Unveiling the Significance of Six Sigma in Business Operations
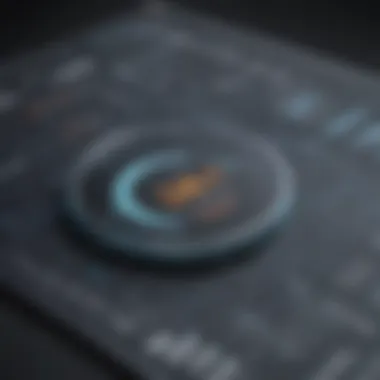

Technological Research Overview
Six Sigma, a quality management methodology, stands out as a pivotal framework within business operations. Understanding its essence requires a deep dive into its core principles and methodologies. In a world driven by efficiency and excellence, Six Sigma plays a vital role in optimizing processes and enhancing overall quality. With a relentless focus on data-driven decision-making and continuous improvement, this methodology offers a systematic approach to attaining near-perfect results.
Data Analytics in Business
The amalgamation of Six Sigma and data analytics can revolutionize business operations. Data analytics, pivotal in today's decision-making landscape, complements Six Sigma by providing insights that drive quality enhancements. Utilizing tools like statistical analysis and predictive modeling, businesses can leverage data to make informed decisions and streamline processes. Real-world case studies illustrate how data-driven strategies underpinning Six Sigma lead to improved efficiency and efficacy.
Cybersecurity Insights
In today's digital age, cybersecurity is a paramount concern for businesses adopting Six Sigma practices. Analyzing the threat landscape allows organizations to fortify their defenses systematically. Implementing best practices in cybersecurity ensures that data integrity and confidentiality are maintained, aligning with Six Sigma's emphasis on quality assurance. Compliance with regulations safeguards business processes, reinforcing the secure foundations of Six Sigma implementation.
Artificial Intelligence Applications
Artificial intelligence (AI) complements Six Sigma methodologies by automating processes and enhancing decision-making precision. AI algorithms analyze vast datasets swiftly, enabling proactive problem-solving and process optimization in business operations. While AI unlocks unparalleled efficiency, ethical considerations in its application are paramount. Mitigating biases and ensuring transparency in AI-driven decisions aligns with Six Sigma's pursuit of excellence through integrity.
Industry-Specific Research
Infusing Six Sigma principles into industry-specific research unveils tailored solutions for diverse sectors. In the finance domain, technology research enhances risk management and operational efficiency. Healthcare advancements driven by tech research optimize patient care and treatment outcomes. Likewise, the retail sector leverages tech solutions to streamline supply chain management and enhance customer experiences.
Introduction to Six Sigma
Six Sigma, a management philosophy that focuses on minimizing defects and improving processes, plays a vital role in enhancing business operations. In this section, we will delve into the foundational aspects of Six Sigma, elaborating on its significance in driving operational excellence and quality improvement within organizations. By understanding the principles and methodologies of Six Sigma, businesses can streamline their processes, reduce inefficiencies, and enhance overall customer satisfaction. The adoption of Six Sigma is crucial for businesses aiming to achieve consistent quality standards and sustainable growth.
Origins of Six Sigma
History of Six Sigma
The history of Six Sigma traces back to the mid-1980s when Motorola pioneered this methodology to elevate their production processes. By focusing on statistical methods to measure quality and eliminate defects, the concept gained traction as a quality management approach. The emphasis on data-driven decision-making and process improvement distinguishes the history of Six Sigma and underscores its impact on quality assurance practices in various industries. Understanding the origins of Six Sigma provides insights into its effective application in addressing quality-related challenges within organizations.
Evolution of Six Sigma Methodology
The evolution of Six Sigma methodology reflects a continuous refinement of tools and techniques aimed at achieving operational excellence. Over the years, Six Sigma has evolved from a quality improvement approach to a comprehensive management system encompassing strategic planning and execution. By incorporating customer feedback, process analysis, and performance metrics, the methodology has become a strategic asset for organizations seeking to optimize their operations. The evolution of Six Sigma methodology highlights its adaptability and relevance in addressing modern business challenges.
Definition of Six Sigma
Understanding the Concept of Six Sigma
Understanding the concept of Six Sigma entails grasping the core principles of process improvement and variance reduction. This methodology aims to achieve near-perfect performance by minimizing variability and enhancing efficiency across organizational processes. The focus on data-driven decision-making and constant improvement distinguishes the concept of Six Sigma as a transformative approach to quality management. By aligning business objectives with customer expectations, Six Sigma offers a systematic framework for driving excellence and consistency in operations.
Key Principles of Six Sigma
The key principles of Six Sigma revolve around defining customer requirements, measuring process performance, analyzing data, improving processes, and controlling variation. These principles guide organizations in identifying root causes of defects, optimizing processes, and sustaining improvements over time. By adhering to these principles, businesses can systematically enhance their quality standards, reduce costs, and achieve competitive advantage. The emphasis on continuous improvement and data-driven decision-making underscores the significance of key principles in implementing Six Sigma effectively.
Importance of Six Sigma
Benefits of Implementing Six Sigma
The benefits of implementing Six Sigma extend beyond defect reduction to encompass enhanced efficiency, customer satisfaction, and profitability. By fostering a culture of quality and problem-solving, organizations can drive innovation, reduce waste, and increase operational effectiveness. The systematic approach of Six Sigma empowers teams to identify improvement opportunities, implement solutions, and measure results systematically. The benefits of implementing Six Sigma are evident in improved productservice quality, enhanced customer loyalty, and sustainable business growth.
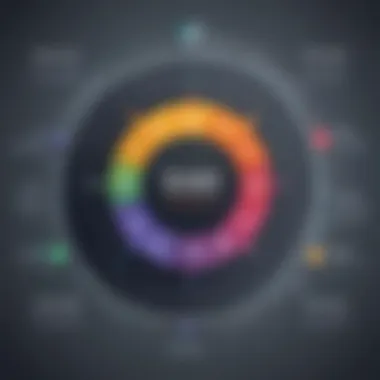

Impact on Business Performance
The impact of Six Sigma on business performance is profound, leading to increased productivity, reduced defects, and streamlined processes. By aligning business objectives with quality metrics and customer expectations, Six Sigma influences strategic decision-making and resource allocation. The methodology's emphasis on data analysis and performance measurement enables organizations to drive efficiency, minimize risks, and adapt to changing market dynamics. The impact of Six Sigma on business performance underscores its role as a catalyst for continuous improvement and organizational success.
Key Concepts in Six Sigma
In the realm of business operations, understanding the key concepts in Six Sigma is paramount. This section delves deep into the core principles and methodologies that drive quality enhancements and operational efficiency within organizations. By comprehending the nuances of Six Sigma concepts, businesses can achieve higher levels of operational excellence and quality improvement. Emphasizing the importance of these concepts sets the foundation for successful implementation and integration of Six Sigma methodologies.
DMAIC Methodology
Define Phase
The Define phase in the DMAIC methodology plays a crucial role in setting the project scope, objectives, and deliverables. By clearly defining the problem statement and project goals, organizations can align their resources and efforts towards achieving specific outcomes. This phase is characterized by its structured approach to clarifying project parameters, which ultimately guides the entire Six Sigma project towards success. The Define phase's unique feature lies in its ability to establish a solid foundation for the project, ensuring that all stakeholders understand the objectives and expectations clearly. While the Define phase provides clarity and direction, it may encounter drawbacks if the initial problem statement is unclear or ambiguous, leading to potential project delays or inefficiencies.
Measure Phase
Within the DMAIC methodology, the Measure phase focuses on quantifying process performance and gathering relevant data for analysis. By implementing measurement systems and metrics, organizations can objectively assess current process capabilities and identify areas for improvement. This phase stands out for its emphasis on data-driven decision-making and accurate performance assessment. The Measure phase's advantage lies in its ability to provide a factual basis for subsequent analysis and improvement initiatives. However, challenges may arise if data collection processes are inadequate or inaccurate, leading to flawed conclusions and misguided improvement efforts.
Analyze Phase
The Analyze phase of DMAIC entails in-depth scrutiny of collected data to pinpoint root causes of process inefficiencies and variations. Through statistical tools and techniques, organizations can identify correlations and patterns that contribute to existing process discrepancies. This phase is notable for its analytical rigor and problem-solving focus, facilitating a systematic approach to process improvement. The Analyze phase's strength lies in its capacity to uncover hidden issues and underlying causes, guiding organizations towards targeted solutions and performance enhancements. Nevertheless, if data analysis is conducted incorrectly or incompletely, organizations may overlook critical factors affecting process performance, hindering the effectiveness of improvement efforts.
Improve Phase
In the Improve phase of DMAIC, organizations implement and test solutions derived from the analysis phase to address identified process deficiencies. This stage emphasizes innovation, experimentation, and stakeholder involvement to drive meaningful change and performance enhancements. The Improve phase stands out for its proactive approach to problem resolution and its focus on sustainable process improvements. Its distinctive feature lies in fostering a culture of continuous enhancement and value creation within organizations. While the Improve phase encourages creativity and solution-oriented thinking, challenges may arise if implemented solutions are not thoroughly evaluated or fail to deliver the desired outcomes, limiting the effectiveness of improvement initiatives.
Control Phase
The Control phase in DMAIC involves implementing control mechanisms to sustain process improvements and prevent regression to previous performance levels. By establishing measurement systems and monitoring processes, organizations can ensure that implemented solutions produce lasting results and maintain desired performance standards. This phase is characterized by its emphasis on standardization, documentation, and ongoing monitoring to uphold process stability. The Control phase's unique feature lies in its ability to institutionalize best practices and embed quality improvements into daily operations. However, organizations may face difficulties sustaining improvements if control mechanisms are not diligently followed or if processes deviate from established standards, jeopardizing the long-term success of Six Sigma initiatives.
Implementing Six Sigma in Business
Implementing Six Sigma in Business is a critical aspect of operational excellence within organizations. As businesses strive for efficiency and quality improvement, the methodologies and principles of Six Sigma play a pivotal role. By integrating Six Sigma into their processes, companies can streamline operations, reduce defects, and enhance customer satisfaction. This section will delve into the essential elements, benefits, and considerations of Implementing Six Sigma in Business.
Steps to Implement Six Sigma
Identifying Processes
Identifying Processes is a foundational step in implementing Six Sigma in Business. By carefully analyzing and defining the key processes within an organization, businesses can pinpoint areas for improvement and optimization. This systematic approach enables companies to prioritize efforts effectively, leading to enhanced operational efficiency and quality outcomes. While Identifying Processes may require significant initial investment in time and resources, the long-term benefits of this step are instrumental in achieving Six Sigma success.
Training Team Members
Training Team Members is another crucial aspect of implementing Six Sigma in Business. Equipping staff with the necessary knowledge and skills to understand and apply Six Sigma methodologies is vital for the successful execution of quality improvement initiatives. Training ensures that team members are aligned with the goals of Six Sigma, fostering a culture of continuous improvement and data-driven decision-making. However, effective training programs can also pose challenges in terms of resource allocation and time management, requiring careful planning and execution.
Setting Quality Objectives
Setting Quality Objectives establishes the framework for Six Sigma implementation within an organization. Clear and measurable quality objectives provide the roadmap for defining success criteria and monitoring progress towards meaningful outcomes. By aligning quality objectives with the overall business strategy, companies can drive sustainable change and focus efforts on areas that will yield the highest impact. However, setting quality objectives requires a thorough understanding of business needs and stakeholder expectations to ensure relevance and alignment.
Data Collection and Analysis
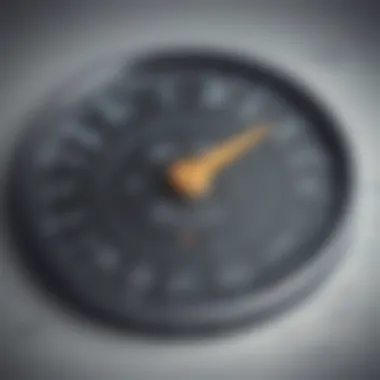

Data Collection and Analysis form the heart of Six Sigma methodologies, offering a systematic approach to problem-solving and decision-making. By gathering relevant data and applying statistical tools, businesses can identify root causes of issues, measure process performance, and validate improvement efforts. Effective data collection and analysis require attention to detail, accuracy, and consistency to derive meaningful insights and drive informed decision-making. However, challenges such as data integrity, accessibility, and analysis complexity may hinder the effectiveness of this crucial step.
Continuous Improvement
Continuous Improvement is the hallmark of Six Sigma, emphasizing the ongoing pursuit of excellence and innovation. By fostering a culture of continuous improvement, organizations can adapt to changing market dynamics, customer needs, and technological advancements. Encouraging feedback, embracing experimentation, and empowering employees to contribute ideas are essential components of driving continuous improvement initiatives. However, sustaining momentum for continuous improvement initiatives amidst competing priorities and resource constraints presents its own set of challenges.
Common Tools and Techniques
Pareto Analysis
Pareto Analysis, known as the 8020 rule, is a valuable tool in prioritizing efforts based on the significance of contributing factors. By identifying the most critical issues that have the greatest impact on outcomes, businesses can focus resources on high-impact areas for maximum efficiency and effectiveness. Although Pareto Analysis provides valuable insights into process improvement priorities, interpreting the data accurately and implementing appropriate actions can be complex and time-consuming.
Fishbone Diagram
The Fishbone Diagram, also known as the Ishikawa diagram, is a visual tool for identifying potential causes of a problem. By categorizing possible causes into distinct categories, businesses can uncover underlying root causes and connections that contribute to quality issues or process deviations. While the Fishbone Diagram aids in structured problem-solving and decision-making, capturing all relevant factors and ensuring comprehensive analysis can be challenging in complex business environments.
Control Charts
Control Charts play a crucial role in monitoring process performance and detecting variations or anomalies over time. By tracking process data and plotting it on control charts, organizations can assess process stability, identify trends, and make timely adjustments to maintain quality standards. However, interpreting control chart patterns accurately, distinguishing between common and special causes of variation, and implementing corrective actions require deep statistical knowledge and expertise.
Statistical Process Control
Statistical Process Control (SPC) leverages statistical techniques to monitor and control process variations, ensuring consistent and predictable outcomes. By establishing control limits and analyzing process data using statistical methods, businesses can proactively detect issues, prevent defects, and optimize process performance. Implementing SPC demands proficiency in statistical analysis, data interpretation, and process understanding to leverage the full potential of this technique for sustainable quality improvement.
Success Stories of Six Sigma
In the realm of business, understanding the success stories of Six Sigma is paramount to grasping the practical applications and outcomes of this methodology. Success stories serve as compelling illustrations of the impact Six Sigma can have on organizational performance, quality enhancement, and operational excellence. By examining successful implementations of Six Sigma, businesses gain valuable insights into how this methodology can drive tangible improvements and deliver positive results. These stories highlight the effective utilization of Six Sigma principles, methods, and tools to achieve specific goals and address critical issues within different industries.
Case Studies
General Electric (GE)
General Electric (GE) stands out as a pioneering example of successful Six Sigma implementation in the business landscape. The key characteristic of GE's approach to Six Sigma lies in its in-depth focus on data-driven decision-making and process improvement. GE's commitment to quality excellence through Six Sigma methodologies has enabled the company to enhance operational efficiency, streamline processes, and provide superior products and services to customers. This has positioned GE as a beneficial and popular choice for showcasing the effectiveness of Six Sigma in driving business success. One unique feature of GE's Six Sigma journey is its continuous pursuit of performance excellence and customer satisfaction, leading to significant competitive advantages and sustainable growth.
Motorola
Motorola's contribution to the realm of Six Sigma underscores the transformative power of this methodology in achieving organizational objectives. The key characteristic of Motorola's Six Sigma implementation is its emphasis on defect reduction, process optimization, and customer-centric strategies. By prioritizing quality control and process excellence, Motorola has reaped substantial benefits in terms of cost savings, market competitiveness, and customer loyalty. This positions Motorola as a preferred example for highlighting the advantages of integrating Six Sigma principles into business operations. One unique feature of Motorola's Six Sigma initiatives is the systemic approach to problem-solving and performance enhancement, leading to unparalleled efficiencies and continuous innovation.
Toyota
Toyota's adoption of Six Sigma principles has significantly influenced its operational capabilities and competitive position in the global market. The key characteristic of Toyota's utilization of Six Sigma revolves around lean manufacturing, waste reduction, and quality management practices. By integrating Six Sigma methodologies into its production processes and supply chain management, Toyota has been able to achieve remarkable improvements in product quality, cost efficiency, and customer satisfaction. This solidifies Toyota's reputation as a strategic choice for showcasing the benefits and considerations associated with implementing Six Sigma in a manufacturing context. A unique feature of Toyota's Six Sigma integration is its emphasis on employee empowerment, continuous learning, and innovative problem-solving, fostering a culture of excellence and sustainability.
Impact on Industries
Manufacturing
In the manufacturing sector, Six Sigma has emerged as a powerful catalyst for driving process efficiency, standardizing operations, and ensuring product quality. The key characteristic of Six Sigma in manufacturing lies in its ability to reduce defects, minimize variations, and optimize production workflows to meet stringent quality standards. By implementing Six Sigma practices, manufacturing companies can enhance productivity, reduce waste, and elevate customer satisfaction levels, making it a beneficial and popular choice for industry transformation. One unique feature of Six Sigma's impact on manufacturing is its emphasis on data-driven decision-making, continuous improvement, and preventive measures to mitigate risks and sustain operational excellence.
Healthcare
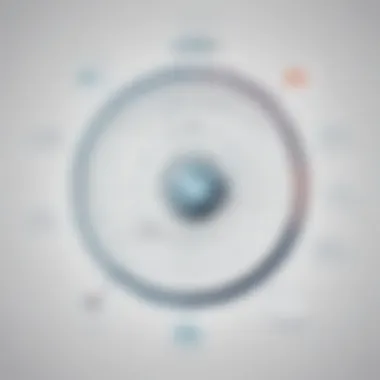

Within the healthcare industry, Six Sigma has proven to be instrumental in enhancing patient care, optimizing clinical processes, and driving organizational efficiency. The key characteristic of Six Sigma in healthcare is its focus on error reduction, outcomes improvement, and patient safety initiatives. By integrating Six Sigma methodologies into healthcare practices, organizations can streamline workflows, reduce medical errors, and improve overall service quality, making it a beneficial and popular choice for advancing healthcare delivery. One unique feature of Six Sigma's impact on healthcare is its emphasis on evidence-based practices, performance metrics, and cross-functional collaboration to achieve patient-centered care and operational effectiveness.
Service Sector
In the service sector, Six Sigma has revolutionized service delivery, customer satisfaction, and business performance by emphasizing process optimization, quality assurance, and continuous improvement. The key characteristic of Six Sigma in the service sector is its emphasis on customer feedback, service reliability, and efficiency enhancement. By leveraging Six Sigma principles, service organizations can enhance service quality, reduce response times, and increase customer loyalty, making it a beneficial and popular choice for service excellence. One unique feature of Six Sigma's impact on the service sector is its focus on service customization, employee training, and performance monitoring to meet changing customer demands and industry standards.
Challenges and Criticisms of Six Sigma
In this segment, we delve into the crucial facets of Challenges and Criticisms of Six Sigma. It is imperative to understand the drawbacks and objections raised against the Six Sigma methodology as a quality improvement approach in modern business practices. By dissecting the Challenges and Criticisms, we can glean valuable insights into areas that warrant reflection and possible refinement, enhancing our overall comprehension of Six Sigma within organizational contexts.
Limitations of Six Sigma
Over-Reliance on Data
The issue of Over-Reliance on Data is a prevalent concern within the Six Sigma framework. While data analysis is fundamental to process improvement, excessive reliance on data can sometimes lead to tunnel vision, where decision-making becomes overly constrained by statistical figures and metrics. This overreliance may result in missing out on broader qualitative aspects that could be equally crucial for achieving sustainable enhancements in operational performance. Striking a balance between data-driven insights and strategic intuition is vital to harness the true potential of Six Sigma methodologies effectively.
Resistance to Change
Resistance to Change poses a significant challenge to the successful implementation of Six Sigma initiatives. Organizations often encounter internal resistance from employees who are reluctant to embrace new methodologies and practices embedded within the Six Sigma principles. This resistance can impede the smooth adoption of Six Sigma strategies, leading to delays in realizing process improvements and quality outcomes. Addressing resistance to change requires effective change management approaches, clear communication channels, and robust leadership support to navigate through organizational transitions seamlessly.
Cost of Implementation
Another critical aspect highlighted in the realm of Six Sigma is the Cost of Implementation. While investing in Six Sigma can yield substantial returns in terms of efficiency and quality enhancements, the initial costs associated with training, infrastructure, and deployment of Six Sigma practices can be prohibitive for some organizations, especially smaller enterprises or startups. Balancing the perceived benefits of Six Sigma with the financial investments required for successful implementation poses a notable challenge that decision-makers must carefully evaluate and mitigate to leverage Six Sigma effectively for sustainable business improvements.
Critiques of Six Sigma
Lack of Focus on Innovation
One of the primary critiques against Six Sigma is its perceived Lack of Focus on Innovation. Critics argue that the relentless pursuit of process optimization and defect reduction may inadvertently stifle creativity and innovative thinking within organizations. By excessively emphasizing operational efficiency and quality control, Six Sigma methodologies might neglect opportunities for disruptive innovation and breakthrough solutions that could potentially drive long-term business growth and competitiveness. Striking a harmonious balance between Six Sigma principles and fostering a culture of innovation remains critical for organizations aiming to stay ahead in dynamic and competitive market landscapes.
Rigid Structure
The Critique of Rigid Structure within Six Sigma methodology raises concerns about the rigid and standardized approach advocated by Six Sigma practices. Critics highlight that the predefined processes and tools prescribed by Six Sigma frameworks may limit adaptability and agility within organizations, particularly in rapidly evolving business environments. The rigid structure of Six Sigma could potentially hinder organizations from swiftly responding to market dynamics, customer needs, and emerging trends, thereby posing challenges in maintaining relevance and sustainability. Balancing the benefits of structured methodology with the flexibility required for innovation and strategic agility becomes pivotal in addressing the critique of rigid structure within Six Sigma implementations.
Future of Six Sigma
Six Sigma has consistently evolved to adapt to the changing landscape of business and technology. Understanding the future trajectory of Six Sigma is vital for organizations aiming to stay ahead in quality management and operational efficiency. This section explores the upcoming trends and advancements that will shape the application of Six Sigma in modern business environments. The discussions will highlight the key elements, benefits, and considerations pertaining to the Future of Six Sigma.
Emerging Trends
Integration with Industry
The Integration with Industry 4.0 represents a pivotal advancement in the incorporation of digital technologies into manufacturing processes, enabling real-time data analytics, automation, and connectivity. This fusion revolutionizes the traditional Six Sigma approach by integrating smart technologies, IoT, and data-driven decision-making into quality management practices. The seamless alignment between Industry 4.0 and Six Sigma enhances process efficiency, reduces defects, and propels continuous improvement initiatives. This integration is characterized by its streamlined data exchange, predictive maintenance capabilities, and agile responsiveness to market demands. While offering substantial benefits in bolstering operational performance and product quality, it also poses challenges related to data security, system interoperability, and workforce upskilling.
Application in Digital Transformation
The Application in Digital Transformation signifies the utilization of Six Sigma methodologies to drive organizational change towards a digitally integrated and innovative ecosystem. This integration facilitates the synergistic application of Six Sigma tools in optimizing processes, enhancing customer experiences, and fostering a culture of innovation. The implementation of digital transformation through Six Sigma empowers businesses to adapt to the digital shift, embrace disruptive technologies, and optimize decision-making processes. The emphasis on digital transformation propels organizations towards heightened competitiveness, customer-centricity, and operational agility. However, this adaptation may introduce complexities in managing digital disruption, aligning cross-functional teams, and ensuring sustainable change management practices.
Adaptation in Modern Business
Agile Implementation
The Agile Implementation approach denotes the utilization of agile methodologies in conjunction with Six Sigma principles to foster flexibility, rapid iteration, and adaptive problem-solving. This methodology emphasizes incremental improvements, collaborative teamwork, and customer feedback integration within the Six Sigma framework. Agile Implementation augments the traditional Six Sigma methodologies by promoting iterative problem-solving, quick decision-making cycles, and dynamic project management practices. The amalgamation of agile principles into Six Sigma drives organizational responsiveness, innovation capability, and agility in accommodating changing market dynamics. However, the adoption of agile methodologies within Six Sigma may necessitate cultural transformation, redefined process metrics, and alignment with organizational goals and values.
Customization for Startups
Customization for Startups delineates the tailoring of Six Sigma principles to suit the organizational structures, resource constraints, and dynamic environments prevalent in startup ventures. This approach emphasizes a leaner, more adaptive application of Six Sigma methodologies to address the unique challenges and opportunities encountered by startups. Customization for Startups focuses on enhancing operational efficiencies, accelerating time-to-market, and nurturing a culture of quality excellence within startup ecosystems. By customizing Six Sigma for startups, organizations can foster innovation, scalability, and sustainable growth while navigating the uncertainties inherent to the startup landscape. However, this tailored approach may require flexibility in implementation, swift decision-making processes, and a robust change management framework tailored to startup dynamics.