. Understanding these factors holistically will empower you to make well-informed decisions regarding MRP adoption within your organization.
Technological Research Overview
In today's fast-paced market environments, technology significantly influences how MRP systems operate. Understanding recent innovations and their impacts can help businesses harness new tools for optimizing resource planning.
Recent Technological Innovations
Recent advances in technology have transformed the landscape of MRP systems. Companies are increasingly turning to cloud computing for MRP solutions, allowing them to access data in real-time from anywhere. This has led to a greater emphasis on data synchronization across platforms, streamlining operations and enhancing responsiveness.
Impact on Business Operations
With technology at the helm of MRP innovations, companies have observed profound improvements in their operational efficiency. For instance, inventory management is more accurate, reducing excess stock and minimizing waste. Additionally, with the growing application of machine learning algorithms, companies can predict demand more accurately, leading to better production scheduling and overall resource allocation. This responsiveness helps mitigate risk and aligns businesses with market dynamics seamlessly.
Future Technological Trends
As we look ahead, emerging trends like Artificial Intelligence (AI) and the Internet of Things (IoT) are poised to revolutionize MRP systems even further. AI can automate routine tasks, freeing up human resources for strategic decision-making, while IoT devices can offer real-time data on production processes. These advancements are likely to push MRP systems toward greater integration, efficiency, and adaptability.
"The future belongs to those who prepare for it today."
This quote serves as a reminder of the importance of staying ahead of technological advancements and being willing to adapt.
Data Analytics in Business
In the modern business world, data analytics plays a crucial role in guiding decision-making processes. MRP systems, with their vast amounts of operational data, benefit significantly from data-driven insights.
Importance of Data Analytics
Utilizing data analytics allows businesses to make informed decisions grounded in reality rather than guesswork. Understanding customer purchasing patterns, production timelines, and inventory turnover rates can drive efficiency and effectiveness in resource planning.
Tools for Data Analysis
Numerous tools exist to facilitate data analysis in the context of MRP systems. Software solutions like Tableau, Microsoft Power BI, and Google Data Studio can help visualize and interpret complex datasets. These tools enable businesses to sift through raw data and extract actionable insights, propelling smarter decisions.
Case Studies on Data-Driven Decisions
Numerous organizations have turned their fortunes around by leveraging data analytics alongside MRP systems. For example, a well-known retailer used predictive analytics to optimize their supply chain. By accurately forecasting demand, they reduced stock-outs by 20%, enhancing customer satisfaction and boosting sales.
Cybersecurity Insights
As businesses increasingly shift towards digitization, the importance of cybersecurity cannot be overstated. With MRP systems handling sensitive data, firms must implement strong security measures to protect against breaches.
Threat Landscape Analysis
MRP systems can be vulnerable to cyber threats, including phishing attacks and malware. Understanding the threat landscape is the first step in mitigating risks, enabling organizations to identify potential hazards and prepare accordingly.
Best Practices for Cybersecurity
Implementing robust cybersecurity practices is paramount. Regular software updates, employee training on security protocols, and using multi-factor authentication are some foundational steps to bolster your defenses against cyber threats.
Regulatory Compliance in Cybersecurity
Businesses must be aware of regulatory requirements concerning data privacy and security. Compliance with frameworks like GDPR in Europe or HIPAA in the United States is crucial for protecting customer information and avoiding legal repercussions. Cozying up to these regulations not only safeguards against data breaches but also enhances credibility with customers.
Artificial Intelligence Applications
The integration of AI in MRP systems is transforming the way businesses handle production and planning.
AI in Business Automation
AI drives efficiency by automating routine tasks, which in traditional MRP frameworks is often labor-intensive. From inventory management to demand forecasting, AI can analyze vast datasets quickly and effectively, leading to faster decision-making processes.
AI Algorithms and Applications
Various algorithms are specifically designed for improving MRP functions. Machine learning algorithms can identify patterns in historical data to optimize future outcomes, ensuring production levels align with market demands.
Ethical Considerations in AI
While the benefits are clear, it is vital to consider the ethical implications of AI in MRP systems. Ensuring transparency in decision-making processes and mitigating biases in algorithms should be a priority for organizations aiming to foster trust and integrity.
Industry-Specific Research
Understanding the implications of MRP systems also involves recognizing the unique challenges and opportunities different sectors face.
Tech Research in Finance Sector
In finance, MRP systems assist in resource allocation, regulatory compliance, and risk management. Advanced analytics and forecasting models are helping financial institutions make informed decisions about future investments.
Healthcare Technological Advancements
The healthcare sector benefits from MRP systems by streamlining supply chain processes, which can be a matter of life and death. MRP systems help ensure that medical equipment and supplies are available when needed.
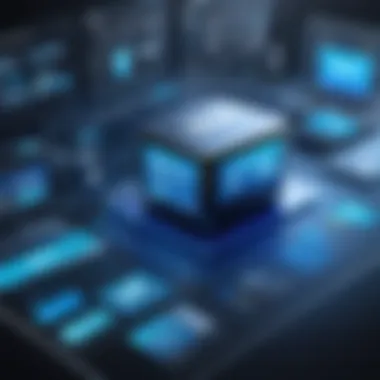
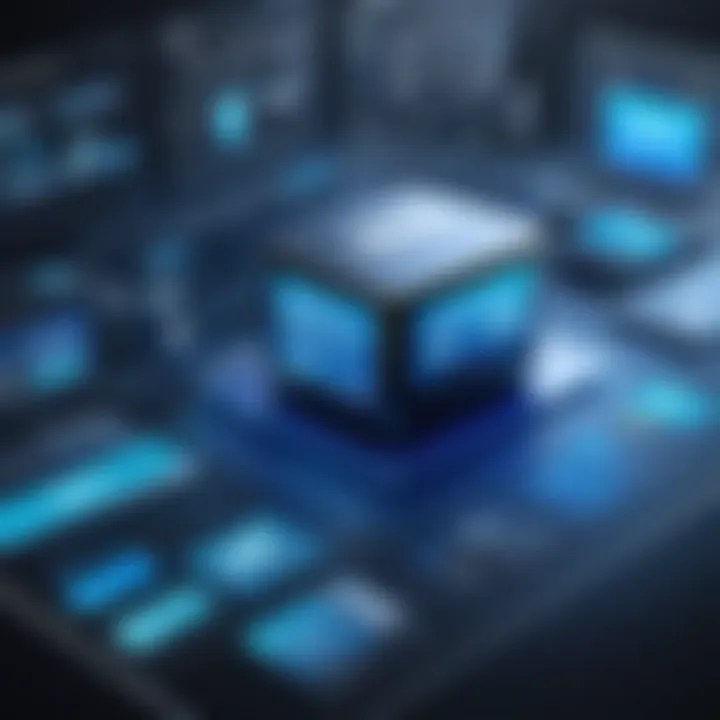
Retail Industry Tech Solutions
As the backbone of inventory management, MRP systems in retail help businesses respond promptly to changing consumer demands. This responsiveness is critical in todayās fast-paced shopping environments, where customer preferences can shift overnight.
Through this exploration, the significance of the MRP system becomes increasingly clear. It provides a robust framework for managing resources effectively, ensuring operational efficiency, and tackling the unique challenges faced in different industries.
Defining the MRP System
Understanding the MRP system is crucial, particularly in the context of contemporary manufacturing and production environments where efficiency reigns supreme. At its core, the Manufacturing Resource Planning (MRP) system is designed to streamline production processes by facilitating a harmonious integration of various components such as inventory control, scheduling, and demand forecasting. With today's rapid pace of technological advancement, itās more important than ever for businesses to not only grasp what MRP is but also to understand the tangible benefits it can provide.
The MRP system primarily offers a framework that assists organizations in managing their inventory and production schedules effectively. By aligning these elements closely, businesses can reduce excess stock, minimize waste, and ultimately improve their overall responsiveness to market demands. The implications of an effective MRP system are extensive; it can lead to significant cost savings, improved customer satisfaction, and a notable increase in operational efficiency.
Historical Background
The roots of MRP date back to the 1960s when manufacturers were grappling with the challenge of efficiently managing their resource availability against production schedules. Initially, MRP systems were rudimentary, focusing primarily on managing components and production schedules based on push methodologies. Over the decades, advancements in computing technology led to more sophisticated software solutions that optimized these processes further.
In the early days, MRP relied heavily on manual inputs and calculations, making it prone to errors. As businesses recognized the need for accuracy, the system evolved into smaller applications that integrated directly with inventory management and scheduling tasks. This transition marked a significant turning point. By the 1980s, MRP had become a cornerstone in the toolkit of many manufacturers, paving the way for more integrated frameworks, ultimately leading to what we know today as ERP (Enterprise Resource Planning).
Basic Principles of MRP
The guiding principles of MRP can be distilled into a few essential components, each playing a vital role in overall functionality:
- Demand-driven Production: MRP systems are fundamentally designed around the idea of producing based on actual demand rather than forecasts. This helps organizations keep their production lines flexible and responsive.
- Inventory Optimization: By carefully monitoring inventory levels, MRP systems aim to maintain just enough stock to meet production needs without becoming overstocked. This balance not only reduces carrying costs but also minimizes the risk of obsolescence.
- Time-phased Planning: Effective planning is at the heart of MRP. By utilizing time buckets, businesses can plan and schedule resources more effectively, ensuring that the right materials are available at the right time.
- Feedback Loop for Data Accuracy: A strong MRP system incorporates feedback mechanisms to continually assess and refine inventory levels and production schedules based on real-time data. This iterative approach helps to enhance system reliability and reflects changing market conditions.
With these principles, the MRP system acts as the backbone of manufacturing processes, ensuring that resources are utilized efficiently while also adapting to changes that may arise within the market or supply chain.
"A well-implemented MRP strategy is not just a tool; it's a philosophy that prioritizes efficiency and foresight in production management."
By deftly understanding the MRP systemās definitions, historical development, and fundamental principles, professionals can better navigate the complexities involved in todayās dynamic manufacturing landscape.
Key Components of MRP Systems
Understanding the key components of MRP systems is crucial for any organization aiming to optimize its manufacturing capabilities. These elements form the backbone of how MRP systems function, directly influencing efficiency and effectiveness in production. Each component brings its own set of benefits, but they must work in harmony to achieve the desired outcomes. Below, we will examine three fundamental components: Inventory Management, Demand Forecasting, and Production Scheduling. The interplay between these components can lead firms to harness their resources much more effectively, ensuring they meet customer needs without inflating costs.
Inventory Management
At the heart of any MRP system lies Inventory Management. Proper management of inventory ensures that materials are available for production without incurring excessive carrying costs. In other words, itās all about striking a balance. If a company holds too much inventory, it ties up capital unnecessarily, while having too little can lead to production delays and customer dissatisfaction.
- Just-In-Time (JIT) Concept: Many organizations strive to adopt a JIT inventory approach where materials arrive as they are needed. This reduces stock on hand and minimizes waste.
- Real-Time Data Tracking: Using MRP systems allows managers to track inventory levels in real-time. This tracking is vital in avoiding stockouts and ensuring a smooth production flow, thus keeping the lines moving and the dollars coming in.
- Safety Stock: Companies must also maintain a safety stock, which acts as a buffer in case unexpected demand spikes occur. Balancing safety stock levels carefully mitigates risks while keeping the warehouse from overflowing.
Effective inventory management is not just about having enough stock; itās about knowing how much and when.
Demand Forecasting
Demand Forecasting serves an integral role in the functionality of MRP systems. It involves predicting future customer demands through historical data analysis and market trends. This forecasting process is essential for planning production schedules and aligning inventory needs.
- Historical Data: By analyzing past sales data, companies can identify seasonal trends and cycles. For instance, a toy manufacturer may see a spike in demand during the holiday season, guiding them to ramp up production in time.
- Collaboration and Communication: Effective demand forecasting depends on collaborative efforts across departmentsāespecially sales and marketing. Insights from these teams can enrich the accuracy of forecasts, enabling organizations to plan needed resources effectively.
- Adjusting Projections: Market shiftsālike economic downturns or consumer behaviour changesārequire companies to remain agile. MRP systems can accommodate fluctuating data, allowing for timely adjustments to production plans, ultimately preventing overproduction or underproduction.
Production Scheduling
Lastly, Production Scheduling ties everything together in an MRP framework. This component helps plan and organize production activities, ensuring timely output that meets market demand.
- Optimized Use of Resources: Effective scheduling leads to an optimized use of resources, where operators, machinery, and raw materials are allocated efficiently. For example, scheduling maintenance during lower production periods can save time and money in the long run.
- Lead Time Considerations: Scheduling must consider lead times, basically how long it takes to get materials. For example, if a supplierās delivery is delayed, it could throw the whole production schedule off balance.
- Flexibility in Change: Markets can shift on a dime. Therefore, an MRP system's scheduling component should maintain flexibility, allowing managers to adjust timelines as necessary.
Each of these components bears considerable weight on the overall success of an MRP system. They donāt just work in isolation but are interconnected gears in the machine of manufacturing management. Recognizing their roles enables businesses to harness the power of MRP, leading to better efficiency and sustainability.
Functionality and Workflow of MRP
The functionality and workflow of an MRP system is the backbone that allows businesses to streamline their operations. By understanding how these components work together, organizations can more effectively manage their resources, improve decision-making, and enhance overall productivity. Each part of the MRP process plays a critical role in ensuring that manufacturing is efficient, well-coordinated, and responsive to market demand.
Input Components
At the heart of every MRP system is the input component. This section involves gathering essential data that drives the entire MRP process. The inputs typically include:
- Inventory Levels: Knowledge of current stock helps determine what items need to be reordered, ensuring that production is not interrupted.
- Bill of Materials (BOM): This is the recipe for products, outlining the raw materials and components needed for production.
- Master Production Schedule (MPS): A roadmap of what is to be produced, detailing quantities and delivery timelines.
- Customer Orders: Direct feedback from the market about what is being sold and when.
The accuracy and timeliness of these inputs are critical. If data quality issues arise, it can lead to excess inventory, stockouts, and ultimately, a diminishing bottom line. A common pitfall in organizations stems from dated information. Thus, routines for regularly updating data should be established, ensuring alignment with active production schedules.
Processing Data
Once data is collected, the real magic happens in the processing stage. Here, the MRP system analyzes inputs to determine the necessary actions. This process involves several calculations, including:
- Material Requirements Planning: It calculates the materials needed for production based on the BOM and MPS, factoring in lead times for each material.
- Resource Allocation: The system evaluates available resources, including machines and labor, optimizing their usage.
- Lead Time Consideration: Effective planning must account for supplier delivery schedules so that raw materials arrive just in time for production, striking a fine balance between availability and excess.
Effective processing yields more than just numbers; it provides actionable insights into production flows, helping businesses anticipate needs ahead of time. As a result, firms can avoid bottlenecks that could disrupt their output.
Output Results
The final part of the workflow involves the outputs produced by the MRP system. These outputs serve as the guideposts for operational activities and include:
- Purchase Orders: Indications of what to order, when to order it, and in what quantity, helping to maintain optimal stock levels.
- Production Schedules: Clear directives on what should be produced and in what timelines, minimizing downtime and ensuring that manufacturing aligns with demand.
- Performance Reports: Insights that evaluate the efficacy of production processes and inventory movement, paving the way for continual improvement.
To sum it up, the intricate tapestry of functionality and workflow in MRP systems is far from simple. Each stage ā from inputs to processing, and output results ā holds significant implications for a business's ability to adapt to market needs while keeping costs in check.

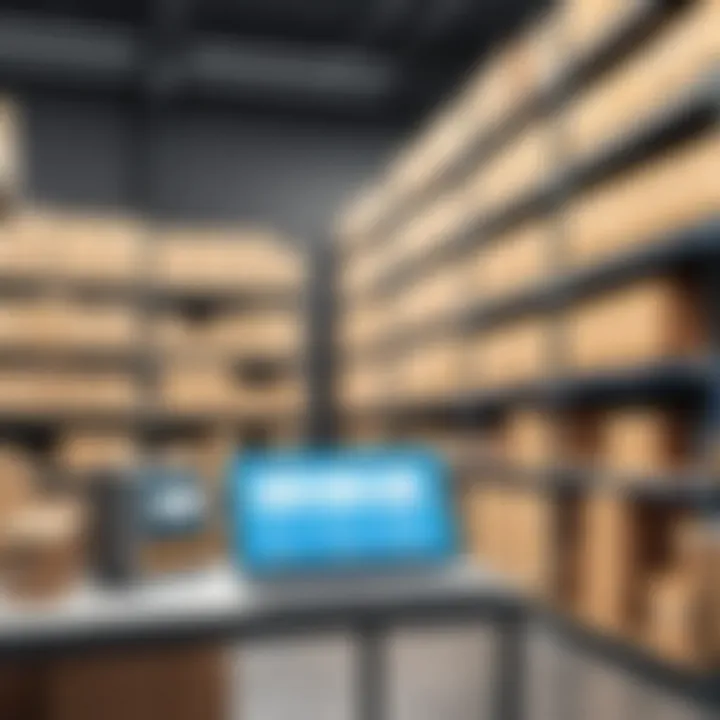
In the rapidly evolving landscape of manufacturing, mastering the MRP functionality and workflow is not just an asset; itās a necessity.
By dissecting these components, any organization can glean a clearer understanding of how an MRP system enhances their operational capabilities, directly influencing their competitiveness in the market.
Integration with Other Systems
In the realm of modern manufacturing and inventory management, the integration of systems is not merely advantageous ā itās critical. The Manufacturing Resource Planning (MRP) system does not function in isolation; rather, it intertwines with various systems to create a seamless flow of information. This interconnectedness fosters collaboration across departments, enhances operational efficiency, and ultimately drives performance improvements. Understanding how MRP integrates with other systems is crucial for any organization seeking to optimize its processes.
One headliner in the integration landscape is the Enterprise Resource Planning (ERP) system. This broad framework encompasses multiple functions within a company, from finance to human resources, and brings them under a single umbrella. By merging MRP with ERP systems, businesses achieve not only better data visibility but also improved strategic planning capabilities. The overlapping functionalities mean that operational insights gained through MRP can inform decisions across the organization, thus aligning resources more effectively.
Moreover, when considering integration with Supply Chain Management (SCM), the benefits multiply. Supply chain dynamics rely heavily on accurate demand forecasts, inventory levels, and production schedules. A well-integrated MRP system can communicate these variables in real time, which is invaluable for maintaining balance and minimizing excess.
"Integration ensures consistent data flow across departments, making it easier to respond swiftly to market changes."
Benefits of System Integration
The integration of MRP systems with ERP and SCM offers several notable benefits:
- Enhanced Data Accuracy: Reduces the risk of errors that can occur when managing data in silos.
- Quicker Decision-Making: Real-time information allows management to make quicker, more informed decisions.
- Streamlined Operations: Fewer duplicate processes mean less time wasted on tasks that don't add value.
However, organizations must be cognizant of certain considerations in this integration journey. Compatibility between systems can be a stumbling block; not all ERP or SCM solutions are created equal. Therefore, before jumping into integration, it's wise to perform thorough assessments to understand any potential barriers. Additionally, overcoming resistance to change in organizational culture is key. Getting buy-in from all stakeholders ensures a smoother transition.
In summary, the broader the integration, the greater the potential for growth and innovation. Organizations that view MRP as just one cog in the wheel miss the chance to leverage synergies that can lead to significant efficiency gains and improved market responsiveness.
ERP Integration
Integrating MRP with an ERP system brings various layers of advantages. For businesses grappling with numerous disparate systems, having a unified platform simplifies everything ā from project management to financial reporting. Under an umbrella of ERP, MRP contributes to financial visibility and operational insights, which helps in making the right decisions at the right time.
An MRP system aligned with ERP can automate many mundane tasks, reducing manual data entry and the associated risks of inaccuracies. Inventory levels, production schedules, and procurement needs can be dynamically adjusted based on comprehensive insights across the organization. Thus, MRP does not just serve production needs; it synchronizes vital resources across business functions.
Taking into account potential pitfalls, ERP integration is a project that requires careful strategic planning. The right approach means investing adequate resources in training and understanding user requirements. Compatibility tests and phased implementations can significantly mitigate risks associated with system fusion.
Supply Chain Management Roles
The relationship between MRP and Supply Chain Management (SCM) systems is symbiotic. MRP provides the fundamental data that drives SCM processes, while SCM enhances the effectiveness of an MRP system by providing context and demand signals that inform procurement and production timelines.
In practice, MRP systems use historical and forecasted demand data to schedule production runs, while SCM systems keep an eye on the flow of goods across the supply chain. When changes in market demand occur, an intuitive integration allows for fluctuation responses in production schedules without having to overstock inventory.
As a deeper dive, the roles within Supply Chain Management further magnify the importance of MRP integration:
- Inventory Managers: They need up-to-the-minute data from MRP to maintain optimal stock levels and avoid shortages.
- Production Planners: They rely on MRP outputs to develop efficient schedules, preventing bottlenecks and ensuring timely delivery.
- Procurement Officers: They benefit from integrated data to make informed purchasing decisions based on consumption patterns.
Overall, the integration of MRP into SCM fosters a holistic view of operations, resulting in improved customer satisfaction due to timely deliveries and better product availability. Thus, thoughtful integration of MRP can propel companies into a more harmonized and responsive operational mode.
Benefits of Implementing an MRP System
The integration of a Manufacturing Resource Planning (MRP) system is more than just a technological upgrade for businesses; itās a transformative approach that reshapes operations and drives long-term improvements in various aspects of the manufacturing process. By employing an MRP system, organizations unlock a treasure trove of benefits that directly contribute to responsiveness, efficiency, and overall management. This section dives deep into these advantages, outlining how they manifest in day-to-day operations while considering the vital elements that contribute to a robust manufacturing framework.
Enhanced Efficiency
One of the primary benefits of an MRP system is the enhanced efficiency it brings to manufacturing processes. Think of it as streamlining a river that once meandered through hills and valleys, creating a smoother path for productivity. MRP systems empower businesses to manage their resources effectively, ensuring that materials are available when they are needed without excess inventory piling up.
- Real-time Data Utilization: An MRP system relies heavily on real-time data. This allows companies to respond rapidly to changes in production demands, customer orders, or supply chain interruptions.
- Tailored Scheduling: With MRP, production scheduling becomes less of a guessing game. The system uses historical data and forecasts to generate informed production schedules, optimizing work processes and minimizing downtime.
In short, the systematic approach to maintaining optimal workloads leads to a more agile and responsive organization. As a result, businesses can fulfill customer needs promptly while avoiding the costs associated with inefficiencies.
Improved Inventory Control
Effective inventory management is another cornerstone benefit of implementing an MRP system. Picture a well-organized library; each book has its place. MRP does for inventory what an organized library does for books. Balancing stock levels is crucial to avoid the pitfalls of overstocking and stockouts, which can cripple any manufacturing operation.
- Optimized Stock Levels: MRP systems analyze demand forecasts and lead times, ensuring businesses maintain just enough inventory to meet customer demand without overcommitting resources.
- Automated Reordering: Setting reorder points becomes easy with MRP. The system triggers purchase orders automatically when stock dips below a predetermined level, ensuring that materials are always available for production.
Consequently, improved inventory control not only saves on holding costs but also enhances overall throughput by making sure the right materials are at the right place at the right time. This responsiveness is crucial in competitive industries, where delays can lead to lost sales and tarnished reputations.
Cost Reduction
Reducing costs while maintaining quality is a perpetual challenge in manufacturing. MRP systems help tackle this challenge head-on. Implementing an MRP system can be likened to finding a hidden treasure map that reveals where savings can be made throughout the supply chain.
- Waste Minimization: By accurately managing inventory and optimizing production schedules, businesses can reduce waste significantlyāboth in terms of materials and labor.
- Reduce Labor Costs: With streamlined processes, companies minimize overtime and underutilization of workforce resources. This ensures that labor is efficient and productive.
In essence, cost reduction is not merely about slashing expenses; itās about a strategic, calculated approach to manufacturing that enhances overall profitability without compromising quality.
Therefore, when a business adopts an MRP system, it's not just a decision to improve operationsāit's a strategic investment that yields dividends in efficiency, control, and cost savings, propelling the company towards greater competitiveness and sustainability in today's fast-paced market.
Challenges in MRP Implementation
Implementing a Manufacturing Resource Planning (MRP) system is no walk in the park. Businesses often encounter a series of challenges that, if not managed properly, could derail the entire process. Understanding these hurdles is crucial for professionals and decision-makers who are navigating the complexities of MRP systems. The importance of addressing these challenges lies not only in ensuring a successful deployment of the MRP system but also in maximizing its potential benefitsāstreamlined operations, improved inventory management, and enhanced overall productivity.
Data Quality Issues
At the core of an effective MRP system lies dataāaccurate, timely, and relevant data. However, many organizations face significant data quality issues when implementing an MRP system.
Data integrity is non-negotiable. Poor-quality data can mislead decision-making processes, resulting in suboptimal inventory levels, production delays, or even increased operational costs. For instance, if a company relies on outdated sales forecasts for production planning, it risks overproducing or underproducing, directly affecting its bottom line.
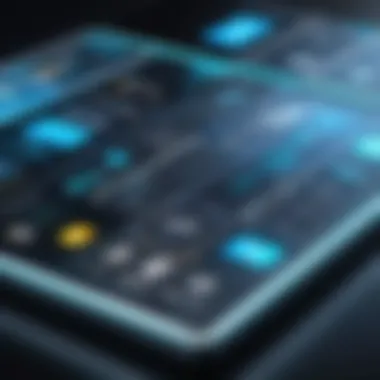
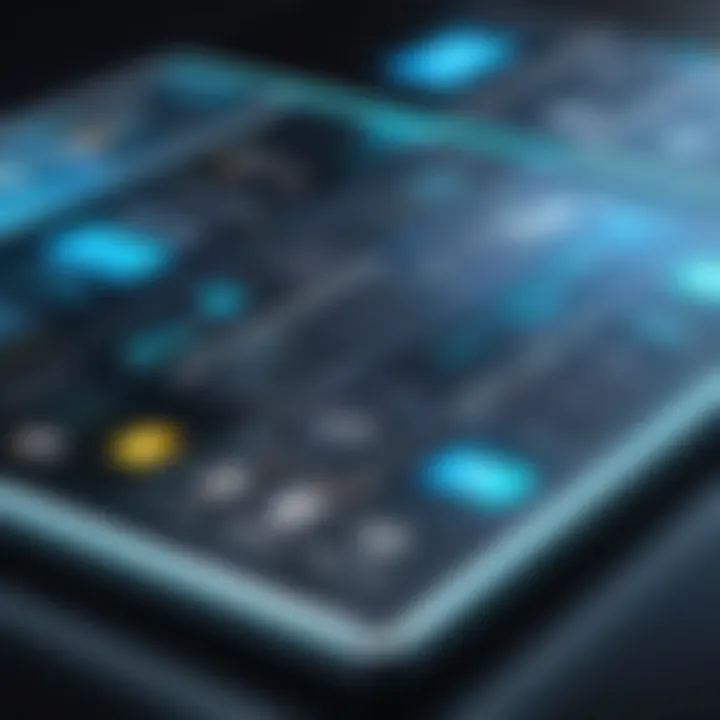
To curb these issues, businesses should establish stringent data governance frameworks that ensure data consistency and accuracy. Regular audits and reviews can help maintain data quality. Furthermore, engaging with all departmentsāsuch as sales, production, and supply chaināduring the data integration phase can foster a culture of accountability regarding data entry.
User Training Requirements
Itās not just about the software; itās about the people behind it. User training is a pivotal component in the successful implementation of any MRP system. Without adequate training, even the most sophisticated system will falter.
Imagine a scenario where operators are tasked with running an MRP system but lack the necessary knowledge to navigate its features effectively. This gap can lead to underutilization of the system and result in costly mistakes.
Organizations must prioritize training sessions that cater to users with diverse technical skills. A blended approach that includes hands-on tutorials, formal workshops, and the creation of user manuals can equip staff with the right know-how. Additionally, continuous education on system updates and best practices helps keep users informed and ready to adapt to changes.
Costs of Implementation
Let's face itācosts of implementation can be daunting. Designing, procuring, and deploying an MRP system often involves substantial financial investments. Many companies underestimate these costs, which can include not only software and hardware expenditures but also training, data migration, and ongoing maintenance expenses.
Hidden costs can add up quickly. For instance, unexpected downtime due to system integration issues can create a ripple effect, leading to lost productivity and missed deadlines. Companies need to conduct thorough assessments of both direct and indirect costs involved in the MRP implementation. A detailed cost analysis should factor in a timeline, necessary resources, and potential risks that can emerge during the implementation process.
"The cost of implementing an MRP system can be high, but the cost of not adapting to modern manufacturing practices could be even higher in the long run."
Ultimately, businesses must weigh the starting expense of implementing an MRP system against its long-term benefitsāimproved efficiency, enhanced inventory control, and increased profitability. By acknowledging the challenges in MRP implementation upfront, organizations can plan strategically to overcome them on their journey toward greater operational excellence.
Evaluating MRP System Performance
Evaluating the performance of an MRP system stands as a pivotal aspect of understanding its effectiveness in modern manufacturing contexts. This evaluation not only unveils how well the system functions but also highlights areas needing improvement, ensuring that resource allocation aligns with organizational goals. A well-functioning MRP system anticipates demands, manages inventory efficiently, and supports scheduling, making the evaluation of its performance crucial for operational success.
Through consistent assessment, companies can determine their productivity levels and understand how effectively the MRP informs their decisions. The insights gained from this evaluation become actionable strategies that drive efficiency, reduce costs, and enhance overall performance.
Key Performance Indicators (KPIs)
KPIs in MRP systems serve as the benchmarks illuminating the system's effectiveness and efficiency. These indicators guide organizations in tracking performance over time, helping them identify trends and areas for improvement. Some common KPIs to consider include:
- Inventory Turnover Ratio: This reveals how quickly inventory is sold and replenished, indicating product demand and inventory efficiency.
- Order Fulfillment Cycle Time: It highlights the time taken from order placement to delivery, informing the company's responsiveness and reliability.
- Capacity Utilization Rate: This metric shows how well the manufacturing capacity is being used, identifying potential bottlenecks in production lines.
By keeping a close eye on these KPIs, businesses can make informed decisions that will lead to adjustments in their strategies. Remember that KPIs should be tailored to match specific organizational goals and objectives to be effective.
Benchmarking Against Industry Standards
Benchmarking against industry standards adds another layer of context to MRP performance evaluation. It allows businesses to measure their practices against those of industry leaders, revealing gaps in performance and potential areas for improvement. The process often involves:
- Analyzing competitors' operational efficiencies and resource allocations.
- Identifying industry benchmarks for specific KPIs such as inventory turnover and order accuracy rates.
- Adjusting internal processes to meet or exceed these identified standards.
This comparative analysis is essential, offering insights into best practices that could be adopted to optimize operational performance. Staying stagnant is never an option; if organizations aspire to maintain relevance, they must measure themselves against the best in the business.
Moreover, benchmarking can foster a culture of continuous improvement and innovation within the organization. By striving to meet or exceed those standards, teams become motivated to enhance their processes, ultimately enjoying a competitive edge in the marketplace.
Future Trends in MRP Systems
As the dynamics of global business landscapes evolve, the Manufacturing Resource Planning (MRP) systems can't afford to lag behind. They are not just tools for inventory management and scheduling; they are becoming integral to a company's strategic framework. Understanding the future trends in MRP systems is essential for decision-makers, entrepreneurs, and tech enthusiasts. This section explores how different elementsālike automation, AI, and cloud-based solutionsāare shaping the MRP landscape, thereby offering avenues for improved efficiency, cost savings, and flexibility in operations.
Automation and AI Integration
In an era where speed and efficiency reign supreme, automation stands out as a game changer for MRP systems. The integration of artificial intelligence is setting the stage for a shift in how businesses approach manufacturing resource planning. For instance, AI algorithms can analyze historical data to forecast demand more accurately than traditional methods, allowing businesses to react swiftly to market changes.
Additionally, automation simplifies numerous MRP functions, such as inventory checks, reorder alerts, and scheduling tasks. This not only reduces human error but also liberates employees from repetitive tasks, allowing them to focus on higher-value activities. With automated systems in place, organizations can expect:
- Increased accuracy in data handling, which leads to fewer stock-outs and overstock situations.
- Better resource allocation, enabling companies to optimize their production schedules based on real-time data.
- Faster decision-making, making it easier to adapt to changing market conditions.
"The smarter the system, the quicker the response to market demands."
This highlighted sentiment sums up the essence of automation's role in MRP.
Furthermore, automation powered by AI can evolve over time. For instance, with machine learning capabilities, MRP systems could learn from past experiences, producing better projections and continuously enhancing their accuracy.
Cloud-Based Solutions
As technology meaningfully shifts how we do business, cloud-based solutions are emerging as vital contributors to modern MRP systems. Traditional systems often require hefty investments in infrastructure, leading to slow ROI and limiting accessibility for remote teams. Cloud-based MRP systems, on the other hand, offer a different ball game.
These solutions are characterized by:
- Scalability: Companies can easily adjust their resources based on fluctuating demands. Whether operating from a small workshop or a large factory, cloud systems allow businesses of all sizes to manage their resources effectively.
- Cost-effectiveness: Without the need for extensive hardware setups, businesses can save on upfront costs and choose flexible subscription models instead.
- Accessibility: Teams can access data from anywhere, enabling real-time collaboration and decision-making. This aspect has shown to be a boon, especially in times when remote operations have become necessary.
Moreover, cloud-based MRP systems are often updated automatically. This ensures that businesses are always equipped with the latest functionality and features without interruptions or additional costs.
Embracing cloud technology in manufacturing resource planning can pave the path to enhanced innovation and efficiency, making businesses more resilient and adaptive to future challenges.
Ending: The Role of MRP Systems in Modern Business
In todayās fast-paced business landscape, the Manufacturing Resource Planning (MRP) system stands as a cornerstone for organizations striving to optimize their manufacturing processes. MRP systems orchestrate a symphony of interconnected components ā from inventory management to production scheduling. Their significance is not merely about managing resources but about enhancing operational efficiency and ensuring responsiveness to market demands. The importance of MRP systems can be boiled down to a few specific elements that are critical for businesses aiming to maintain a competitive edge.
Enhanced Decision-Making: One of the primary advantages of implementing an MRP system is its ability to facilitate better decision-making. By aggregating data from various sources, these systems provide a clearer picture of inventory levels, production capacity, and customer demand. Decision-makers can therefore develop informed strategies that align production plans with market realities.
Improved Customer Satisfaction: An underrated aspect of MRP systems is their role in boosting customer satisfaction. With enhanced forecasting abilities, businesses ensure that they can meet customer demand without delay. When companies effectively manage their resources, it leads to quicker response times and a consistent supply of products. In industries where time is of the essence, this attribute can define the difference between meeting or missing a sales target.
"An MRP system is not just a tool; itās a crucial ally in the quest for operational excellence."
Cost Effectiveness: Another compelling reason for the implementation of MRP systems is cost effectiveness. Through precise inventory management, companies can minimize excess stock, thereby reducing carrying costs. Furthermore, MRP systems streamline production processes, leading to lower operational costs and improved profit margins. Companies see a positive return on investment by eliminating inefficiencies in resource allocation.
Flexibility to Adapt: In an era where change is the only constant, MRP systems offer organizations the flexibility required to adapt to fluctuations in supply chain dynamics. Whether it is supplier disruptions or unexpected increases in demand, the agility afforded by these systems allows businesses to respond proactively rather than reactively, maintaining productivity in turbulent times.
Integration and Future-Readiness: As businesses increasingly move towards integrating different technological solutions, MRP systems provide a robust framework for such endeavors. With the rise of IoT and smart manufacturing technologies, organizations can harness data analytics and emerging technologies to enhance MRP processes further. This integration not only prepares businesses for the future but also solidifies their operational backbone.
Summary of Key Insights
- Decision-Making Efficiency: MRP systems aggregate data for insightful decision-making.
- Customer Satisfaction Improvement: Accurate forecasting leads to meeting customer needs promptly.
- Cost Reduction: Effective inventory management lowers operational costs.
- Adaptability: MRP systems offer flexibility amidst changing market dynamics.
- Integration: Modern MRP systems prepare businesses for future technological advancements.