Unveiling the Depths of Six Sigma: A Compendium for Business Professionals
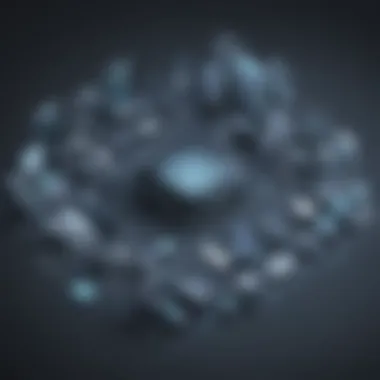
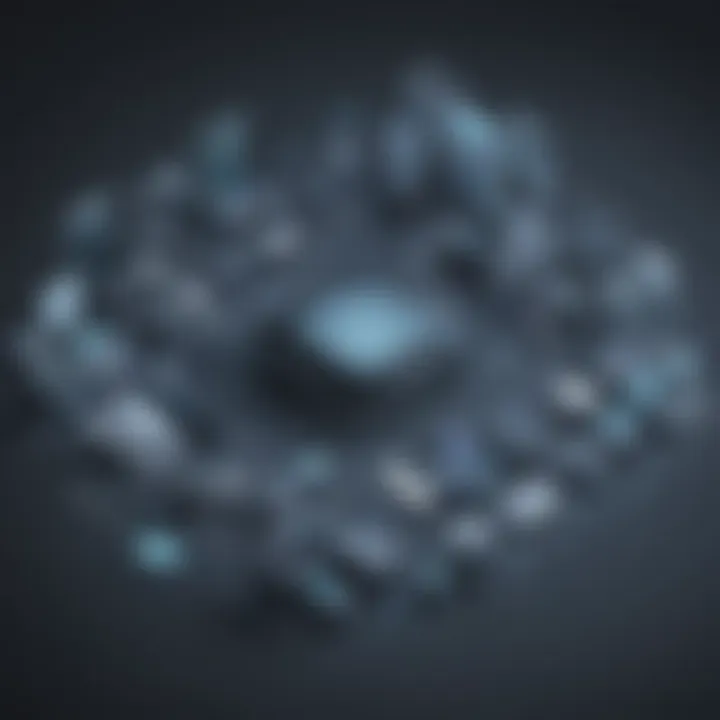
Technological Research Overview
Six Sigma, a highly data-driven methodology, is poised to revolutionize how businesses approach process improvement. By focusing on reducing defects and variations, Six Sigma aims to enhance operational efficiency and quality.
Data Analytics in Business
In the context of Six Sigma, data analytics plays a pivotal role in driving informed decision-making processes. Businesses leverage data analytics to identify trends, patterns, and areas for improvement. By utilizing tools such as statistical analysis and trend modeling, organizations can make data-driven decisions to streamline operations and enhance overall performance. Real-world case studies further highlight the tangible benefits of integrating data analytics into business processes.
Cybersecurity Insights
Within the realm of Six Sigma implementation, cybersecurity holds significant importance in safeguarding sensitive business information and maintaining operational continuity. Analyzing the evolving threat landscape is crucial for implementing robust cybersecurity measures. Best practices in cybersecurity encompass preventive measures, incident response protocols, and ongoing risk assessments. Additionally, adhering to regulatory compliance standards ensures that organizations comply with data protection regulations and mitigate potential security risks.
Artificial Intelligence Applications
The integration of Artificial Intelligence (AI) into Six Sigma methodologies presents opportunities for automation and predictive analytics. AI algorithms drive enhanced decision-making processes and facilitate the identification of potential process improvements. However, ethical considerations surrounding AI deployment, such as data privacy and algorithm bias, warrant careful attention to ensure responsible and transparent use of AI technologies.
Industry-Specific Research
In various industries, including finance, healthcare, and retail, Six Sigma applications are tailored to address sector-specific challenges and opportunities. Technological advancements in the finance sector involve leveraging data analytics and AI to optimize financial processes and minimize risks. In healthcare, technological advancements enhance patient care delivery, streamline administrative processes, and improve healthcare outcomes. Retail industry solutions focus on enhancing customer experience through data-driven insights and personalized service offerings.
Introduction to Six Sigma
Six Sigma is a fundamental methodology that serves as the core of process improvement in various industries. In this comprehensive guide, we explore the significance of the Introduction to Six Sigma, shedding light on its critical components and potential impact on businesses. This section delves into the definition of Six Sigma, tracing its roots to Motorola's pioneering efforts. We will also scrutinize the key historical milestones that have shaped Six Sigma into what it is today.
Definition of Six Sigma
Understanding the Core Philosophy
The essence of Six Sigma lies in its relentless pursuit of perfection through minimizing process defects and variations. This philosophy emphasizes precision and data-driven decision-making, aiming to enhance organizational efficiency and quality significantly. By adhering to the core principles of Six Sigma, companies can refine their processes and deliver exceptional results consistently.
Importance of Statistical Methods
Statistical methods are the backbone of Six Sigma, enabling businesses to analyze data accurately and make informed decisions. By leveraging statistical tools and techniques, organizations can pinpoint areas for improvement, identify root causes of problems, and drive meaningful change. The systematic application of statistical methods ensures that process enhancements are not based on gut feelings but on concrete data-driven insights.
Focus on Customer Requirements
Central to Six Sigma is its unwavering focus on meeting customer expectations and demands. By aligning process improvements with customer needs, organizations can ensure satisfaction and loyalty. Understanding customer requirements allows companies to tailor their operations effectively, resulting in enhanced product and service quality.
History of Six Sigma
Origins at Motorola
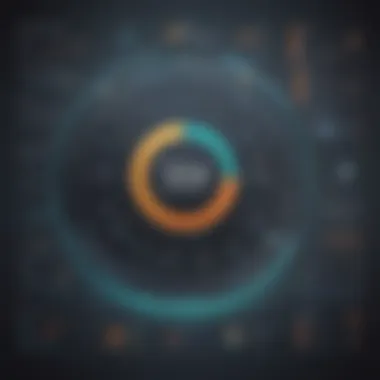
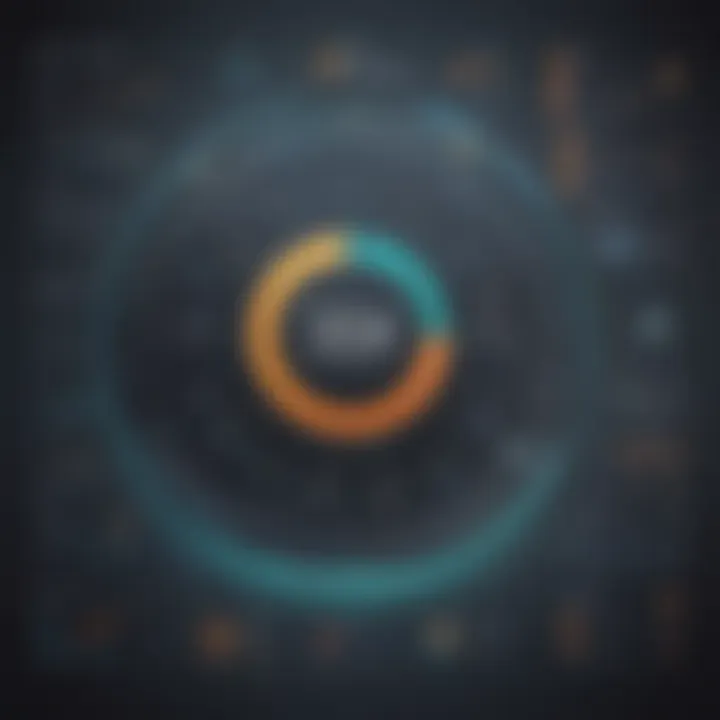
The origins of Six Sigma can be traced back to Motorola, where the methodology first took root in the 1980s. Initially conceived as a quality management approach, Six Sigma gained prominence for its ability to drive operational excellence and customer satisfaction. The success achieved by Motorola paved the way for widespread adoption of Six Sigma principles across industries.
Evolution and Adoption by Organizations
Over the years, Six Sigma has evolved from a manufacturing-centric process to a comprehensive business strategy embraced by organizations worldwide. Companies have recognized the value of Six Sigma in enhancing productivity, reducing costs, and fostering a culture of continuous improvement. The widespread adoption of Six Sigma underscores its adaptability and effectiveness across diverse sectors.
Impact on Quality Management
Six Sigma has had a transformative impact on quality management practices, revolutionizing how businesses approach quality control. By prioritizing defect reduction and process optimization, organizations can deliver superior products and services that meet and exceed customer expectations. The integration of Six Sigma principles in quality management has set new benchmarks for excellence.
Key Concepts in Six Sigma
DMAIC Methodology
At the core of Six Sigma lies the DMAIC methodology, a structured approach for process improvement. DMAIC, which stands for Define, Measure, Analyze, Improve, and Control, provides a roadmap for addressing operational challenges and driving sustainable results. By following the DMAIC framework, organizations can systematically enhance their processes and achieve continuous performance improvement.
Roles of Green Belts and Black Belts
In the realm of Six Sigma, Green Belts and Black Belts play crucial roles in leading process improvement initiatives. Green Belts are team members responsible for executing Six Sigma projects, while Black Belts take on more strategic roles, overseeing project portfolios and driving organizational change. By leveraging the expertise of Green Belts and Black Belts, companies can successfully implement Six Sigma methodologies and achieve business objectives.
Measurement of Defects and Sigma Levels
Measuring defects and sigma levels is essential to monitoring process performance and quality standards. The sigma level indicates the capability of a process to meet customer requirements, with higher sigma levels corresponding to lower defect rates. By accurately measuring defects and sigma levels, organizations can assess their operational efficiency and identify areas for improvement.
Benefits of Implementing Six Sigma
Understanding the importance of implementing Six Sigma is crucial in this comprehensive guide on the methodology. Six Sigma aims to enhance business processes by minimizing defects and variabilities. By implementing Six Sigma, organizations can achieve significant improvements in quality and efficiency. The benefits are substantial, encompassing various elements that can revolutionize operational effectiveness and customer satisfaction.
Improvement in Quality and Efficiency
Reduction in defects and errors
Exploring the reduction in defects and errors within the Six Sigma framework is pivotal to achieving operational excellence. By minimizing defects and errors, organizations can enhance product quality and customer satisfaction. This aspect of Six Sigma focuses on identifying root causes of errors and implementing data-driven solutions. Embracing a culture of continuous improvement through defect reduction is a cornerstone of Six Sigma methodologies, leading to heightened operational efficiency.
Streamlining of processes
Efficient processes are at the core of successful business operations. Streamlining processes within the Six Sigma methodology involves optimizing workflows to eliminate unnecessary steps and enhance productivity. By streamlining processes, organizations can improve overall efficiency, reduce waste, and expedite time-to-market for products and services.
Enhanced customer satisfaction
Customer satisfaction is a fundamental pillar of business success. Through the implementation of Six Sigma, organizations can proactively address customer needs and preferences, leading to enhanced satisfaction levels. By focusing on delivering defect-free products and services, businesses can build trust with customers and foster long-term relationships, ultimately driving growth and profitability.
Financial Impact

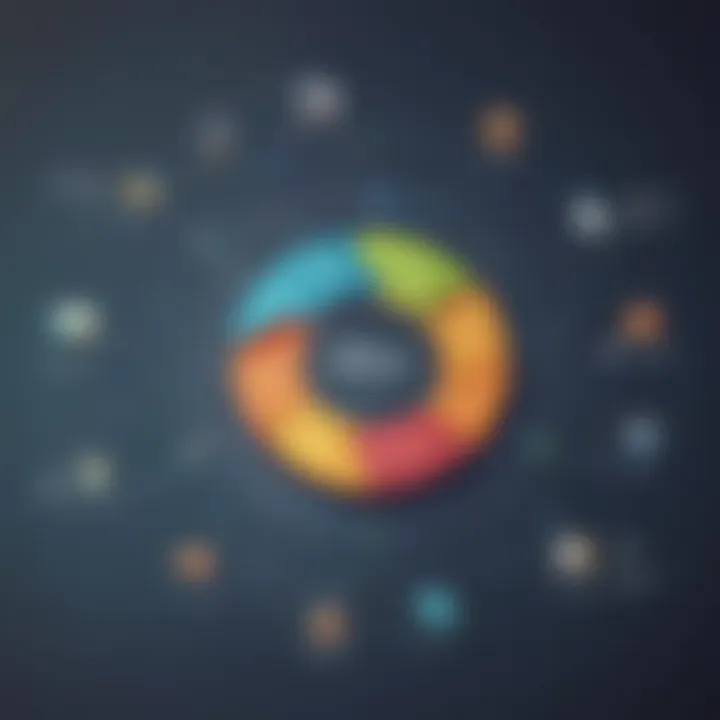
Cost savings and increased revenue
Cost savings and revenue growth are key outcomes of implementing Six Sigma methodologies. By reducing defects and streamlining processes, organizations can decrease operational costs and improve bottom-line profitability. The rigorous analysis of data and performance metrics enables businesses to identify cost-saving opportunities and capitalize on revenue-generating activities.
ROI analysis and performance metrics
Return on Investment (ROI) analysis is essential for evaluating the financial impact of Six Sigma initiatives. By measuring performance metrics and analyzing ROI, organizations can assess the effectiveness of their quality improvement efforts. This data-driven approach ensures that resources are allocated efficiently and strategic decisions are based on quantifiable results.
Risk mitigation
Risk mitigation is a critical component of Six Sigma implementation, as it helps organizations identify and proactively address potential threats to quality and efficiency. By systematically managing risks and uncertainties, businesses can safeguard their operations and reputations. Through the integration of risk mitigation strategies, organizations can minimize disruptions and optimize business performance.
Cultural Transformation
Promoting a data-driven mindset
Promoting a data-driven mindset is essential for fostering a culture of continuous improvement within an organization. By emphasizing the importance of data-driven decision-making, businesses can enhance transparency, accountability, and collaboration. A data-driven culture empowers employees to make informed choices and drive positive changes, ultimately contributing to organizational success.
Fostering continuous improvement
Continuous improvement lies at the heart of Six Sigma methodologies. By fostering a mindset of continuous improvement, organizations can adapt to changing market dynamics and customer demands. Continuous improvement initiatives encourage employees to innovate, experiment, and iterate, leading to enhanced operational efficiency and sustained business growth.
Empowering employees
Empowering employees is key to creating a culture of ownership, accountability, and innovation. Six Sigma implementation involves providing training, support, and opportunities for professional development to enable employees to contribute meaningfully to quality improvement efforts. Empowered employees are more engaged, motivated, and dedicated to driving organizational success through their knowledge and skills.
Implementing Six Sigma in Organizations
Six Sigma deployment within organizations holds paramount significance for driving operational excellence and quality enhancements. This pivotal section of the article delves into the intricate processes and strategies involved in integrating Six Sigma principles within the organizational framework, emphasizing the meticulous attention required for seamless implementation.
Leadership and Management Support
Top-down Commitment
Top-down commitment is a fundamental pillar in the successful execution of Six Sigma methodologies within organizations. This approach necessitates unwavering endorsement and active participation from top-level management to instill a culture of quality and process improvement throughout the organization. The distinctive characteristic of top-down commitment lies in its ability to set the tone for organizational priorities and allocate resources effectively, showcasing its indispensability in driving impactful change. While its advantages include clear communication of objectives and quicker decision-making processes, potential disadvantages may arise from the risk of disconnect between leadership vision and frontline operations, underscoring the need for robust communication channels and cross-functional collaboration.
Allocation of Resources
Efficient allocation of resources is a cornerstone of implementing Six Sigma practices within organizations, ensuring that adequate personnel, finances, and tools are dedicated to process improvement initiatives. The key characteristic of resource allocation lies in its ability to maximize the utilization of available assets, optimizing the effectiveness of Six Sigma projects and fostering continuous improvement. This strategic approach is popular for its role in enhancing operational efficiency and achieving measurable results, aligning resources with strategic objectives to drive tangible outcomes. However, challenges may emerge from resource constraints or misalignment with organizational goals, necessitating adaptive resource management strategies to mitigate risks and enhance project success rates.
Training and Skill Development
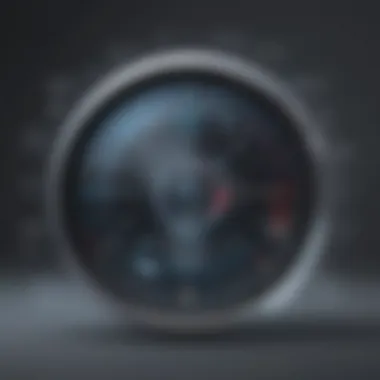
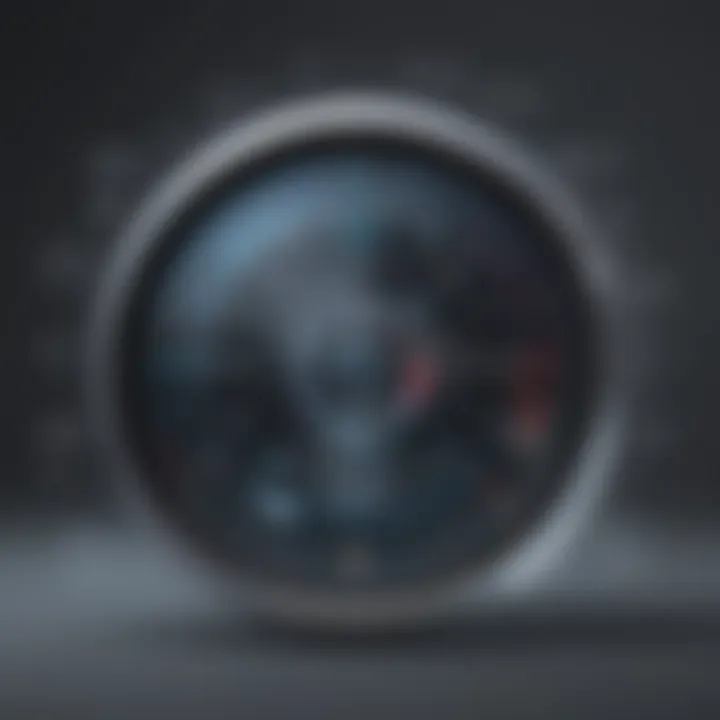
Comprehensive training and skill development programs form the bedrock of ensuring organizational readiness for Six Sigma implementation, equipping employees with the necessary competencies to drive quality improvements and uphold process excellence. The key characteristic of training and skill development lies in its capacity to enhance employee capabilities, empower problem-solving skills, and cultivate a culture of continuous learning within the workforce. This approach is beneficial for nurturing a talent pipeline of Six Sigma practitioners and champions, fostering knowledge-sharing networks, and sustaining long-term success. Nevertheless, challenges may arise from resistance to change, inadequate training infrastructure, or skill gaps, necessitating tailored development pathways and holistic training frameworks to address evolving business needs and bridge knowledge disparities.
Challenges and Pitfalls in Six Sigma Implementation
Implementing Six Sigma in organizations comes with its set of challenges and pitfalls that need careful consideration. Understanding these challenges is essential for successful implementation and optimization of processes. The ability to identify the issues and proactively address them can lead to better outcomes and sustained results. By navigating through these hurdles effectively, organizations can maximize the benefits of Six Sigma and drive continuous improvement.
Resistance to Change
Cultural Barriers
Cultural barriers pose a significant challenge in the realm of Six Sigma implementation. These barriers can manifest in various forms, hindering the smooth transition to a data-driven and process-oriented culture. Resistance to change rooted in organizational traditions, beliefs, and practices can impede the adoption of new methodologies. Overcoming these cultural barriers requires a strategic approach that involves cultural sensitivity, effective communication, and alignment of Six Sigma principles with existing cultural norms. By addressing these barriers head-on, organizations can create a conducive environment for change and maximize the impact of Six Sigma initiatives.
Lack of Buy-in from Stakeholders
The lack of buy-in from stakeholders can derail Six Sigma initiatives and impede progress towards achieving process excellence. Stakeholder engagement and alignment are crucial for the successful implementation of Six Sigma methodologies. Without the support and commitment of key stakeholders, projects may face resistance, skepticism, or lack of resources. Building consensus and garnering support from stakeholders require effective communication, advocacy for the benefits of Six Sigma, and clear articulation of the value proposition. By actively involving stakeholders in the process and addressing their concerns, organizations can foster a shared vision and drive success in Six Sigma implementation.
Over-reliance on Methodologies
While methodologies are the backbone of Six Sigma, an over-reliance on them can lead to rigidity and lack of adaptability. Organizations may fall into the trap of following methodologies blindly without considering unique challenges or evolving needs. This tunnel vision can limit creativity, innovation, and problem-solving capabilities, undermining the core principles of Six Sigma. Balancing methodological rigor with flexibility is essential for sustainable success in Six Sigma. By encouraging a culture of continuous improvement and agility, organizations can leverage methodologies effectively while embracing dynamic business environments.
Overemphasis on Metrics
Loss of Focus on Qualitative Aspects
An overemphasis on metrics can sometimes overshadow the qualitative aspects of organizational performance. While metrics provide quantitative insights and performance indicators, they may not capture the full spectrum of qualitative factors that impact decision-making and strategic direction. Neglecting qualitative aspects such as customer experience, employee engagement, and organizational culture can lead to blind spots in the improvement process. Integrating qualitative measures alongside quantitative metrics is crucial for a comprehensive understanding of performance and holistic decision-making. By striking a balance between quantitative metrics and qualitative insights, organizations can drive sustainable growth and enhance overall quality.
Misinterpretation of Data
Misinterpreting data is a common pitfall in Six Sigma implementation that can undermine the integrity of decision-making and process optimization. Data interpretation requires precision, accuracy, and contextual understanding to derive actionable insights. Misreading data points, drawing incorrect conclusions, or misaligning data with project objectives can result in inefficiencies and suboptimal outcomes. Cultivating data literacy, investing in data analysis skills, and promoting data-driven decision-making are essential steps to mitigate the risks of data misinterpretation. By fostering a culture of data accuracy and interpretation, organizations can leverage data effectively to drive informed decisions and propel continuous improvement.
Unintended Consequences
Future Trends and Innovations in Six Sigma
In discussing the future trends and innovations in Six Sigma, it becomes imperative to explore how this methodology is evolving to meet the demands of modern business landscapes. As technology continues to advance at a rapid pace, Six Sigma is adapting to integrate with Industry 4.0, a term encompassing the digital transformation of industries through automation and data exchange. Understanding these advancements is essential for forward-thinking professionals seeking to optimize processes and improve outcomes. By embracing these innovations, businesses can stay ahead of the curve and remain competitive in a rapidly changing world.
Integration with Industry
Application of IoT and AI in quality control
When delving into the application of IoT and AI in quality control within the realm of Six Sigma, it's crucial to acknowledge the significant impact of these technologies. IoT (Internet of Things) and AI (Artificial Intelligence) play a pivotal role in optimizing quality control processes by enabling real-time monitoring, predictive maintenance, and automated decision-making. Their ability to analyze vast amounts of data swiftly and accurately enhances the efficiency and effectiveness of quality control measures. While their implementation requires initial investment and upskilling of workforce, the long-term benefits in terms of improved accuracy, reduced downtime, and enhanced overall quality make them highly favorable for businesses adopting Six Sigma practices.
Predictive analytics for process optimization
Exploring predictive analytics for process optimization in the context of Six Sigma reveals a strategic approach to anticipating and mitigating potential issues before they impact operations. By leveraging advanced data analytics and machine learning algorithms, organizations can forecast trends, identify patterns, and optimize processes for maximum efficiency. The ability to proactively address bottlenecks and streamline workflows through predictive analytics empowers businesses to make informed decisions and achieve continuous improvement. While the complexity of implementation and the need for skilled data analysts pose challenges, the advantages of predictive analytics in enhancing operational performance and driving sustainable results cannot be overlooked.
Automation of data collection
Addressing the automation of data collection within the framework of Six Sigma sheds light on the transformative power of streamlined data gathering processes. Automation reduces human error, accelerates data collection, and enhances data accuracy, thereby facilitating more informed decision-making within organizations. By automating data collection processes, businesses can streamline operations, improve data integrity, and ensure timely access to critical insights for driving strategic initiatives. Though initial setup costs and integration challenges may arise, the long-term benefits of increased productivity, data efficiency, and decision-making precision make automation a vital component of modern Six Sigma practices.