Revolutionizing Warehouse Operations: The Impact of WMS Automation
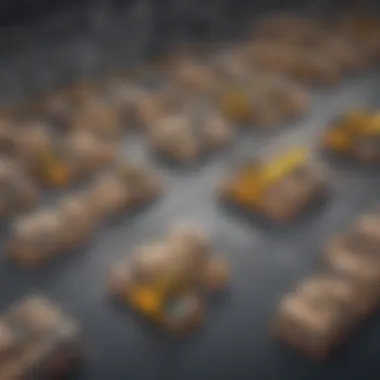
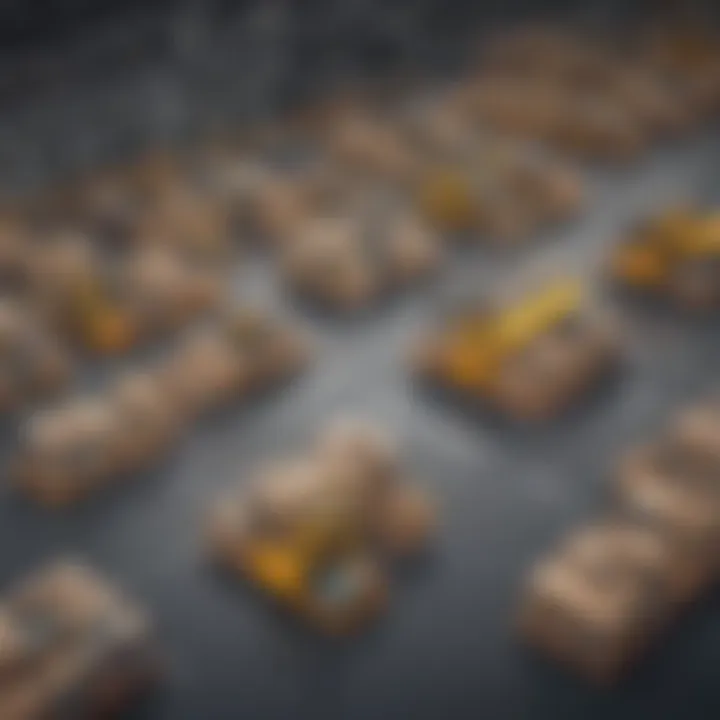
Technological Research Overview
In the realm of warehouse operations, the integration of technological advancements is reshaping traditional practices. Recent innovations in Warehouse Management Systems (WMS) automation have catalyzed a profound revolution, propelling businesses towards unparalleled efficiency and operational excellence. This section will delve into the critical role played by WMS automation in streamlining processes, optimizing inventory control, and ultimately aligning warehouse operations with the evolving demands of the modern market landscape.
With the proliferation of cutting-edge WMS automation technologies, businesses witness a substantial impact on their day-to-day operations. From increased productivity to enhanced accuracy in order fulfillment, the adoption of these systems revolutionizes the efficiency benchmarks of warehouses. This subsection will explore the tangible benefits experienced by organizations embracing WMS automation, shedding light on the newfound agility and resilience they demonstrate in response to market fluctuations.
As industries hurtle towards a technologically driven future, it is imperative to anticipate the trajectory of WMS automation. Unraveling the future trends in this domain will equip businesses with foresight, allowing them to strategize and adapt proactively. By exploring potential advancements such as advanced robotics integration and predictive analytics within warehouse systems, this segment aims to provide a glimpse into the technological landscape that awaits businesses venturing into automated warehouse management.
Introduction
Warehouse management system (WMS) automation stands at the forefront of modernizing businesses, offering a transformative impact on operational efficiency and inventory control. As industries evolve and adapt to the demands of a dynamic market landscape, the role of WMS automation becomes increasingly crucial. This article delves deep into the significance of revolutionizing warehouse operations through automation, shedding light on the myriad benefits, considerations, and future implications.
Understanding Warehouse Management Systems (WMS)
Defining Warehouse Management Systems
Warehouse management systems (WMS) encompass a comprehensive software solution tailored to streamline and optimize warehouse operations. Central to the logistics function, a WMS facilitates efficient inventory management, order tracking, and warehouse layout optimization. Its key characteristic lies in its ability to automate and synchronize various warehouse processes, enhancing operational productivity. In the context of this article, the defining feature of WMS is its integration of state-of-the-art technologies to drive accuracy and speed in warehouse management, making it a preferred choice for enterprises seeking to boost their logistical capabilities. While the unique feature of WMS lies in its real-time monitoring and reporting capabilities, which provide unparalleled visibility into warehouse activities, offering advantages in process optimization and resource allocation.
Key Features and Functionalities of WMS
When exploring the key features and functionalities of WMS, one encounters a robust array of tools designed to expedite order fulfillment, minimize errors, and optimize inventory control. From barcode scanning for seamless tracking to automated replenishment strategies for proactive stock management, WMS offers a comprehensive suite of functions to enhance operational efficiency. The standout characteristic of WMS functionalities lies in their ability to centralize data, enabling real-time decision-making and strategic planning. This centralized approach proves beneficial for users by ensuring accuracy, timely inventory insights, and streamlined warehouse operations. However, challenges may arise in customizing WMS functionalities to align with specific business needs, necessitating careful assessment during implementation to maximize advantages while minimizing disadvantages.
Evolution of WMS Automation
Historical Overview of Warehouse Automation
A historical overview of warehouse automation reveals a progressive journey from manual labor-intensive processes to fully automated systems powered by cutting-edge technologies. This evolution has reshaped traditional warehousing practices, ushering in an era of increased efficiency and accuracy. The key characteristic of historical warehouse automation lies in its gradual shift towards mechanization, driven by the quest for operational excellence and cost-effectiveness. This shift has significantly benefited enterprises by optimizing storage capacities, accelerating order fulfillment, and reducing human errors. Emphasizing the unique feature of historical warehouse automation, it has paved the way for modern WMS solutions by laying the groundwork for seamless integration of automation technologies into warehouse operations, presenting advantages in increased productivity and reduced lead times.
Integration of Technologies into WMS
The integration of advanced technologies into WMS represents a milestone in warehouse automation, marking a transition towards smarter, more adaptive warehouse management solutions. This integration blends cutting-edge innovations such as artificial intelligence, IoT, and machine learning into traditional WMS platforms, enhancing their functionalities. The key characteristic of technology integration in WMS lies in its ability to harness data-driven insights for predictive analytics and strategic decision-making. By leveraging interconnected technologies, WMS can optimize storage utilization, streamline order processing, and enhance inventory visibility. However, the challenge lies in ensuring seamless integration and compatibility of diverse technologies within the WMS framework, requiring meticulous planning and testing to capitalize on the advantages while mitigating potential disadvantages.
Benefits of Warehouse Management System Automation
Warehouse Management System (WMS) automation plays a pivotal role in transforming how modern businesses operate. By streamlining operations and enhancing overall efficiency, WMS automation is a key driver in optimizing warehouse processes. The implementation of automated systems in warehouse management not only increases productivity but also reduces errors substantially, leading to cost savings and improved customer satisfaction.
Enhanced Efficiency and Productivity
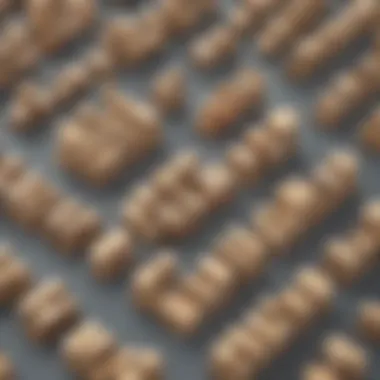
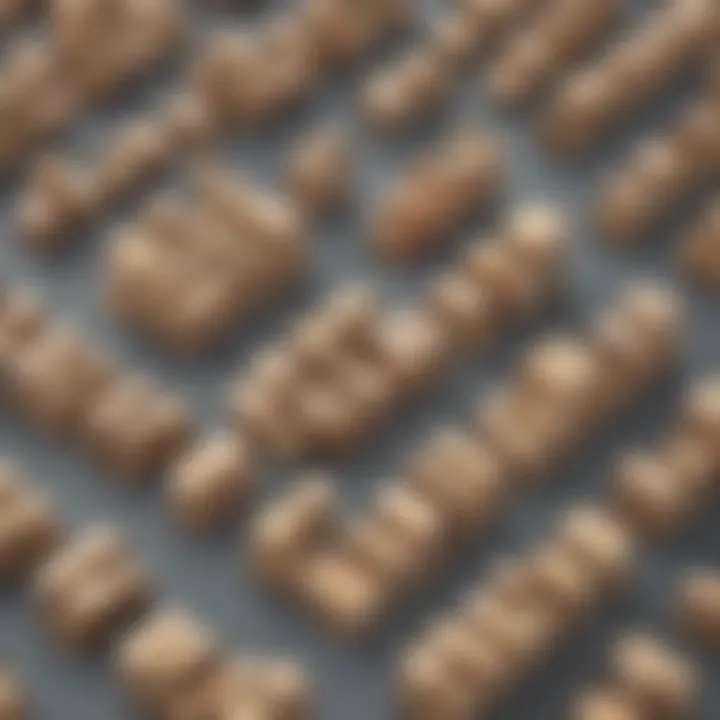
Streamlining order fulfillment processes: Streamlining order fulfillment processes is a critical aspect of WMS automation that greatly contributes to operational excellence. This approach involves optimizing the flow of orders from placement to delivery, focusing on speed and accuracy. By automating this process, businesses can minimize order processing times, reduce errors, and ensure timely deliveries. The key characteristic of streamlining order fulfillment is its ability to synchronize different stages seamlessly, resulting in a more efficient and reliable system. One of the significant advantages of this process is the significant reduction in order processing times, leading to enhanced customer satisfaction and increased operational efficiency.
Reducing manual errors and operational costs: Another vital aspect of WMS automation is reducing manual errors and operational costs. Manual errors in warehouse operations can lead to delays, stock discrepancies, and customer dissatisfaction. By automating tasks that are prone to human error, such as data entry and inventory management, businesses can vastly reduce mistakes and enhance the accuracy of their operations. Additionally, by automating repetitive tasks, companies can significantly lower operational costs associated with labor, training, and inefficient processes. The unique feature of this aspect is its ability to implement error-checking algorithms and validation processes that minimize the occurrence of mistakes, resulting in improved operational efficiency and cost-effectiveness. Embracing automated solutions for error reduction can yield long-term benefits in terms of operational excellence and profitability.
Real-Time Inventory Control
Inventory tracking and visibility: Real-time inventory tracking and visibility are indispensable components of effective warehouse management. By leveraging automated systems, businesses can monitor inventory levels accurately in real-time, allowing for better decision-making and inventory planning. The key characteristic of this aspect is its ability to provide instant updates on stock levels, locations, and movements, ensuring optimal inventory control. This feature is a valuable choice for this article as it highlights the significance of real-time information in managing inventory efficiently. One of the unique advantages of this system is its capacity to prevent stockouts, overstocking, and delays in order fulfillment, resulting in improved customer service and operational agility.
Automated replenishment strategies: Automated replenishment strategies involve using data-driven algorithms to optimize inventory levels and automate restocking processes. By analyzing demand patterns and setting reorder points, businesses can ensure that stock is replenished promptly and efficiently. The key characteristic of this approach is its proactive nature, which minimizes the risk of stockouts and maximizes storage efficiency. Automation of replenishment strategies is a popular choice for this article as it underscores the importance of smart inventory management practices. The unique feature of this strategy lies in its ability to adapt to changing demand dynamics and adjust stock levels accordingly, enhancing operational efficiency and responsiveness to market fluctuations.
Optimized Space Utilization
Dynamic slotting techniques: Dynamic slotting techniques involve organizing warehouse inventory based on picking frequency, storage requirements, and product characteristics to maximize space utilization and efficiency. By strategically assigning storage locations to items, businesses can reduce travel times, improve picking accuracy, and optimize overall warehouse layout. The key characteristic of dynamic slotting is its ability to continuously optimize storage locations to align with changing demand patterns and seasonal fluctuations. This method is a beneficial choice for this article as it emphasizes the importance of proactive warehouse layout strategies. The unique feature of dynamic slotting lies in its flexibility and adaptability, allowing businesses to enhance operational efficiency and minimize picking times through smart inventory organization.
Maximizing storage capacity: Maximizing storage capacity is crucial for businesses looking to optimize warehouse space and accommodate growing inventory volumes. By employing space utilization techniques such as vertical stacking, cross-docking, and racking systems, companies can make the most of their available space. The key characteristic of maximizing storage capacity is its focus on efficient space utilization without compromising accessibility or operational efficiency. This strategy is a popular choice for this article as it highlights the importance of resource optimization in warehouse management. The unique feature of maximizing storage capacity is its ability to increase inventory density, reduce storage costs, and streamline warehouse operations, resulting in enhanced productivity and cost savings.
Implementation of WMS Automation
Assessment and Planning
Evaluating current warehouse processes
Evaluating current warehouse processes is an essential step in the implementation of WMS automation as it provides insights into existing operational inefficiencies and areas for improvement. Assessing current processes involves analyzing workflow, identifying bottlenecks, and understanding the gaps that automation can address. This evaluation not only streamlines warehouse operations but also sets the foundation for developing a customized automation strategy tailored to the specific needs of the business.
Developing a customized automation strategy
Developing a customized automation strategy is critical in leveraging the full potential of WMS automation for warehouse operations. This process involves designing a tailored solution that aligns with the unique requirements of the business, such as order volume, product types, and customer demands. By creating a customized strategy, businesses can ensure seamless integration of automation technologies, maximize operational benefits, and drive long-term efficiency gains.
Integration with Existing Systems
Compatibility with ERP systems
Integrating WMS automation with Enterprise Resource Planning (ERP) systems is integral to ensuring a cohesive and efficient operational environment. Compatibility with ERP systems streamlines data exchange, enhances visibility across departments, and facilitates real-time decision-making. By integrating WMS automation with ERP systems, businesses can achieve operational synergy, optimize resource allocation, and improve overall productivity and responsiveness.
Data migration and system integration
Effective data migration and system integration are essential components of WMS automation implementation. Smooth data migration ensures accurate transfer of information from legacy systems to the new automated platform, minimizing disruptions and data discrepancies. System integration, on the other hand, focuses on aligning different software and hardware components to function cohesively, enabling seamless communication and interoperability within the warehouse ecosystem.
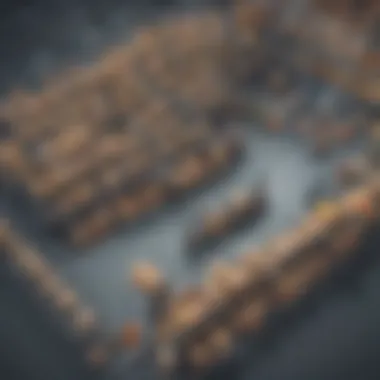
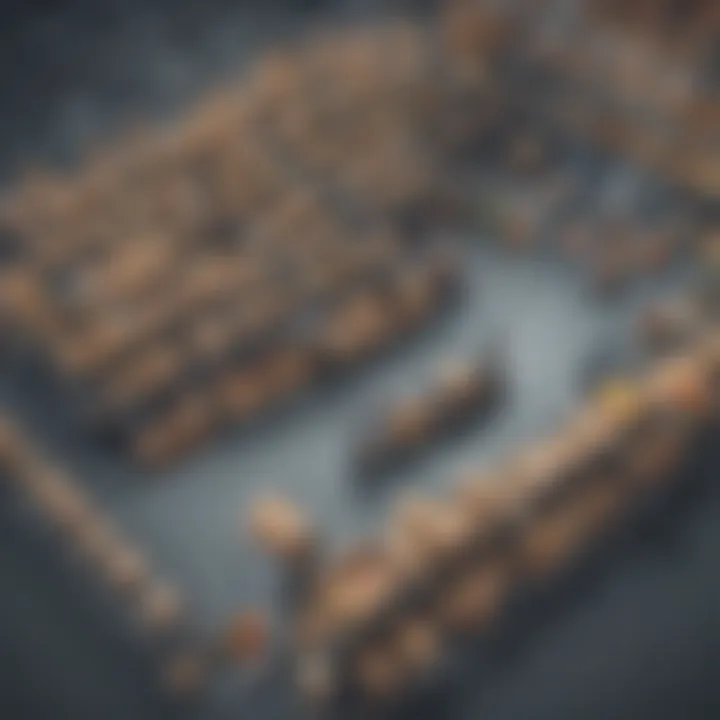
Training and Change Management
Employee training on new systems
Providing comprehensive training to employees on new automation systems is critical to the successful implementation of WMS automation. Employee training enhances proficiency in using automated tools, fosters a culture of continuous learning, and ensures smooth transition to the automated environment. By investing in employee training, businesses can empower their workforce, increase operational efficiency, and drive overall productivity.
Managing organizational transition
Effective management of organizational transition is key to overcoming resistance to change and ensuring smooth adoption of WMS automation. Managing organizational transition involves proactive communication, stakeholder engagement, and change readiness assessments. By addressing employee concerns, aligning organizational goals, and providing adequate support during the transition phase, businesses can mitigate disruptions, boost employee morale, and accelerate the realization of automation benefits.
Challenges and Considerations
In the realm of revolutionizing warehouse operations through automation, delving into the challenges and considerations is paramount. Understanding the complexities and intricacies involved in implementing warehouse management system automation is crucial for successful deployment. These challenges encompass various facets, from initial financial investments to ensuring cybersecurity measures and mitigating operational disruption. Businesses embarking on this transformational journey must navigate through these challenges adeptly to reap the full benefits of automation.
Cost Implications
Breaking down the cost implications of warehouse management system automation is a multifaceted endeavor. The decision-making process often revolves around comparing the initial investment with the long-term return on investment (ROI). This analysis plays a pivotal role in designing a sustainable and financially sound automation strategy. Evaluating the balance between upfront costs and future gains is essential for businesses striving to optimize their warehouse operations through automation.
Initial Investment vs. Long-term ROI
Comparing the initial investment required for implementing warehouse management system automation with the anticipated long-term ROI sheds light on the financial viability of the project. Businesses need to assess the short-term commitments against the projected benefits over an extended period. This deliberation aids in determining the economic feasibility of automation initiatives and aligning them with overarching business goals.
Maintenance and Upgrade Costs
The ongoing maintenance and upgrade costs associated with warehouse management system automation constitute a critical component of the overall cost implications. Ensuring the seamless operation of automated systems necessitates continuous investment in maintenance and timely upgrades. Balancing the expenses related to system upkeep with the potential efficiency gains is integral to sustaining the efficacy of automation solutions.
Cybersecurity Risks
Addressing cybersecurity risks in the context of warehouse management system automation is indispensable in safeguarding critical data and operations. Implementing robust data security measures and protocols is imperative to fortify the digital infrastructure against potential threats. Mitigating cyber threats requires a proactive approach that encompasses preemptive strategies and vigilant monitoring to uphold data integrity and operational continuity.
Data Security Measures and Protocols
Implementing comprehensive data security measures and protocols forms the cornerstone of a secure automation framework. Establishing stringent access controls, encryption protocols, and regular cybersecurity audits are fundamental in mitigating vulnerabilities and ensuring data confidentiality. By prioritizing data security, businesses can instill trust and reliability in their automated warehouse systems.
Mitigating Cyber Threats
The proactive mitigation of cyber threats involves deploying advanced cybersecurity tools and proactive monitoring mechanisms. Identifying potential vulnerabilities and preemptively addressing security loopholes are central to thwarting malicious cyber activities. By staying ahead of emerging threats and bolstering cybersecurity defenses, businesses can avert potentially detrimental impacts on their automated warehouse operations.
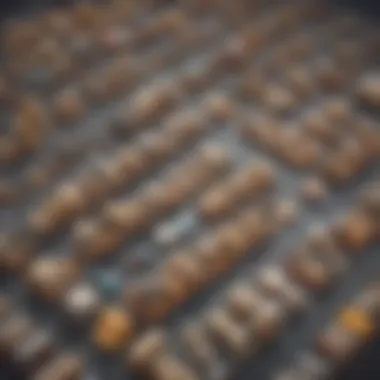
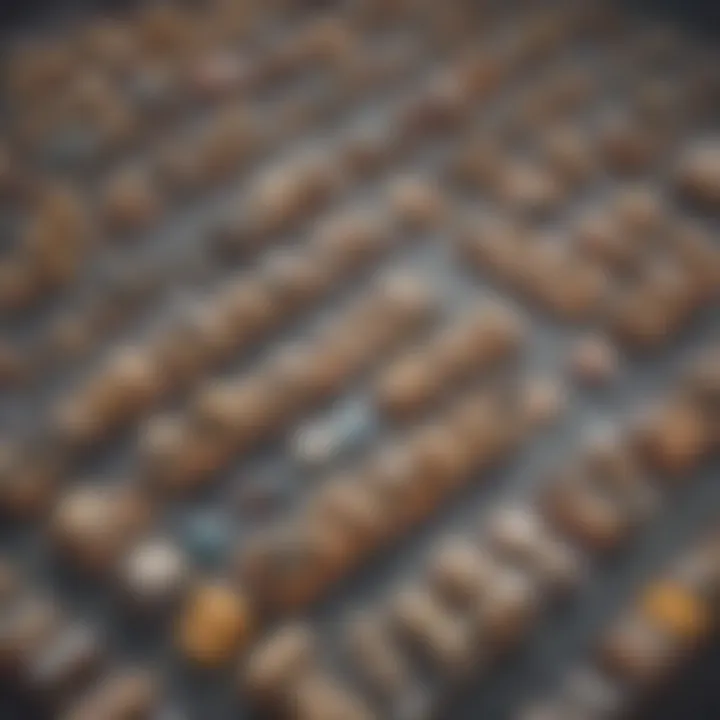
Operational Disruption
Understanding the implications of operational disruption within the realm of warehouse management system automation necessitates a comprehensive analysis of potential challenges. Transitioning to automated processes can introduce disruptions that require strategic planning and effective management to mitigate adverse impacts. Anticipating and addressing operational disruptions are key to ensuring a seamless transition to automated warehouse operations.
Transition Impact on Daily Operations
The transition impact on daily operations underscores the need for meticulous planning and stakeholder engagement. Implementing changes associated with automation can temporarily disrupt established workflows and routines. Balancing the integration of automated processes with ongoing operations is essential to minimize productivity interruptions and ensure a smooth operational shift.
Contingency Planning for System Failures
Developing robust contingency plans for system failures is critical in maintaining operational resilience amidst potential technological setbacks. Preparing for unforeseen system malfunctions or downtime events requires proactive risk management and strategic contingency planning. Establishing backup strategies and recovery protocols can mitigate the impact of system failures on warehouse operations.
Future Trends in WMS Automation
The discourse on Future Trends in WMS Automation is of paramount significance within the broader conversation of warehouse management systems. As businesses navigate a rapidly evolving market landscape, the integration of cutting-edge technologies such as AI and machine learning into warehouse operations becomes a focal point for enhancing efficiency and productivity. The emphasis on Future Trends in WMS Automation underscores the importance of staying abreast of the latest advancements to remain competitive and meet the demands of the dynamic market.
AI Integration and Machine Learning
Predictive Analytics for Demand Forecasting
The integration of Predictive Analytics for Demand Forecasting within warehouse management systems leverages data-driven insights to anticipate market trends and consumer behavior. This strategic application of predictive analytics enables businesses to optimize inventory levels, streamline supply chain processes, and enhance overall operational efficiency. The adaptability and scalability of predictive analytics contribute significantly to forecasting accuracy, empowering organizations to make informed decisions swiftly and effectively.
Automated Decision-Making Algorithms
Automated Decision-Making Algorithms play a pivotal role in refining decision-making processes within warehouse operations. By automating critical decisions based on predefined parameters and data analysis, businesses can expedite response times, minimize human error, and enhance strategic planning. The agility and precision offered by automated decision-making algorithms empower organizations to optimize resource allocation, mitigate risks, and capitalize on emerging opportunities, ultimately fostering a competitive edge in the marketplace.
Robotics and Autonomous Vehicles
Utilizing Robots for Picking and Sorting
The incorporation of Robots for Picking and Sorting revolutionizes traditional warehouse processes by introducing precision and speed into order fulfillment activities. Robots equipped with advanced sensors and algorithms can navigate complex warehouse environments, retrieve items with precision, and optimize inventory storage. The seamless integration of robotics minimizes operational downtime, enhances order accuracy, and increases overall productivity, positioning organizations for scalability and operational excellence.
Incorporating Drones for Inventory Management
Incorporating Drones for Inventory Management introduces aerial capabilities to streamline warehouse logistics and inventory tracking. Drones offer real-time visibility into inventory levels, expedite stock counting procedures, and enhance surveillance of warehouse facilities. The agility and efficiency of drones enable organizations to conduct timely inventory audits, mitigate discrepancies, and ensure optimal inventory control, thereby amplifying operational efficiency and responsiveness.
IoT for Enhanced Connectivity
Real-Time Monitoring of Warehouse Operations
Real-Time Monitoring of Warehouse Operations integrates IoT devices to provide instant visibility into key operational metrics, such as inventory levels, equipment status, and order fulfillment progress. This real-time data orchestration facilitates proactive decision-making, resource allocation optimization, and performance benchmarking. The interconnectedness afforded by IoT devices enhances operational transparency, facilitates data-driven insights, and fosters a culture of continuous improvement within warehouse management systems.
Connected Devices for Data Synchronization
The synchronization of Connected Devices within warehouse management systems harmonizes data flows across disparate operational touchpoints, ensuring seamless communication and information exchange. Connected devices enable real-time collaboration, synchronized data updates, and streamlined connectivity between warehouse stakeholders. The interoperability of connected devices enhances operational visibility, accelerates decision-making processes, and fortifies data accuracy, culminating in enhanced operational efficiency and strategic alignment.