Enhancing Warehouse Operations with WMS Experience
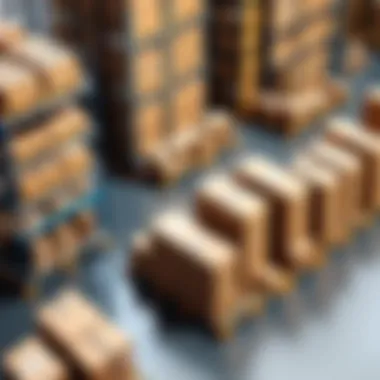
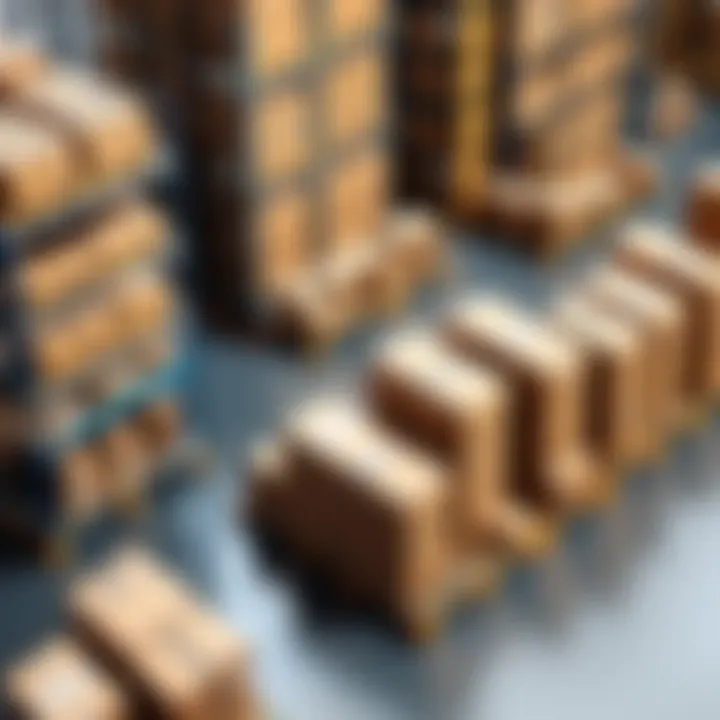
Intro
The landscape of modern warehousing is changing faster than a freight train on a downhill slope. With the advent of technology, businesses are discovering new ways to streamline their operations and boost their efficiency. Warehouse Management Systems (WMS) have become pivotal tools in this realm, transforming how goods are tracked, stored, and delivered. As companies strive for operational excellence, understanding the WMS experience can mean the difference between simply surviving and thriving in a competitive market.
In this article, we'll unfold the various layers of WMS and its impact on warehouse operations. Through a blend of technological insights, user experiences, and future opportunities, we aim to provide a solid foundation for decision-makers seeking to optimize their WMS implementations. Each section will guide you deeper into the nuances of WMS, revealing how technology and innovation fuse to craft a vastly improved business model.
"A successful WMS experience is not just about implementing technology; it's about evolving business practices to embrace it fully."
Let's embark on this exploration with a closer look at the Technological Research Overview, highlighting the pivotal innovations that are reshaping warehouse management today.
Understanding Warehouse Management Systems
Warehouse Management Systems, or simply WMS, serve as the backbone for modern warehousing and distribution centers. They are not just software; they encapsulate a crucial aspect of logistics and supply chain management that directly affects business efficiency. In this overview, we will delve into the essence of WMS and its significant components, laying a solid foundation for understanding its intricate relationship with supply chains.
Definition and Purpose
At its core, a Warehouse Management System is designed to support and optimize warehouse functionality and distribution center management. It enhances inventory visibility and ensures accurate order fulfillment while streamlining warehouse operations. WMS helps in tracking inventory levels, orders, deliveries, and shipments, creating a cohesive environment for logistics operations.
The primary purpose of a WMS is to ensure that the right products are stored in the right place and that they are delivered to the right customers at the right time. With so many moving parts in warehousingâdifferent products, fluctuating inventory levels, and the need for real-time dataâWMS serves as a crucial tool for navigating this complexity.
Key Components of WMS
A robust Warehouse Management System has several key components that play integral roles in optimizing warehouse functions. Understanding these components can help organizations appreciate the full scope of what a WMS offers:
- Inventory Management: This enables real-time tracking of stock levels, locations, and conditions, ensuring accuracy in stock maintenance.
- Order Fulfillment: WMS automates order processing, from picking to packing to shipping, drastically reducing the chances of errors.
- Labor Management: This component helps in tracking employee productivity and movements within the warehouse, allowing for better workforce planning.
- Reporting and Analytics: Offers insights into warehouse performance metrics and helps in data-driven decision-making.
- Integration Functionality: Enables WMS to connect with other systems such as ERP (Enterprise Resource Planning) and TMS (Transportation Management Systems), fostering a seamless flow of data across business functions.
This interplay of components adds layers of efficiency, reducing overhead costs and improving customer satisfaction.
Importance in Supply Chain Management
The significance of Warehouse Management Systems cannot be underestimated in the realm of supply chain management. It plays a vital role by:
- Enhancing Inventory Accuracy: Erroneous inventories can derail supply chains. A WMS ensures precise tracking and reduces discrepancies, thus enhancing overall accuracy.
- Increasing Productivity: By automating routine tasks, a WMS frees up employees, allowing them to focus on more complex responsibilities, and thus dramatically improves productivity.
- Facilitating Better Customer Service: Fast, accurate order fulfillment strengthens confidence in the business and boosts customer loyalty. A WMS significantly contributes to achieving these objectives.
- Supporting Scalability: As a business grows, its warehouse needs can change. WMS systems offer scalability that can accommodate this growth without significant additional costs.
"In todayâs competitive market, your warehouse isnât just a storage space; itâs a strategic asset that can make or break your business."
These facets illustrate why a thorough understanding of WMS is indispensable for professionals, entrepreneurs, and decision-makers who aim to enhance operational efficiency in their organizations.
WMS Experience: A User-Centric Perspective
Understanding the Warehouse Management System (WMS) experience from a userâs perspective is not merely an academic concern. It serves as a linchpin in the toolkit of businesses seeking to optimize their warehouse operations. The essence of a user-centric approach in WMS reveals how effectively these systems serve those who interact with them daily â the warehouse operators, managers, and support staff.
Defining the User Experience in WMS
In any operational setting, the user experience plays a pivotal role. For WMS, it goes beyond just functionality. The user experience encapsulates how intuitive and accessible the system is in terms of navigation, operation, and practical engagement. So, what defines the user experience?
- Accessibility: A well-designed WMS interface must be easy to navigate, enabling users to perform tasks swiftly without unnecessary clicks or confusion.
- Training and Onboarding: The effectiveness of training programs is a major contributor. If users feel that they can master new software without a steep learning curve, satisfaction naturally rises.
- Feedback Mechanisms: Systems that incorporate user feedback into updates show a commitment to improving the user experience, thereby enhancing overall satisfaction.
Ultimately, the user experience in WMS must balance efficiency and ease of use, compelling businesses to invest not only in robust systems but also in user-centric design principles.
Factors Influencing User Satisfaction
User satisfaction in WMS doesnât sit on a lone island; a variety of factors influences it. Identifying these can guide additional enhancements. Some critical factors include:
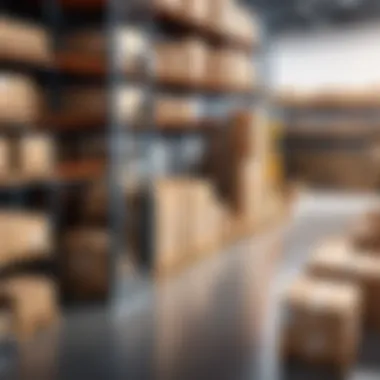
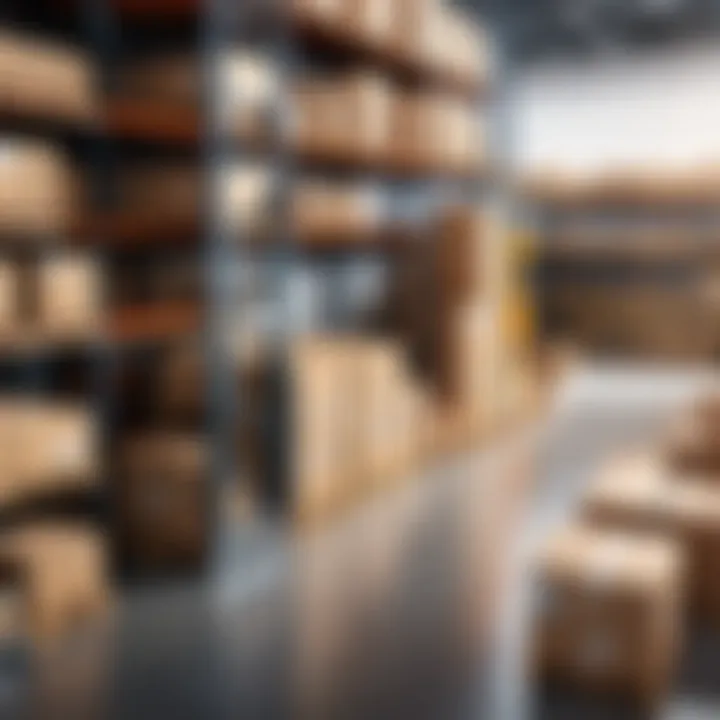
- System Reliability: A dependable system will invariably lead to reduced frustration. Frequent crashes or bugs deter users from fully engaging with the system.
- Performance Speed: Users expect real-time data and prompt processing. Slow responses can undermine their trust and increase errors.
- Adaptability: Businesses evolve; thus, systems that can grow and adapt to new requirements are highly valued.
To drive satisfaction, organizations must constantly observe and measure user feedback. By integrating this feedback loop, they can refine interfaces and functionalities accordingly.
Case Studies of WMS Implementation
Real-world stories often shine a light on theoretical concepts, and this holds true for WMS implementation. Letâs look at a couple of insightful examples:
Case Study 1: ABC Distribution
ABC Distribution faced significant challenges with manual inventory tracking, leading to discrepancies and mismanagement. Upon implementing a WMS, they streamlined operations. During the onboarding, they involved employees in the process. As a result, not only did efficiency increase by 30%, but employee satisfaction improved too. Strong user feedback was instrumental in continuous system refinement.
Case Study 2: XYZ Retail
XYZ Retail integrated a WMS with a focus on mobile accessibility. Their warehouse staff utilized handheld devices. This approach not only allowed for easier access to information on-the-go but also reduced paperwork. The outcome was remarkable: order fulfillment rates soared while errors plummeted. Satisfaction surveys indicated that employees felt empowered and capable.
"The user experience should be the bedrock upon which your Warehouse Management System stands. Itâs where technology meets human touch, and therein lies the true value."
Technological Advancements in WMS
The landscape of Warehouse Management Systems (WMS) is evolving at a rapid pace due to the continuous integration of cutting-edge technologies. These advancements not only enhance operational efficiency but also bolster inventory management, accuracy, and overall workplace safety. Understanding the role of technology in WMS is crucial for professionals who are navigating the complex world of logistics and supply chain management.
Integration with AI and Automation
In recent years, artificial intelligence (AI) and automation have emerged as powerful allies for warehouse managers. The integration of AI facilitates smarter decision-making by analyzing vast amounts of data in real time. For instance, using machine learning algorithms, a WMS can forecast inventory needs based on historic trends, seasonal demands, and sales patterns. Consequently, businesses can avoid overstock or stockouts, leading to better cash flow management.
Furthermore, automated systems such as conveyor belts and automated guided vehicles (AGVs) are swift and efficient in moving products. This technology not only reduces labor costs but also minimizes human errors, making operations smoother. Companies stand to gain significantly if they adopt these innovations. Itâs about not just keeping pace but staying a step ahead.
The Role of Robotics in Warehousing
Robotics sprinkled into the warehouse mix is like adding a turbocharger to a car. Robotics are revolutionizing warehouse operations by performing repetitive tasks with precision. Tasks that once took hours can now be done in mere minutes. Consider how warehouses are integrating robotic arms for sorting and packaging. These robots increase speed and reduce the risk of repetitive strain injuries. Additionally, warehouses are deploying robotic inventory drones to perform cycle countsâsaving time and ensuring accuracy.
However, introducing robotics requires a strategic approach. Companies must ensure that their workforce is properly trained to work alongside these machines, fostering collaboration rather than competition. Balancing human intuition against robotic efficiency can yield impressive results.
Cloud-Based WMS Solutions
The shift towards cloud-based WMS solutions is more than a trend; it's an essential evolution for businesses aiming for operational flexibility. Cloud technology provides scalability and accessibility. This means businesses can adjust their WMS as demand fluctuates without heavy upfront investments in infrastructure.
Cloud solutions also guarantee real-time updates and data security, allowing teams to track inventory and analyze performance metrics from anywhere in the world. Coupled with mobile capabilities, staff can access information and receive instructions on-the-go. This is vital in todayâs fast-paced environment where having the right information at the right moment can make all the difference.
Investing in technological advancements in WMS is not just optional anymore; it has become a necessity to maintain competitive edge in the market.
In summary, the integration of AI, automation, robotics, and cloud solutions into WMS represents crucial advancements. These technologies contribute not just efficiencies but also create a framework for sustainable growth. The future of warehousing will likely be shaped by those organizations willing to embrace these innovations and adapt rapidly to change.
Challenges in WMS Experience
In the landscape of Warehouse Management Systems, encountering challenges is par for the course. Recognizing these challenges is crucial not just for tech enthusiasts but also for professionals and decision-makers looking to bolster their operations. Without a clear understanding of the specific elements that pose obstacles during implementation and usage, even the most advanced systems may fall short of expectations. This section aims to unpack common hurdles faced in the WMS journey and consider the subsequent implications on operational efficacy.
Common Pitfalls in Implementation
Implementing a new WMS is akin to mixing a fine cocktailâget the ratios wrong, and the whole drink could end up tasting bitter. One of the most prominent issues organizations face is inadequate planning prior to deployment. Procrastination in assessing the unique needs of a warehouse can lead to selecting a system that doesnât align with operational workflows. Furthermore, failing to involve key stakeholders during the selection phase can spark a cascade of user dissatisfaction down the line.
Consider these points for a deeper understanding of common pitfalls:
- Poorly Defined Goals: Not having clear objectives can cause confusion, leading to misallocation of resources and wasted time.
- Underestimating Training Needs: Assuming that users will intuitively grasp system functions can be detrimental. Comprehensive training is non-negotiable.
- Neglecting Data Migration: Data migration can be a labyrinthine task when not properly strategized. Incomplete or incorrect data can hinder operations.
Highlighting the importance of these pitfalls is critical, as making mistakes during implementation can severely tarnish the overall WMS experience, making it harder to achieve desired efficiencies.
Impact of Resistance to Change
When introducing a WMS, itâs not uncommon for friction to arise among existing staff, a phenomenon known as resistance to change. This can manifest in various waysâsome may feel overwhelmed, while others could be skeptical about the benefits of the new system. Take a step back and reflect: how often have you clung to old habits even when faced with a more efficient alternative?

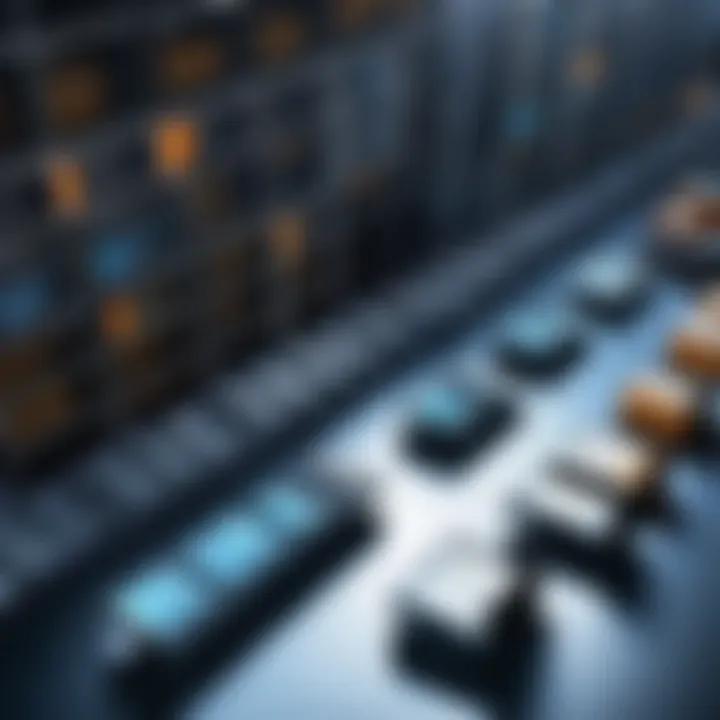
The implications of this resistance can be far-reaching:
- Decreased Morale: Staff who are hesitant to adapt may feel alienated from the process, leading to dissatisfaction.
- Stalled Progress: Resistance can slow down implementation timelines, delaying the potential benefits that could come from an efficient WMS.
- Increased Errors: Users who are reluctant or frustrated might make mistakes, leading to data inaccuracies, inefficiencies, or even financial losses.
"An organizationâs true strength emerges not from its technology, but from its ability to embrace change."
This new perspective can ease transition pains and improve overall user experience.
Data Security Concerns
In a digitized age, safeguarding sensitive information is non-negotiable. The move to a WMS typically brings a host of data security concerns to the fore. For instance, warehouses often contain valuable intellectual property, customer data, and supply chain details that, if compromised, could lead to significant damageâfinancially and reputationally.
Common security worries include:
- Unauthorized Access: Without strict access controls, sensitive data may be exposed or manipulated.
- Data Loss: System outages or failures can result in the loss of critical data if not backed up securely.
- Regulatory Compliance: Inconsistent compliance with industry standards can lead to legal repercussions.
To mitigate these risks, organizations can look into enhanced cybersecurity measures and regular audits of their WMS. Investing in training staff on data protection policies is equally essential to cultivate a security-aware culture.
Navigating these challenges demands attention, but acknowledging them lays the groundwork for a more fruitful WMS experience.
Enhancing WMS User Experience
Creating a truly effective Warehouse Management System (WMS) is not just about technology; itâs also about the folks using it. When the user experience is prioritized, it leads to better satisfaction among employees, fewer errors in operations, and, ultimately, a smoother workflow overall. In this section, we take a closer look at a few key facets of enhancing the WMS user experience and what benefits come with them.
Training and Development Programs
Training is the backbone of any successful system implementation. Strong training programs ensure employees know how to navigate the WMS effectively. A good program trains users on the mechanics of the system but also ties training to real-world scenarios they will face in their daily tasks. This dual approach not only increases competence but fosters confidence.
Some aspects to consider include:
- Initial Onboarding: New users should have a structured onboarding process that familiarizes them with the systems they will be using daily.
- Continued Education: As the system evolves, itâs crucial to provide ongoing training to keep users updated on new features or processes.
- Mentorship Programs: Pairing seasoned workers with newcomers can improve knowledge transfer and instill a stronger workplace culture.
Investment in training leads to significant improvements in productivity and job satisfaction. Staff that feels equipped and knowledgeable is often more engaged and less likely to make avoidable mistakes, which brings us to the next point.
User Interface and Usability Improvements
An intuitive user interface can dramatically shape the user experience. If the system is overly complicated, it may lead to frustration and decreased efficiency. WMS platforms should minimize the number of clicks needed to perform critical tasks, thus streamlining processes.
Key attributes of a user-friendly interface include:
- Simplicity: Clear icons and straightforward language can make navigation intuitive.
- Customization Options: Allowing users to tailor certain features to their preferences can also aid usability.
- Responsive Feedback: Systems that provide immediate feedback when a task is completed help users understand the effectiveness of their actions.
It's vital to remember that usability isnât just about making things easier; itâs about making processes more effective too.
Feedback Loops and Continuous Improvement
Implementing a feedback loop is essential in creating a dynamic environment where users feel their voices are heard. Regularly collecting feedback on both the system and training methods can help identify shortcomings and highlight areas for improvement.
Consider these methods for effective feedback collection:
- Surveys and Questionnaires: Regularly ask users about their experiences and any difficulties they encounter. Be specific in questions to elicit practical responses.
- Focus Groups: Gathering a small group of users to discuss functionality can yield deeper insights than surveys alone.
- Real-Time Reporting: A system that allows employees to report problems or suggestions right away ensures issues are brought to light promptly.
All of these efforts contribute to a culture of continuous improvement, ensuring that the WMS remains relevant and effective for its users.
"A system cannot just be built; it requires constant nurturing and adjustments to truly serve its purpose."
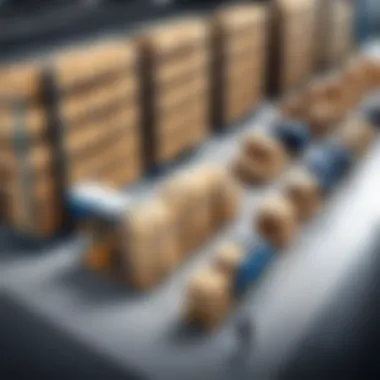
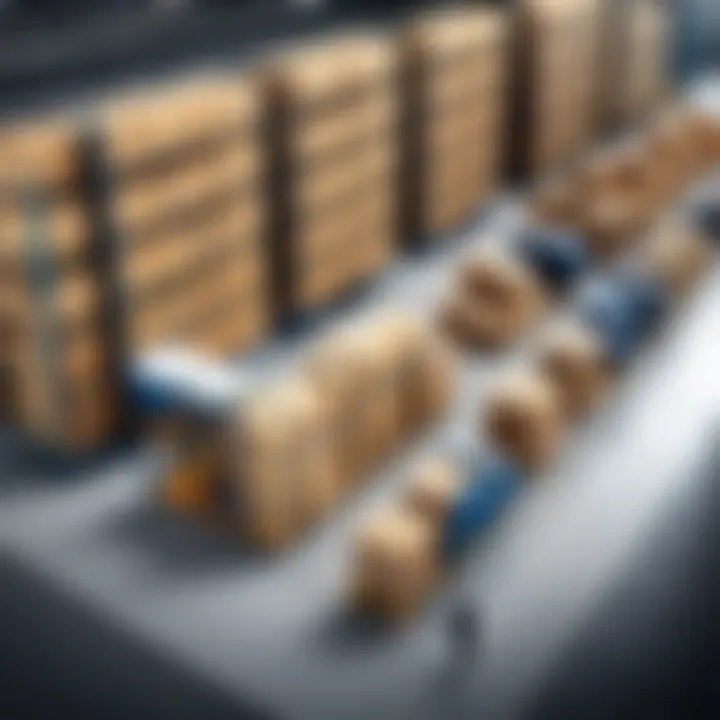
Integrating these elements creates an environment that doesnât just accommodate users but empowers them. By aligning the WMS with the needs and experiences of its users, organizations can achieve a more seamless operation.
Future Trends in WMS Experience
Understanding the future trends in Warehouse Management Systems (WMS) is crucial because the landscape of warehousing and logistics is evolving rapidly. An intricate combination of technology, consumer behavior, and environmental awareness is reshaping how businesses approach warehouse operations. The trends discussed in this section highlight innovative practices and strategies that are designed to optimize efficiency, sustainability, and adaptability in warehousing. By recognizing these trends, companies can remain competitive and relevant in a constantly changing market.
Predictive Analytics in Warehousing
Predictive analytics has emerged as a game changer in the warehousing sector. By harnessing data from various sources, including historical sales data, inventory levels, and customer demand patterns, businesses can forecast future trends with impressive accuracy. This approach not only helps in managing stock levels but also reduces overhead costs. Companies can anticipate peaks in demand and adjust their inventory accordingly.
For instance, a retail company might analyze past sales data to predict which items are likely to sell during the holiday season. This proactive approach enables warehouses to optimize their storage and movement of goods, enhancing overall operational effectiveness.
"In the world of warehousing, it's not about what has happened, it's about anticipating what will happen next."
Moreover, predictive analytics allows for better allocation of resources, minimizing the risk of stockouts and overstocks. When integrated with other technologies like artificial intelligence, the forecasting becomes even sharper, enabling companies to develop strategic plans that align with their business objectives.
Sustainability in Warehouse Operations
Sustainability has become more than just a buzzword; it is now an essential objective for many businesses. Within the context of warehouse operations, implementing sustainable practices can lead to significant benefits, from cost savings to improved brand reputation. Strategies can include energy-efficient systems, eco-friendly packaging, and waste reduction initiatives.
Expanding on the trend of sustainability, companies are reassessing their warehousing layouts to enhance eco-efficiency. Using renewable energy sources, such as solar panels, for powering warehouse operations can offset energy costs and decrease carbon footprints.
Furthermore, employing a green supply chain approach not only reduces the environmental impact but also appeals to consumers who are becoming increasingly conscious about their choices. This can translate into a competitive advantage as customers tend to favor brands that prioritize sustainability.
The Influence of E-commerce on WMS
E-commerce has revolutionized the way businesses manage their warehouses. With the surge in online shopping, warehouses must adapt to meeting customer expectations for rapid fulfillment and accuracy. Efficient Order Management Systems integrated with WMS facilitate real-time inventory tracking, enabling businesses to respond swiftly to consumer demands.
Additionally, the rise in e-commerce has led to a trend towards decentralization of warehouses. Instead of relying on a few large distribution centers, companies are establishing smaller hubs closer to urban areas. This approach not only enhances delivery speed but also reduces transportation costs.
However, this decentralization presents challenges, such as managing multiple inventory systems and ensuring cohesive operations across various sites. Thatâs where advanced WMS come into play, equipped with features that streamline processes across several locations, ensuring smooth operations.
Epilogue: Maximizing WMS Experience
The journey of optimizing Warehouse Management Systems (WMS) is crucial for organizations aiming to enhance their operational efficiency. This section wraps up the discussions presented throughout the article, underscoring how aligning WMS with business goals and employing strategic insights can create a more effective and responsive warehousing environment.
To navigate through the complexities of todayâs logistics landscape, understanding and fostering a robust WMS experience is indispensable. It serves not only as a tool for managing day-to-day operations but also as a strategic asset that can drive long-term success.
"A well-integrated WMS can streamline processes, reduce errors, and ultimately, elevate customer satisfaction."
Considerable benefits await those who prioritize the alignment of their WMS with their overarching business ambitions. Companies that invest time in understanding the nuances of their operations are likely to reap the rewards, from efficiency gains to improved inventory management. Achieving this alignment facilitates the identification of key performance indicators that can be tracked and measured effectively, providing clarity on the impact of WMS systems on overall productivity.
Aligning WMS with Business Goals
For any WMS initiative to be truly effective, it must be matched with the broader business objectives of the organization. This means that before implementation, stakeholders need to sit down and map out their goals clearly. Are you looking to reduce overhead costs? Maybe increasing inventory turnover is top of mind? Whatever the aim, a thoughtful approach ensures that the WMS is not just a stand-alone system but a component that enhances the organizationâs strategic vision.
Key elements to consider include:
- Operational Goals: Identify specific operational targets you wish to achieve with your WMS.
- Performance Metrics: Outline success metrics, such as order picking accuracy or cycle times, which align directly with business objectives.
- Scalability: Recognize the potential for growth and how a WMS can evolve alongside your companyâs demands.
- Integration with Other Systems: Ensure that your WMS can seamlessly communicate with existing software and tools to provide cohesive functionality.
By keeping these aspects in mind, organizations can avoid the pitfalls of disjointed implementation efforts, ensuring that the WMS truly serves to boost overall success.
Strategic Insights for Implementation
When it comes to the actual implementation of a WMS, strategic insights can make all the difference between a smooth process and a bumpy road. The following points should be taken into account:
- Stakeholder Involvement: Engage all relevant players from different departments early in the process. Getting buy-in from everyone can foster a collaborative atmosphere and streamline decision-making.
- Phased Rollout: Instead of a big bang approach, consider rolling out your WMS in phases. This method allows for more manageable changes and iterative improvements based on real feedback.
- Training Programs: Invest in quality training for your workforce. A well-trained staff is more likely to use the system effectively, maximizing its capabilities.
- Feedback Mechanisms: Establish channels for ongoing feedback during and after implementation. Continuous input will provide clarity on whatâs working and what requires adjustment.
- Performance Reviews: After implementation, it is essential to regularly review performance metrics against the set goals to ensure the WMS is delivering the expected results.
The culmination of aligning WMS with business goals and applying strategic insights will lead to maximizing the WMS experience. Through iterated learning and adaptation, organizations can create not only an efficient operation but one that anticipates future challenges and opportunities in the realm of warehousing.
Ultimately, a well-executed WMS strategy can result in a significant competitive edge, driving sustained improvements in both business operations and customer satisfaction.