Effective Warehouse Management Strategies in Manufacturing
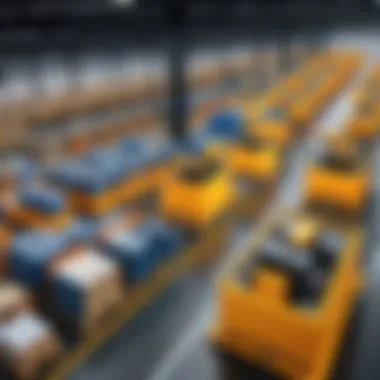
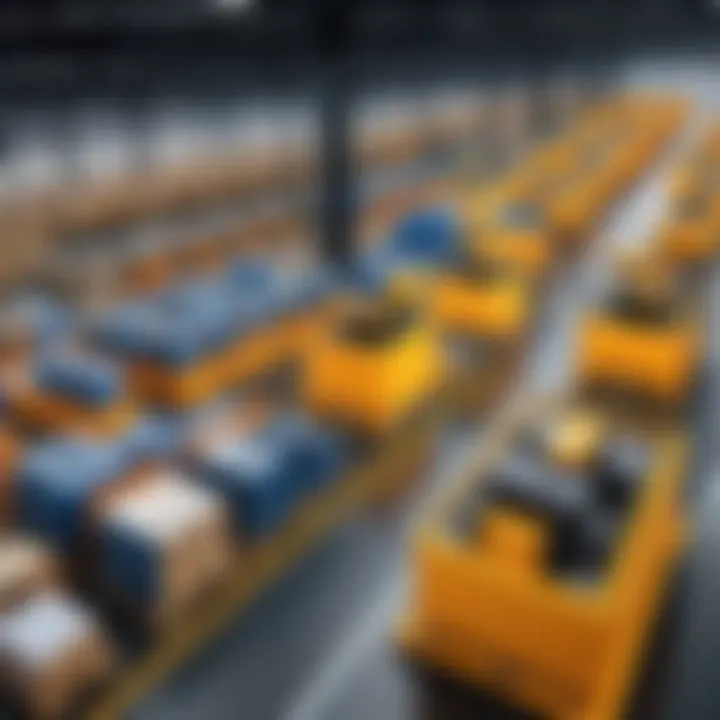
Intro
Warehouse management encompasses the processes and systems that facilitate the efficient handling of goods and materials within a manufacturing environment. It’s not just about storing things; it’s a complex ballet of logistics that directly influences productivity, profitability, and overall business success. In a landscape where margins are thin and competition is intense, understanding the nuances of warehouse management can be the difference between merely surviving and truly thriving.
With the rapid advancement of technology and changing market dynamics, companies are compelled to rethink their warehousing strategies continually. This article aims to explore various facets of warehouse management, highlighting the importance of both traditional methods and cutting-edge innovations. We will delve into specific strategies that enhance operational efficiency and examine the challenges prevalent in the industry, providing actionable insights for manufacturers looking to optimize their warehousing practices.
Technological Research Overview
Recent Technological Innovations
In recent years, technological advancements have transformed warehouse management. The introduction of Automated Guided Vehicles (AGVs) and drones is revolutionizing the way goods are moved within warehouses. These systems can reduce labor costs and minimize the potential for human error, offering manufacturers a significant competitive edge.
Additionally, the implementation of Radio Frequency Identification (RFID) technology enables real-time tracking of inventory, ensuring that businesses maintain precise control over stock levels. At the same time, Warehouse Management Systems (WMS) have evolved, integrating seamlessly with Enterprise Resource Planning (ERP) systems to create a cohesive operational environment.
Impact on Business Operations
The integration of these technologies can be likened to oil in an engine; everything runs more smoothly and efficiently. For example, the use of data analytics within WMS allows companies to forecast demand more accurately, adapt their inventory turns, and ultimately enhance customer satisfaction. Moreover, with the advent of cloud computing, manufacturers can access their warehousing data anytime, anywhere, leading to better decision-making.
"The best warehouse is one where every square inch is utilized effectively and waste is minimized."
Future Technological Trends
As we look forward, the trajectory of technological advancements shows no sign of slowing. A strong trend emerging is the move towards artificial intelligence (AI) integration in warehouse management. From predictive analytics to robotic process automation, AI applications hold the promise of further revolutionizing operations. Supply chain optimization through advanced data modeling will enable manufacturers to enhance agility and responsiveness, essential traits in today’s fast-changing market.
Data Analytics in Business
Importance of Data Analytics
Data analytics is no longer a luxury; it’s a necessity for modern warehouse management. By extracting valuable insights from data, businesses can make informed decisions that lead to enhanced operational efficiency. The old adage, "If you can’t measure it, you can’t manage it," rings particularly true in a warehouse setting, where every movement and transaction can yield data crucial for optimizing performance.
Tools for Data Analysis
Various tools and software solutions are available that can assist in data analysis. Solutions like Salesforce and Tableau provide robust functionalities that allow manufacturers to visualize data trends and patterns, making it easier to spot inefficiencies and implement improvements.
Case Studies on Data-Driven Decisions
Case studies have shown that companies that leverage data analytics can significantly improve inventory turnover and reduce holding costs. For instance, a major manufacturer implemented a data-driven approach, resulting in a 30% decrease in excess inventory within just a year.
Cybersecurity Insights
Threat Landscape Analysis
As warehouses become increasingly digitized, they also become prime targets for cyberattacks. Understanding the threat landscape is essential. Businesses must be aware of vulnerabilities that could expose their logistics and sensitive customer information.
Best Practices for Cybersecurity
Implementing strong cybersecurity measures is crucial. Best practices include regular software updates, employee training on phishing attacks, and utilizing firewalls to protect data. It is always better to be safe than sorry, especially in an age where data breaches can lead to significant financial losses.
Regulatory Compliance in Cybersecurity
Compliance with regulations like the General Data Protection Regulation (GDPR) is vital for companies operating in today's digital arena. Failing to comply not only results in legal penalties but can also severely damage a brand’s reputation.
Artificial Intelligence Applications
AI in Business Automation
AI is shaking up the warehousing landscape. Businesses are increasingly using intelligent algorithms to automate routine tasks, from order processing to inventory management. By reducing human intervention, companies can minimize errors and enhance speed.
AI Algorithms and Applications
AI can process vast datasets and generate insights that would be impractical for humans to analyze. Practical applications range from demand forecasting to route optimization for delivery.
Ethical Considerations in AI
With great power comes great responsibility. The ethical implications of employing AI, particularly regarding employment and data privacy, must not be ignored. Businesses must tread carefully and ensure that AI is implemented in a way that benefits both the organization and its employees.
Industry-Specific Research
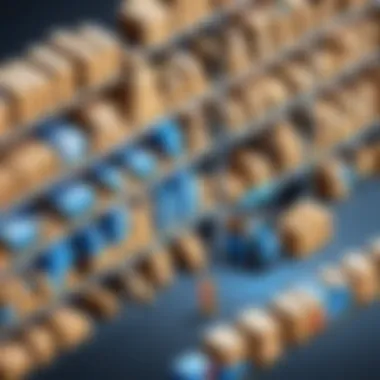
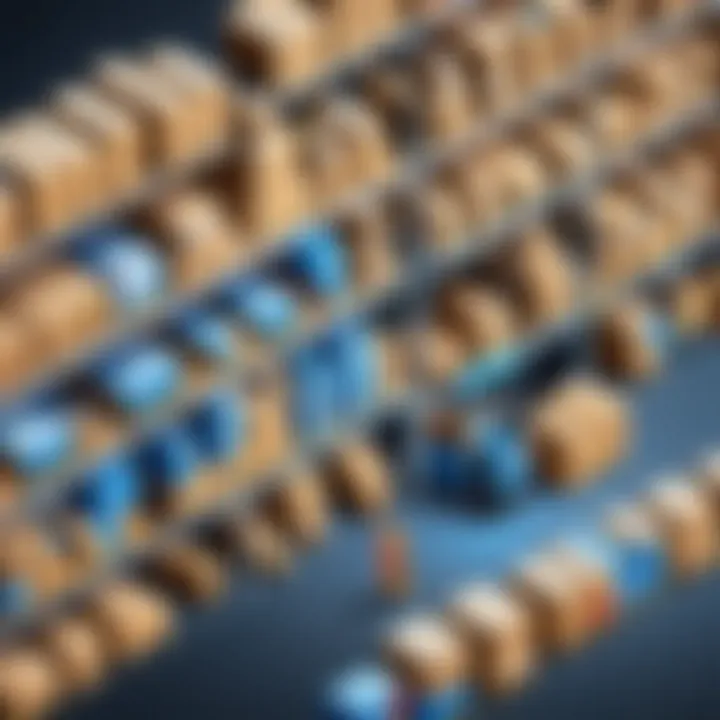
Tech Research in Finance Sector
Innovation does not happen in a vacuum. It’s essential to look at how technological advancements in industries like finance can inform warehouse management practices. For instance, blockchain technology is gaining traction in finance for its ability to enhance transparency and tracking, possibly offering solutions in supply chain transparency.
Healthcare Technological Advancements
Similarly, the healthcare sector has adopted unique warehousing strategies. The push for maintaining compliant and safe inventory, particularly for pharmaceuticals, presents lessons that can be applied across other sectors.
Retail Industry Tech Solutions
Lastly, retail industry leaders are using omnichannel strategies to improve their warehousing methodology. The integration of warehousing and e-commerce fulfillment offers inspiration for manufacturers looking to streamline their processes.
Each aspect explored in this article will build upon the core theme of optimizing warehouse management in manufacturing, presenting an informative guide for decision-makers and professionals in the field.
Prolusion to Warehouse Management
Warehouse management is a vital cog in the large machinery of manufacturing. It encompasses not just the act of storing goods but also the processes involved in receiving, tracking, and distributing inventory efficiently. Trade-offs and decision-making involved in warehouse management can heavily influence a firm's bottom line, which makes understanding this domain all the more essential.
Definition and Scope
Warehouse Management refers to the systematic control of the warehouse operations like storage, inventory management, and order fulfillment. It is not just about the physical space but also involves strategic planning related to where to store products and how to optimize the flow of materials in and out of the facility. Factors such as layout design, inventory levels, and product accessibility come under this umbrella, each integrating to form a robust management system.
The scope of warehouse management extends to include the entire spectrum of operations, from employing warehouse management systems (WMS) to workforce optimization and layout redesign. It recognizes that even the smallest hiccup—like a misplaced pallet—can ripple through the supply chain, impacting production schedules and customer satisfaction. It’s a balancing act where clear visibility and accurate data enable better decision-making at any given moment.
Importance in Manufacturing
Moreover, it helps manufacturers respond more swiftly to market demands. In today’s fast-paced environment, consumers expect quick turnaround times and on-demand delivery. Any dysfunction in warehousing can lead to delays that ripple through the entire supply chain.
An effective warehouse management strategy is no longer just an option; it's a necessity for manufacturing firms to maintain their competitive edge in a scenario that demands agility and precision.
In summary, warehouse management serves as the backbone that supports operational efficiency, customer satisfaction, and sustainability in the manufacturing business. It enables organizations to be proactive rather than reactive, setting the stage for success in a landscape that is perpetually evolving.
Fundamental Principles of Warehouse Management
Warehouse management is an area that needs to be done right to keep everything in the manufacturing game on point. Having a solid foundation in the fundamental principles of warehouse management facilitates smoother operations, prevents costly mistakes, and ensures that all parts are moving in sync. Understanding these core elements provides a roadmap to achieving efficiency and effectiveness in warehousing, leading to overall operational success.
Inventory Control
When we say inventory control, we mean tracking products from the moment they hit the warehouse to when they leave for the customer. This is crucial because, without a handle on what you have, what you're losing, or what you need to order, chaos rules. Good inventory control prevents overstock, which ties up cash unnecessarily, as well as stockouts that can put a snarl in customer satisfaction.
A popular method for managing inventory is the First-In, First-Out (FIFO) approach, ensuring older stock is used before newer stock. This is especially important for perishable items. Not to mention, technology now enables automated tracking and alerts for stock levels, which has made life much easier. Anyone can tell you manual counts are a hassle, and they often lead to errors.
"Effective inventory control is like a well-oiled machine; you may not see it working, but when it breaks, everyone notices."
Process Optimization
Process optimization takes a close look at all the steps involved in warehousing operations, aiming to trim the fat and streamline workflows. This means analyzing every nook and cranny of current practices to find bottlenecks or redundancies and then eliminating them. When processes are optimized, workers don’t waste time wandering around, and shelf space gets utilized better. The idea is to maintain a constant flow of goods within the warehouse.
Access paths are a key consideration here. If the layout hinders movement, efficiency goes down like a sack of potatoes. Implementing methods like cross-docking can significantly reduce handling time and minimize storage costs. Regular reviews of processes and making adjustments are fundamental practices that can lead to long-term gains in efficiency.
Workforce Management
The human element in warehouse management can’t be overlooked. Workforce management involves ensuring that the right number of people is scheduled at the right time, trained appropriately, and motivated to perform well. A well-managed workforce can impact productivity significantly since ultimately it’s the workers who keep things moving.
Training programs should go beyond the basics. Continuous education about new technologies, equipment, and safety protocols is important. Also, consider using performance metrics to identify who shines and who needs extra help. Bonus: fostering a positive culture in the workspace can lead to better morale, which in turn translates to higher efficiency.
To sum it up, the fundamental principles of warehouse management are all about making sure the processes are smooth and efficient while keeping track of what you have. From controlling your inventory to optimizing those pesky processes and motivating the workforce, getting a grip on these principles can set manufacturing endeavors up for success.
Technological Innovations in Warehouse Management
Technological innovations in warehouse management play a pivotal role in elevating the efficiency and effectiveness of operations within the manufacturing industry. By integrating advanced technologies, manufacturing businesses can achieve better inventory accuracy, optimize their logistical processes, and ultimately diminish operational costs. The sustainable growth of this sector hinges more than ever on the exploitation of these technological advancements. In this section, we will explore three key components of technological innovations: Automation and Robotics, Warehouse Management Systems (WMS), and the Role of Artificial Intelligence.
Automation and Robotics
Automation and robotics have ushered in a new era of warehouse management, transforming the way tasks are performed. Whether it's automated guided vehicles (AGVs) transporting goods or robotic arms handling packaging, such technologies drastically reduce human errors and enhance productivity. The implementation of automation facilitates faster order processing—what once took hours can now be accomplished in minutes.
Moreover, automated systems, such as conveyor belts and sorting machines, streamline the movement of materials. As a result, warehouses can benefit from reduced labor costs, as fewer workers are needed for repetitive tasks, allowing personnel to focus on more strategic initiatives. However, it’s important to carefully assess the cost of implementation versus the expected ROI to avoid unnecessary expenditures.
"Investing in automation is not just about technology—it's about re-evaluating operational strategies to unlock true efficiency."
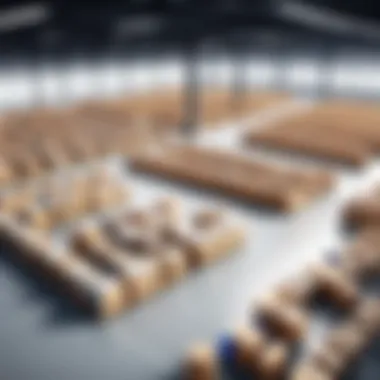
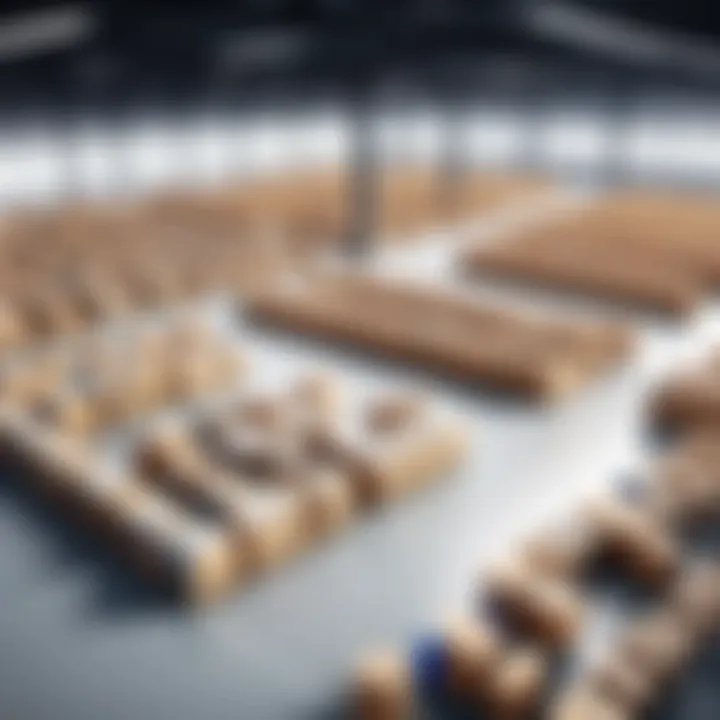
Warehouse Management Systems (WMS)
Warehouse Management Systems (WMS) are the backbone of modern warehouse operations. These complex software solutions allow businesses to manage inventory levels, order fulfillment, and warehouse organization with precision. A well-implemented WMS can provide real-time visibility into stock levels and order statuses, allowing teams to make informed decisions based on data analytics—leading to a more agile response to market demands.
Additionally, a WMS can integrate with other systems across the supply chain, further enhancing coordination between manufacturers, suppliers, and retailers. This interconnectedness not only improves communication but also contributes to better forecasting and inventory planning, ultimately reducing excess stock and minimizing waste.
The Role of Artificial Intelligence
Artificial Intelligence (AI) has started to carve its niche in warehouse management, ushering in innovative solutions for inventory management and operational decision-making. AI algorithms can analyze vast amounts of data to predict trends, foresee inventory needs, and even identify patterns of demand that managers might overlook.
With AI, it’s possible to automate routine operational processes, such as reordering supplies or scheduling maintenance for equipment. As such predictive analyses become more robust, businesses can proactively address challenges before they escalate into more significant problems. However, the successful implementation of AI requires a cultural shift within organizations, ensuring that staff are ready to embrace technology rather than resist it.
Best Practices in Warehouse Management
Layout Design
A well-thought-out warehouse layout is crucial. It’s not just about cramming as much product into a space as possible; it’s about maximizing flow.
A carefully planned layout helps reduce time spent in storage and retrieval. For instance, ABC classification of items can make a difference: high-demand products are stored closer to the shipping area, while slower-moving items are further away. This principle is often referred to as the "the 80/20 rule"; 80% of sales usually come from 20% of your stock. Thus, positioning those high-turnover items conveniently can result in notable time savings.
Furthermore, incorporating wide enough aisles for equipment can lead to smoother operations, especially when using forklifts or automated guided vehicles (AGVs).
"The layout you choose today can dictate the progress you make tomorrow."
Inventory Tracking Techniques
Effective inventory tracking techniques ensure that stock levels remain accurate and accessible. These techniques not only help stave off stockouts, which can be detrimental to operations, but also guard against overstocking, which ties up capital unnecessarily.
Modern methodologies such as Just-In-Time (JIT) inventory can help. This system allows you to maintain minimal stock, thereby reducing carrying costs. The First-In, First-Out (FIFO) approach is another technique that can streamline your operations by ensuring that older inventory is used or sold first, mitigating the risks of obsolescence.
Utilizing barcode systems or Radio-Frequency Identification (RFID) can further strengthen your inventory tracking. These technologies allow real-time data capture, meaning you can quickly assess stock levels, receive alerts for reordering, and minimize human errors. Regular audits—both random and scheduled—can also validate the accuracy of inventory records.
Safety and Compliance Measures
When it comes to warehouse management, safety isn't just a box to tick off; it's paramount. There exists a natural correlation between safety and productivity. A safe environment keeps accidents at bay and minimizes downtime.
Companies should ensure that every employee is trained in safety protocols. Regular safety drills and refreshers can be beneficial. Keeping pathways clear and ensuring proper signage can enhance safety metrics, making the warehouse more navigable. Furthermore, equipment maintenance shouldn't be neglected; scheduled maintenance is vital to avoid breakdowns that could cause injuries or accidents.
Compliance with safety regulations can be daunting, but it’s crucial. Neglecting safety standards can lead to hefty fines and damage to reputation. Thus, implementing your safety measures and documenting adherence to regulations ensures that you not only comply but thrive. In light of this, safety isn't an afterthought but categorically a component of operational excellence.
Challenges Faced in Warehouse Management
Supply Chain Disruptions
A major challenge that warehouses face is the unpredictable nature of supply chain disruptions. These can result from various factors including natural disasters, geopolitical tensions, or even supplier bankruptcies. An event in one corner of the world can ripple through the supply chain, leading to delays, increased costs, and, ultimately, customer dissatisfaction.
To mitigate such disruptions, companies can develop contingency plans that outline clear steps to take when issues arise. These might include:
- Diversifying suppliers to minimize risk.
- Implementing visibility tools to track shipments in real-time.
- Maintaining buffer stock to cushion against unexpected shortages.
"Supply chain resilience is increasingly becoming a buzzword, but it's vital for survival."
Inventory Shrinkage
Inventory shrinkage is another significant hurdle. This phenomenon refers to the loss of inventory that can occur due to theft, damage, or errors during handling and storage. It not only affects the bottom line but also complicates inventory management processes. To combat shrinkage, manufacturers can employ several strategies:
- Regular audits to keep track of stock.
- Enhanced security measures, such as surveillance systems.
- Employee training on proper inventory handling.
These steps not only help to keep inventories accurate but also instill a culture of accountability within the workplace.
Technological Adaptation
The fast-paced evolution of technology presents a double-edged sword for warehouses. While innovations such as automated sorting and data analytics offer the potential for improved efficiency and accuracy, the cost and time required for technological adaptation can be daunting. Embracing new tools demands not only investment but also a commitment to training staff and modifying existing workflows.
Organizations can ease this transition by:
- Conducting thorough research to choose the right technologies.
- Implementing them gradually to allow time for adjustment.
- Providing ongoing training to ensure competency among staff.
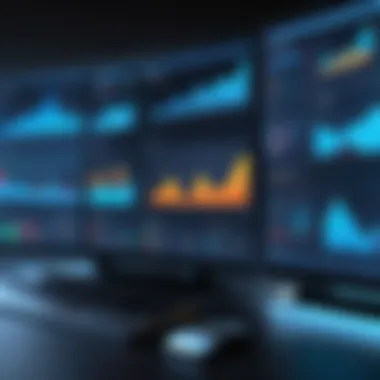

As a result, the focus shifts from merely adapting to change to strategically leveraging new technologies, thereby facilitating growth and sustained operational effectiveness.
Case Studies of Successful Warehouse Management
In the realm of warehouse management, case studies serve as a compass that guides businesses through the various challenges and opportunities within the manufacturing industry. They illustrate not just what works well but also reveal the methodologies, innovations, and practices that lead to real-world improvements. Successful case studies provide tangible evidence of how efficient warehouse management can elevate operational performance, cut costs, and enhance customer satisfaction.
When reviewing these case studies, it’s important for practitioners to glean insights from various contexts. Learning from the successes and setbacks of others helps in crafting a unique strategy that aligns with specific business goals. This understanding can ensure that warehouse managers dodge common pitfalls and adopt tried-and-tested solutions tailored for their circumstances.
Large Scale Manufacturing
Large-scale manufacturing businesses often face complexities due to their size, volume of inventory, and the multitude of operations taking place simultaneously within their warehouses. One notable example includes Tesla, whose Gigafactory operates on a grand scale. Their approach to warehouse management involves a combination of advanced automation tools and sophisticated warehouse management systems (WMS).
Key Elements Considered:
- Automation and Robotics: Tesla employs a suite of automated vehicles and robots to transport goods within the warehouse. This not only speeds up the process but also reduces human error and labor costs while keeping employees safer.
- Real-Time Inventory Management: Their system uses predictive analytics for inventory forecasting, allowing them to proactively address stock outages that could impact production.
- Lean Inventory Practices: This method minimizes waste and maximizes efficiency, ensuring that resources are allocated where they're most needed without unnecessary surplus.
The benefits for large-scale operations are significant; not only do they see improved workflow and processing speeds, but they also enjoy heightened adaptability to market changes, which is crucial in today's fast-paced environment.
Small and Medium Enterprises
Small and medium-sized enterprises often operate with different constraints compared to larger manufacturers. However, case studies from these entities reveal a rich ground for creativity and innovation. For instance, a local craft brewery in the United States implemented a customized WMS tailored to their unique storage needs for various beer ingredients and finished products.
Considerations for Success:
- Cost-Effective Solutions: Rather than investing heavily in high-end technology, this brewery focused on affordable, scalable software that could grow with their business to help monitor stock levels, deliveries, and shipments.
- Employee Training: Understanding that their workforce was crucial to the success of the implementation, the brewery invested time in training employees to use the technology effectively, thereby increasing morale and productivity.
- Community Engagement: This company leverages community feedback to tweak their inventory based on local preferences, ensuring that they never run out of popular brews, improving customer satisfaction.
Future Trends in Warehouse Management
As the manufacturing industry surges ahead, it's crucial to keep an eye on the horizon where warehouse management is concerned. The landscape is shifting under the influence of technology and external pressures, making it vital for professionals to grasp these future trends. The drive for efficiency and adaptability will shape warehouses into smarter, more proactive environments. Embracing these trends and understanding their implications can significantly elevate operational effectiveness and competitive edge.
Integration of IoT
The Internet of Things (IoT) is changing the game in warehouse management. This technology involves connecting various devices through the internet, enabling effortless communication and data sharing. Imagine sensors that can track inventory in real time; this is no longer just a pipe dream but a growing reality.
The benefits of IoT in warehouse settings are manifold:
- Real-time inventory visibility: Through smart sensors and RFID tags, businesses can obtain precise data about stock levels and location.
- Enhanced operational efficiency: Automated tracking cuts down on manual labor, reducing the chances of human error.
- Predictive analytics: With IoT, data generated can be analyzed to predict trends, improving decision-making for reordering stock.
Consider a large manufacturing firm that implemented IoT solutions and witnessed a dramatic reduction in inventory discrepancies. The results not only streamlined operations but also bolstered customer satisfaction with timely order fulfillment. Integration of IoT, however, does come with its share of considerations, such as data security risks and the need for robust infrastructure.
Sustainability Practices
In today's world, sustainability is not just a buzzword; it's a necessity. As industries grapple with climate change and the need to reduce carbon footprints, warehouse management is no exception. Implementing sustainable practices in warehouse operations holds numerous benefits.
- Energy efficiency: Utilizing renewable energy sources—like solar panels on warehouse roofs—can significantly lower operational costs and impact.
- Waste reduction: Adopting recycling measures and choosing sustainable packaging options helps minimize waste.
- Eco-friendly transportation: Partnering with logistics providers who prioritize green practices can enhance overall sustainability efforts.
It's worth noting that sustainability often aligns with cost-saving initiatives. A study from a major consulting firm indicated that companies investing in green technologies experienced up to a 30% decrease in operational costs over time. Thus, integrating these practices not only meets regulatory demands but also fosters a positive brand image among consumers.
"The future is not something we enter. The future is something we create."
Both IoT integration and sustainability practices are set to transform warehouse management. By understanding and adapting to these trends, organizations not only future-proof their operations but also reinforce their position in a rapidly evolving market.
The End
The conclusion of this article wraps up the myriad of discussions centered around warehouse management within the manufacturing sector. After delving into principles, challenges, and innovative strategies, it’s clear that efficient warehouse management is a linchpin in operational success. It’s not merely about moving goods in and out; it’s about orchestrating a symphony of logistical elements that contribute to overall productivity.
Summary of Key Points
Throughout this article, several crucial points emerged:
- Definition and Importance: Warehouse management is a systematic approach to handling various tasks related to warehousing, proving essential for manufacturing efficiency.
- Fundamental Principles include effective inventory control, process optimization, and proper workforce management. These aspects significantly impact how smoothly operations run.
- Technological Innovations like automation, advanced Warehouse Management Systems (WMS), and artificial intelligence greatly enhance the capability to manage warehouses effectively.
- Best Practices offer insights into how layout design, inventory tracking, and safety measures play a vital role in improving warehouse performance.
- Challenges range from supply chain disruptions and inventory shrinkage to the need for tech adaptation, all of which require strategic planning and proactive responses.
- Future Trends, such as IoT integration and sustainability practices, are shaping the next steps for warehouses, emphasizing the necessity of staying ahead of the curve.
Strategic Recommendations
To improve warehouse management in manufacturing, consider the following recommendations:
- Embrace Technology:
- Enhance Training Programs:
- Refine Layouts:
- Implement Robust Safety Protocols:
- Focus on Sustainability:
- Invest in scalable Warehouse Management Systems that allow for flexibility and adaptability to changing business needs.
- Leverage data analytics to gain insights into inventory levels and demand forecasting, enabling proactive decision making.
- Develop ongoing training for staff to keep them informed on best practices and new technologies.
- Foster an environment that encourages continuous learning and adaptability among the workforce.
- Regularly assess and optimize warehouse layouts to improve efficiency in logistics and reduce operational bottlenecks.
- Implement a logical zoning system for different categories of inventory to streamline picking and packing processes.
- Ensure that safety measures are not just in place but consistently reviewed and enhanced. This reduces accidents and keeps morale high.
- Explore sustainable practices such as energy-efficient lighting and recycling programs within warehouses.
- Consider partnerships with suppliers who adhere to eco-friendly practices.