Understanding TMS Work Orders: A Comprehensive Exploration
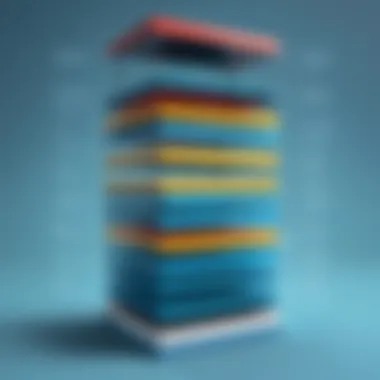
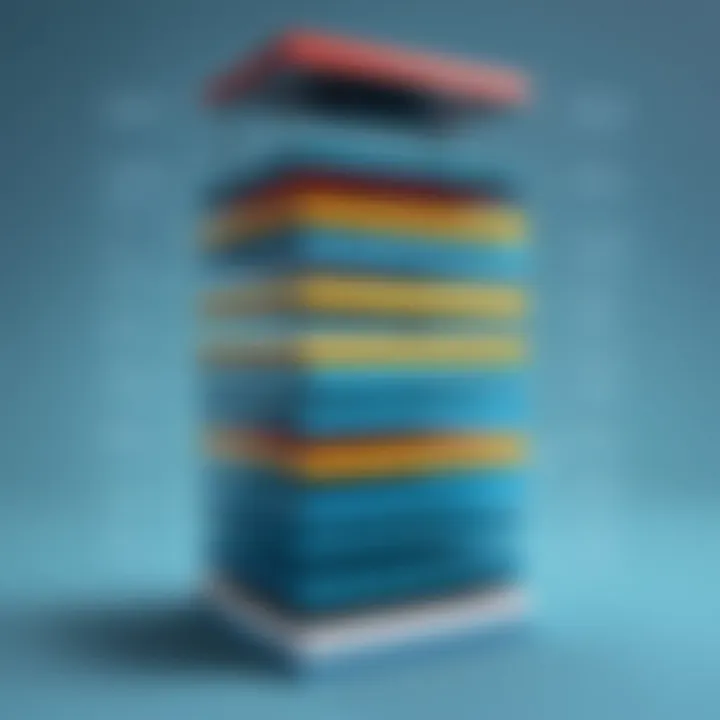
Intro
Transportation Management Systems (TMS) have become essential tools in today's logistics and supply chain landscape. Their role in managing work orders is critical, as it leads to improved operational efficiency and streamlined communication among stakeholders. This article will examine the structure and functionality of TMS work orders, shedding light on why they are vital in modern transportation management. Understanding these systems is not just a matter for specialists; professionals, decision-makers, and tech enthusiasts will find value in exploring how TMS work orders can transform their businesses and enhance their logistics processes.
Technological Research Overview
Recent advancements in technology have drastically reshaped the logistics industry. Modern TMS systems are equipped with cutting-edge features that not only simplify the process of creating and managing work orders but also enhance overall business operations.
Recent Technological Innovations
Transportation Management Systems have integrated several innovations, including:
- Cloud Computing: Offers flexibility and scalability, allowing businesses to access their TMS from any location.
- Real-time Tracking: Enables companies to monitor shipments and delivery processes instantaneously.
- Mobile Access: Facilitates operations and communications through apps that keep all stakeholders informed.
Impact on Business Operations
The integration of TMS technologies into the logistics workflow leads to improved operational performance. As companies leverage these systems, they often experience:
- Enhanced route planning
- Reduced operational costs
- Increased customer satisfaction due to timely deliveries
Future Technological Trends
Looking ahead, the evolution of TMS work orders will likely be influenced by:
- AI and Machine Learning: These technologies are expected to further automate processes, allowing for more accurate predictions and decisions.
- Blockchain: This may ensure greater transparency and security in transaction processes.
Data Analytics in Business
Data analytics play an indispensable role in enhancing the capabilities of TMS work orders. Companies that utilize data effectively can make informed decisions that significantly impact their bottom lines.
Importance of Data Analytics
Using analytics allows organizations to:
- Identify trends in transportation and logistics.
- Optimize resource allocation based on real-time data.
- Generate reports that support strategic planning.
Tools for Data Analysis
Various tools can help businesses analyze data related to TMS work orders:
- Tableau for data visualization
- Microsoft Power BI for report generation
- SQL databases for structured data storage and extraction
Case Studies on Data-Driven Decisions
Analyzing successful case studies can offer insights into effective data utilization. Companies, like Amazon, utilize TMS analytics to streamline their operations and enhance efficiency throughout their supply chain.
Cybersecurity Insights
As TMS systems increasingly rely on digital frameworks, cybersecurity has become paramount. Understanding the threat landscape and adopting best practices is essential for safeguarding data.
Threat Landscape Analysis
The transportation industry faces a range of cyber threats, including:
- Ransomware attacks that disrupt operations.
- Data theft that compromises sensitive customer information.
Best Practices for Cybersecurity
To mitigate risks, companies should:
- Regularly update their software to patch vulnerabilities.
- Train employees on recognizing phishing attempts.
- Employ robust encryption methods for sensitive data.
Regulatory Compliance in Cybersecurity
Adhering to regulations such as GDPR or CCPA is essential. Compliance not only protects companies legally but also fosters trust with customers.
Artificial Intelligence Applications
Artificial intelligence is changing how TMS work orders are managed. AI outputs provide insights that enhance decision-making processes.
AI in Business Automation
Through automation, AI allows for:
- Reduction in manual processing errors.
- More efficient workload management.
AI Algorithms and Applications
Employing algorithms can help in various functions:
- Predictive analytics for forecasting demand.
- Scheduling optimization to reduce delays.
Ethical Considerations in AI
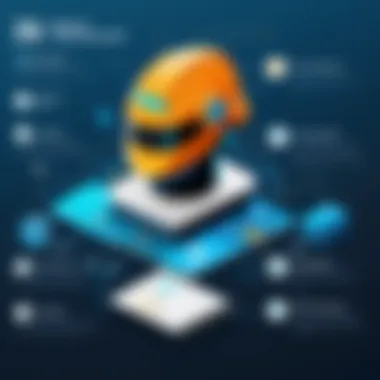
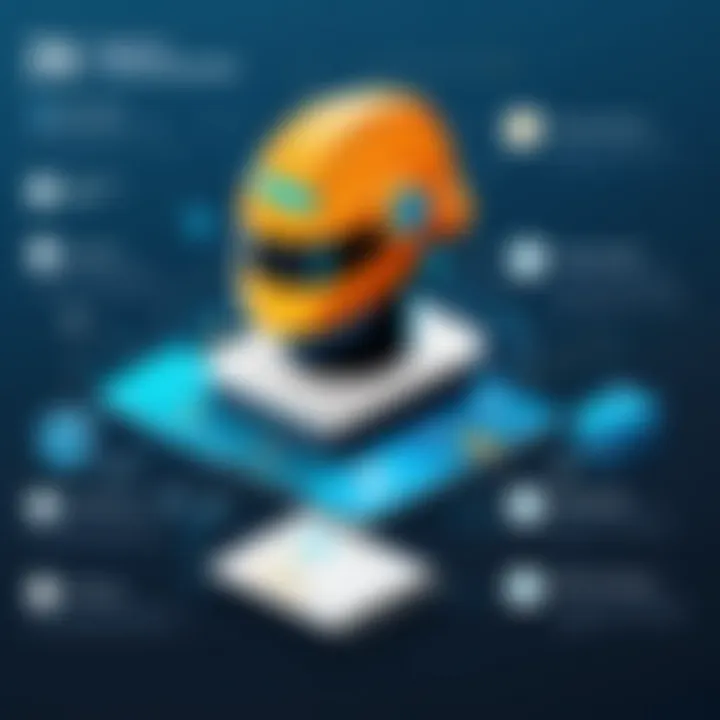
As AI takes a more prominent role in business processes, organizations must ensure ethical considerations, such as:
- Fair treatment of all suppliers.
- Transparency in AI decision-making.
Industry-Specific Research
Different sectors may have unique challenges that TMS work orders can address.
Tech Research in Finance Sector
In finance, efficiency in logistics can translate into cost savings and enhanced service provision.
Healthcare Technological Advancements
For healthcare, accurate work orders ensure timely delivery of crucial supplies.
Retail Industry Tech Solutions
Retailers utilize TMS for efficient inventory management and faster responses to market changes.
Preface to TMS Work Orders
Transportation Management System (TMS) work orders are vital in managing the logistics and supply chain processes efficiently. This section elaborates on the significance of TMS work orders. It highlights how they serve as a foundation for transportation operations and their impact on overall productivity.
TMS work orders streamline various tasks within the shipping and transportation industry. They provide the structure needed to execute orders with precision and clarity. The importance of establishing well-defined work orders cannot be overstated. They contribute to reducing errors, avoiding delays, and enhancing communication among stakeholders.
Benefits of TMS Work Orders
- Clarity: Clear work orders specify all expected actions, responsibilities, and timelines.
- Efficiency: Properly managed work orders save time by outlining processes step-by-step.
- Monitoring: Work orders allow tracking of progress in real-time, which links closely with performance metrics.
In summary, understanding TMS work orders lays the groundwork for improving business operations in transportation management. With precise definitions and importance, they form the backbone of a robust logistics strategy.
Defining TMS Work Orders
TMS work orders refer to documents that outline specific tasks and protocols to be followed within the transportation management framework. These orders detail what needs to be done, who is responsible for the tasks, and when they need to be completed. Generally, they include information related to pickup and delivery locations, cargo descriptions, and timing schedules.
A well-defined work order acts as a guideline for executing transportation activities. This definition encompasses several elements such as the type of service required, the vehicle needed, and any special instructions necessary for handling cargo. When organizations adopt precise definitions of work orders, they enhance uniformity in operations that can lead to better outcomes.
Importance of Work Orders in Transportation Management
Work orders hold a critical role in the logistics sector. Their importance can be categorized into several key aspects:
- Coordination: Work orders facilitate better coordination between parties involved. They provide a clear reference that various teams can rely on.
- Accountability: When tasks are explicitly outlined, it is easier to hold individuals accountable for their responsibilities.
- Data Recording: Work orders serve as a record of what has been done. This data is vital for future analysis and planning.
Components of TMS Work Orders
Understanding the various components of TMS work orders is crucial for maximizing the efficiency and effectiveness of logistics processes. These components serve as the backbone of the work order system, ensuring that all necessary information is captured and processed correctly. In an environment where transportation management directly impacts overall operational performance, grasping the structure of work orders helps professionals make informed decisions.
Key Elements of a Work Order
A TMS work order typically contains several key elements that are essential for clarity and actionability. These include:
- Order ID: A unique identifier that simplifies tracking and referencing the work order.
- Origin and Destination: Clear specifications about where the goods are coming from and where they are headed.
- Description of Goods: Detailed descriptions including type, quantity, and any specific handling instructions.
- Scheduled Dates: Information on when the transport is to occur, incorporating start and estimated completion dates.
- Assigned Resources: Details about equipment, vehicles, and personnel designated for the task.
- Cost Estimates: Financial implications associated with the transport, facilitating budget management.
Each of these components contributes to a holistic view of transportation processes, allowing for better planning and execution of logistics activities.
Work Order Lifecycle
The lifecycle of a TMS work order is pivotal for ensuring that processes flow smoothly from initiation to completion. Understanding this lifecycle can help logisticians identify bottlenecks and optimize the overall workflow.
- Creation: The process begins with the creation of the work order, which includes inputting all essential data from various stakeholders.
- Assignment: Once created, the work order is assigned to relevant personnel or departments responsible for execution.
- Execution: This phase involves the actual transportation of goods according to the specified details in the work order.
- Monitoring: During transportation, real-time tracking is crucial for identifying any deviations from the plan.
- Completion: Finalizing the work order involves confirming delivery and closing the order, often requiring signatures or digital confirmations.
Understanding the life cycle ensures that all parties involved in transportation management can remain aligned with the status of each work order, thus promoting efficiency and reducing errors.
Creating TMS Work Orders
Creating TMS work orders is a crucial aspect of effective transportation management. It involves systematically organizing and documenting tasks necessary to ensure smooth logistics operations. The creation process not only enhances operational efficiency but also facilitates communication among different stakeholders. Therefore, understanding the nuances of this process can significantly impact overall performance in supply chain management.
Data Collection and Entry
Data collection and entry form the foundation of generating accurate TMS work orders. This stage involves gathering essential information from various sources. The effectiveness of the data entered directly influences the quality of the work orders created. Examples of necessary data include:
- Shipment details, including origin, destination, and weight.
- Vehicle capacities to ensure proper resource allocation.
- Time-sensitive information for delivery schedules.
- Customer requirements for specific services, such as handling or packaging.
Organizations need to adopt a structured approach for data collection. Implementing standardized forms and procedures can help reduce errors and ensure consistency. It is equally important to train personnel on the significance of accurate data entry.
Automation in Work Order Creation
Automation plays a transformative role in the creation of TMS work orders. Integrating automation tools helps streamline processes, reduce manual efforts, and improve data accuracy. The benefits of automation in this context include:
- Speed: Automated systems can process data much faster than manual methods, leading to quicker work order generation.
- Accuracy: Automation minimizes the potential for human error, ensuring that work orders reflect accurate and up-to-date information.
- Scalability: With automation, increasing the volume of work orders does not require a proportionate increase in workforce.
- Integration: Automated systems can connect with other software solutions, allowing for seamless data transfer across different platforms.
Consider implementing comprehensive software solutions that provide automation capabilities specifically for TMS work orders. The investment in technology may yield significant returns in operational efficiency and productivity.
The Role of Technology in Work Orders
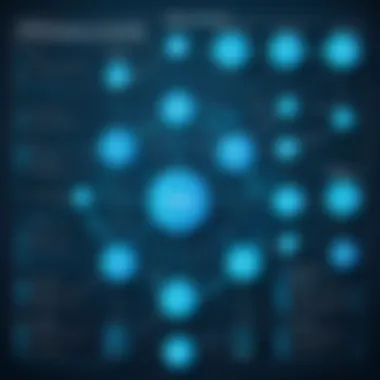
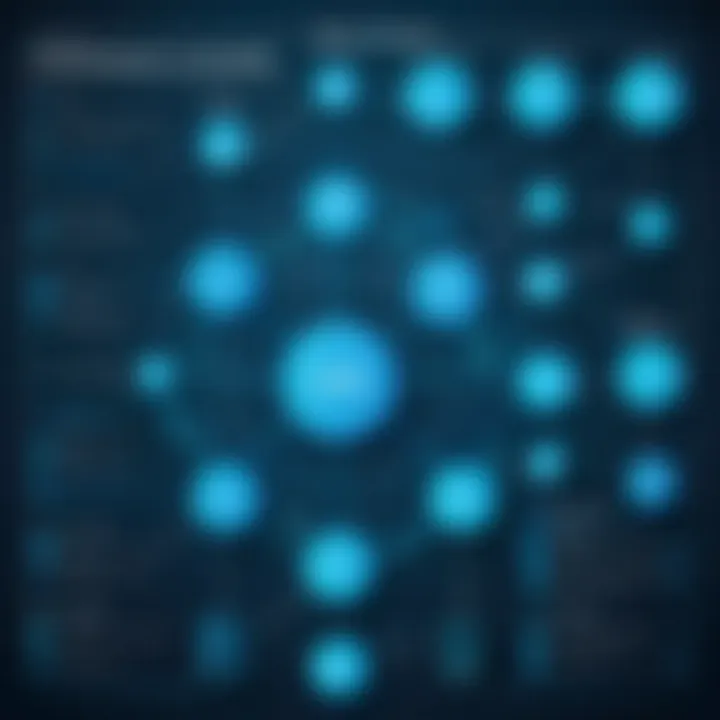
In the modern landscape of transportation management, the role of technology is pivotal. Technology acts as a facilitator, enhancing the functionality and efficiency of Work Order Systems. It helps streamline processes, reduces manual errors, and fosters communication among various stakeholders. By automating tasks and providing real-time tracking, organizations can react promptly to any disruption. In this light, understanding the technological elements behind TMS work orders is essential for optimizing performance in logistics operations.
Software Solutions for TMS Work Orders
Various software solutions exist that cater specifically to managing TMS work orders. One of the critical advantages of these platforms is their ability to integrate with other systems, creating a seamless flow of information. For example, software like SAP Transportation Management and Oracle Transportation Management provide comprehensive tools to handle work orders effectively.
Key features often include:
- Centralized Management: These systems allow companies to manage multiple work orders from one interface, thus saving time.
- Real-Time Updates: Users can receive instant notifications, enhancing response times and decision making.
- Data Analytics: In-depth data analysis aids businesses in understanding trends and areas for improvement.
The choice of software can significantly influence the overall effectiveness of work order management. Companies should consider their specific operational needs and scalability when selecting these tools.
Impact of AI and Machine Learning
The integration of AI and machine learning technologies marks a transformative step in TMS work order management. These technologies can analyze vast amounts of data and provide insights that were previously hard to identify.
Some notable impacts include:
- Predictive Analytics: AI models can predict delays and adjust work orders accordingly, enhancing efficiency.
- Optimized Routing: Machine learning algorithms can determine the most effective routes for transportation, saving time and costs.
- Improved Resource Allocation: These systems can suggest the best allocation of resources based on historical data.
The implementation of AI does come with challenges, such as data privacy concerns and resource requirements. Nonetheless, the benefits can substantially outweigh these issues, making it a worthwhile investment for many organizations in the sector.
"Technology is not just a facilitator, it is the backbone of effective TMS work order management. Without it, organizations risk falling behind in an increasingly competitive milieu."
As we look to the future, the continuous evolution of technology will further shape the landscape of TMS work orders, making it imperative for businesses to stay informed and adaptable.
Managing TMS Work Orders
Managing TMS work orders is a crucial aspect of effective transportation management. This process not only ensures that shipments are tracked and delivered efficiently, but also aids in optimizing resource allocation. Efficient management of work orders can lead to significant improvements in operational performance.
One key component of managing TMS work orders is tracking and monitoring processes. By implementing systematic tracking methods, organizations can keep an eye on the status of shipments in real-time. This visibility helps in identifying potential delays and taking proactive measures to mitigate them. Moreover, advanced tracking tools provide rich data analytics that can inform decision-making, leading to more informed operational strategies.
Additionally, effective communication strategies between stakeholders play a vital role in managing TMS work orders. Clear communication channels are necessary to ensure that all parties, including drivers, warehouse staff, and management, are aligned on shipment details. Miscommunication can lead to errors, delays, or even financial losses. By utilizing collaborative platforms and tools that facilitate information sharing, companies can enhance visibility and transparency within the supply chain.
Overall, by prioritizing effective management of TMS work orders, organizations can streamline their logistics operations. This ultimately contributes to reduced costs and improved customer satisfaction. Below, we explore the specific strategies related to tracking processes and communication that can significantly impact TMS work order management.
Tracking and Monitoring Processes
Tracking and monitoring processes are foundational in TMS work order management. They encompass a range of activities that provide visibility into the movement of goods throughout the supply chain. Effective tracking involves not only knowing where goods are but also understanding their condition, estimated delivery times, and any potential risks along the way.
Digital tools are immensely beneficial in this regard. Transport management systems often include GPS tracking features and real-time dashboards. These functionalities enable logistics managers to view shipment locations and status updates instantly.
Some essential tracking techniques include:
- Barcode scanning: Enhances accuracy in recording item movements.
- RFID Technology: Provides automated tracking and stock updates.
- Cloud-based software: Allows for centralized access to shipment data from anywhere.
By using these techniques, organizations improve efficiency in process tracking and can address issues proactively before they escalate.
"Real-time tracking is not just about visibility; it's about taking control of your logistics operations."
Communication Strategies Between Stakeholders
Effective communication strategies are key to the success of TMS work order management. Good communication reduces the probability of misunderstandings and enhances teamwork among stakeholders. It is also critical in managing expectations and providing updates throughout the shipment process.
One effective tactic is using integrated communication platforms that link all parties involved. By having a centralized system, information about shipments is accessible to drivers, warehouse staff, and office personnel. This synchronization reduces the likelihood of siloed information and incorrect assumptions.
Other communication strategies include:
- Regular updates: Scheduled check-ins can ensure everyone is on the same page.
- Alerts and notifications: Automated alerts can inform stakeholders about critical changes, delays, or issues.
- Feedback mechanisms: Allowing stakeholders to report issues can enhance the workflow.
By improving communication flow, companies can ensure that TMS work orders are managed effectively with all necessary adjustments made promptly. This harmonization ultimately leads to smoother operation, boosted efficiency, and better customer relations.
Challenges in TMS Work Order Management
Managing TMS work orders is essential for ensuring efficiency and effectiveness within logistics and supply chain operations. This process can be quite complex due to various challenges that organizations face. Recognizing these challenges is the first step toward overcoming them. In this section, we will explore the common issues encountered in TMS work order management and present mitigation strategies to tackle these difficulties.
Common Issues Encountered
TMS work order management can come with numerous issues. Some of the most notable challenges include:
- Inaccurate Data Entry: Errors can occur during data entry, leading to discrepancies in work orders. These errors can stem from manual inputs or poor integration with other systems.
- Lack of Visibility: Stakeholders often encounter issues with tracking work orders. When information is not readily available, delays can happen, affecting overall operations.
- Poor Communication: Communication breakdowns between departments can lead to misunderstandings. This can delay decision-making and hinder process efficiency.
- Regulatory Compliance Issues: Ensuring all work orders are compliant with industry regulations can be cumbersome. Non-compliance may lead to fines and operational disruptions.
- Resource Allocation Problems: Inadequate resource allocation can occur when the demand for transport does not align with available resources. This can result in delays and increased operational costs.
Mitigation Strategies
To enhance TMS work order management, organizations need to implement effective strategies for mitigation. Here are several recommended approaches:
- Invest in Training: By providing thorough training to staff, organizations can minimize data entry errors and promote awareness of proper procedures.
- Leverage Technology: Utilizing specialized TMS software can improve data management and increase visibility. Solutions that integrate with ERP and other systems can streamline operations.
- Establish Clear Communication Channels: Developing standardized communication practices can significantly reduce misunderstandings. Regular meetings and update systems can help keep everyone on the same page.
- Regular Compliance Audits: Conducting periodic reviews of work orders against regulatory requirements can identify potential compliance issues before they escalate.
- Dynamic Resource Allocation: Employing flexible resource allocation methods can help match transport capacity with demand fluctuations, reducing delays and costs.
Implementing these strategies can greatly improve the landscape of TMS work orders, ensuring smoother operations and better outcomes for all stakeholders involved.
By addressing these common issues and employing effective mitigation strategies, companies can enhance their TMS work order management processes. This not only results in improved operational efficiency but also fosters better communication and compliance across the board.
Case Studies on Effective TMS Work Order Implementation
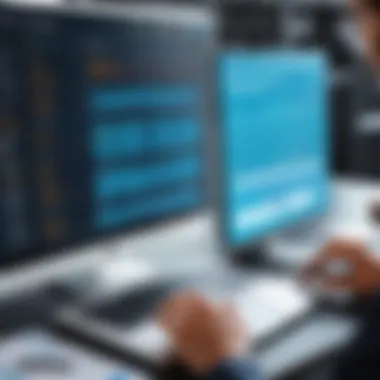
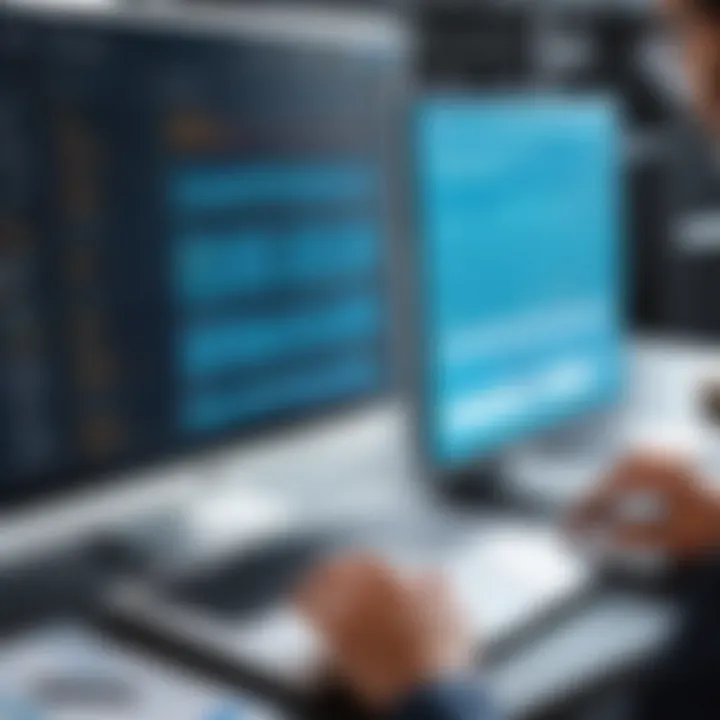
Case studies play a crucial role in understanding the practical application of TMS work orders. They provide real-world examples that illustrate both successes and failures within transportation management. By examining these case studies, professionals can glean insights into best practices while avoiding common pitfalls. The analysis of effective implementations highlights key strategies and decisions that can lead to enhanced performance across logistics operations.
Successful Examples in Industry
In various industries, successful TMS work order implementation has resulted in significant operational improvements. One notable example is Amazon, which utilizes sophisticated work order systems to optimize their supply chain processes. By automating work orders, Amazon minimizes downtime and enhances inventory management. Their use of data analytics helps make informed decisions, leading to smoother operations.
Another example is DHL, a global leader in logistics. DHL implemented TMS work orders to streamline communication between drivers and warehouses. This integration resulted in quicker response times and improved resource allocation. As a result, clients experience faster delivery times, reflecting positively on DHL's reputation.
To summarize, successful implementations of TMS work orders in these companies demonstrate the importance of technology in transportation management. The alignment of work orders with operational goals enhances efficiency and customer satisfaction.
Lessons Learned from Failures
On the flip side, failures in TMS work order management provide valuable lessons. Target, for instance, faced difficulties when launching an ambitious logistics system. Their efforts to integrate multiple technologies led to confusion and errors in work order processing. Consequently, this caused delays in product deliveries, negatively impacting customer trust and satisfaction.
Another case to consider is Kraft Heinz, which encountered issues during their transition to a new TMS framework. The lack of employee training and support led to resistance and mismanagement of work orders. These errors echoed through the supply chain, revealing how essential proper implementation is.
The failures highlighted in these cases underscore critical elements for organizations considering TMS work order implementations:
- Thorough Training: Employees must understand the tools and processes.
- Clear Communication: All stakeholders should be aligned and informed on updates.
- Gradual Integration: Implementing systems in phases can reduce errors.
"The failures in TMS work order management remind us that success is built on foundation of thorough planning and execution."
Overall, lessons from these failures emphasize the importance of careful planning, employee engagement, and incremental implementation in achieving effective TMS work order management.
Impact of Regulations on TMS Work Orders
The regulation landscape is critical for effective Transportation Management System (TMS) work orders. Understanding these regulations helps organizations maintain compliance and avoid potential legal issues. Regulations can influence workflows, data management, and even the technology used in TMS. Without proper adherence to regulations, a company can face penalties, damage to reputation, and operational disruptions. Therefore, it is important to analyze how regulations impact TMS work orders.
Compliance and Legal Considerations
Legal frameworks governing TMS work orders are diverse and can vary significantly by jurisdiction. Compliance ensures that all operations are performed within the law, especially when handling sensitive information such as driver details, shipment data, and environmental regulations. Companies must prioritize compliance in their TMS work orders to avoid costly fines.
Organizations frequently check relevant regulations to develop policies that are aligned with the legal requirements. This involves regular audits and consultations with legal experts to keep abreast of any changes. Additionally, significant considerations include:
- Data Security: Ensuring that customer and shipment data is securely handled.
- Environmental Regulations: Adhering to guidelines that address sustainable transportation practices.
- Health and Safety Laws: Ensuring that transportation methods comply with safety standards for personnel and vehicles.
Establishing a robust compliance framework helps in addressing these considerations and ensures smooth TMS operations.
Adapting to Changing Regulations
The regulatory environment is not static; it evolves constantly, influenced by technological advancements, environmental concerns, and shifts in public policy. Companies using TMS must be agile, adapting their work orders to fit new regulations.
The process of adapting involves:
- Monitoring Regulatory Changes: Regularly engage with government updates, industry groups, and news outlets to stay informed.
- Training Staff: Implement training programs that educate employees about new regulations and their implications for work orders.
- Updating TMS Protocols: Modify existing TMS functionalities to incorporate changes, ensuring that all workflows remain compliant.
By proactively addressing changes in regulations, organizations can mitigate risks and enhance their operational efficiency. Regulatory flexibility can lead to better resource allocation, reduced operational risks, and improved stakeholder trust.
Transportation organizations that embrace change not only comply with regulations but also position themselves as industry leaders.
The Future of TMS Work Orders
The landscape of logistics and supply chain management is ever-evolving. As such, understanding the future of TMS work orders is crucial for professionals in the field. These work orders are not static; they adapt to changes in technology, regulations, and market demands. This section highlights important aspects that define the future of work orders, including trends, innovations, and the potential hurdles that may arise.
Emerging Trends and Innovations
Several emerging trends indicate a shift in how TMS work orders will be structured and used. One notable trend is the integration of advanced technologies. Companies are increasingly utilizing cloud-based platforms. This not only facilitates real-time data access but also enhances collaboration among different stakeholders.
Another important trend is the use of predictive analytics. By leveraging data intelligence, organizations can anticipate demand fluctuations and adjust their work orders accordingly. This capability streamlines operations and reduces inefficiencies.
Moreover, IoT (Internet of Things) devices are becoming vital in managing logistics. These devices help track shipments in real-time, contributing to the accuracy of work orders. As technologies like autonomous vehicles and drones emerge, expect a transformation in logistics management.
- Key Innovations Include:
- Automation of routine tasks
- Real-time tracking using IoT
- Use of data analytics for decision-making
Anticipating Future Challenges
While the future holds promising prospects, challenges will inevitably emerge. One of the main concerns is data security. As companies rely more on digital platforms, the risk of cyberattacks increases. Protecting sensitive information will be paramount.
Compliance with ever-changing regulations is another challenge. As governments adapt laws to new technologies, staying updated on compliance requirements can be daunting. Organizations must invest in training and resources to ensure they are aligned with legal standards.
Lastly, the integration of new technologies may lead to resistance among employees. Change management will be essential for organizations to adapt effectively. Maintaining a workforce that is flexible and responsive to technology is a strategic imperative.
โUnderstanding these potential challenges is critical for companies looking to thrive in the rapidly changing landscape of TMS work orders.โ
Addressing these future challenges will be essential for the sustainable growth and efficiency of transportation management systems.
Epilogue
The conclusion of this article serves as a vital synthesis of the complexities surrounding TMS work orders. In the context of transportation management, it underscores the pivotal role these work orders play in enhancing operational efficiency and facilitating seamless communication among various stakeholders. Through the previous sections, we have explored the numerous facets of TMS work orders, from their fundamental definition to the technological advancements that influence their management.
Summarizing Key Insights
In reviewing the key insights gained throughout the article, it is apparent that TMS work orders are not merely administrative documents. They represent a strategic element that can streamline logistics and improve the overall supply chain management. Here are several critical points that emerge:
- Efficiency Gains: Proper management of TMS work orders leads to significant time savings and resources optimization.
- Enhanced Communication: Clear work orders foster better collaboration not only internally within an organization but also externally with suppliers, carriers, and customers.
- Adaptability: TMS work orders are critical in adapting to changes in regulatory environments and market conditions, ensuring compliance and operational continuity.
- Integration of Technology: The role of advanced software solutions and AI technologies cannot be overstated in managing TMS work orders effectively.
"Effective TMS work order management not only enhances efficiency but fosters a repeatable cycle of improvement in logistics operations."
Final Thoughts on TMS Work Orders
Decision-makers should prioritize investing in the right technologies and training to boost the effectiveness of their TMS work orders. By doing so, organizations will not only meet current logistical challenges but will also position themselves advantageously in the face of future developments. Thus, recognizing the essential nature of TMS work orders will allow firms to navigate the logistics landscape more adeptly and achieve long-term operational success.